Just got my first engine drive welder from a weld supplier Encore in southern California. If your ever in town or live near by its definitely a weld supplier you wanna visit.
Signal hill California
Ontario California
And Valencia California.
Jorge LLamas
Posted
26 May 23:35


Posted
27 Mar 02:18
Hi joey, I wanted to ask if i could download some of my favorite video content outside of the courses? keeping your pop in prayers , thanks for all the valuable content.
Posted
08 Feb 23:25
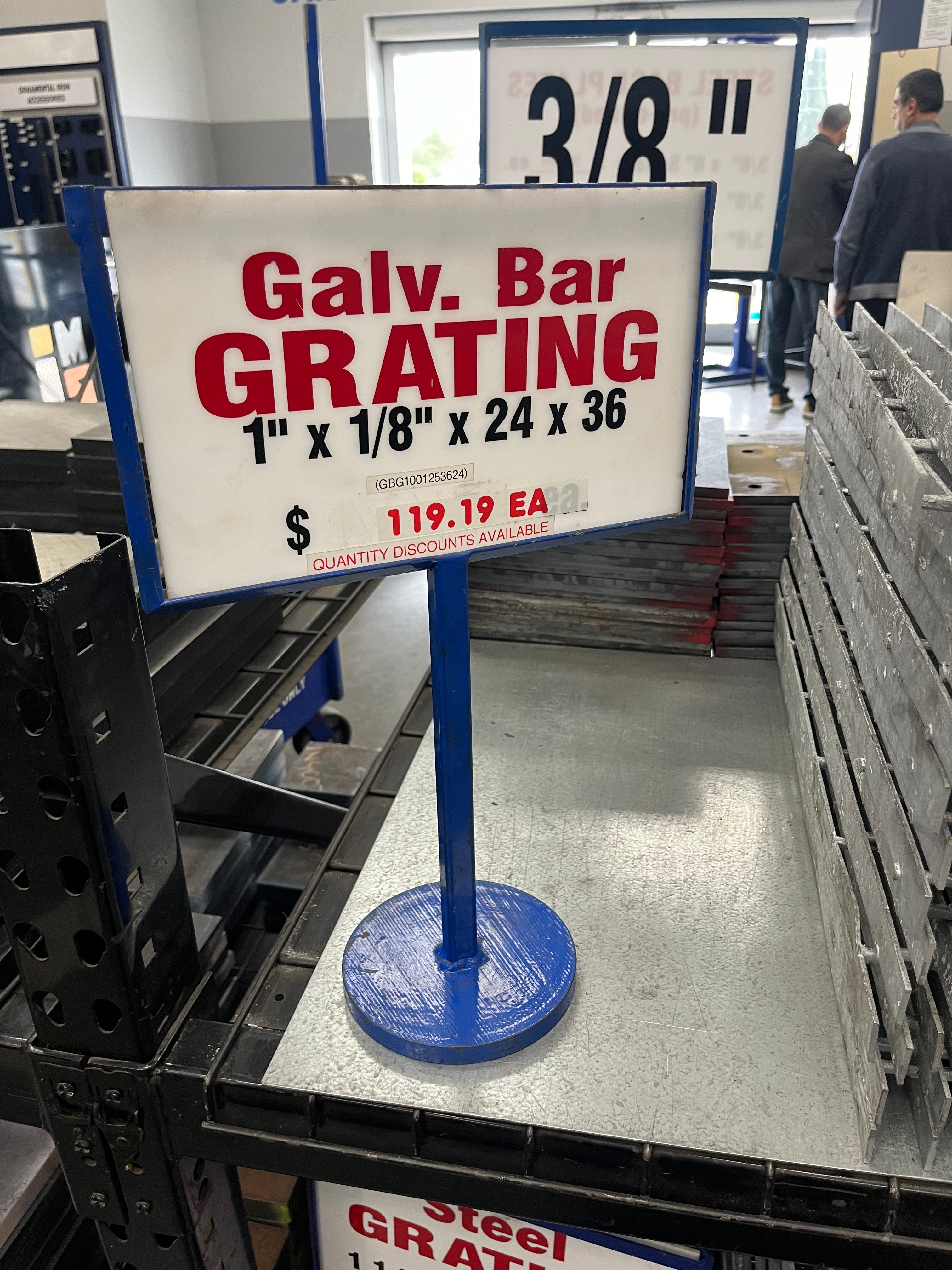
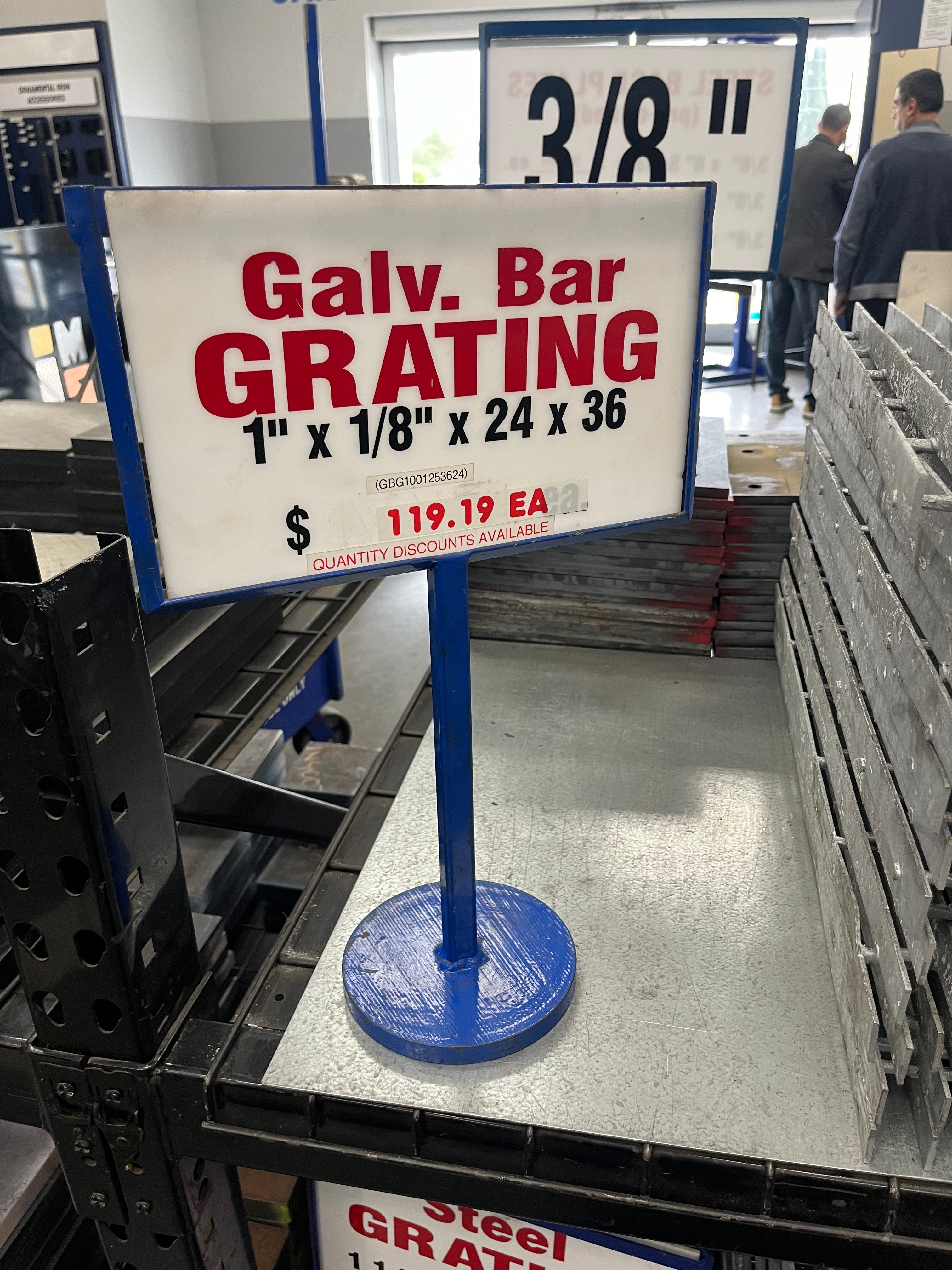
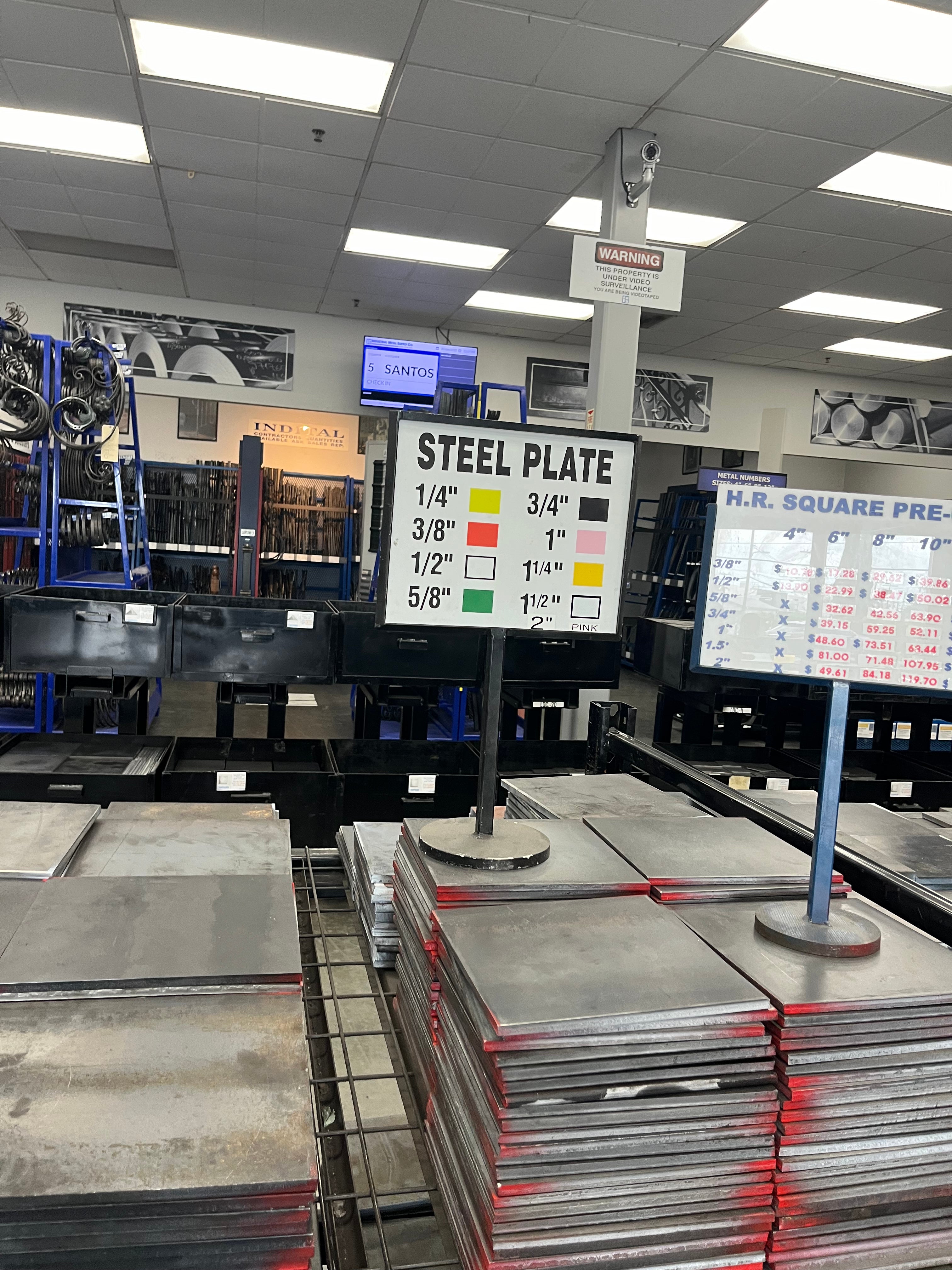
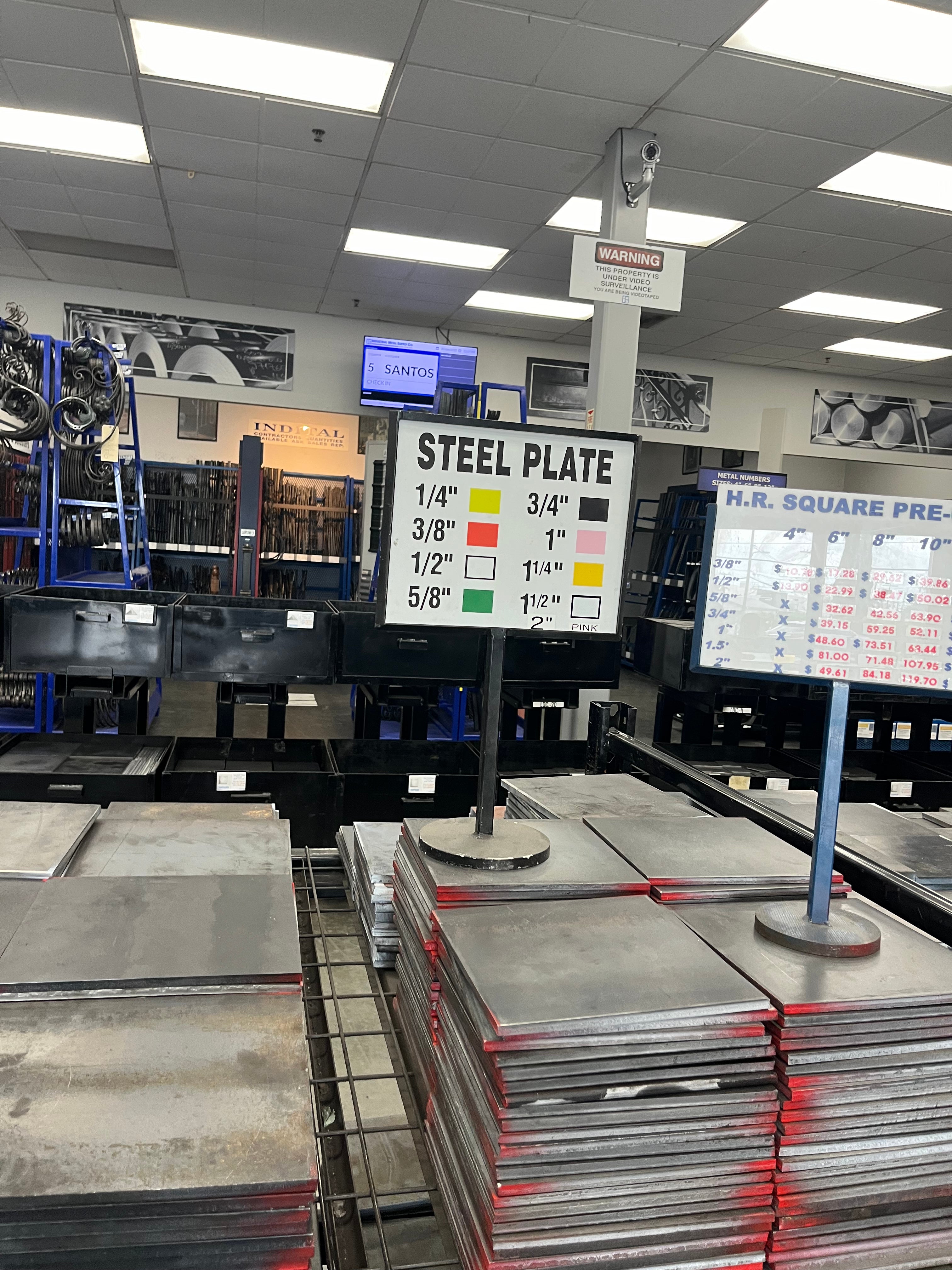
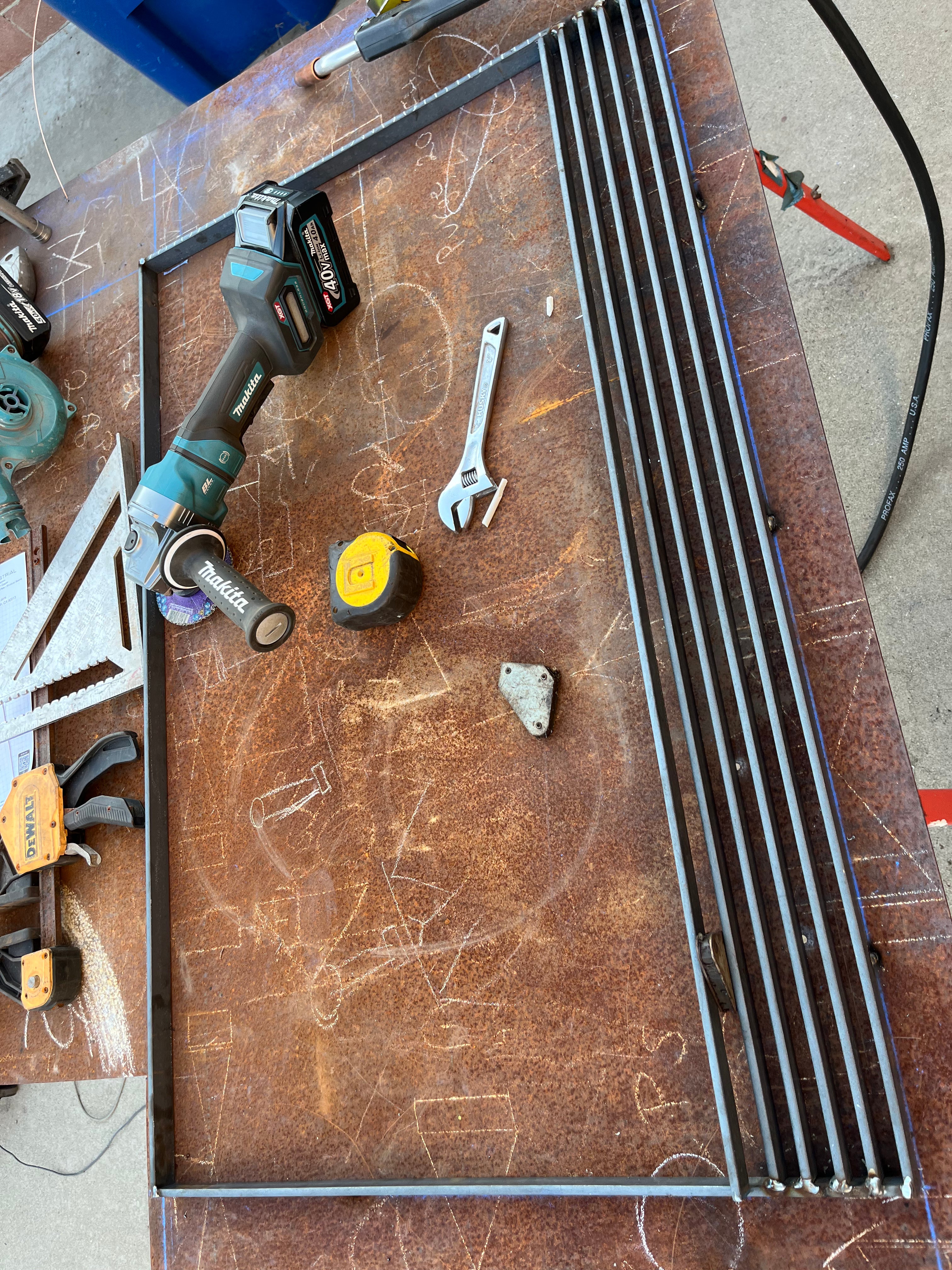
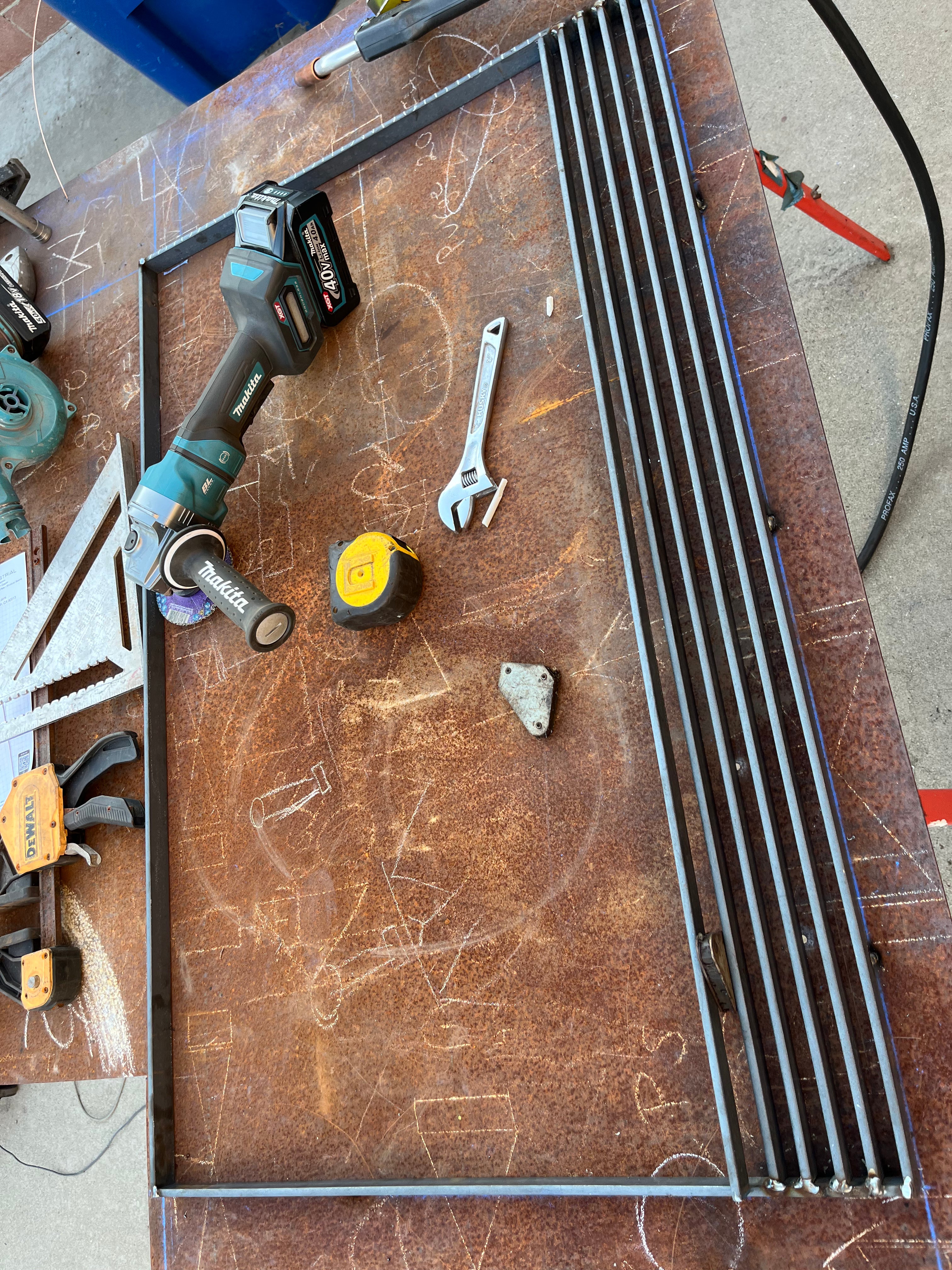
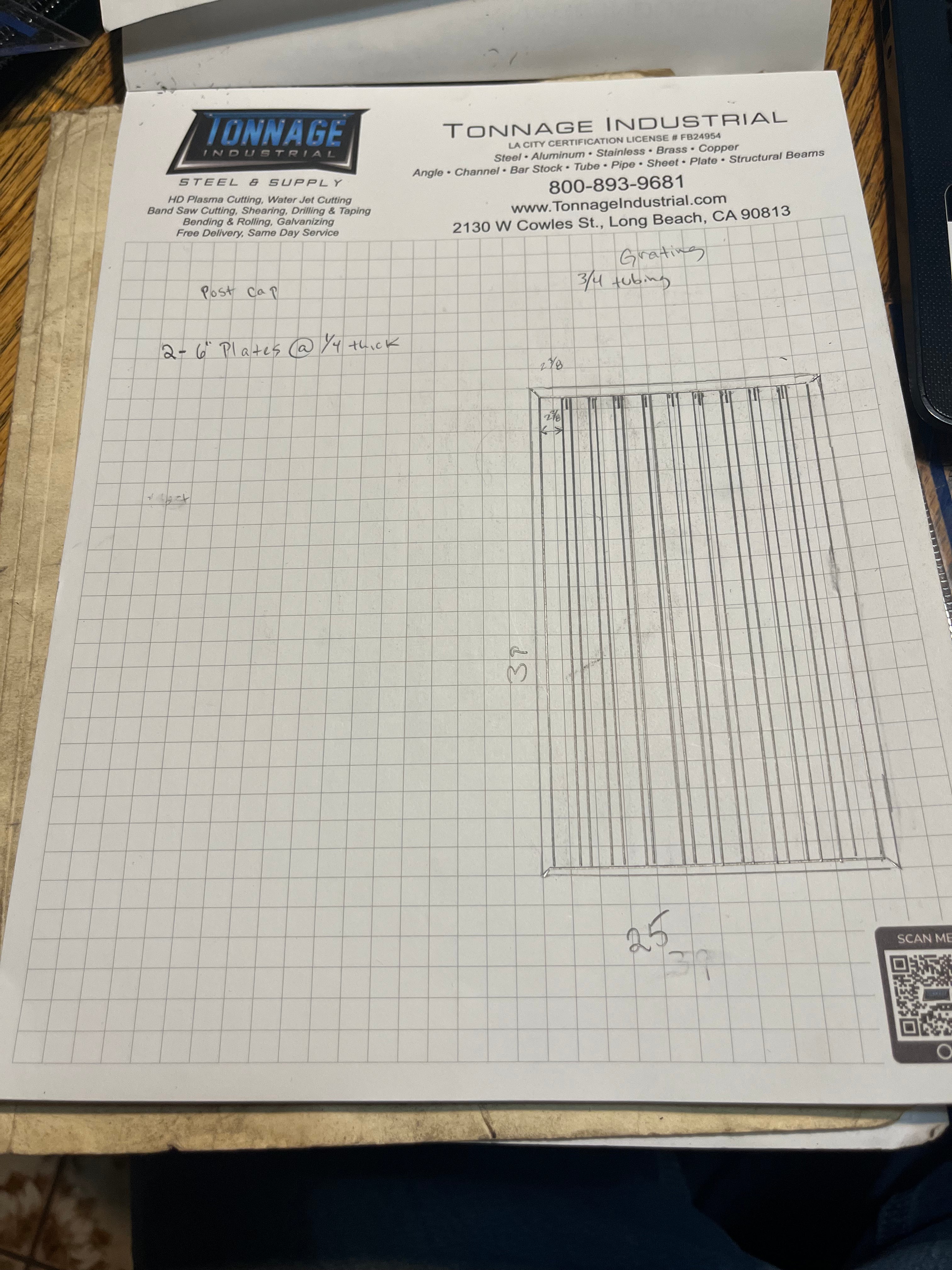
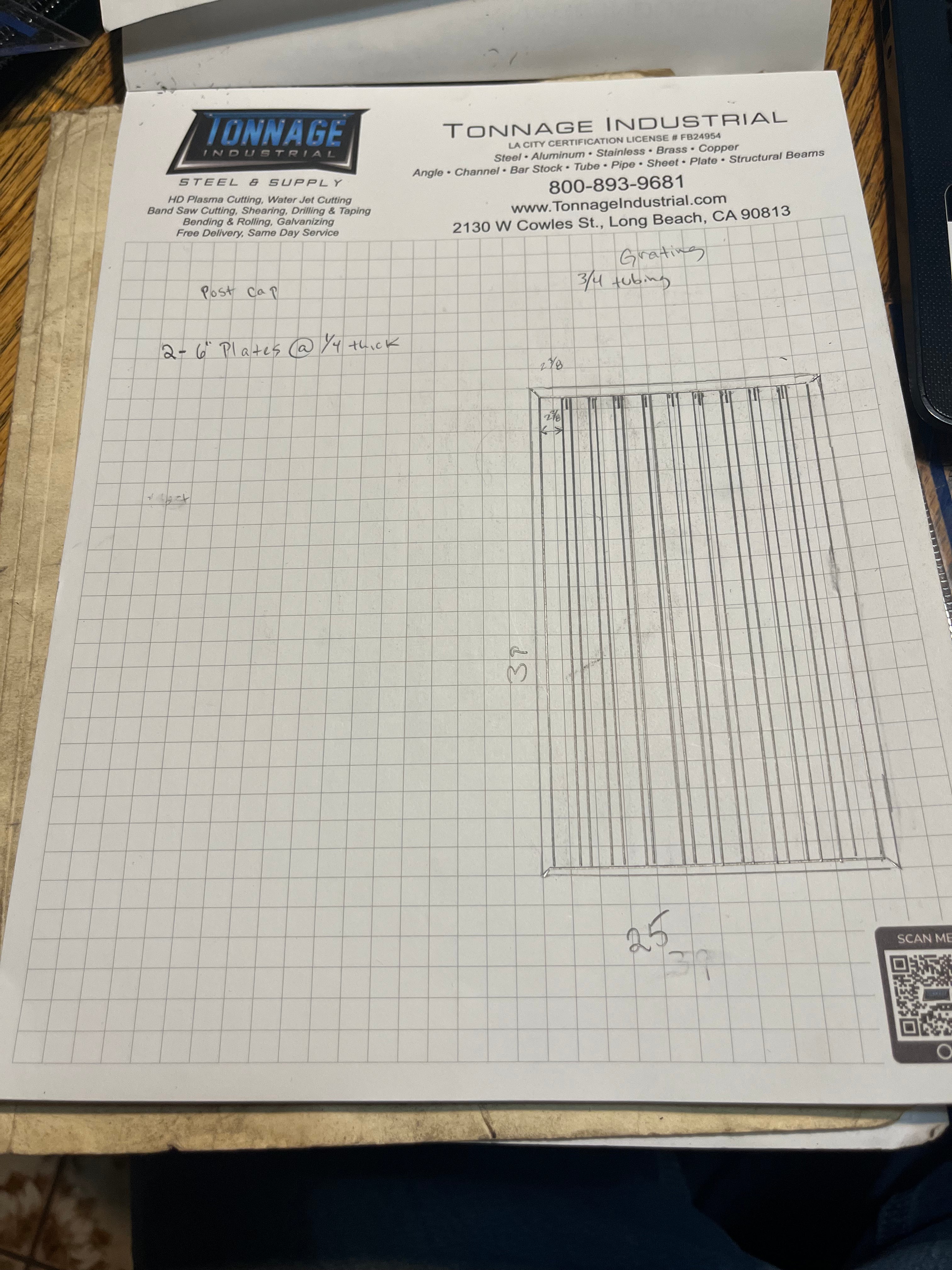
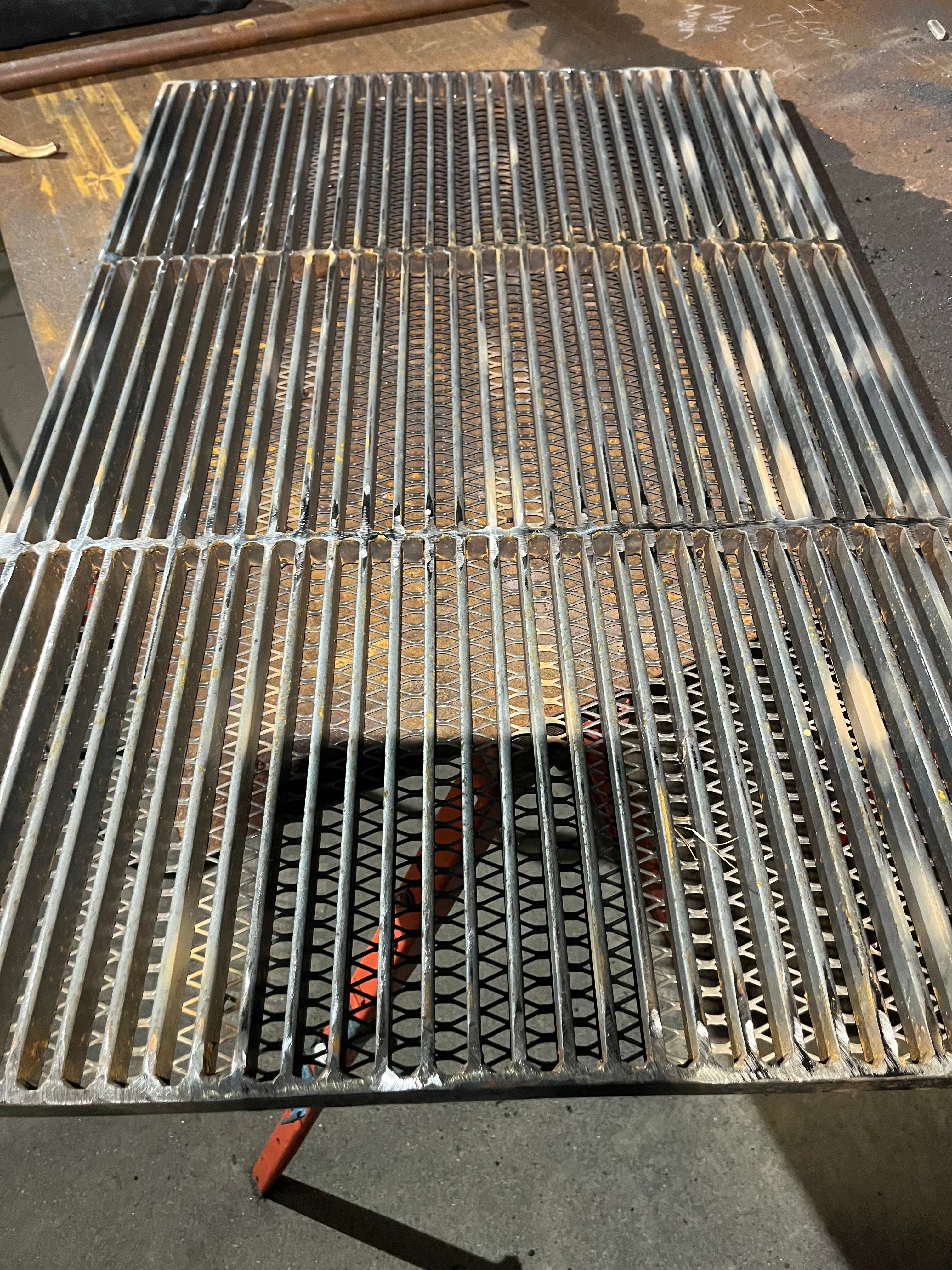
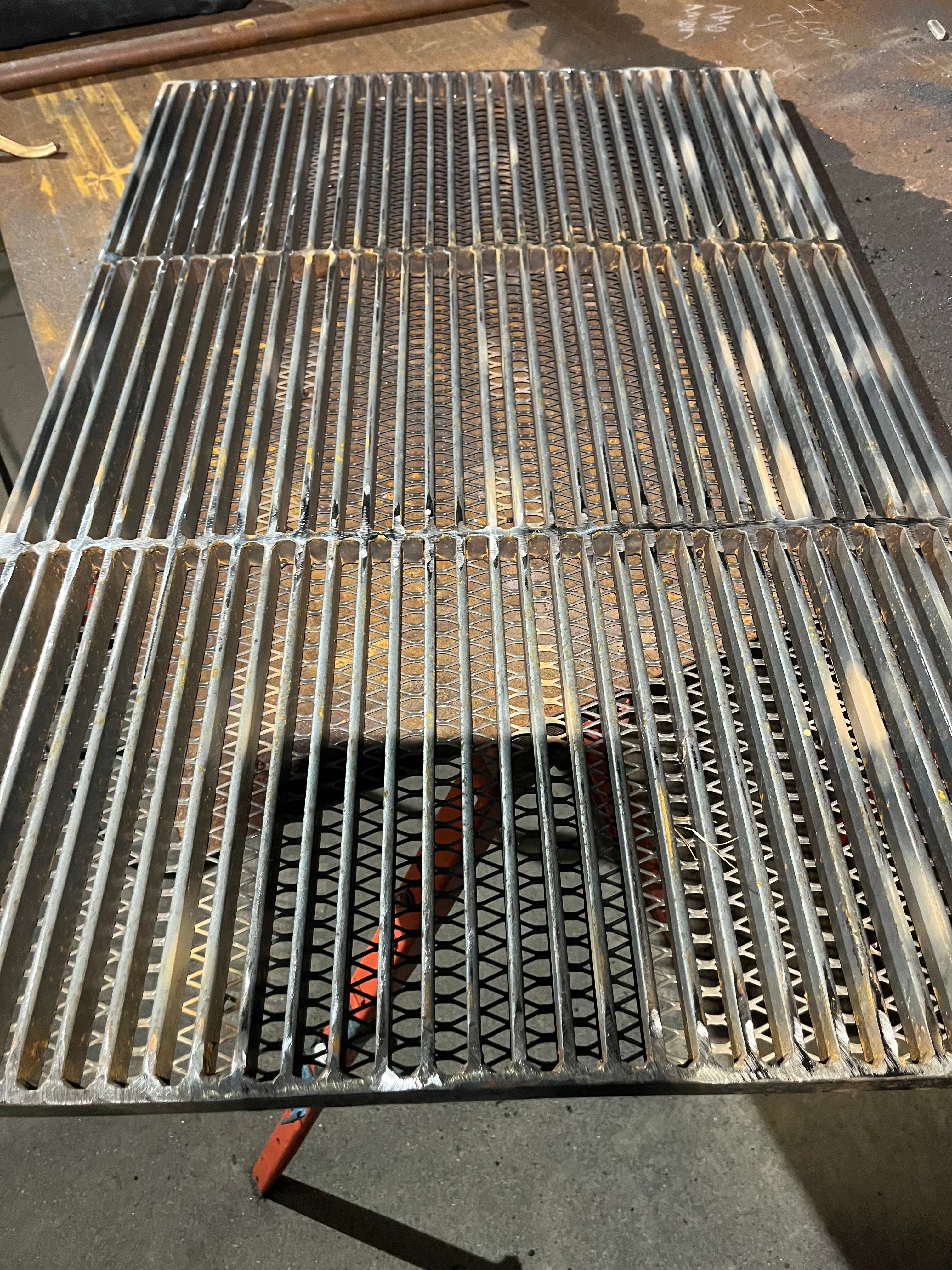
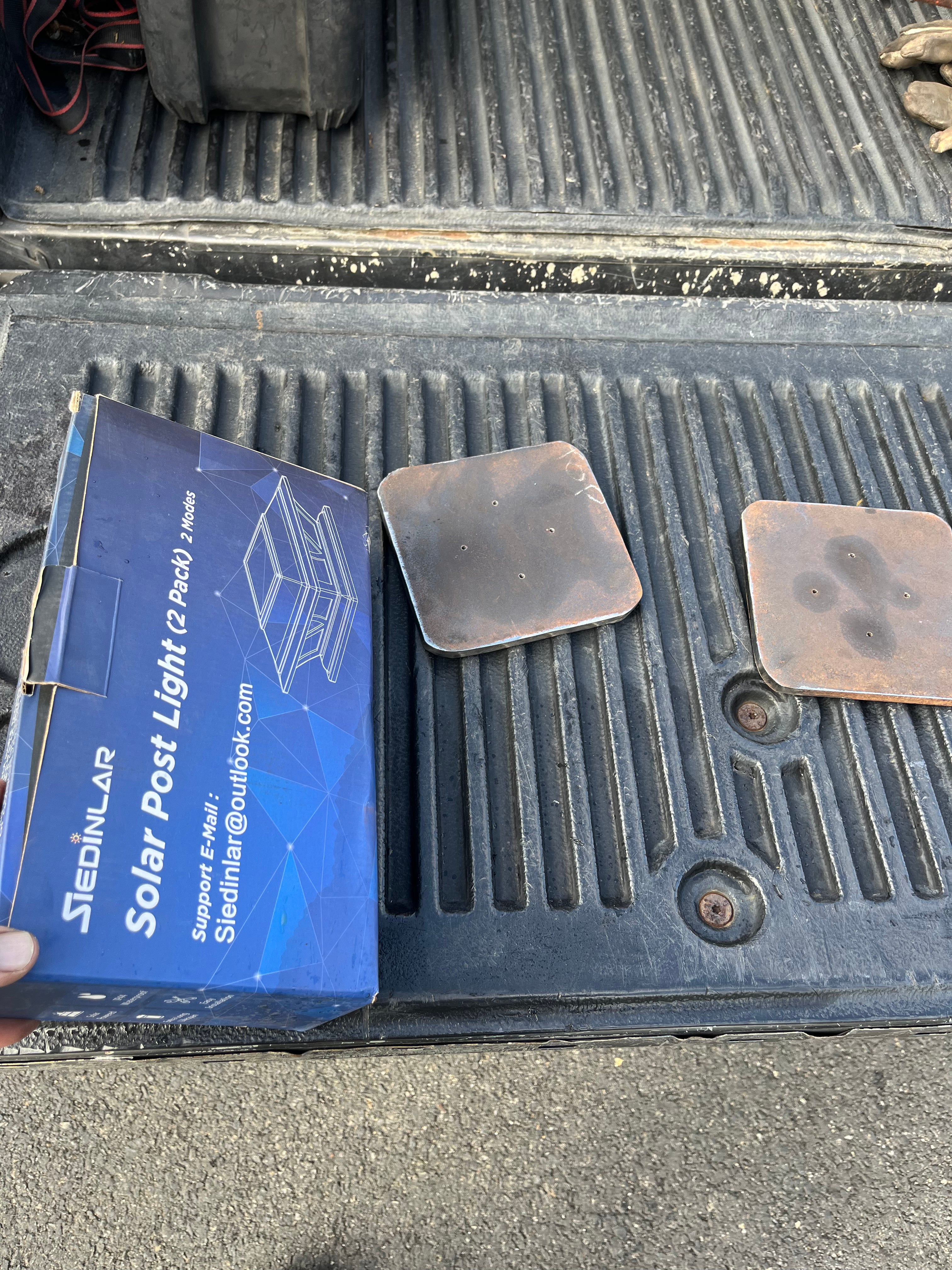
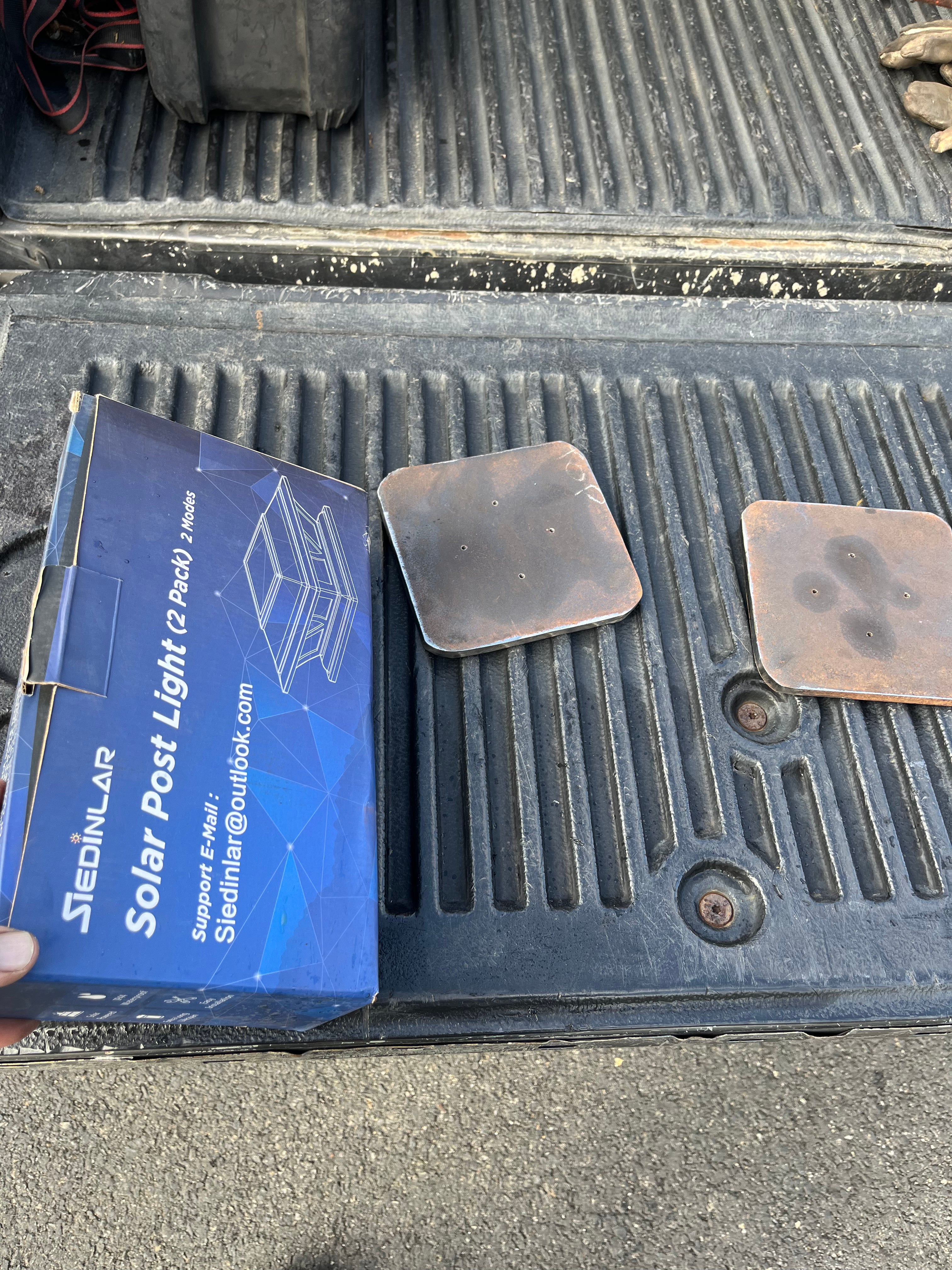
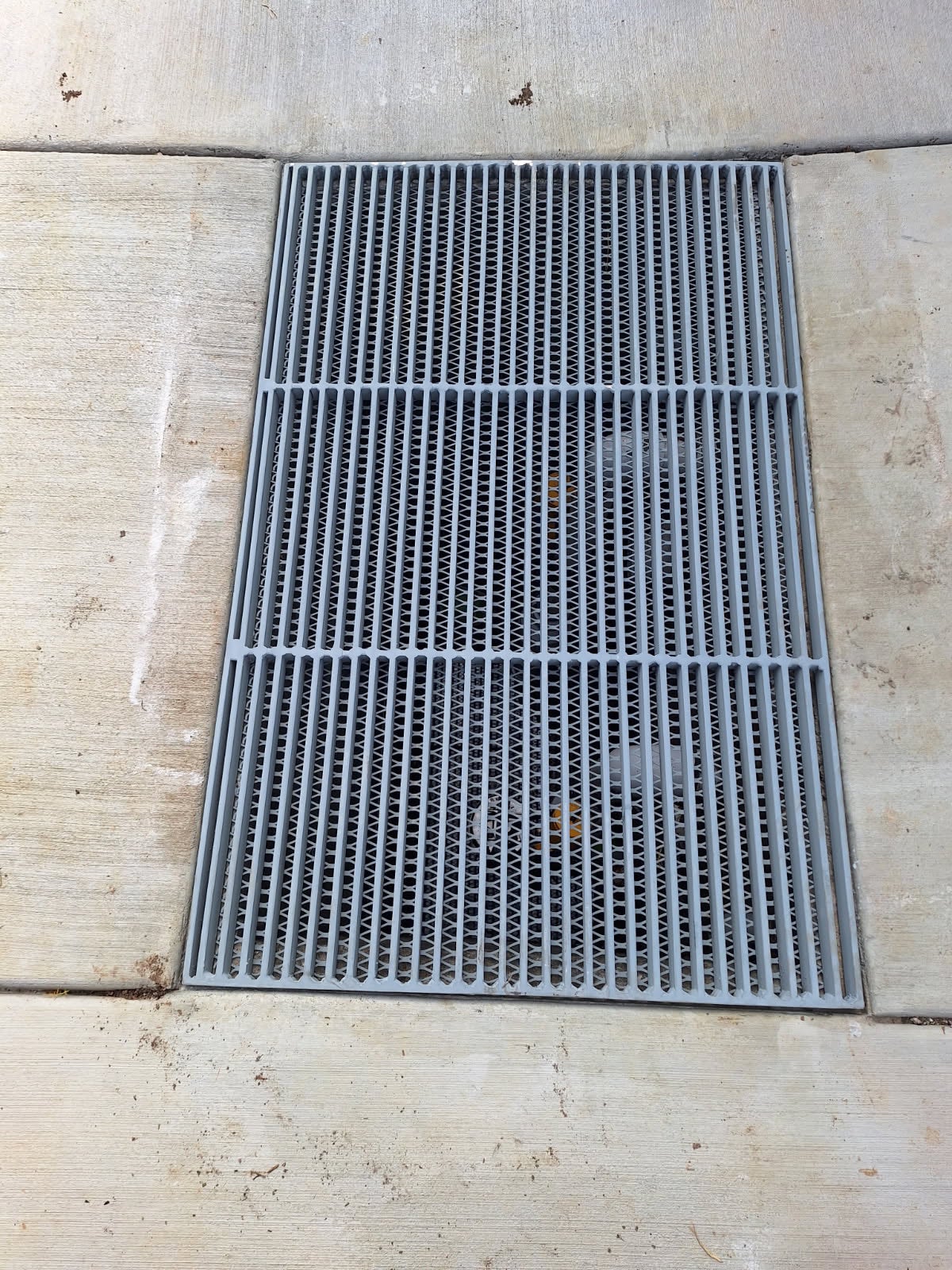
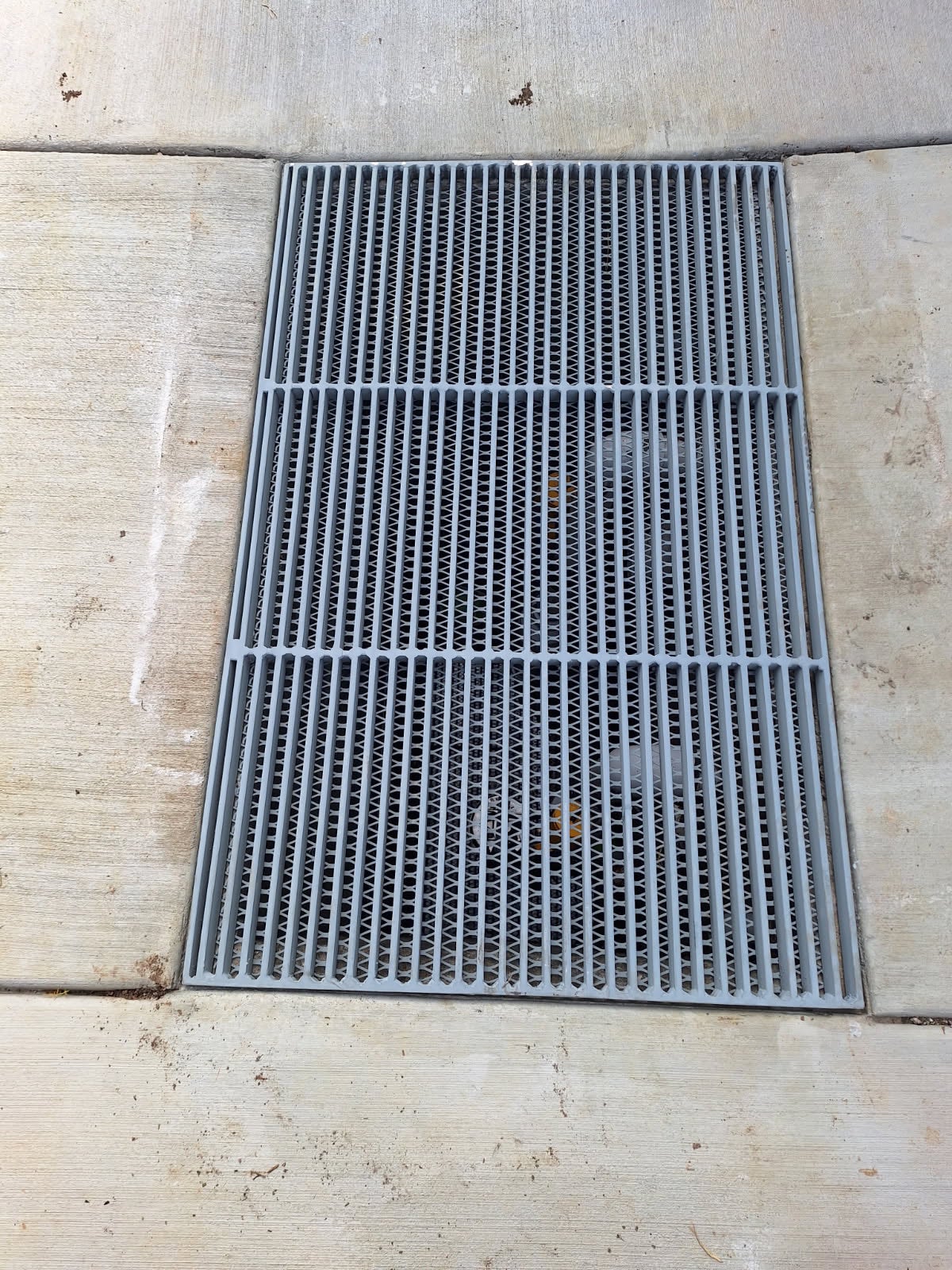
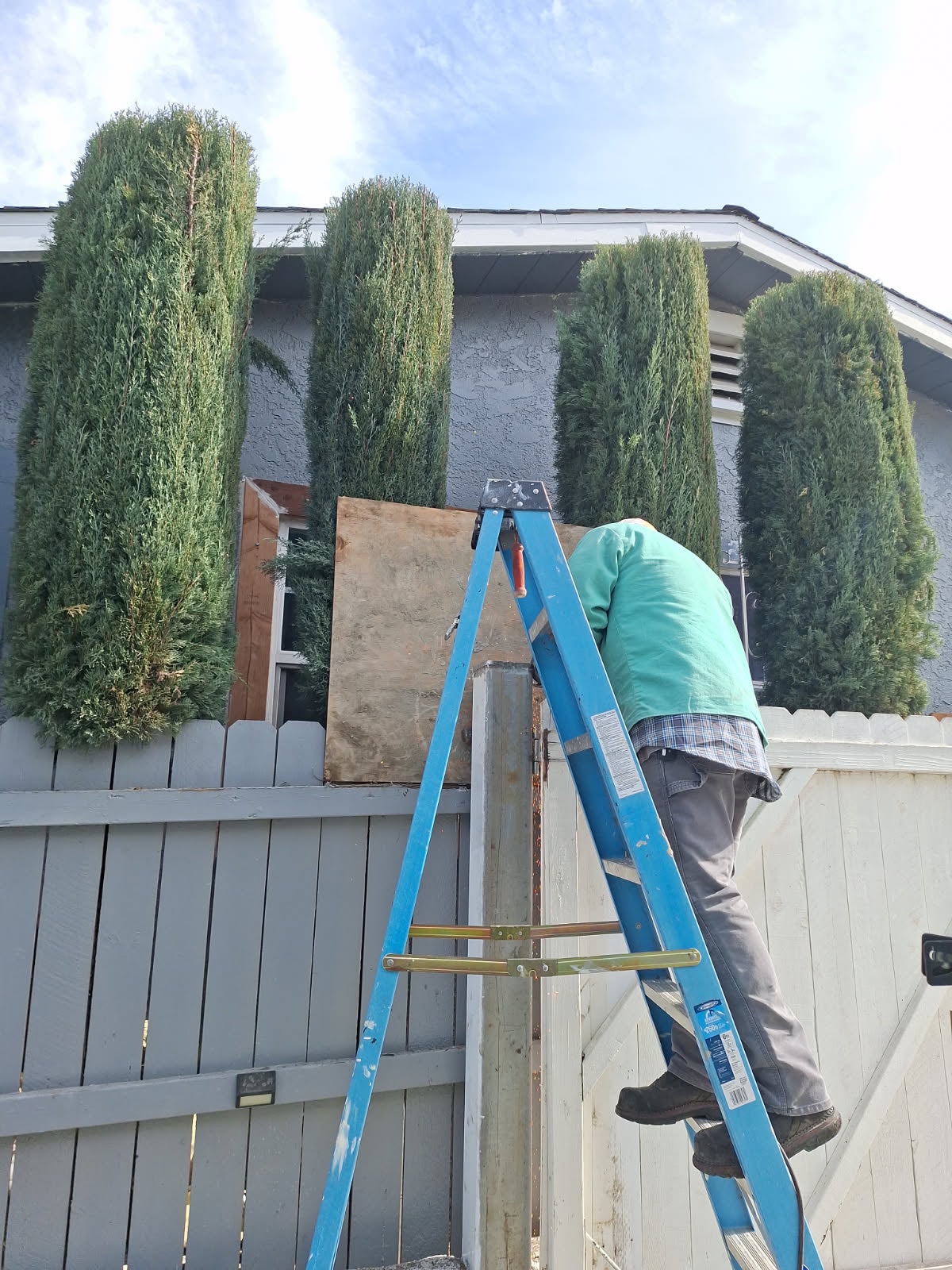
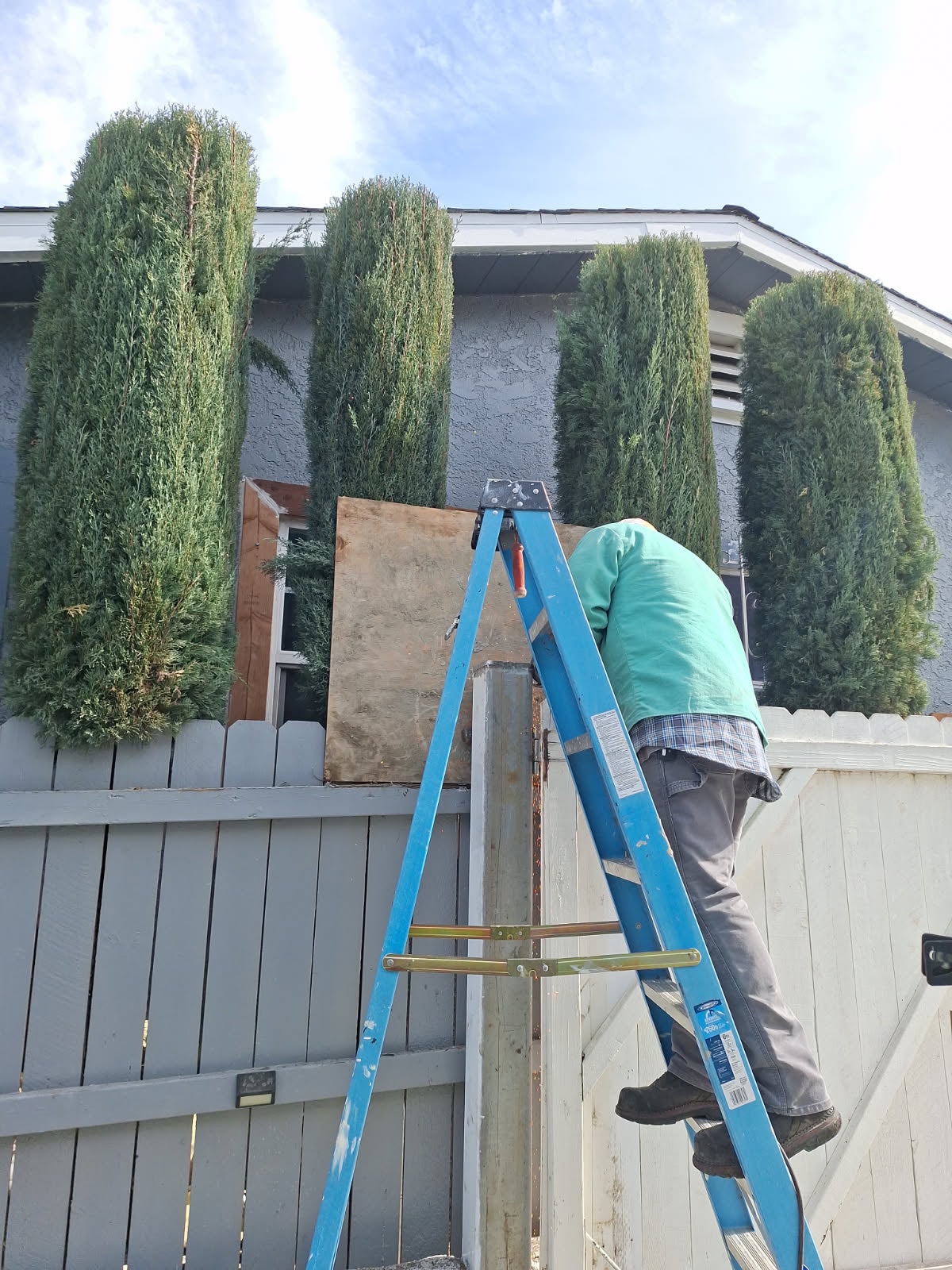
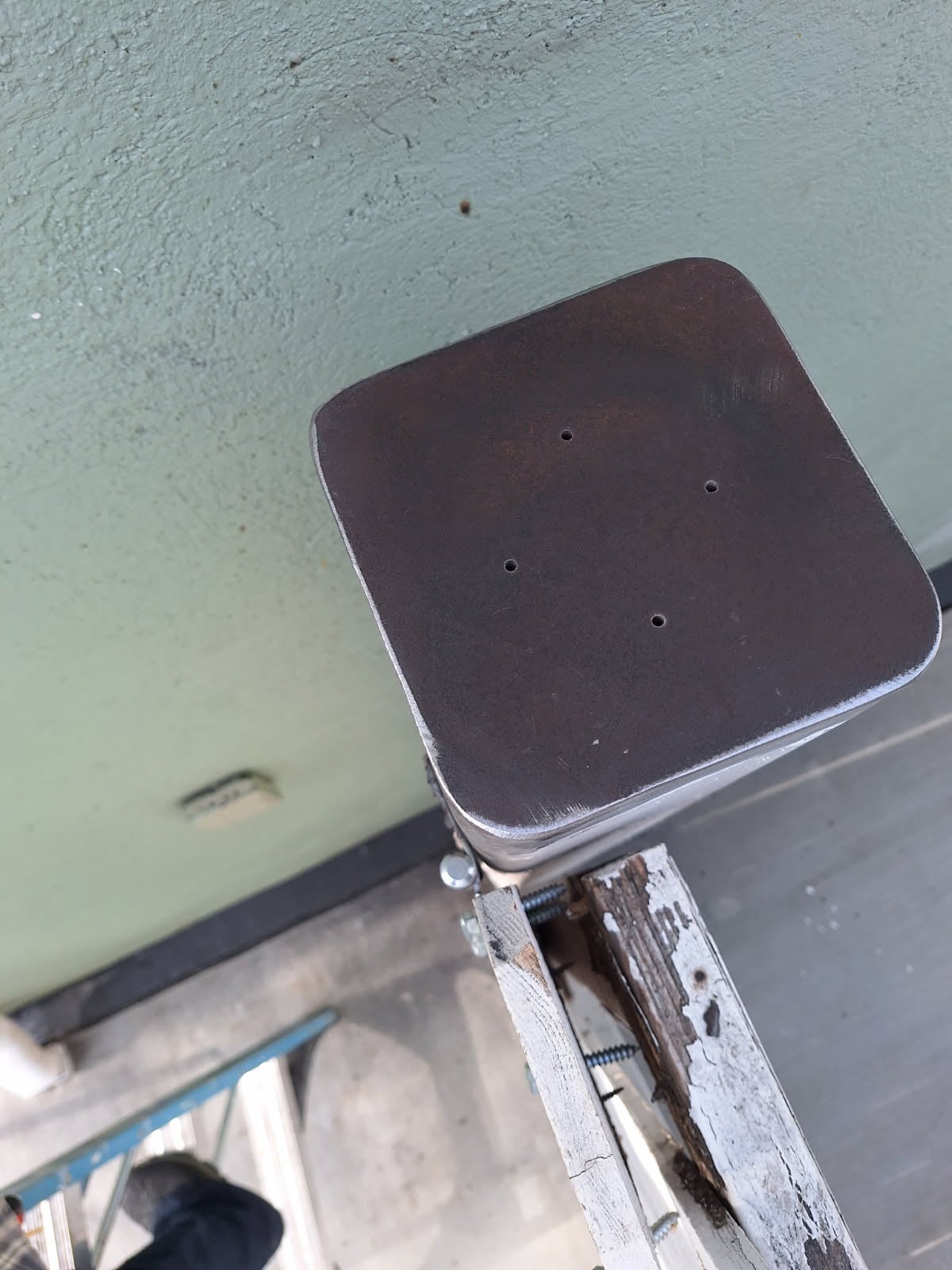
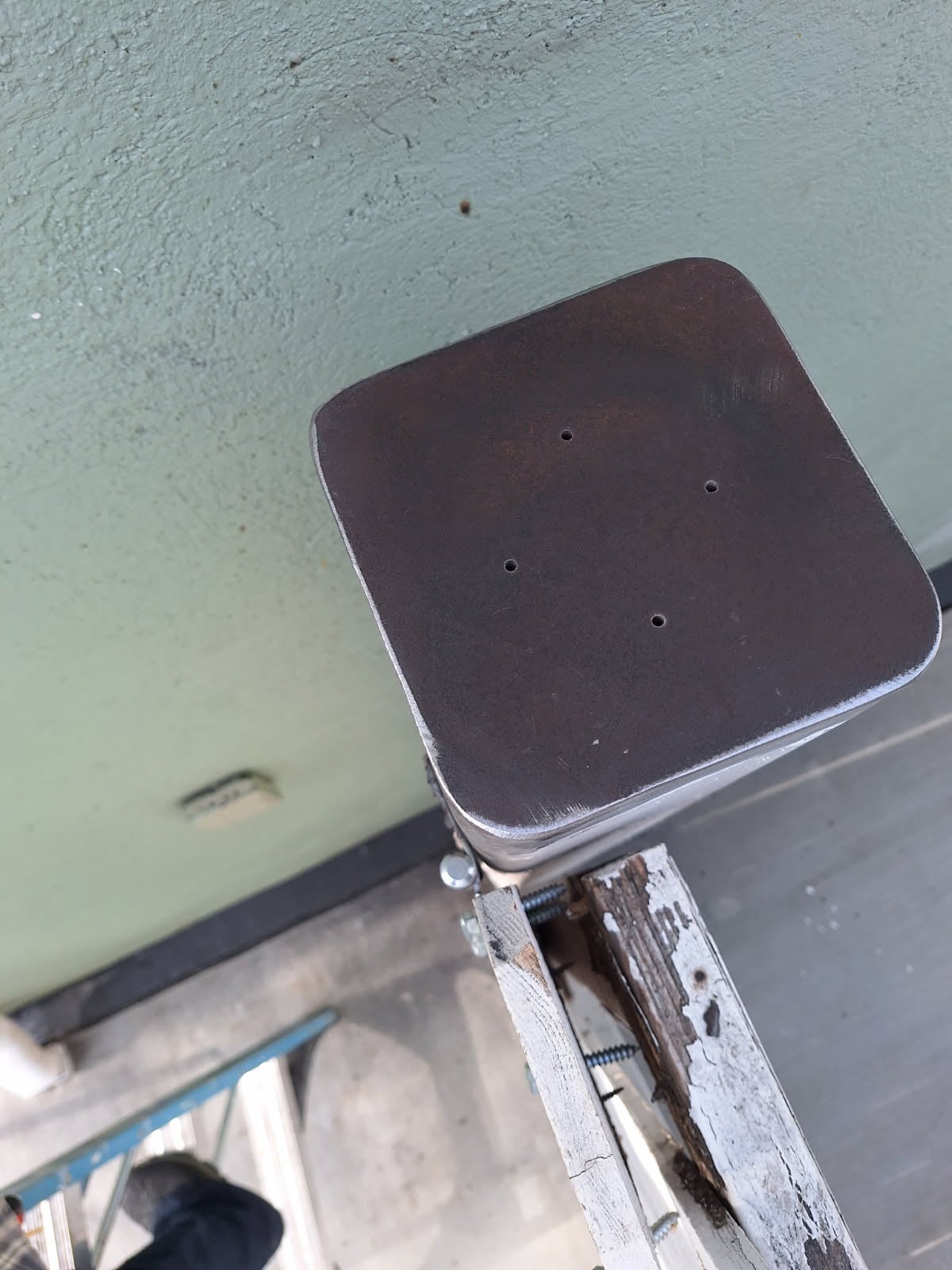
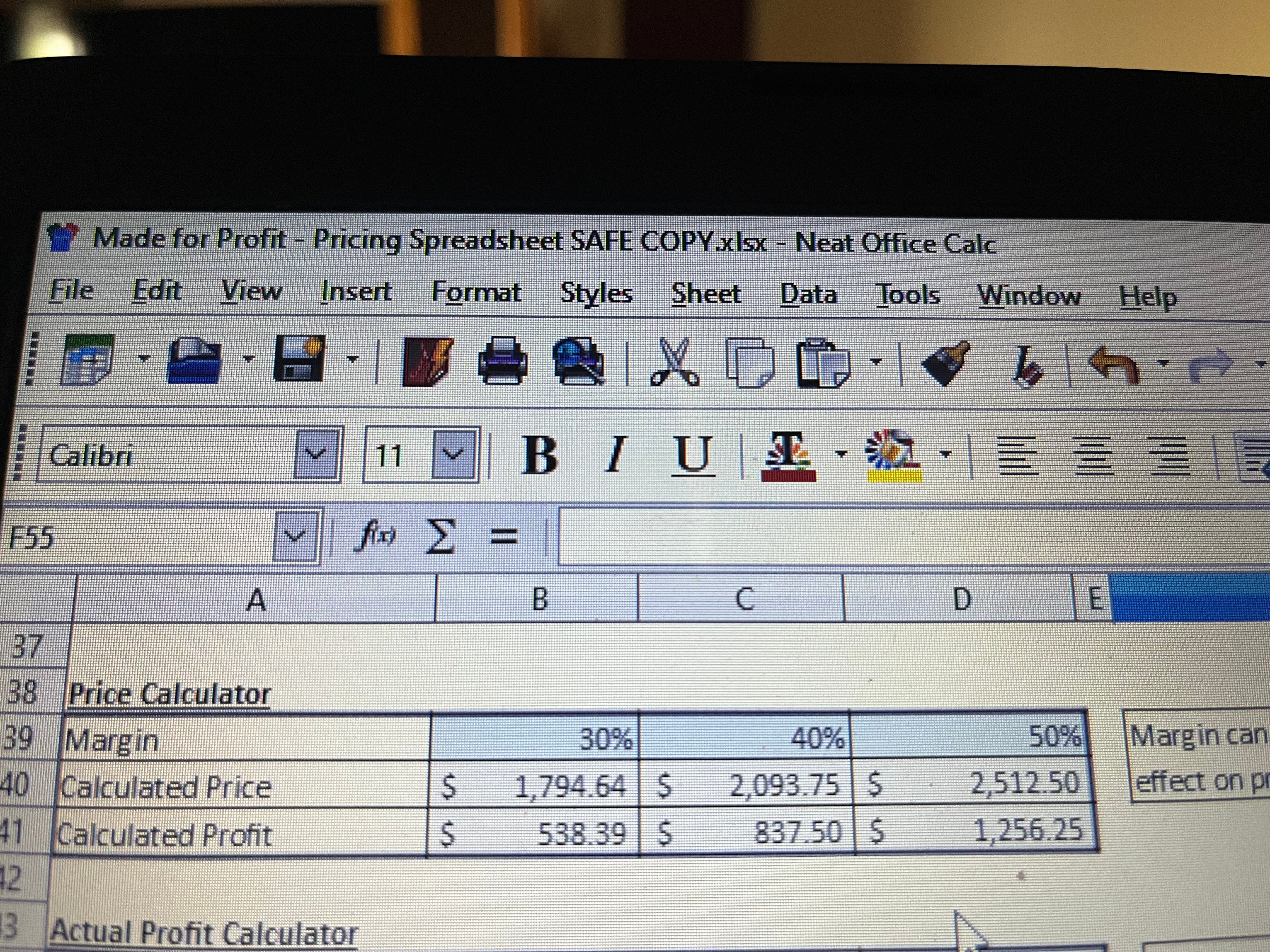
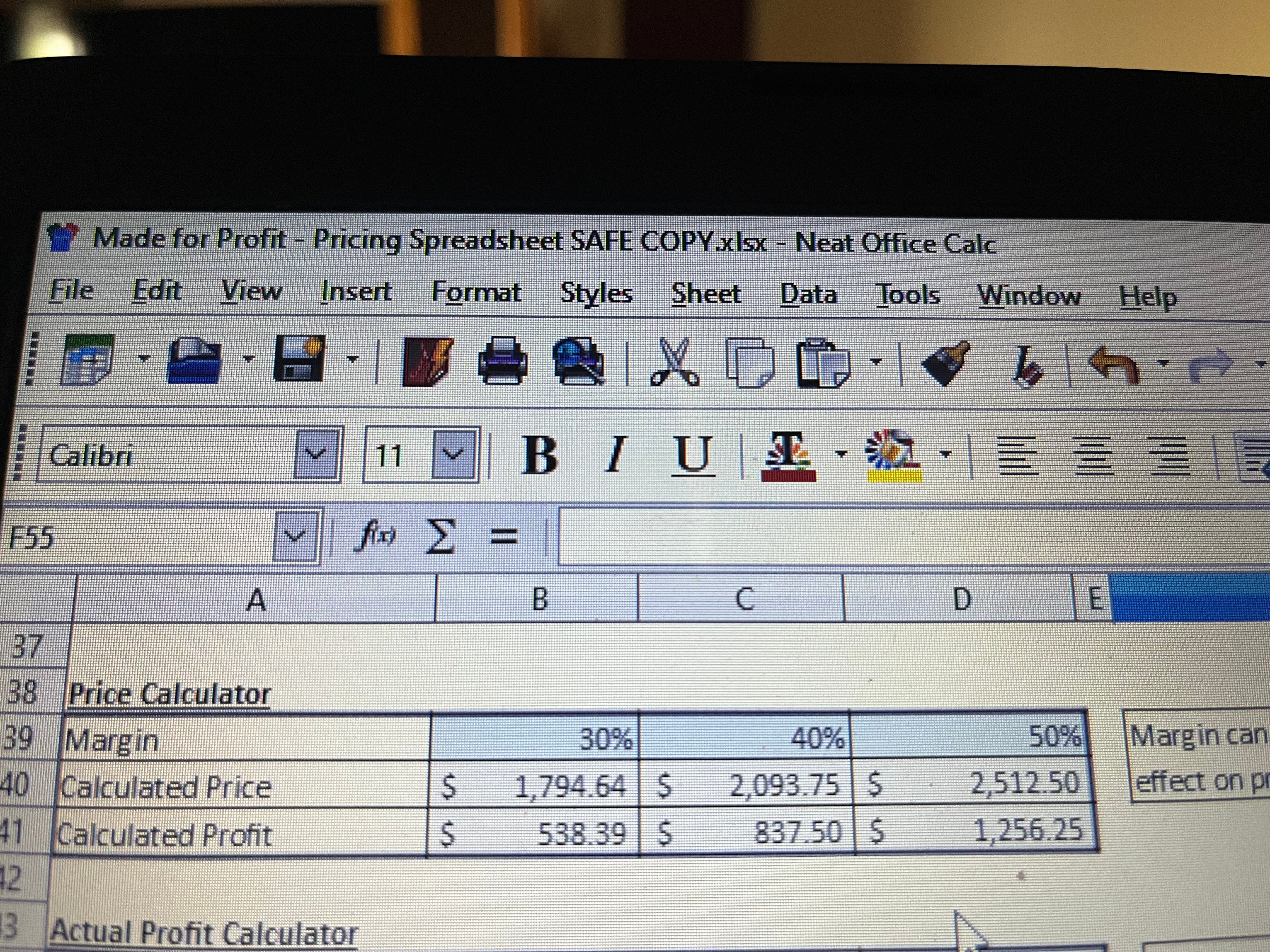
Just finished this little project building a grate for a sump pit and two caps for fence post. I couldn’t find the grate big enough to cover the hole in one piece, plus the customer asked for a screen to keep leaves out. I decided to just build one. After deciding to use flat bar instead of tubing I was able to plug in all numbers in a excel spreadsheet format I purchased from a guy @ a website “MADE FOR PROFIT “ and was able to quote the job at a 40% margin. I do this on my spare time by with these numbers I wanna do more .
The tools I used are mine , the leads are mine and the welder I used was station at my house , but when it came to being mobile, I got one from the the rental yard for 75$ a day.
I think I’ll hold off buying my gas driven welder for now.
Posted
12 Dec 22:47
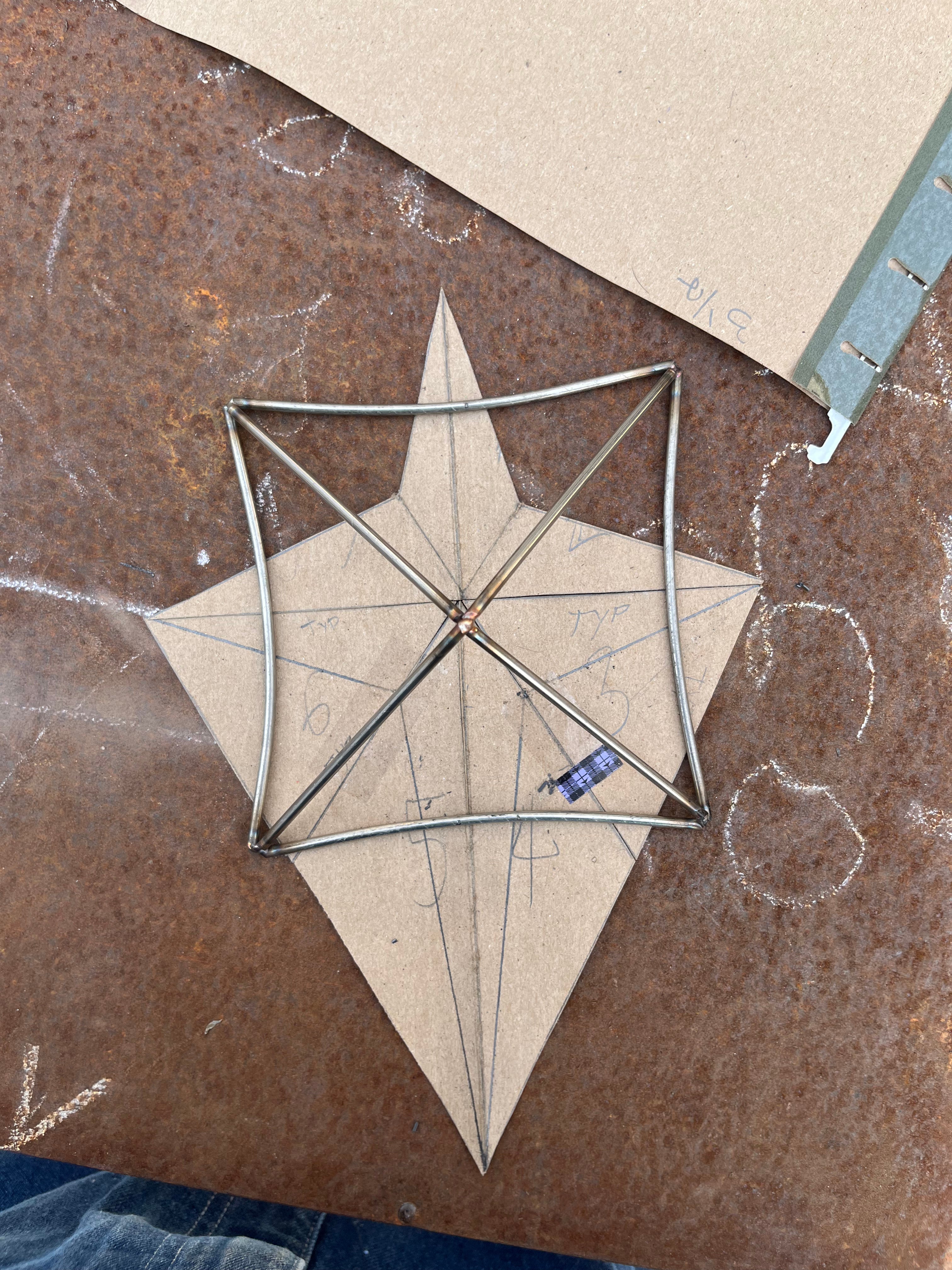
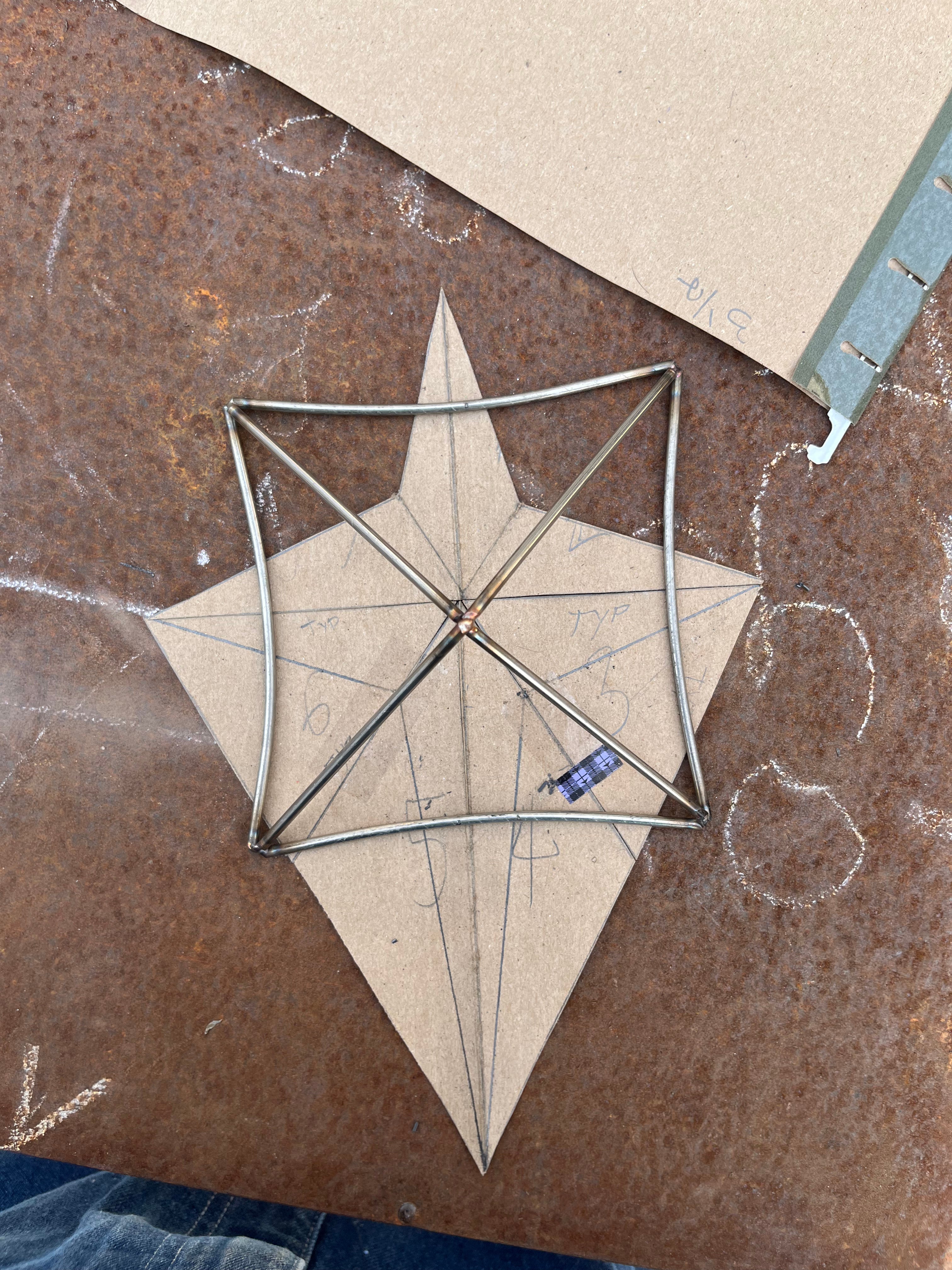
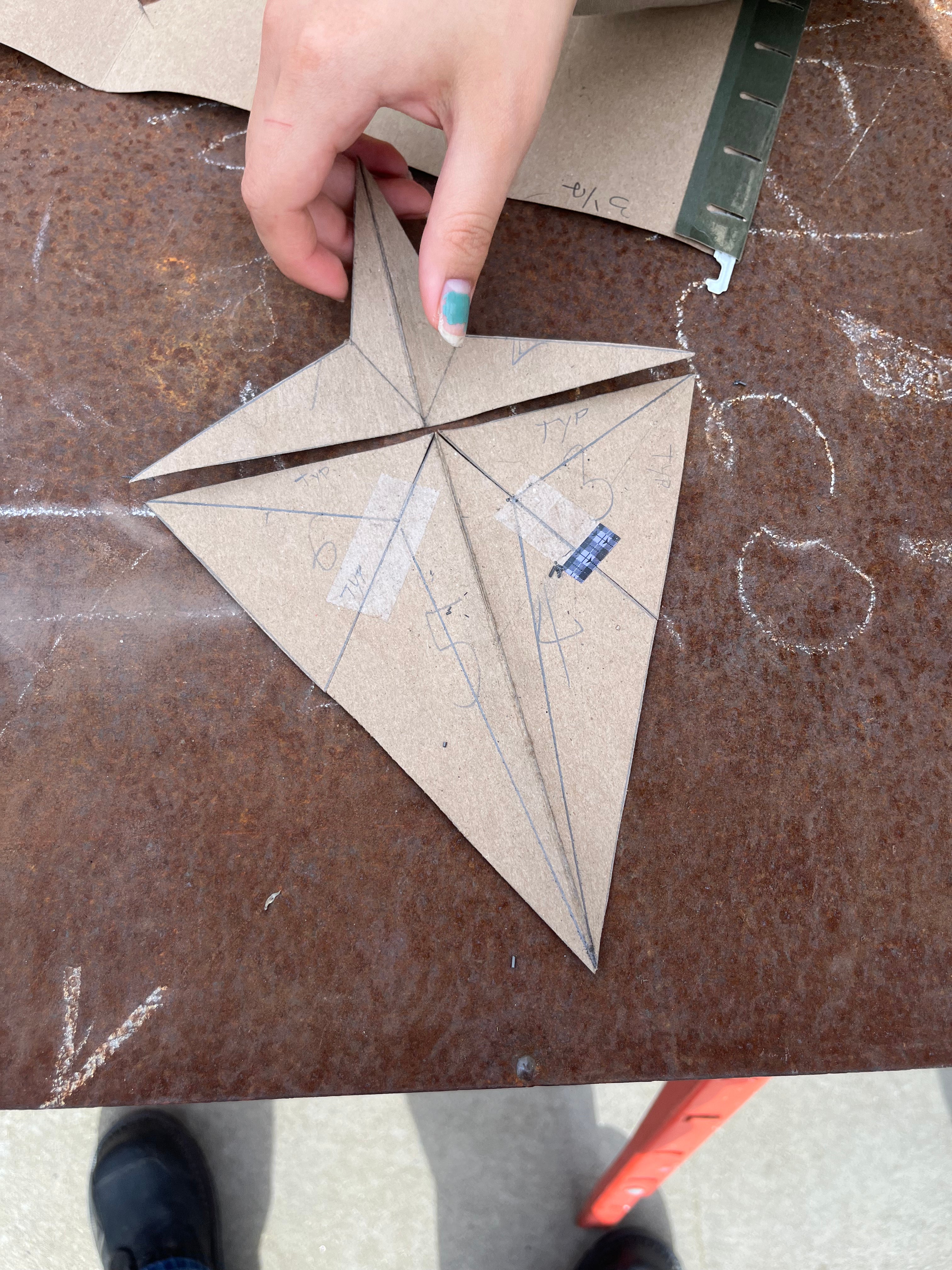
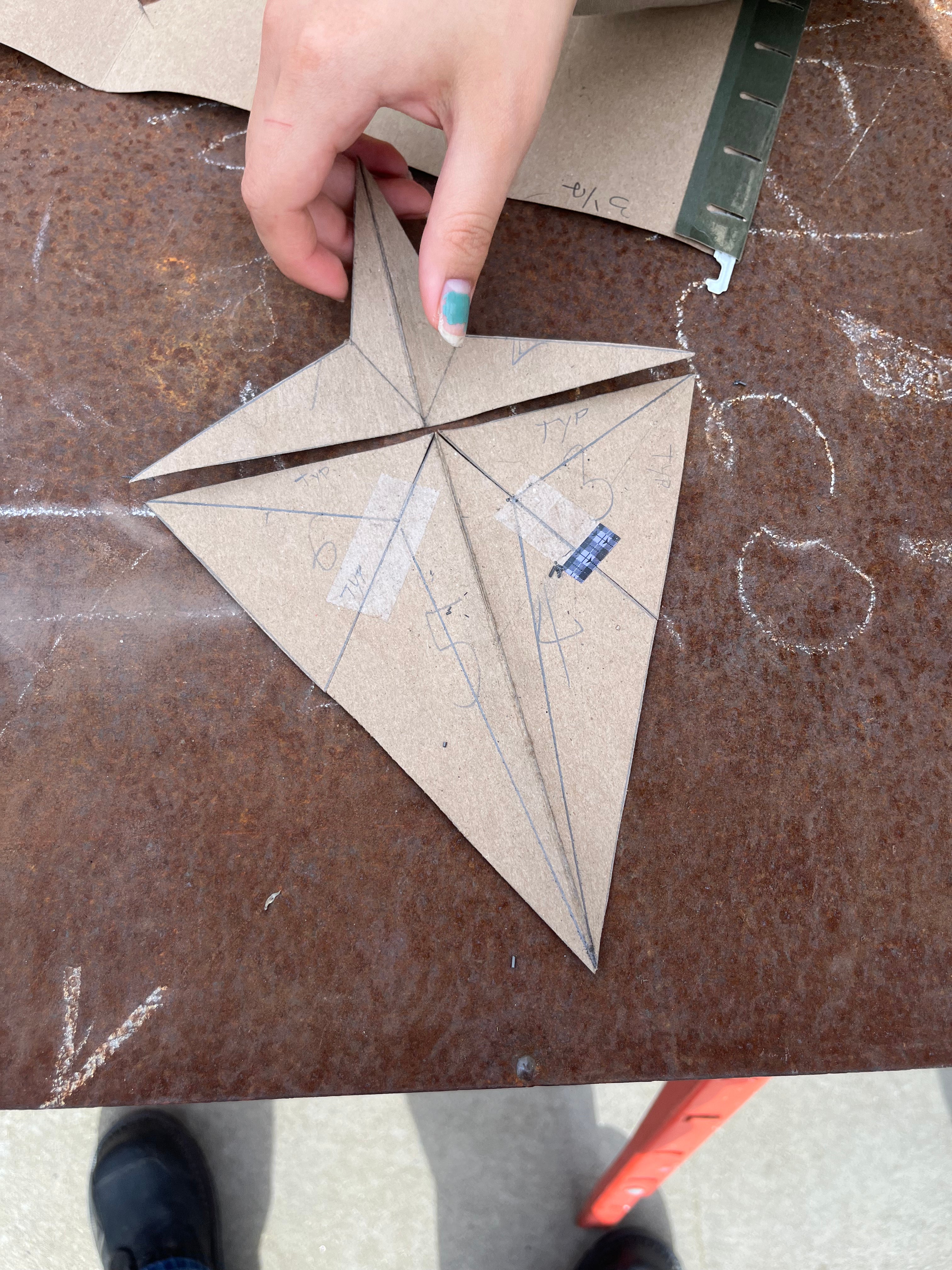
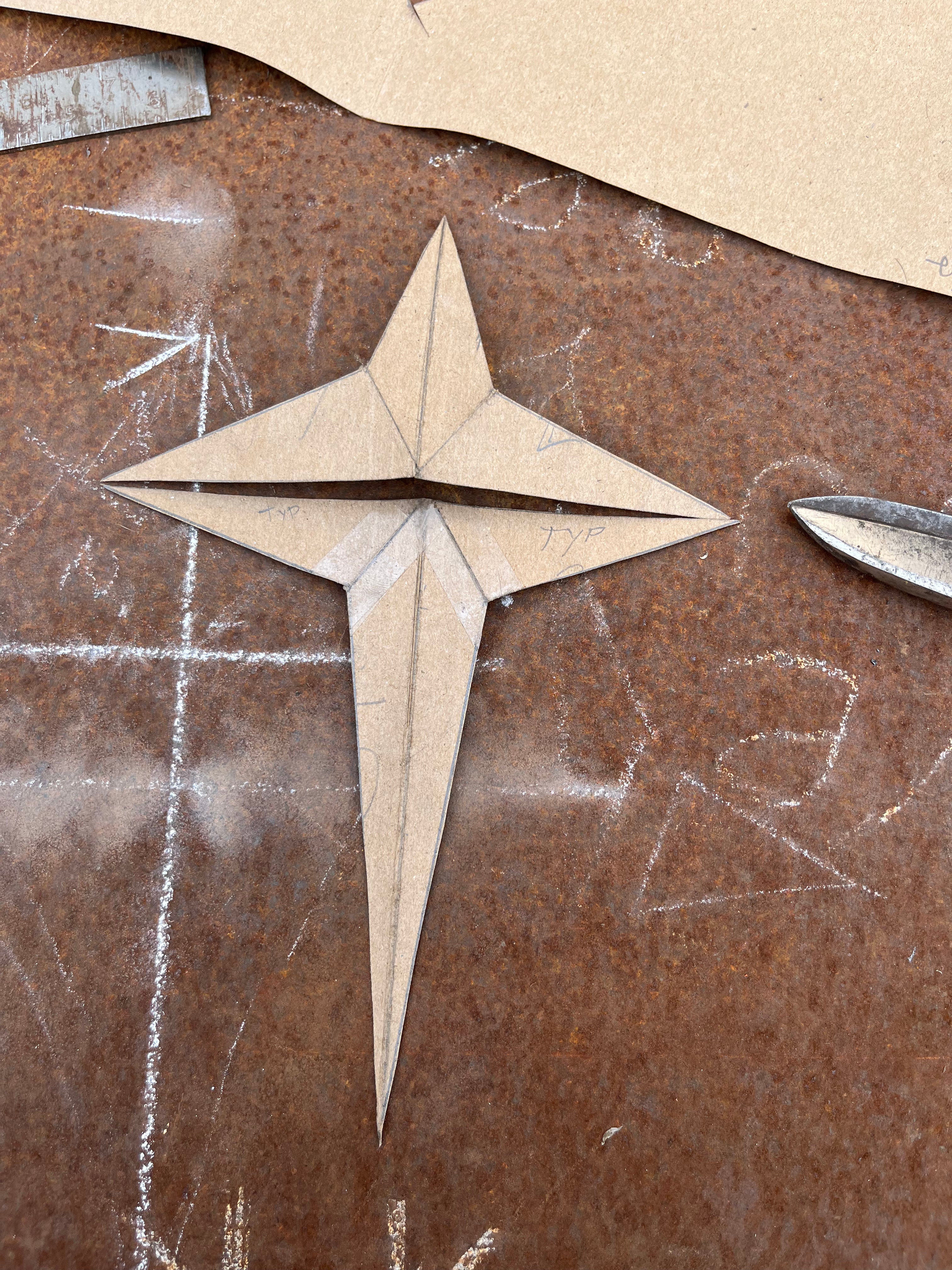
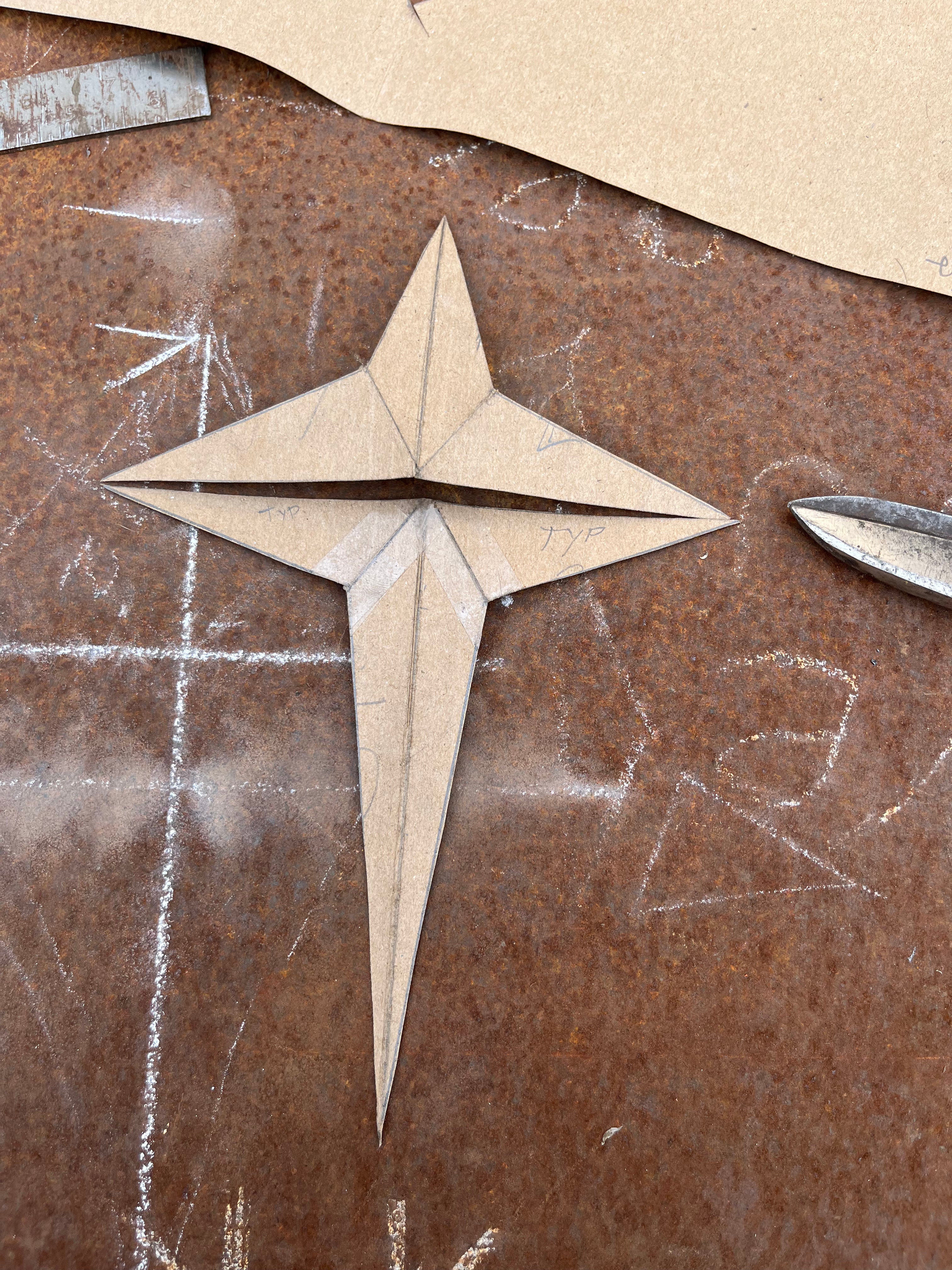
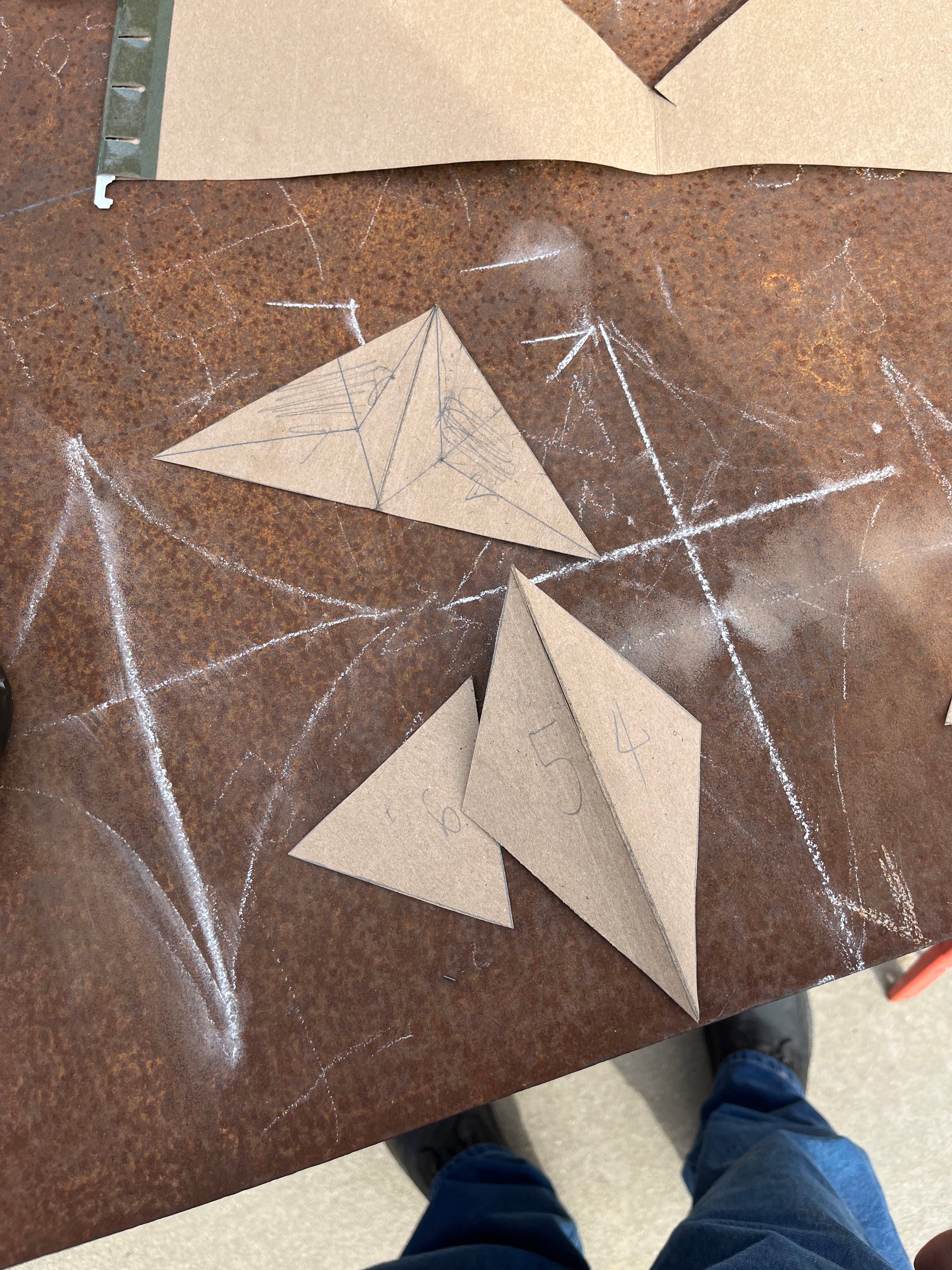
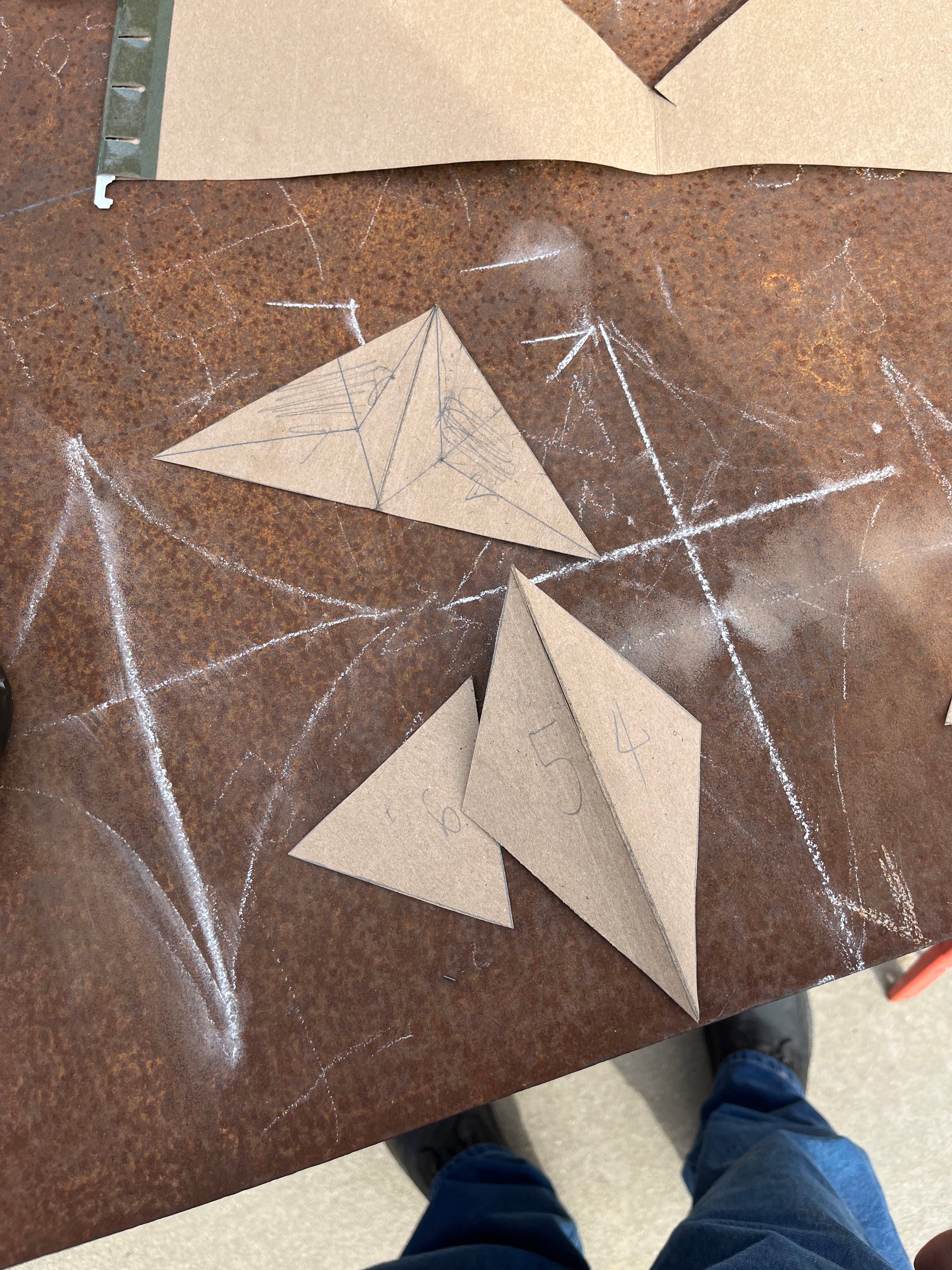
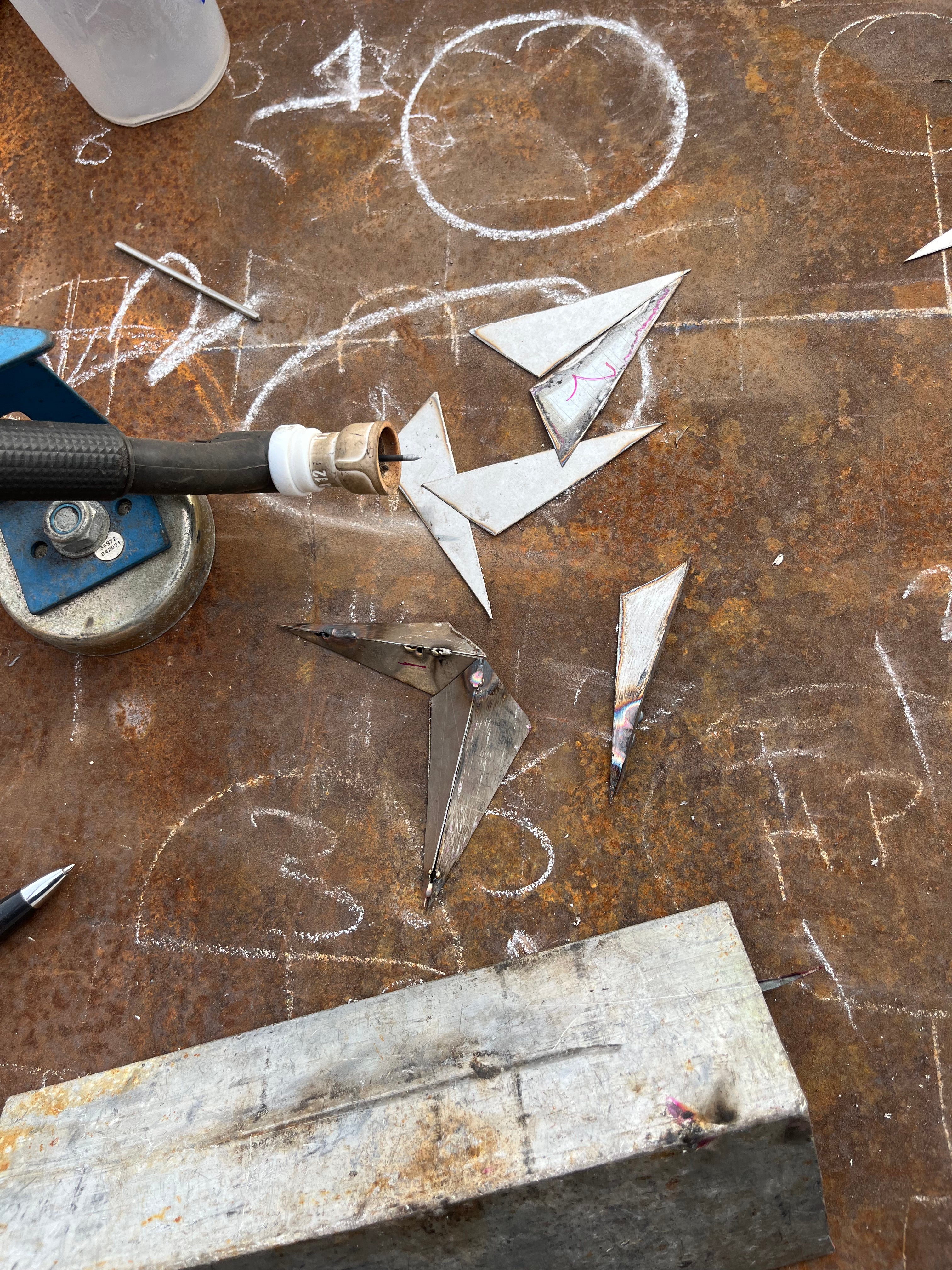
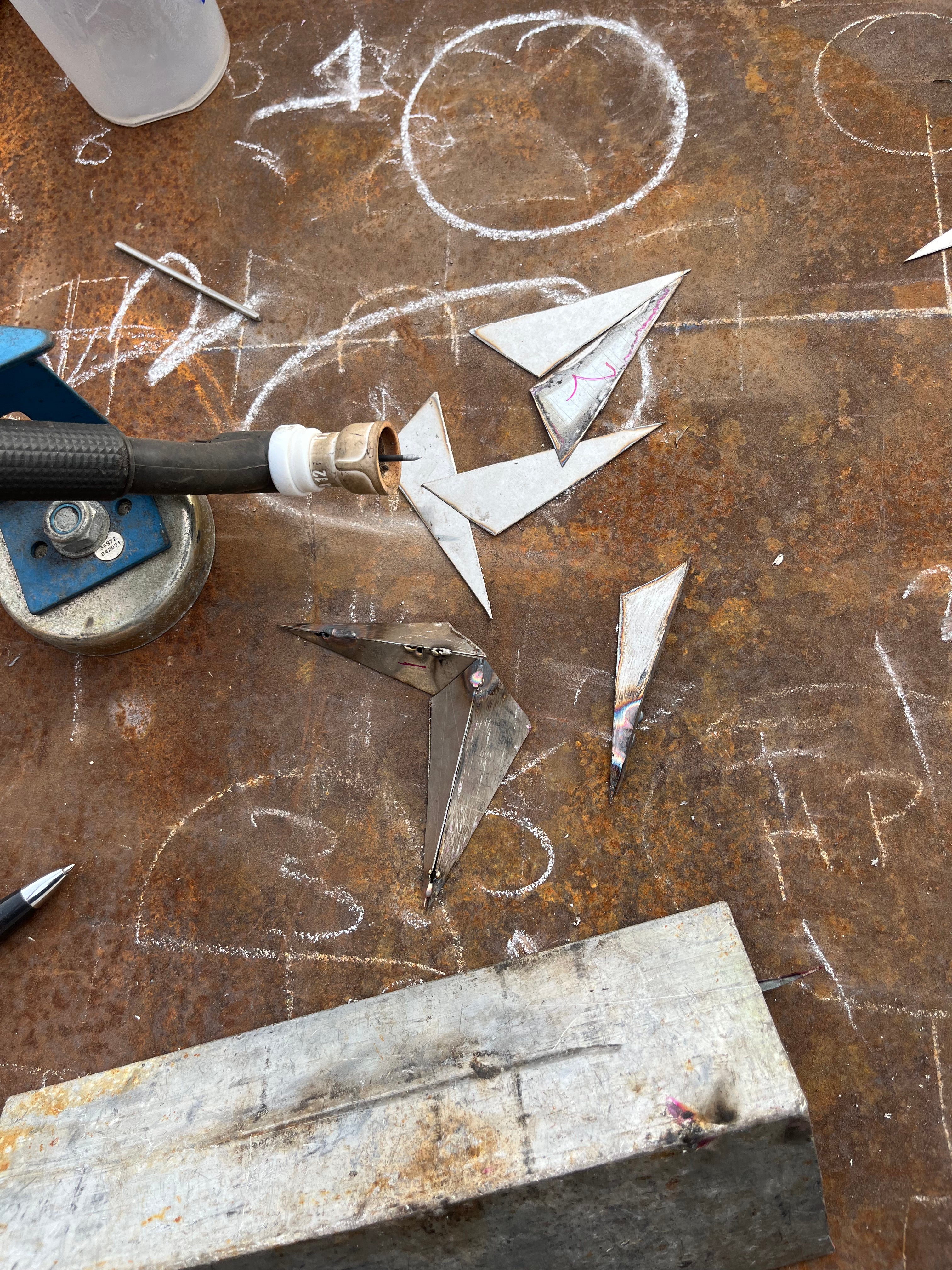
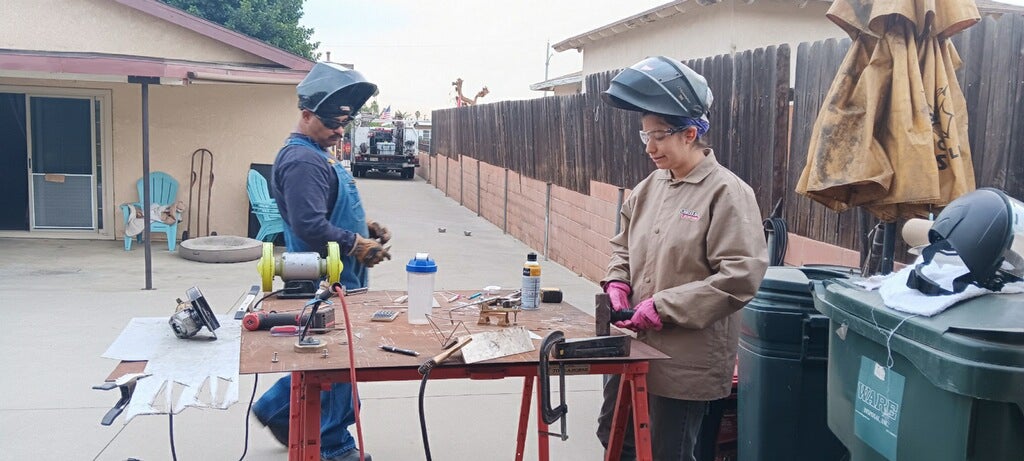
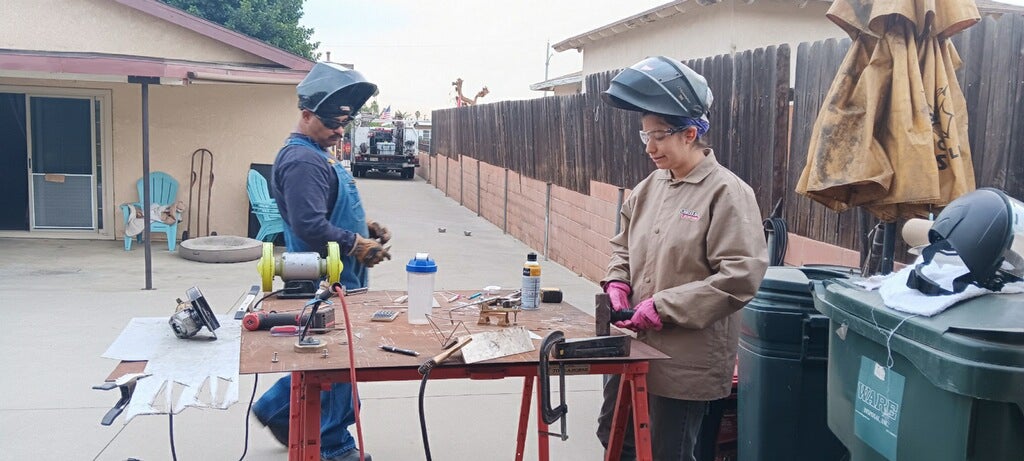
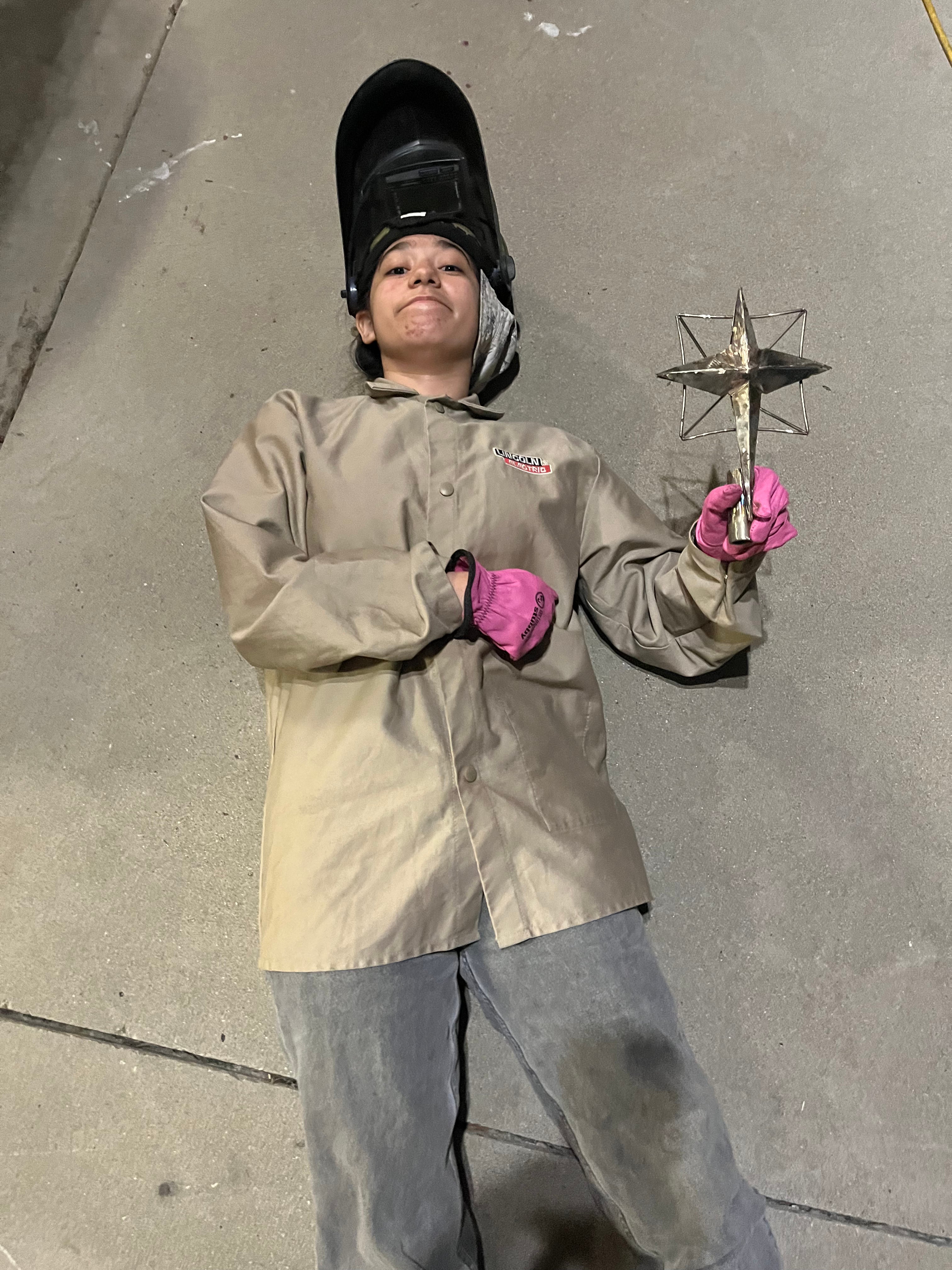
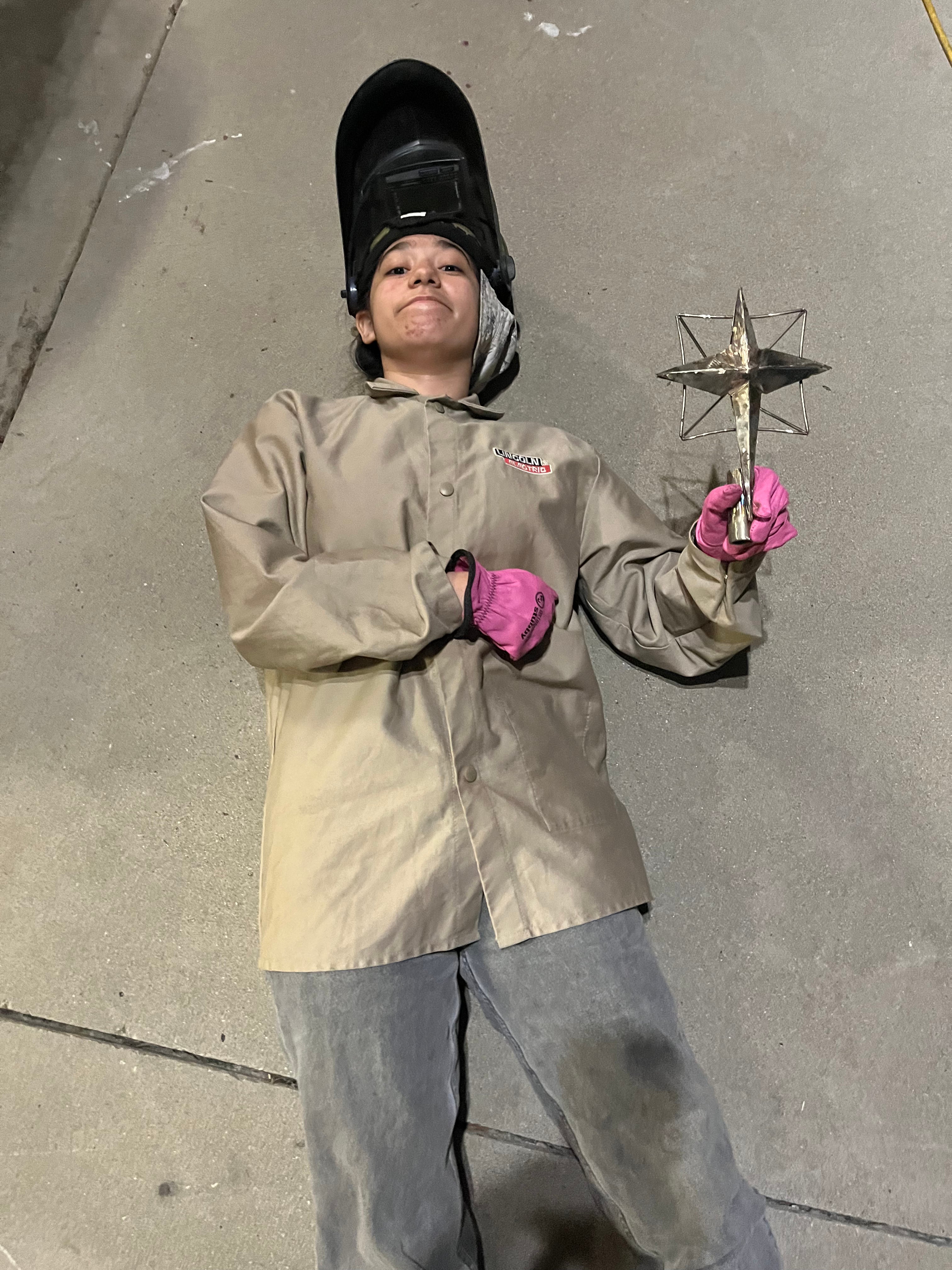
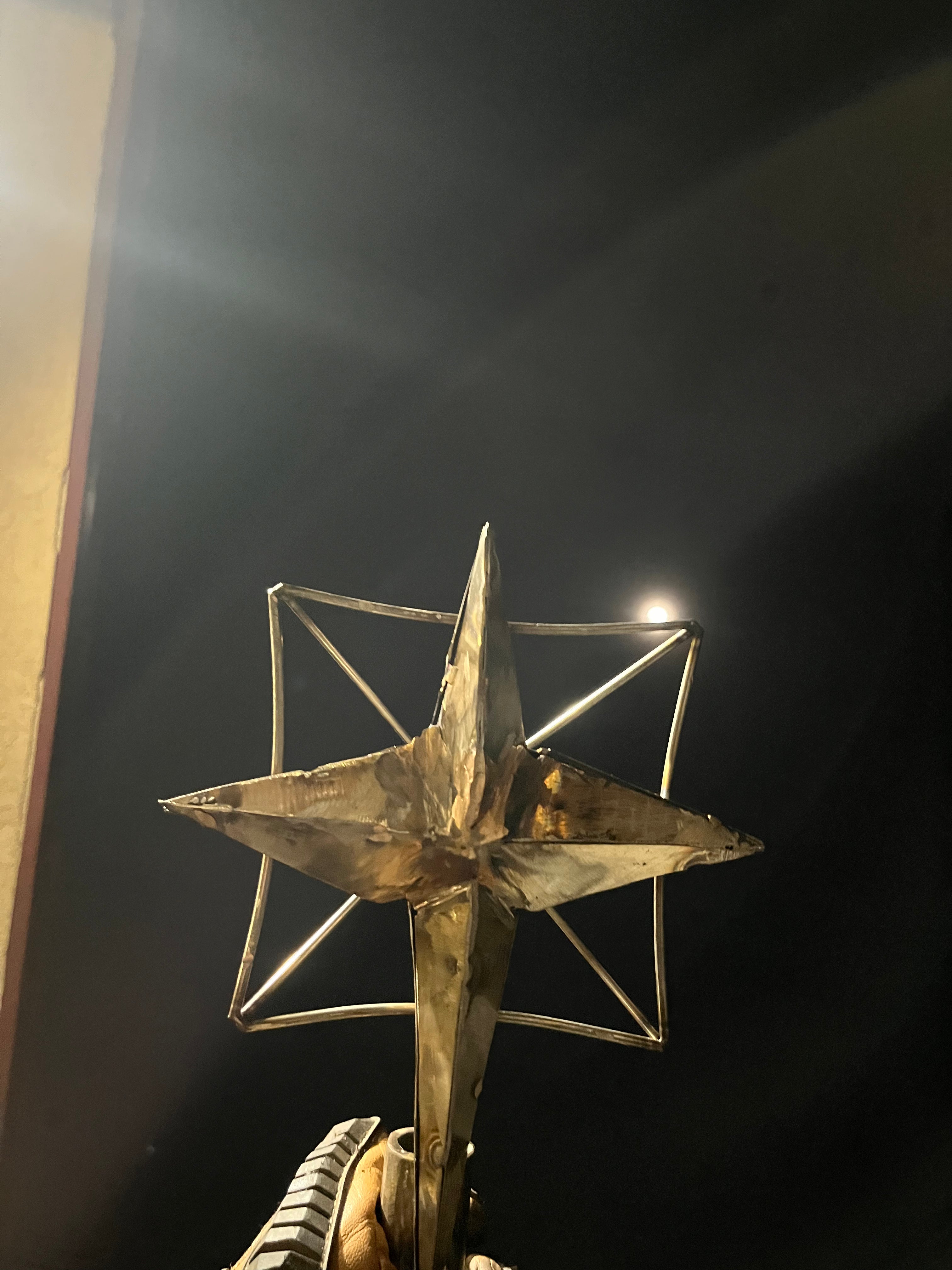
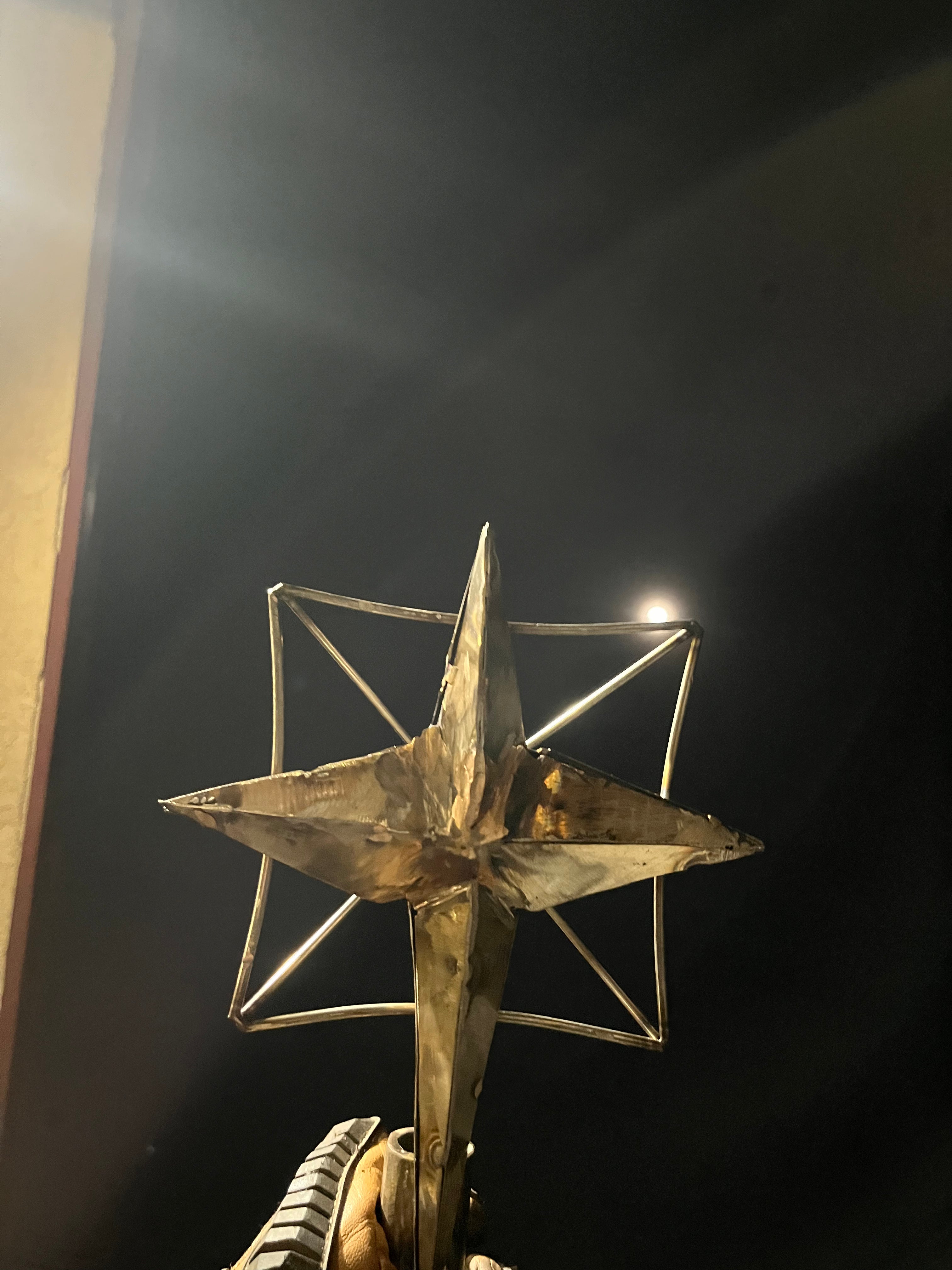
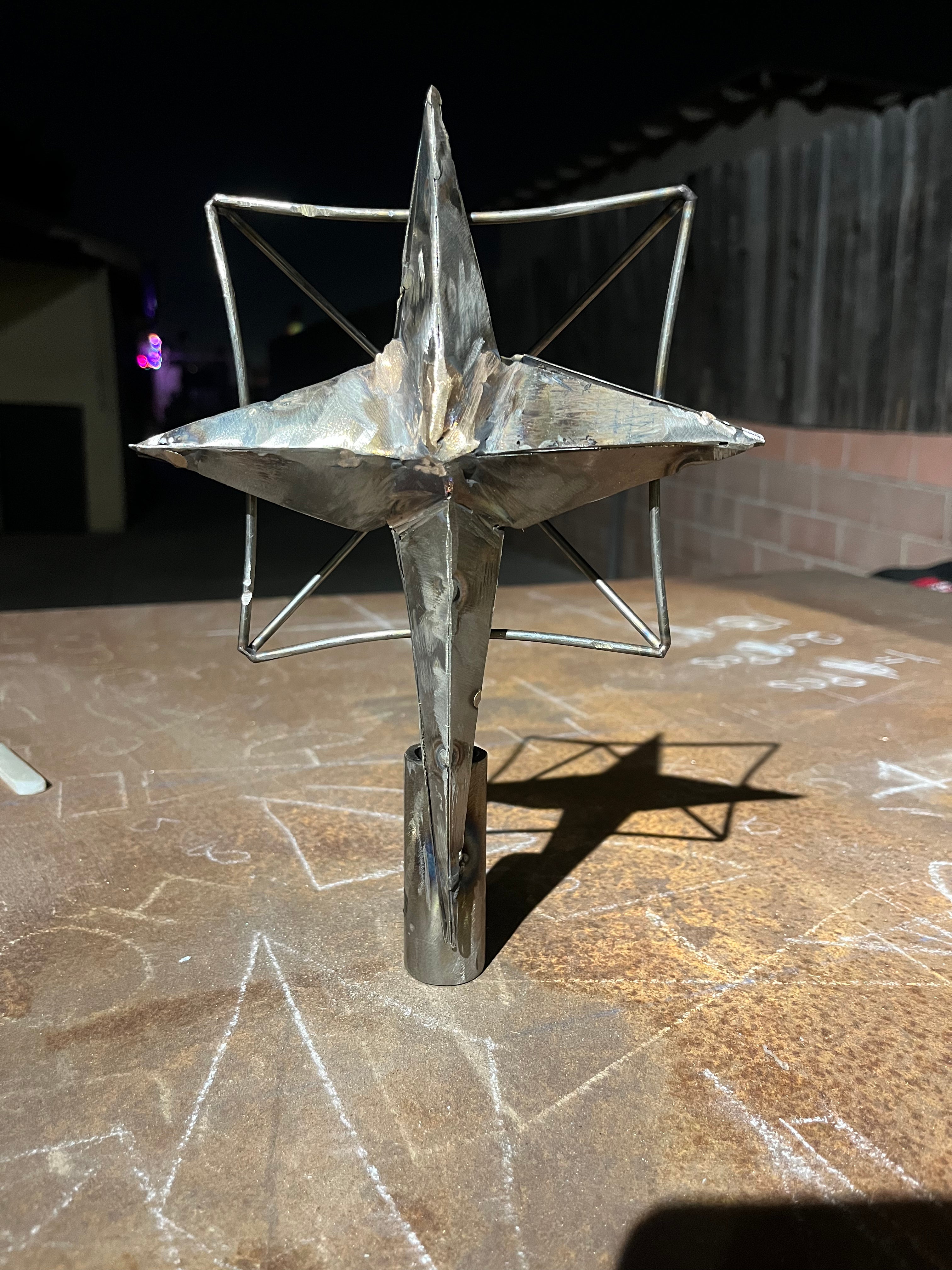
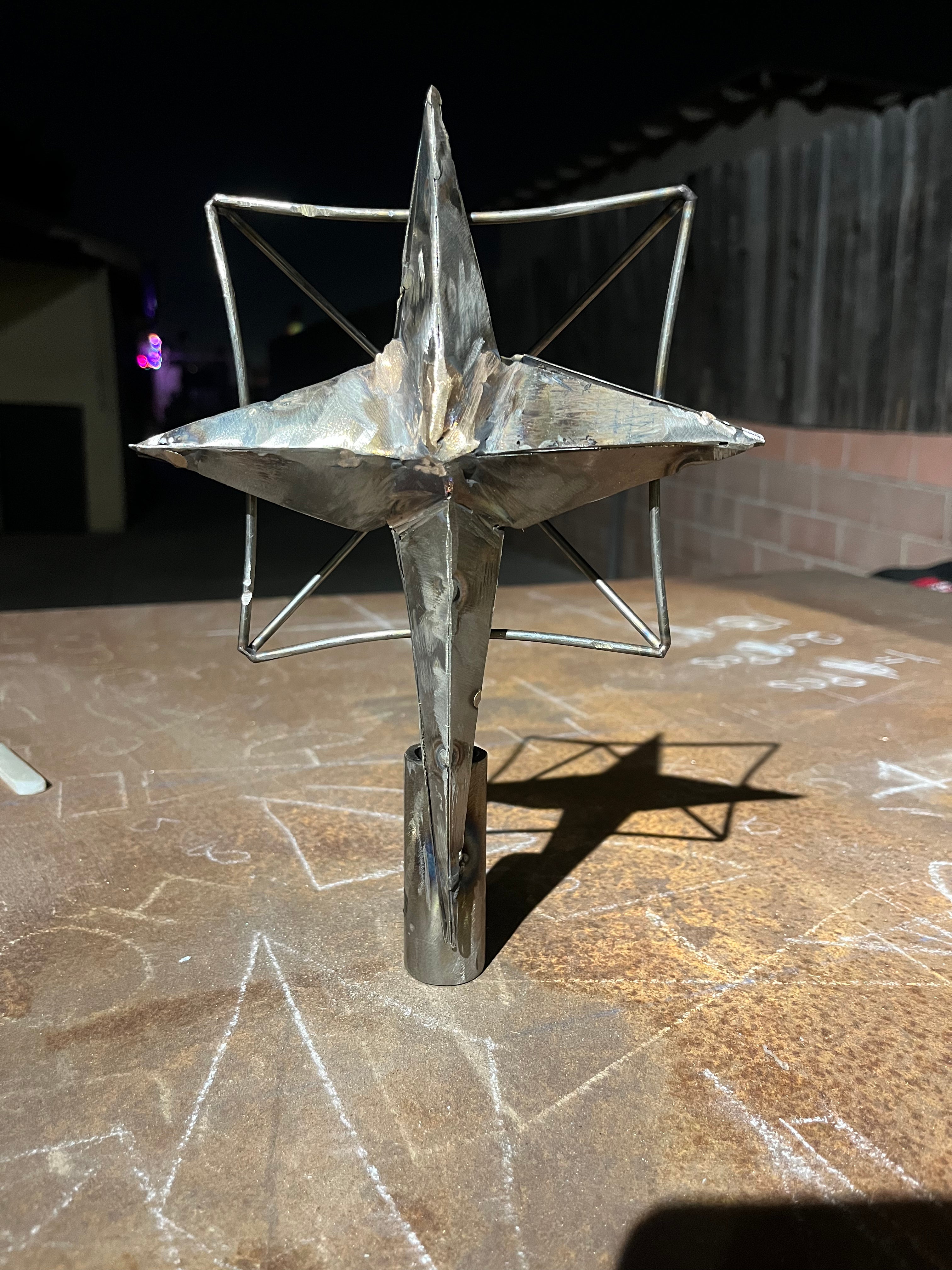
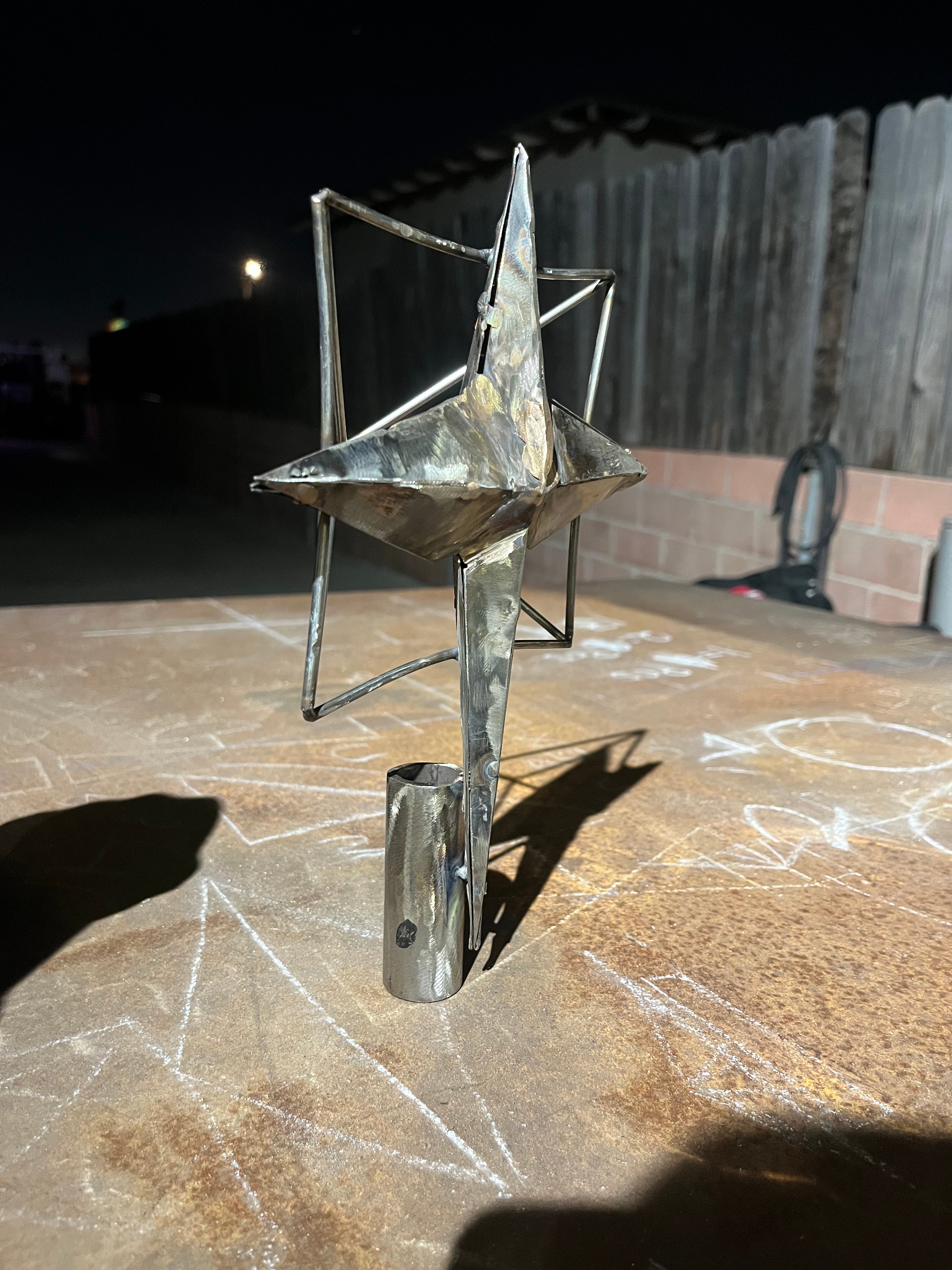
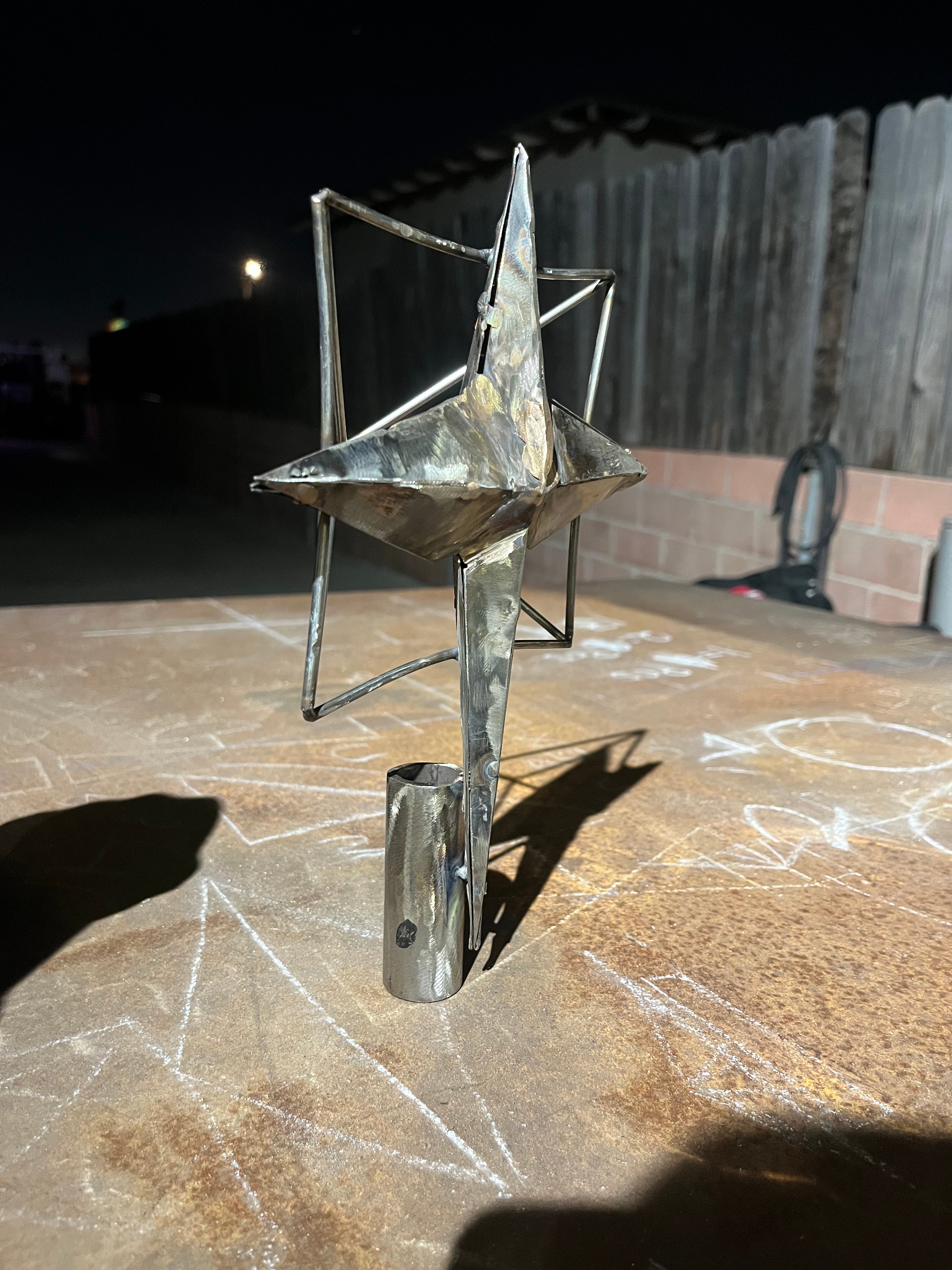
Ok , to be honest after laying out the cardboard cad, I I thought this was gonna look sharp, then I started matching up the and and cutting things out, next thing I knew I was squeezing and tacking, beating and welding. lol , it really was a fun ,easy and affordable project to create . Learned a bit about fit up, chill blocks (used a 3x3 aluminum angle to weld all panels) filled gaps with silicone bronze., and best of all its was done with my daughter, she actually engineered the whole thing, gave me a sketch and we work together to build it.
Question
1) silicone bronze don’t work on dirty steel right?
2) what the quickest way to clean off the old peel on stainless steel, you know the protective cover.
3) does the sili bronze filller flow like mud, or was I completely doing it wrong
Happy holidays
Brad Goodman Matt Hayden Shaun Graham
Posted
11 Dec 17:31
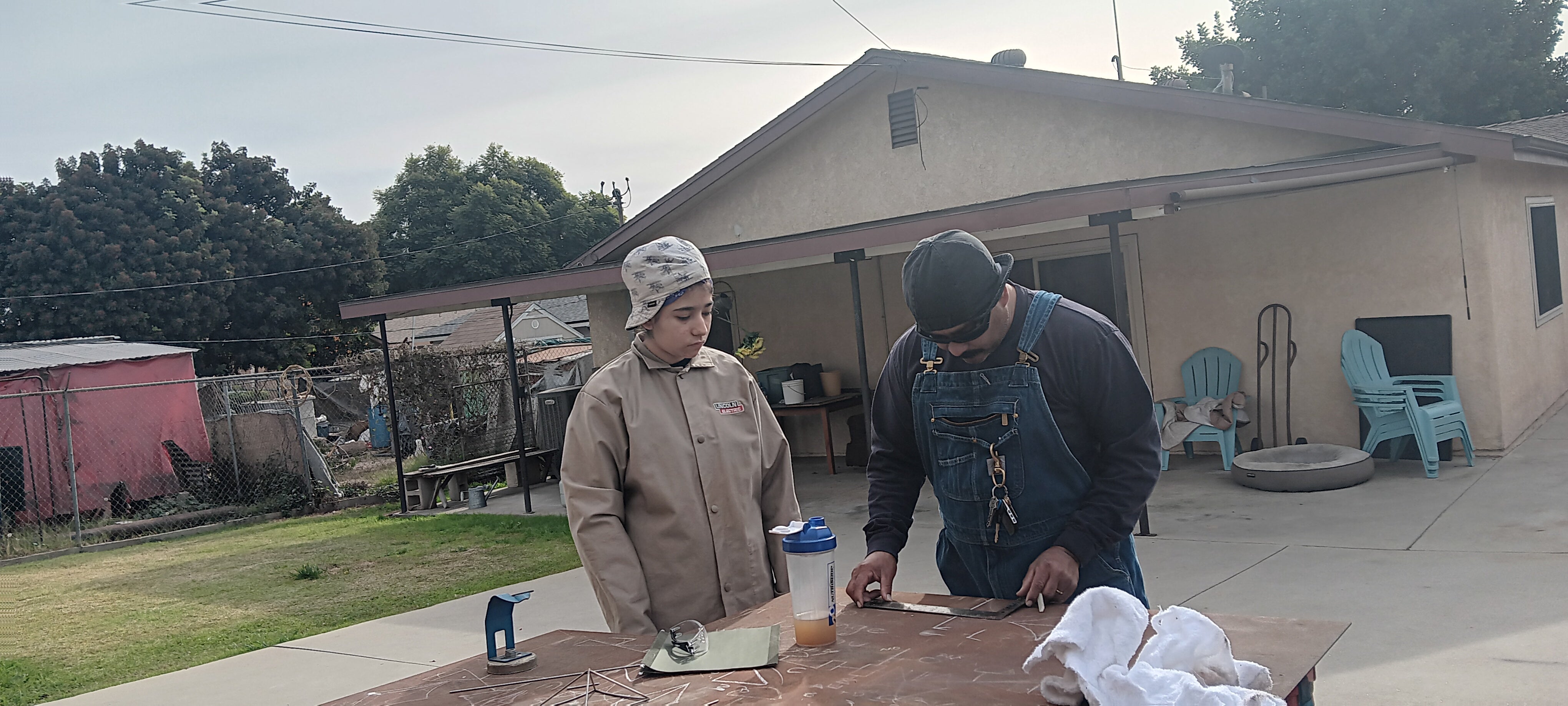
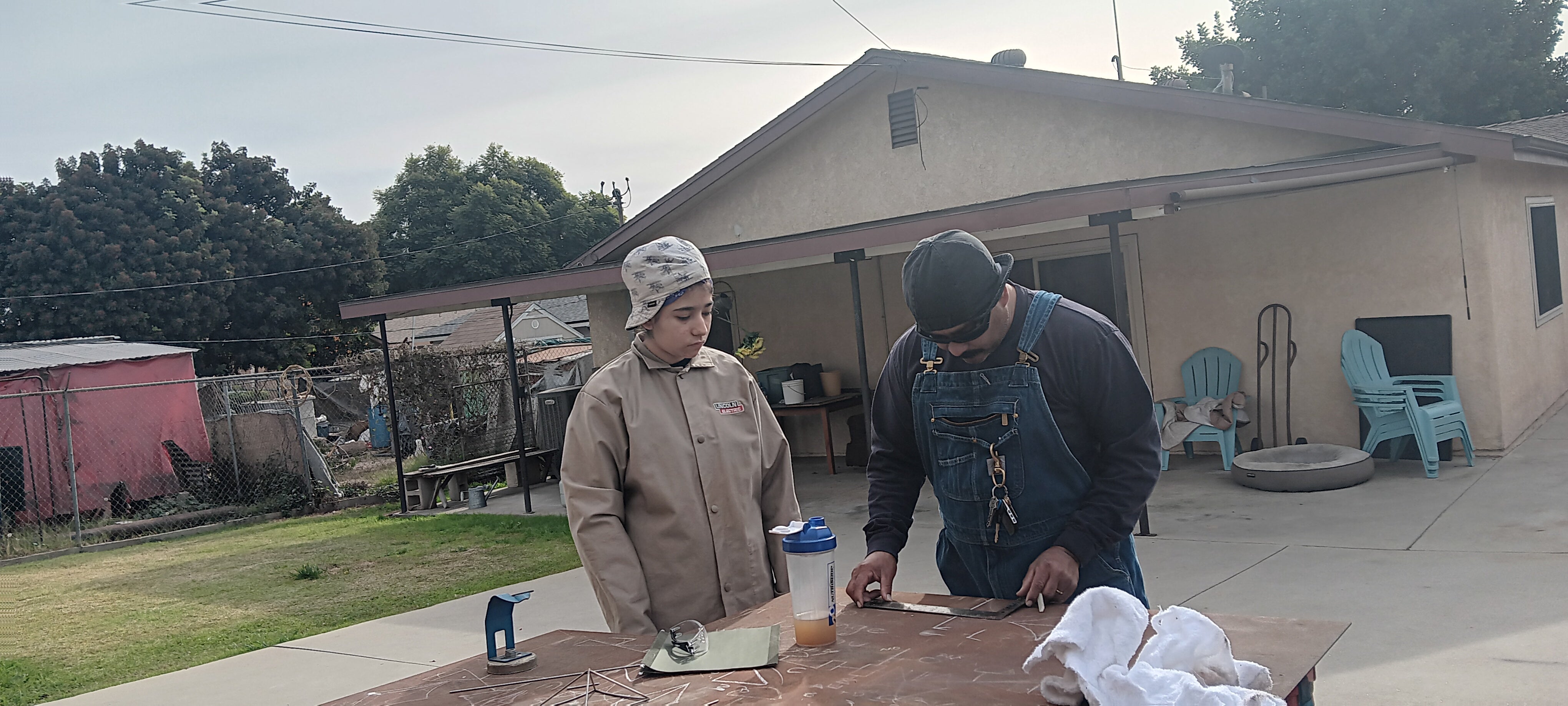
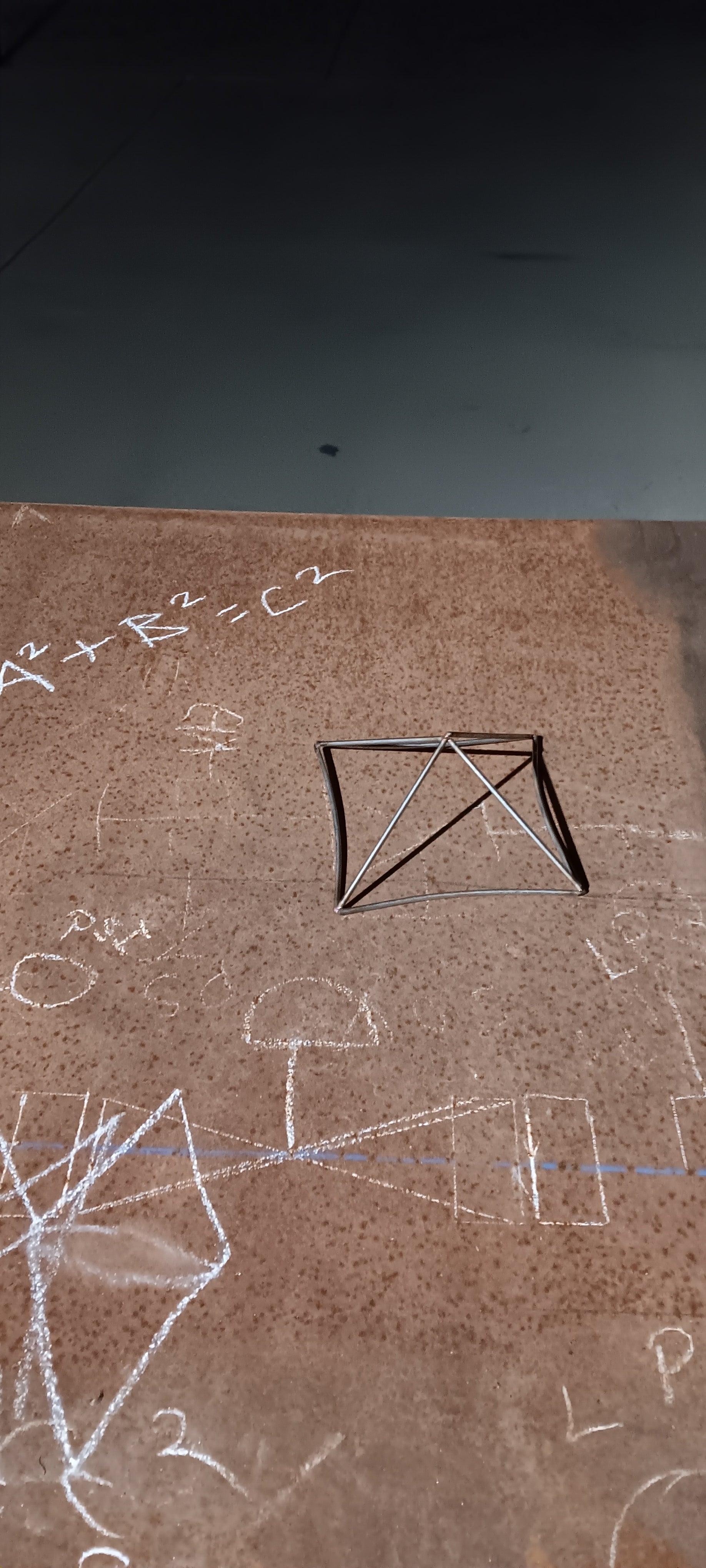
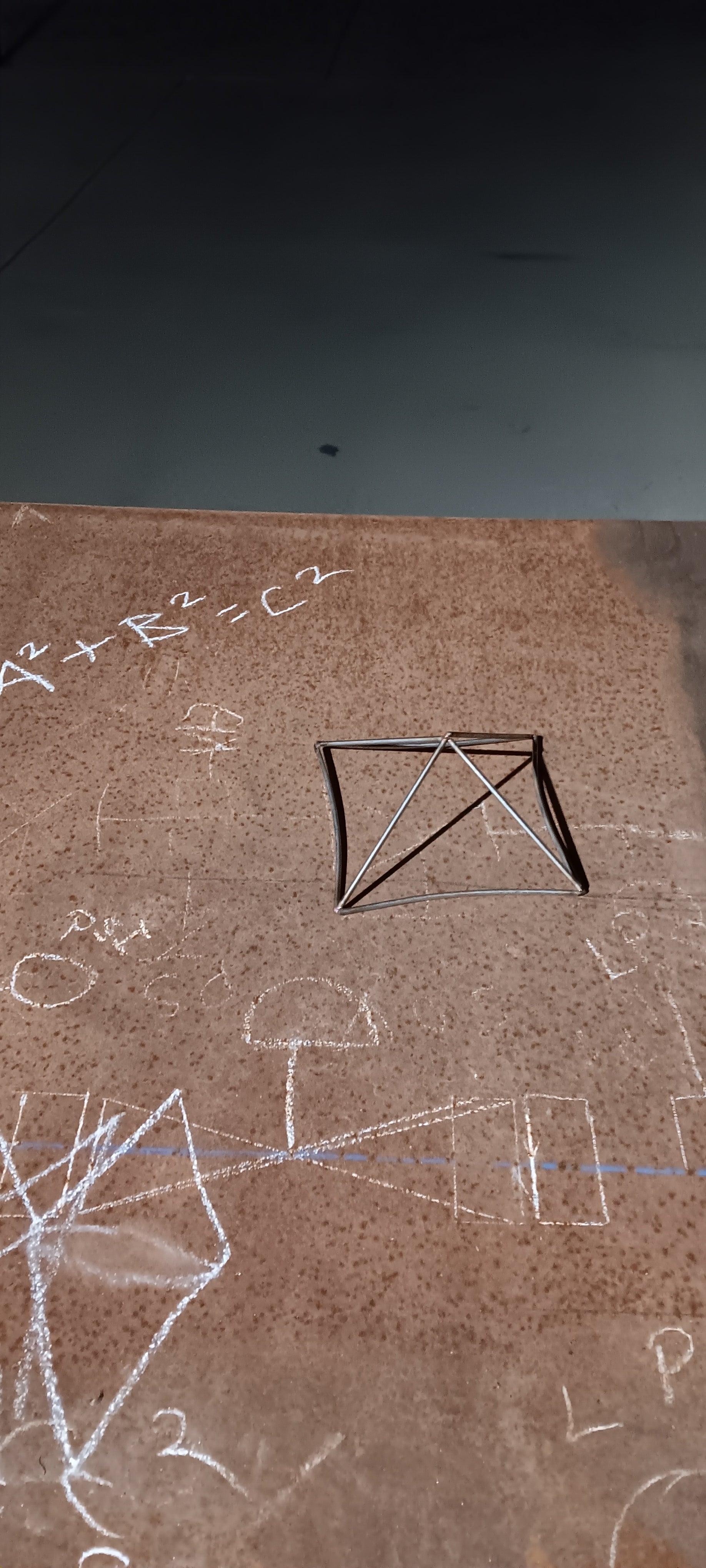
Brad Goodman Matt Hayden you guys ever fabricated with a slip roller, if so can you share your experience.
Allso, working plate and sheet metal is so different, especially with out a sheer, if you wanted to cut multiple small shapes with accuracy, what method would you recommend.
I'm trying to make a hoilday tree topper star out of 18 Guage, and 6 " cut off wheel. Let just say I taught my daughter the Importance of making the part match the template.
Anyhow I hope I get to post it.
Happy holidays
Posted
11 Nov 21:38
Drilling through these Stainless Steel fittings was a breeze with this drill press. 5/16 drill thru 1/4 stainless steel compression fittings.
Posted
24 Oct 00:16
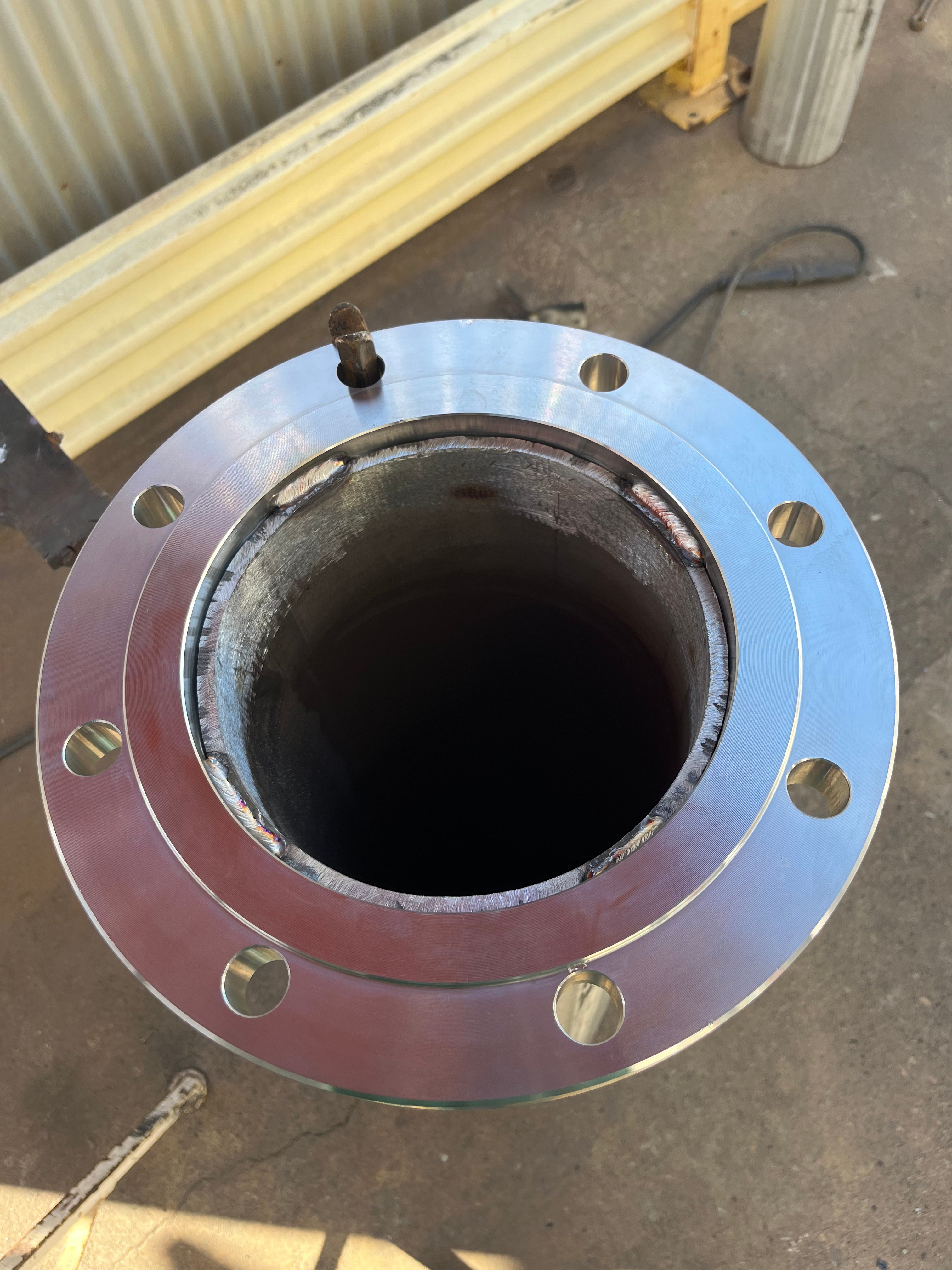
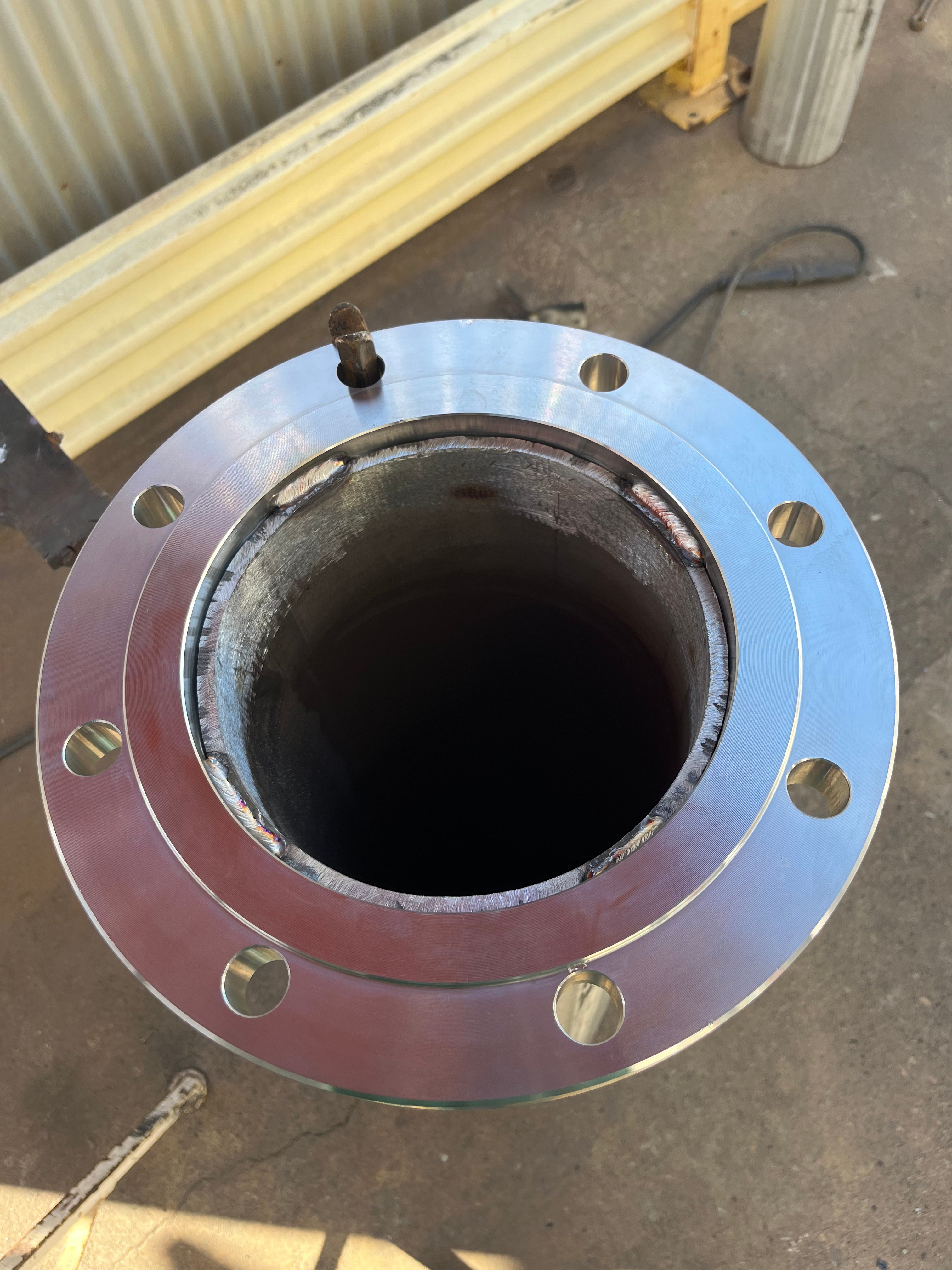
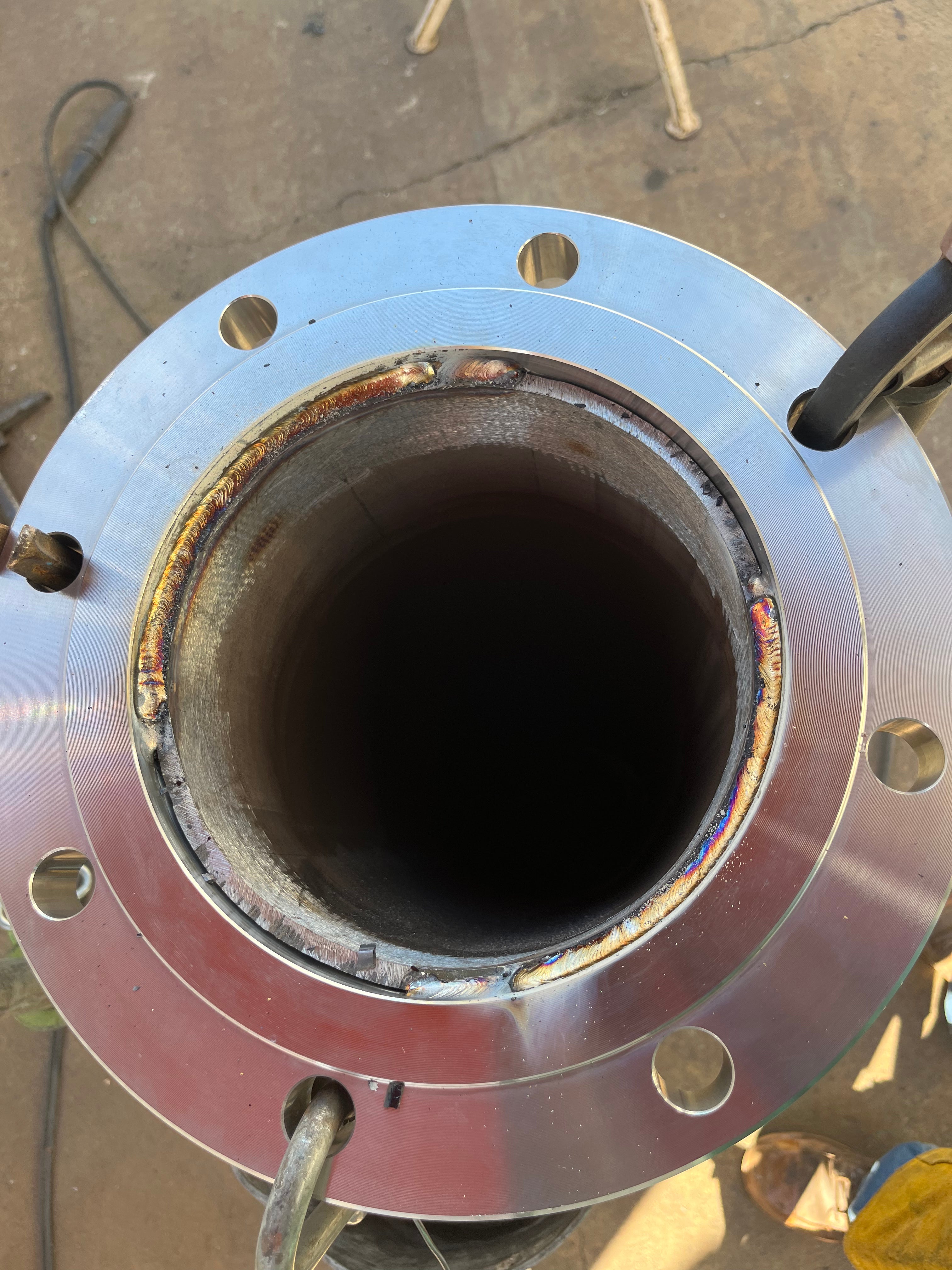
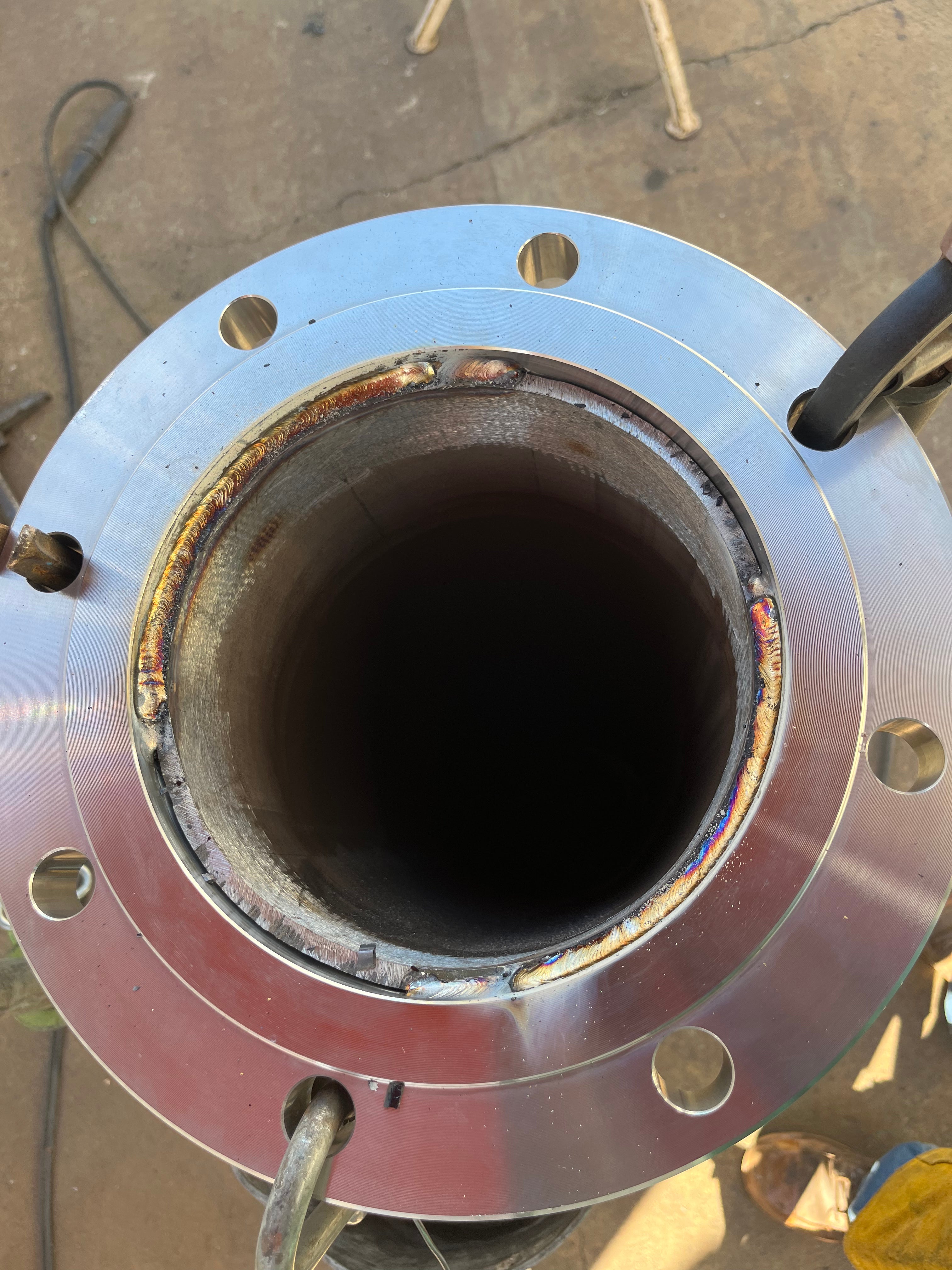
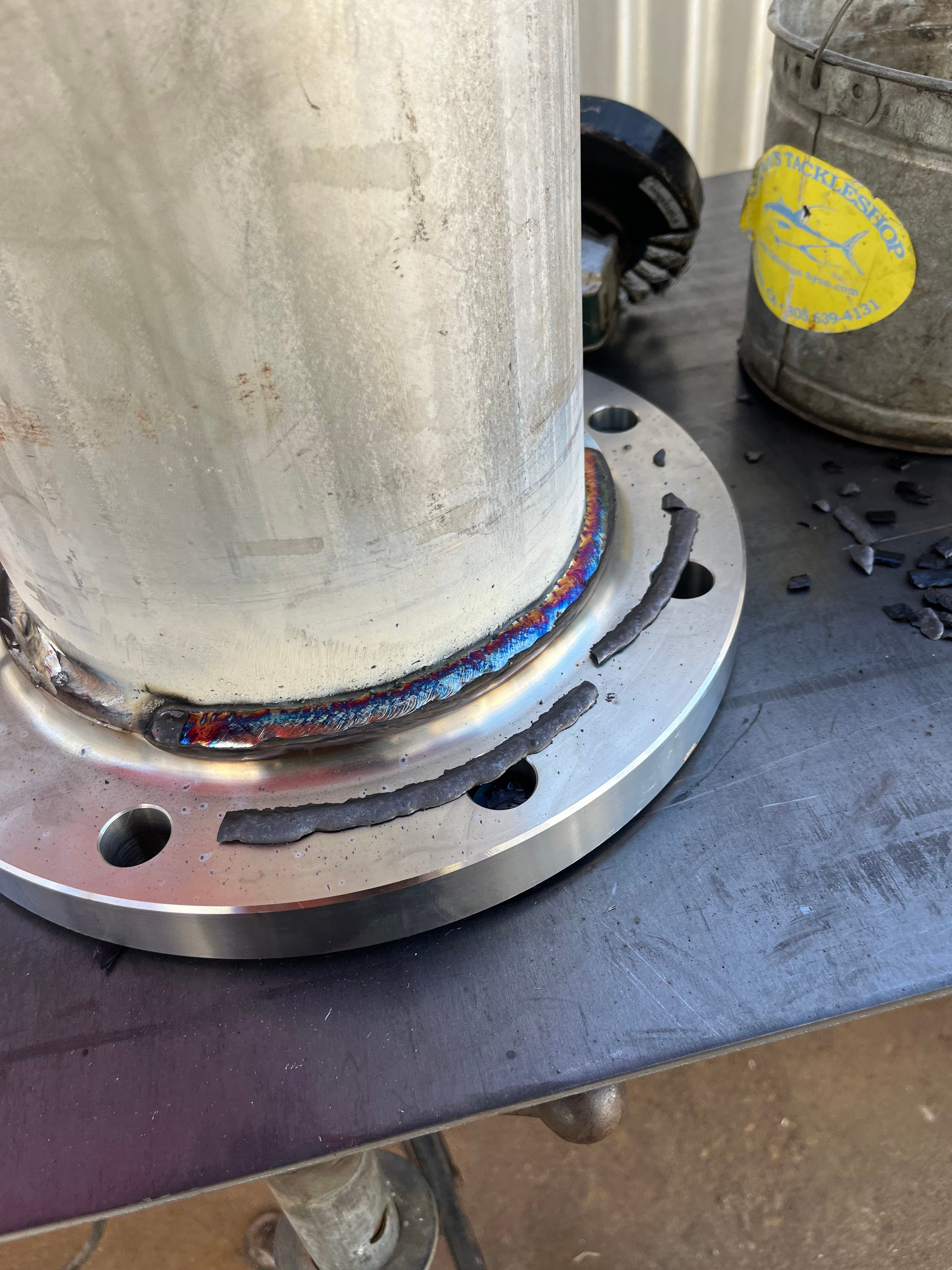
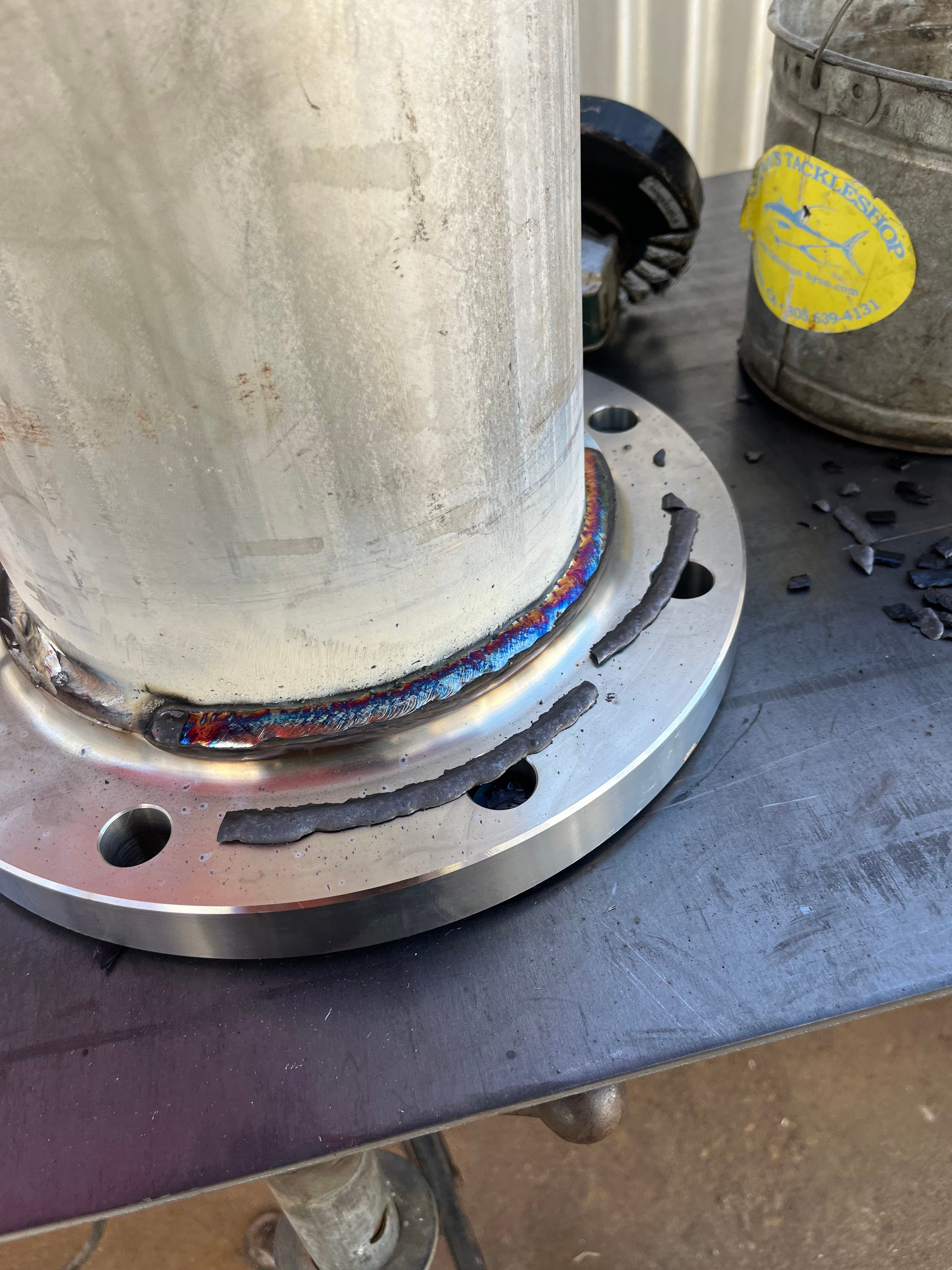
Fun little project, piping for Instrumentation air measurements. 8 pipe , 150 lb mating flange welded with 316/316L -16 1/8 rod smaw . 110 amps DC + 3 pass. Never really ran stainless stick, but I always heard the the slag has a tendency to pop off at you, the funny thing is the slag keeps popping even after you clean the weld, kind like jumping beans. Was able to find a small box rod on the store shelf for about 115 bucks.
Posted
09 Oct 01:28
This thing felt like I was working on a giant rat trap. Now that I’m done I want to see it dump a load. lol also make me wanna build a crane or something, imagine that.
Posted
09 Oct 01:23
A month ago I took on this trailer , making some small odd repairs, including removing that battery, and relocate in side the newly mounted tool box. The real challenge was replacing the hydraulic pump , hose and fittings to match up with the original hydraulic ram. Then figuring out how to wire in the switch for a single action hydraulic line ( manufacturer had it set for dual action)
Finding the right fluid wasn’t to difficult, and with support of a local hydraulic parts supplier it only took a couple of trips. lol
Ill show the hydraulics in action on the next video.
Posted
25 Sep 19:04