Hi everyone, I’m a welding student that completed 2 years of welding in college while in high school. I’ve done MiG, Stick and Tig but my experience really shines in Stick. I’m trying to go back to school for more or get a beginner job in the industry. Thank you Jody for all the videos you have made. We used to watch your videos in class and I still watch them outside of school. Currently 18 years old and excited to make a career and learn everything that I can.
Hi welding friends, thanks for all the tips and tricks that this site shares. Ronnie from Denver, Colorado. Welding AC/DC tig for the first time on a water cooled Everlast 255EXT. I’ve Mig, Stick, Brazed and Gas welded in the past but never had a tig welder for constant usage. Thanks to Jody for all the great videos.
Will be teaching myself so I can start on a few race car projects. Chromoly roll cage, titanium/stainless headers, new body panels and many more projects ahead!
Hi folks, meant to fill this out after first joining the site, but spaced it out. I've always been primarily a " I'll weld when I need to weld something" kind of guy for most of my 60 years. Started stick welding in high school and on the farm. Got into MIG and then TIG later in life. After a hitch in the USAF, I worked in telecommunications all over Alaska for 30+ years. Primarily into doing machinist work on the side, but welding a lot more after selling the mill and lathe ( preparing for our move to the "lower 48" ). With the machine work gone, welding is the new focus, and would like to up my skills. Main interest is motorcycle related welding, saving machined parts from the scrap barrel, general repair work, and just plain "making stuff". Has been a great way to spend time after retiring, and enjoying welding more and more. Also volunteer doing machine and fabrication on a steam locomotive restoration , which has been very rewarding. Sure do appreciate the knowledge shared on here. Thanks!
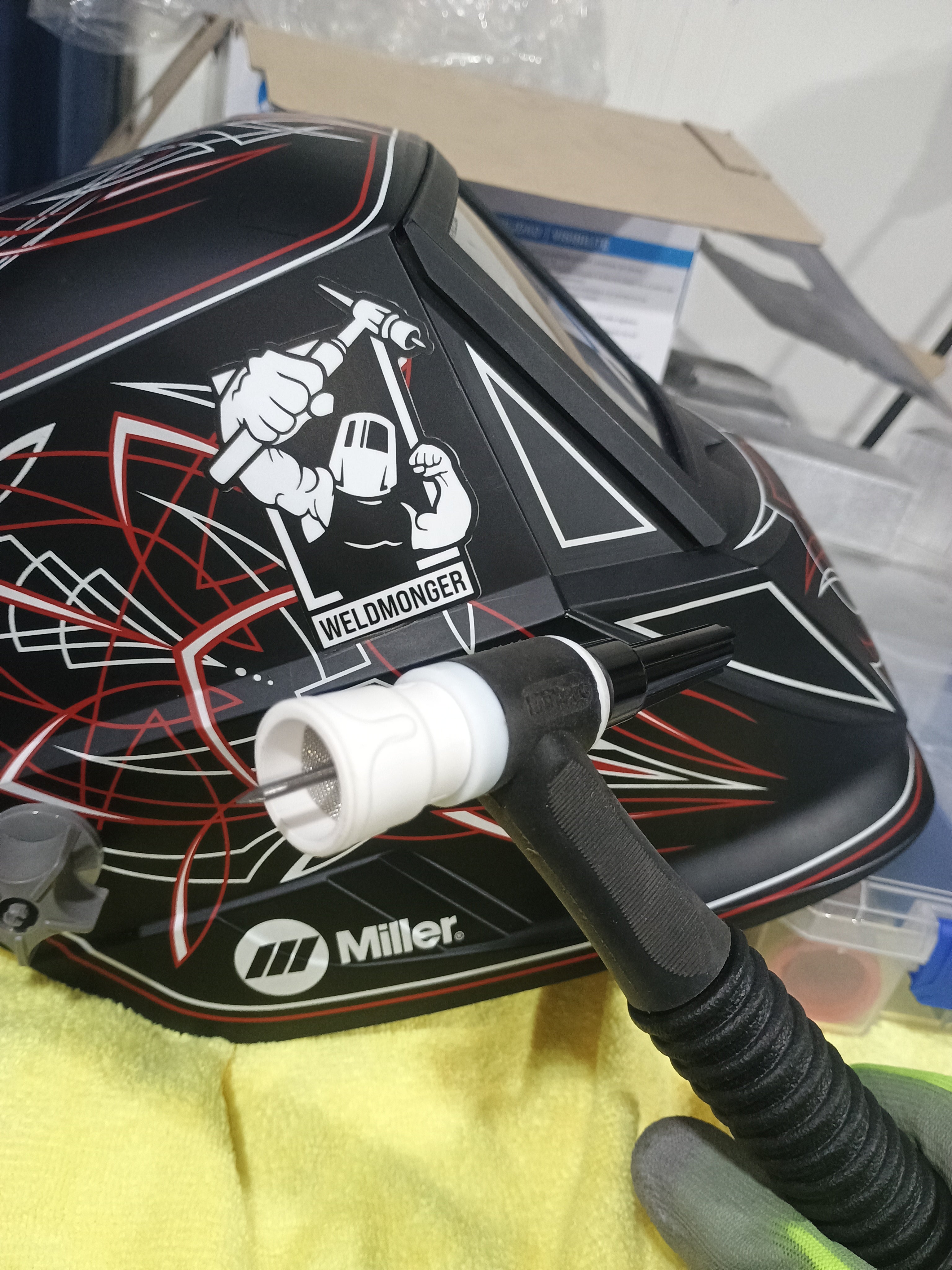
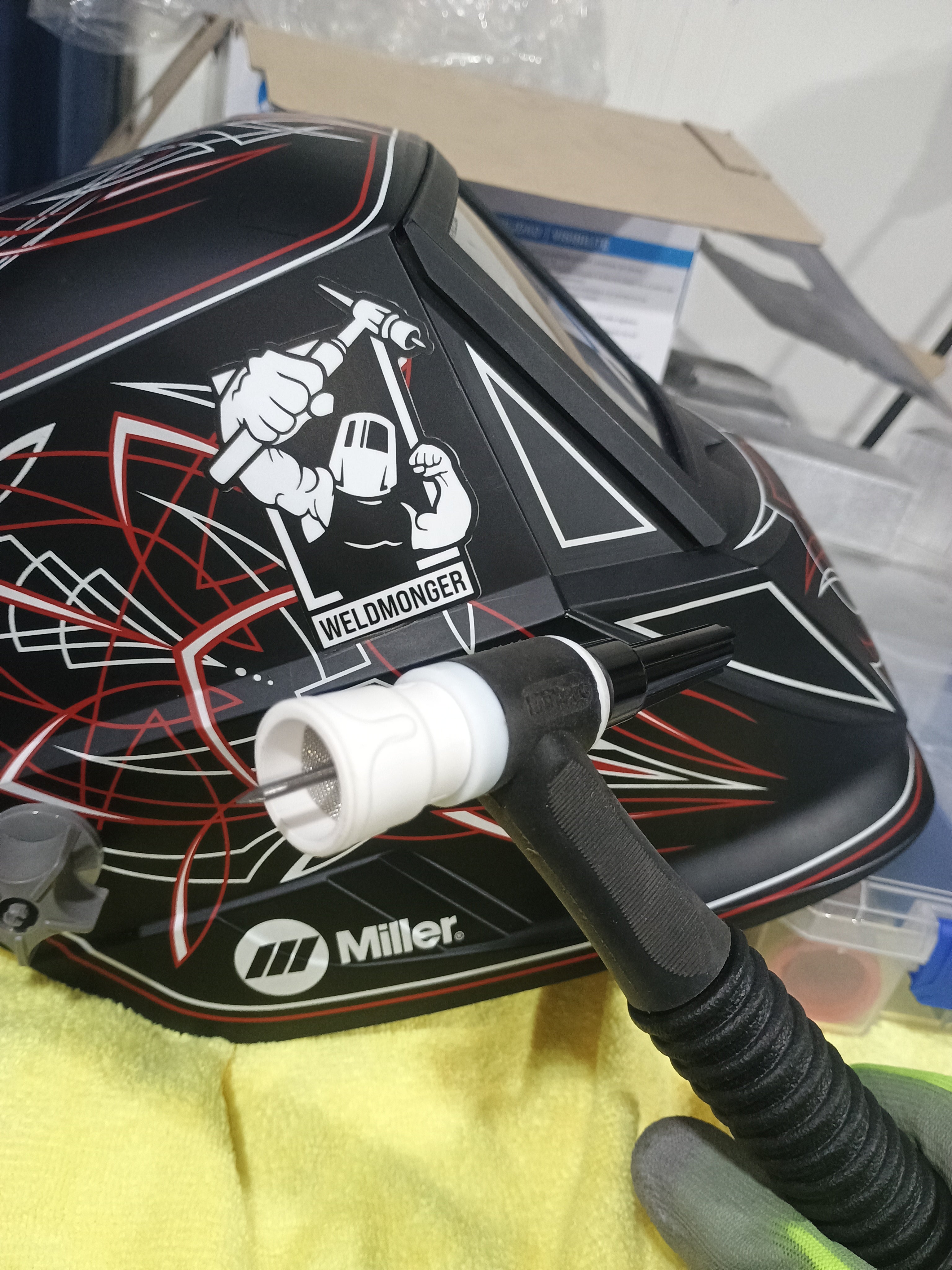
New to the page just signed up so that I could learn to Tig with my new miller 180 diversion. Sort of struggling to navigate the page and finding courses to teach me on practice techniques and so forth. Any help would be greatly appreciated.
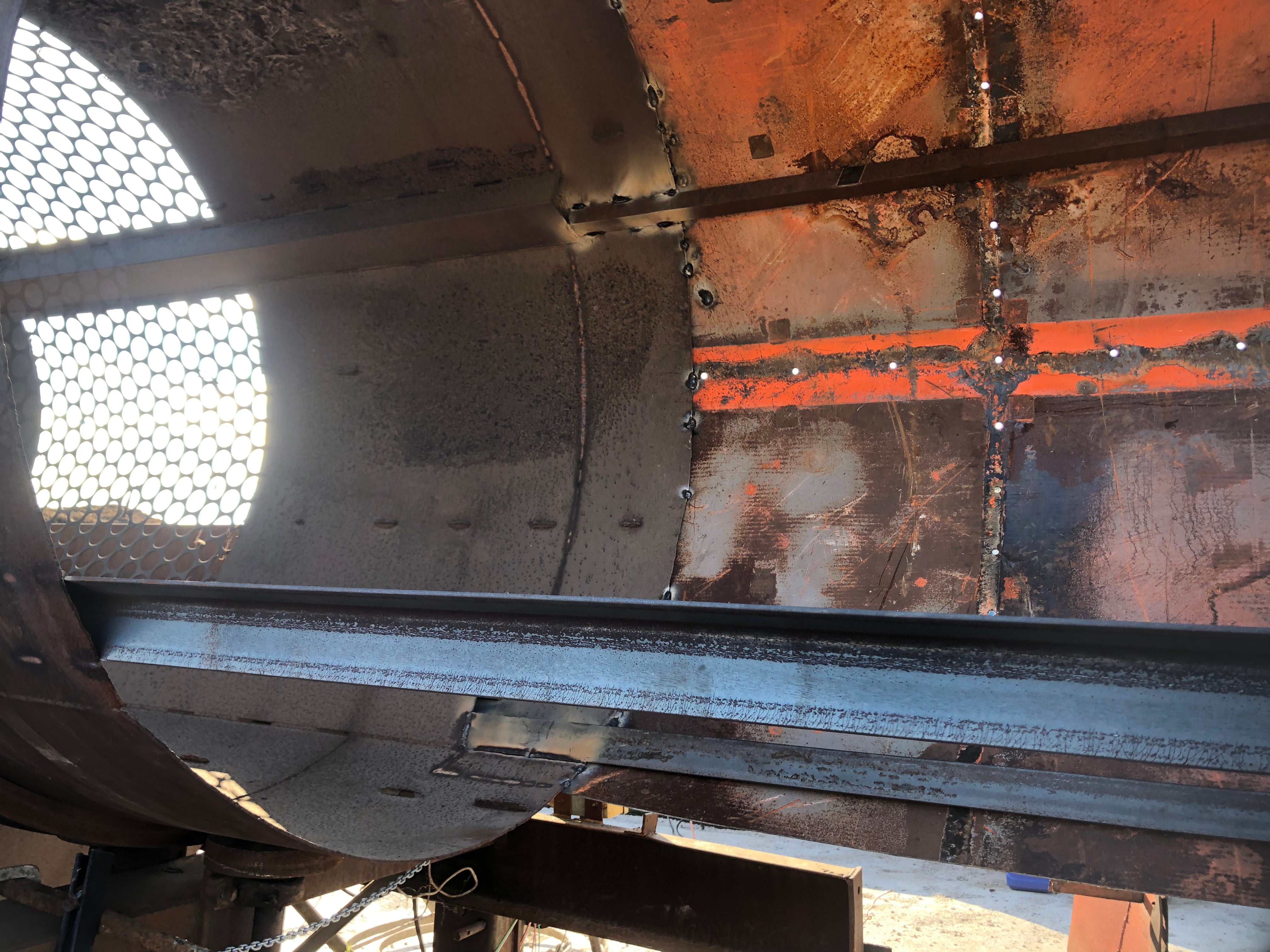
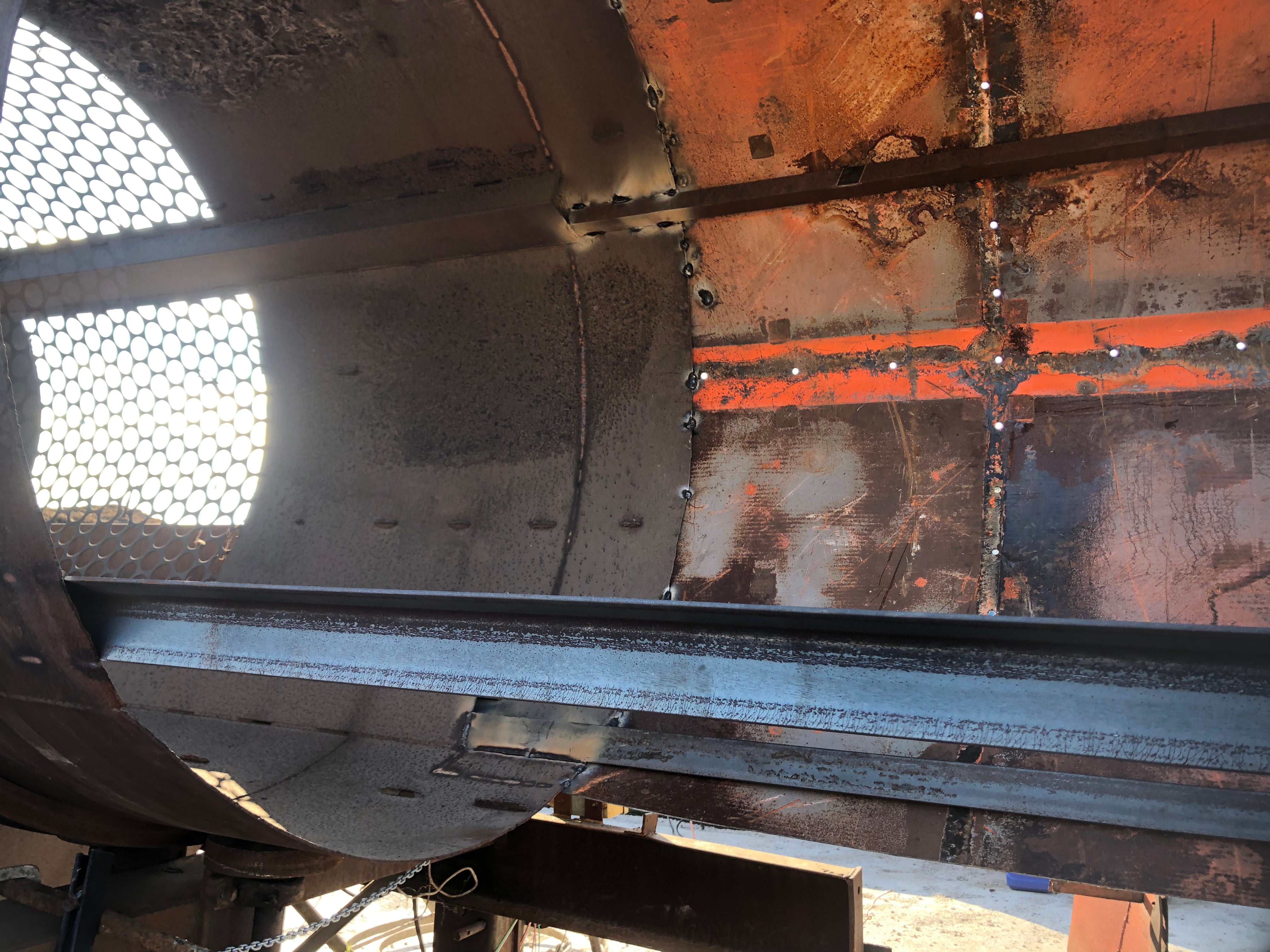
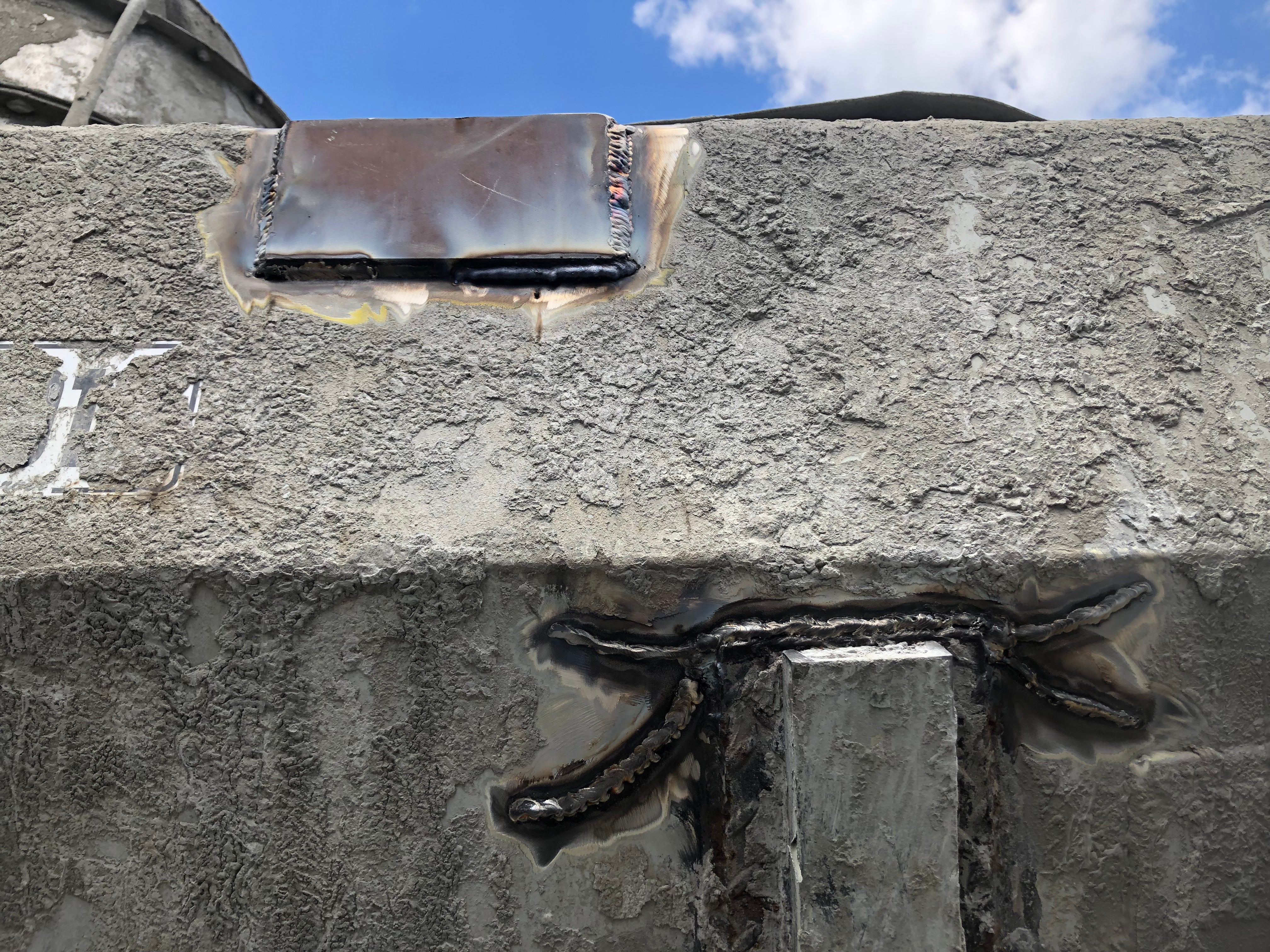
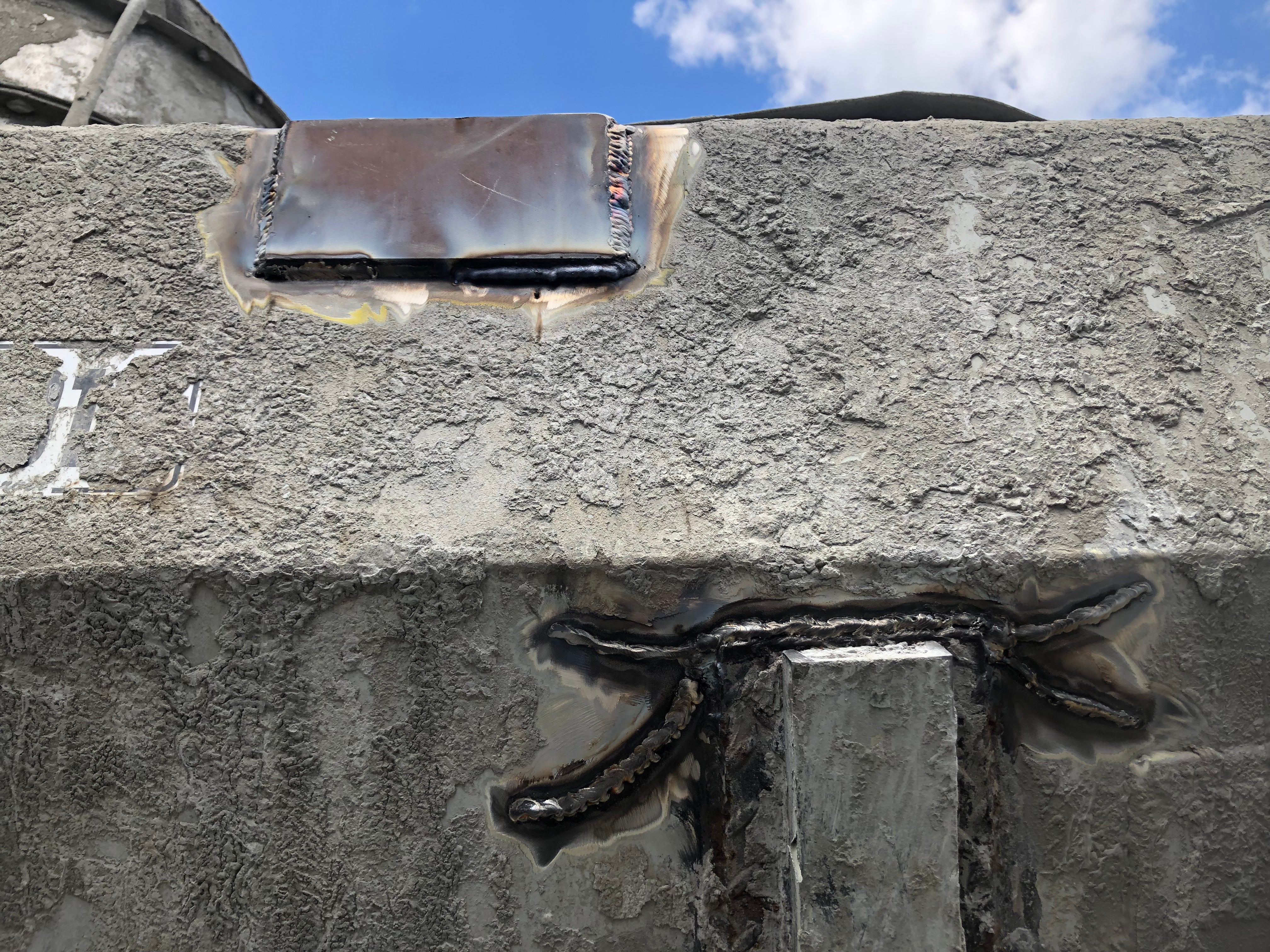
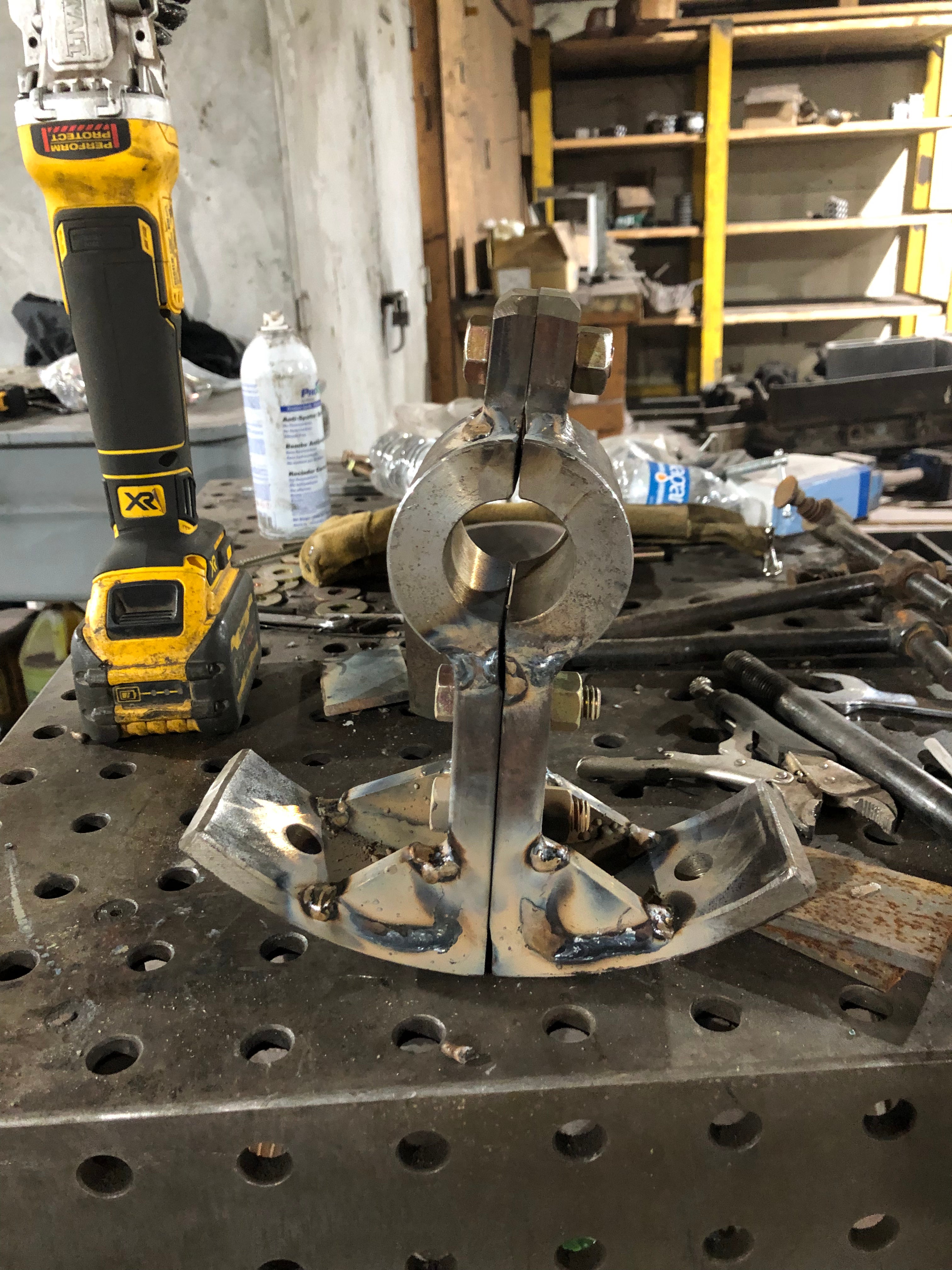
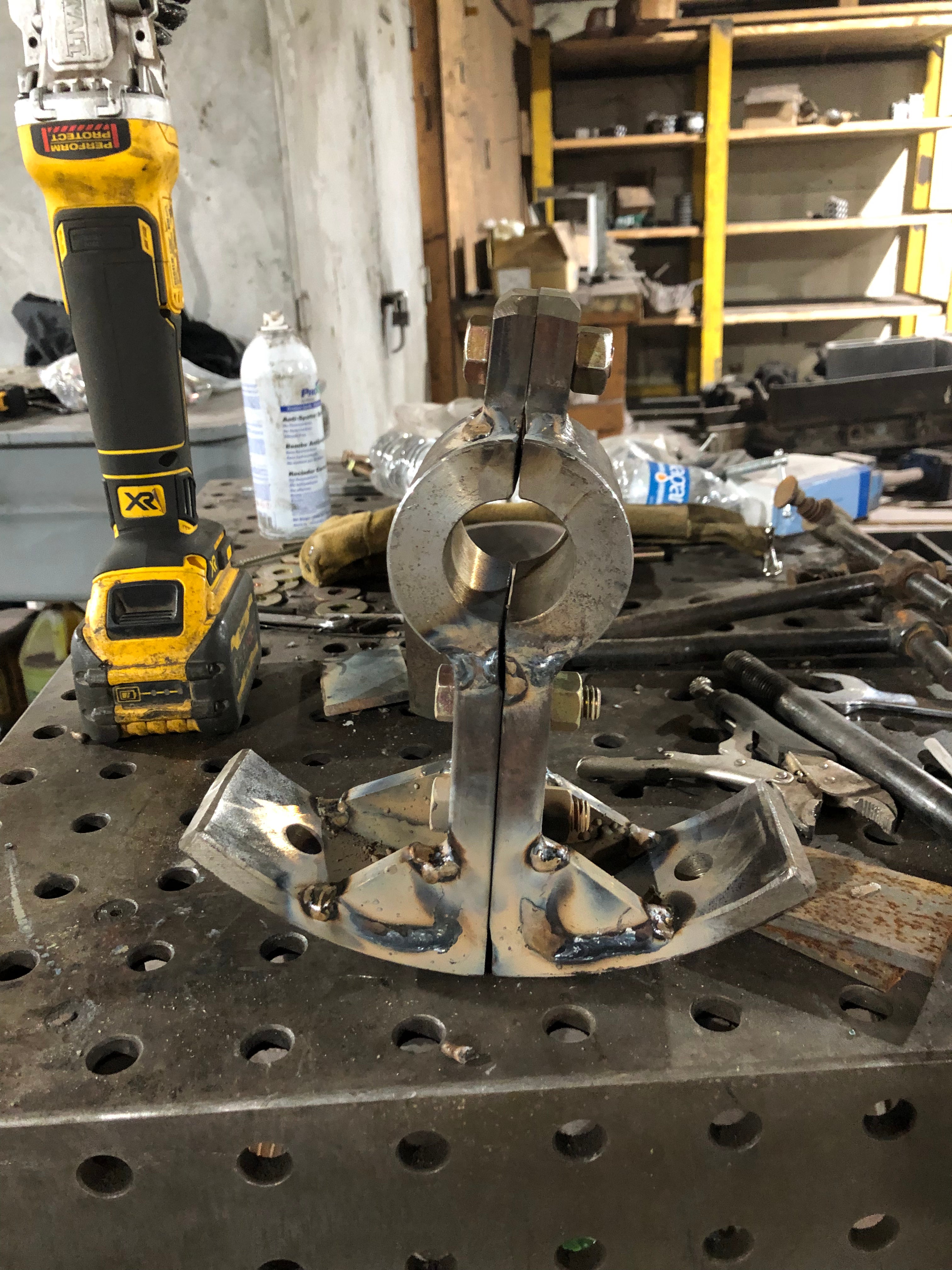
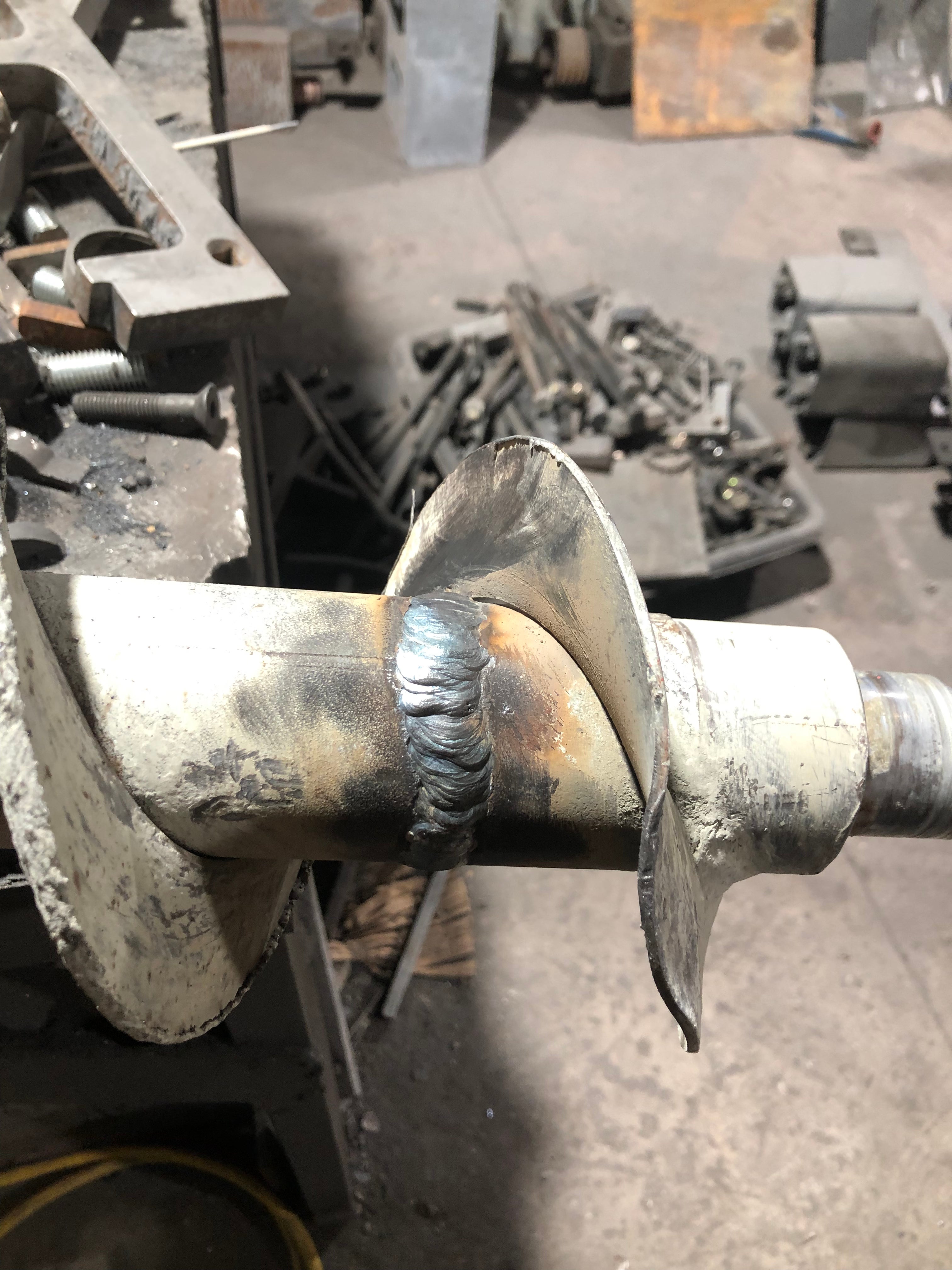
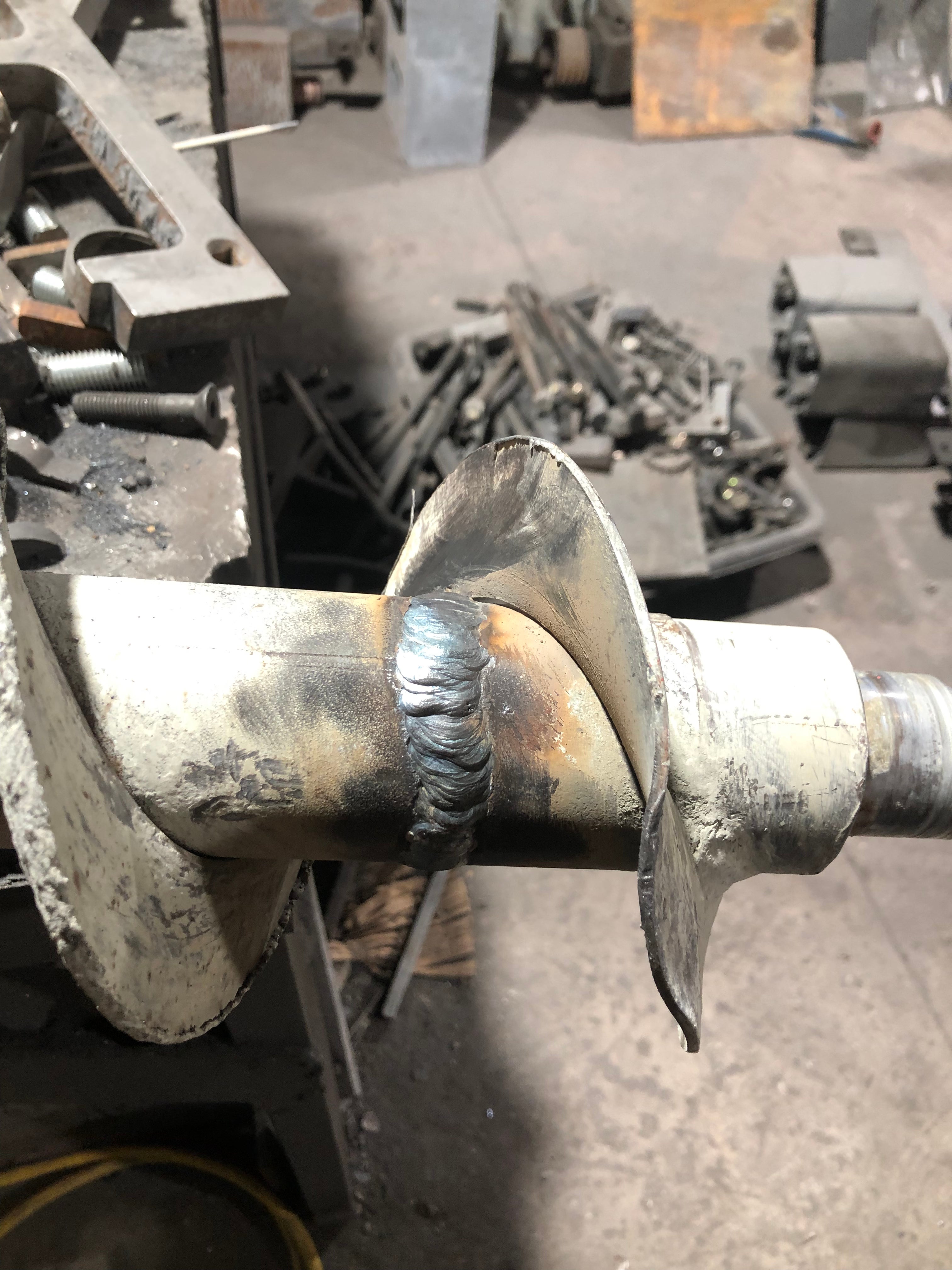
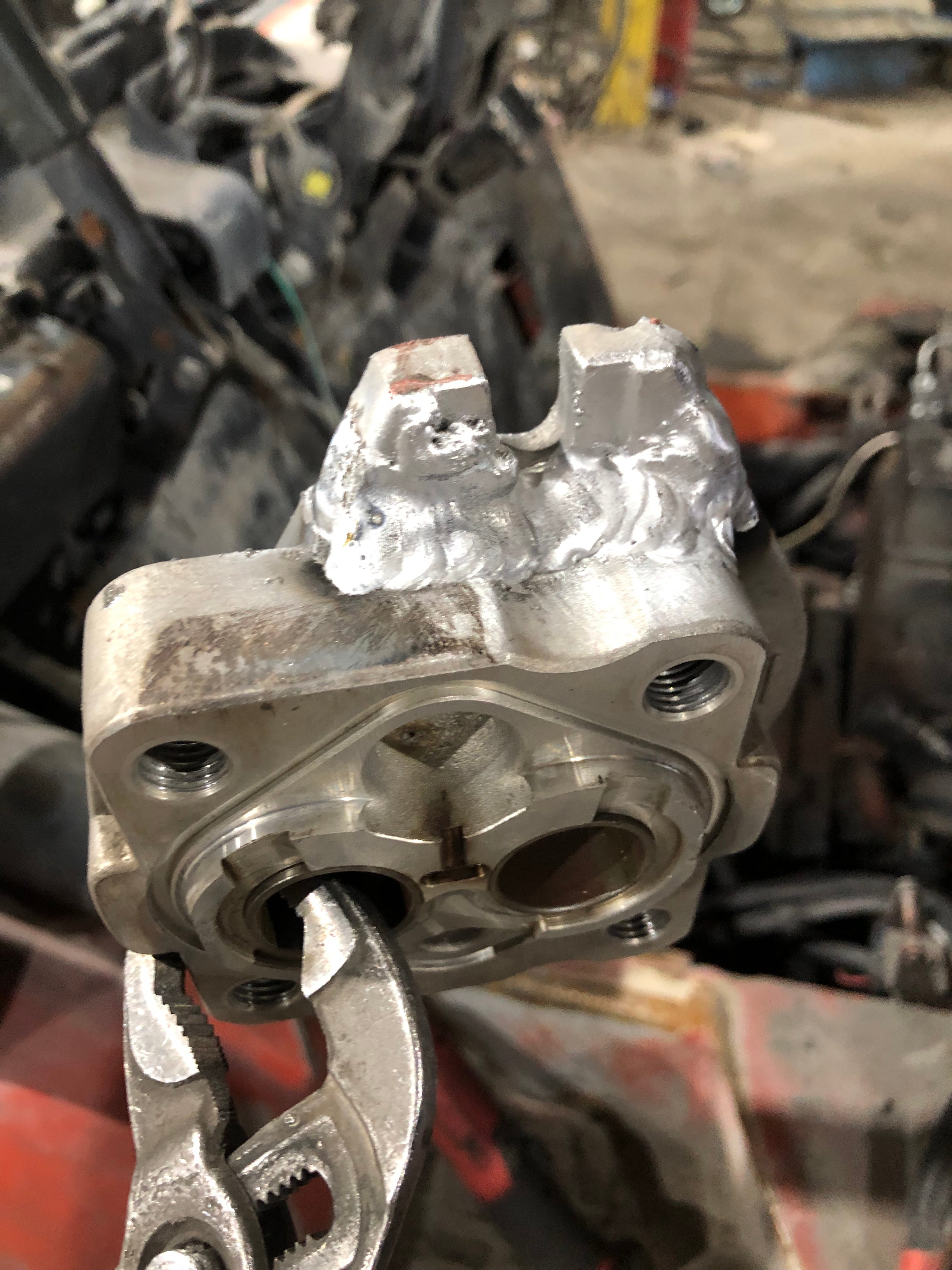
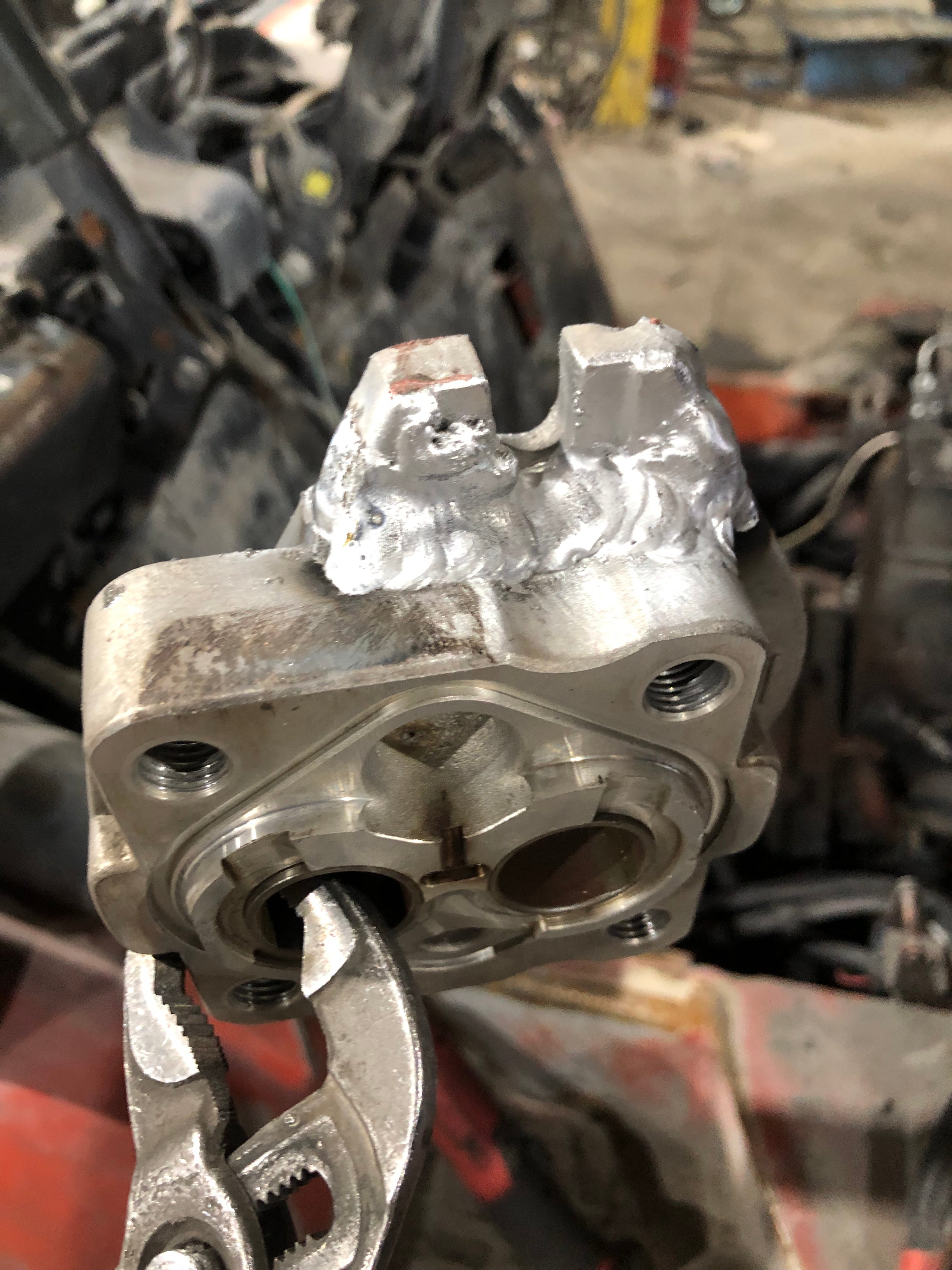
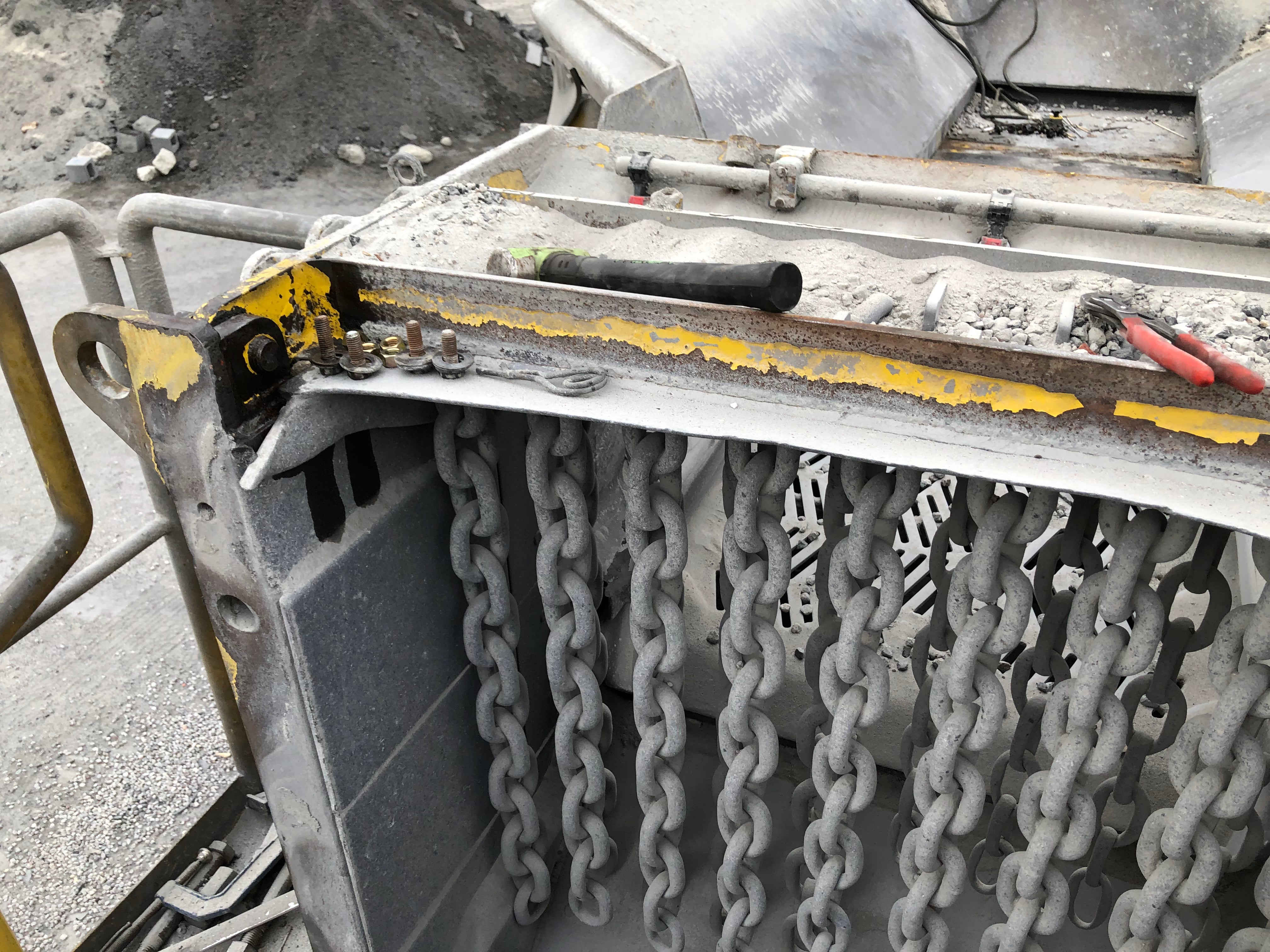
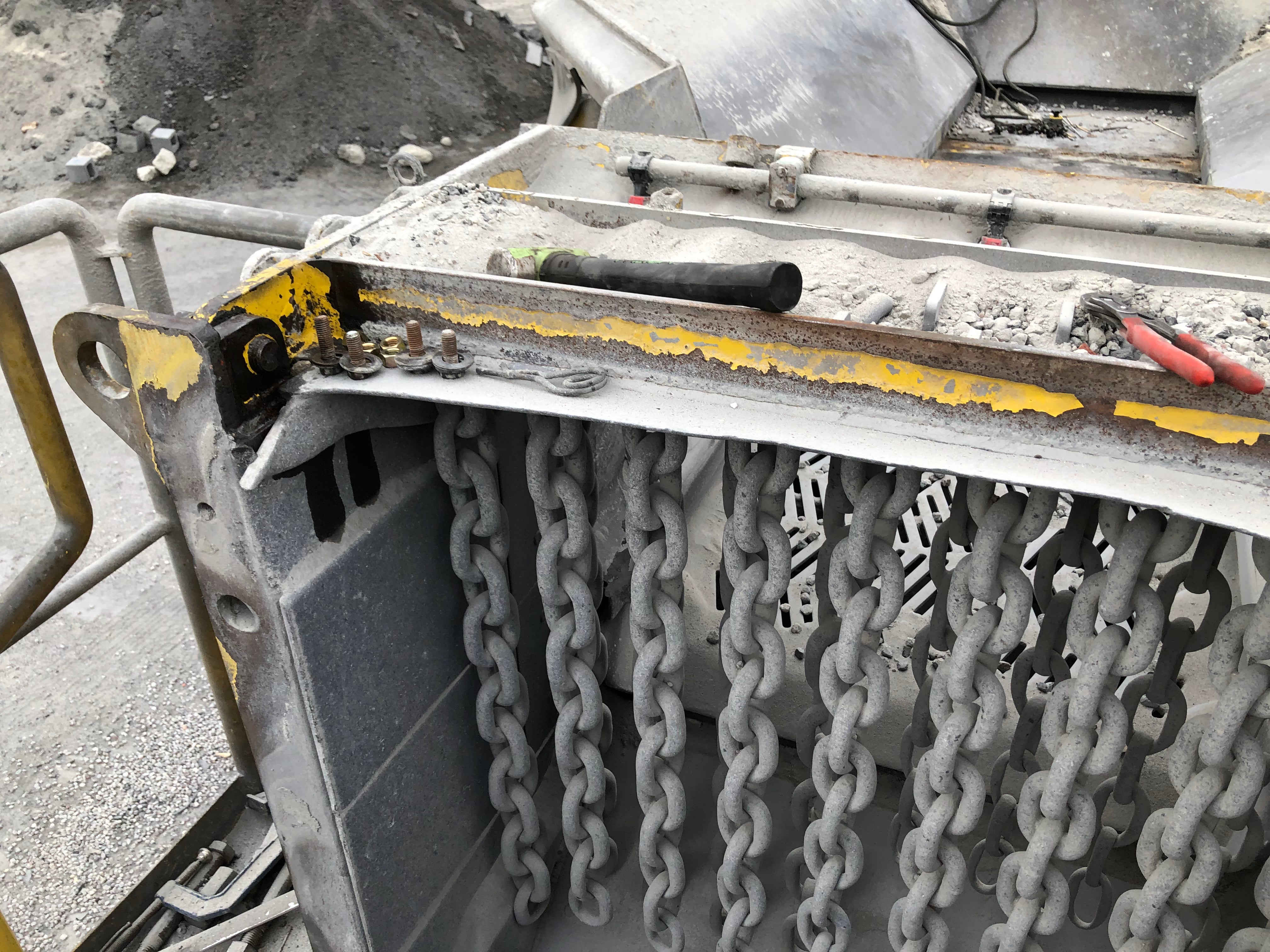
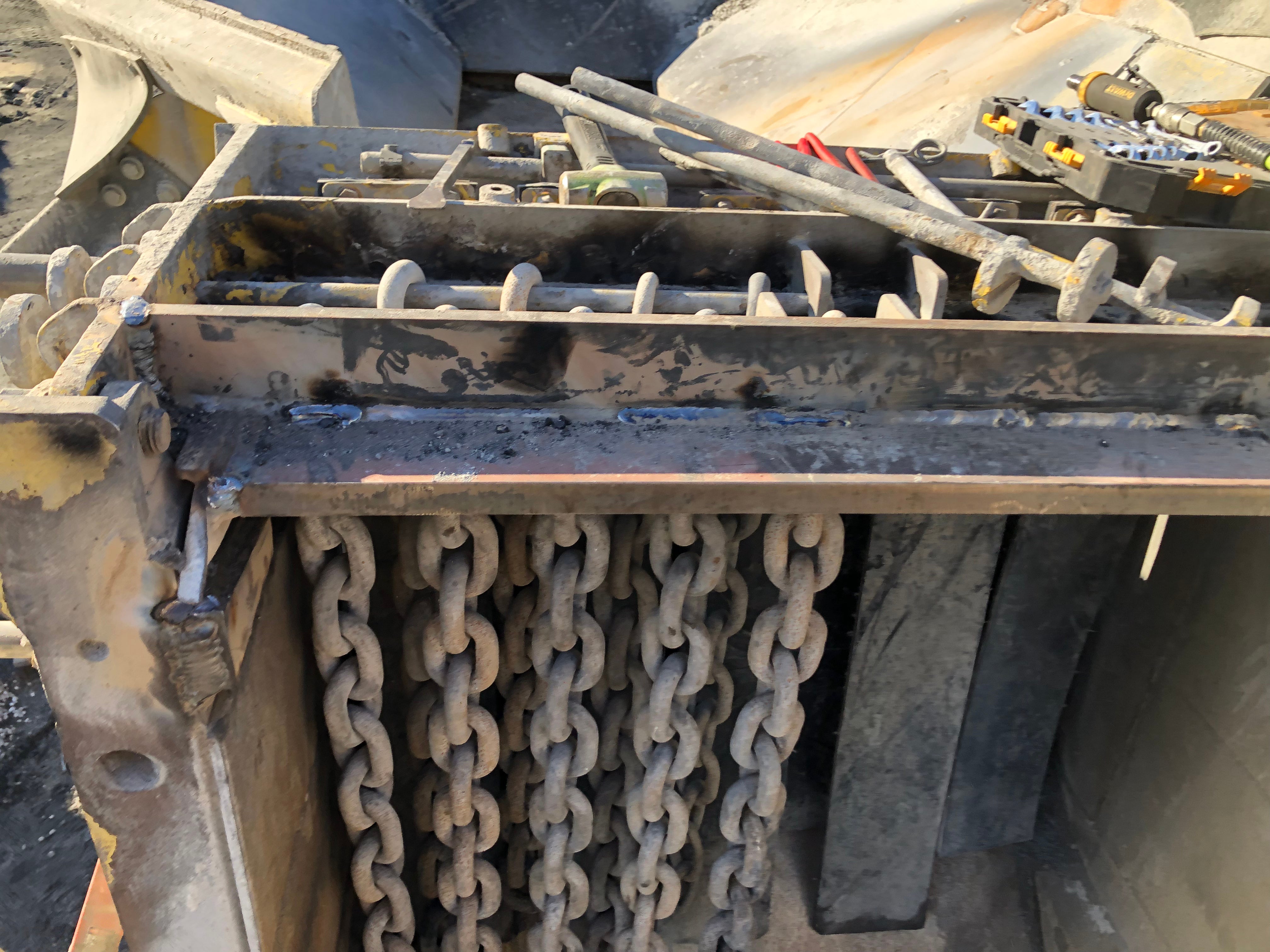
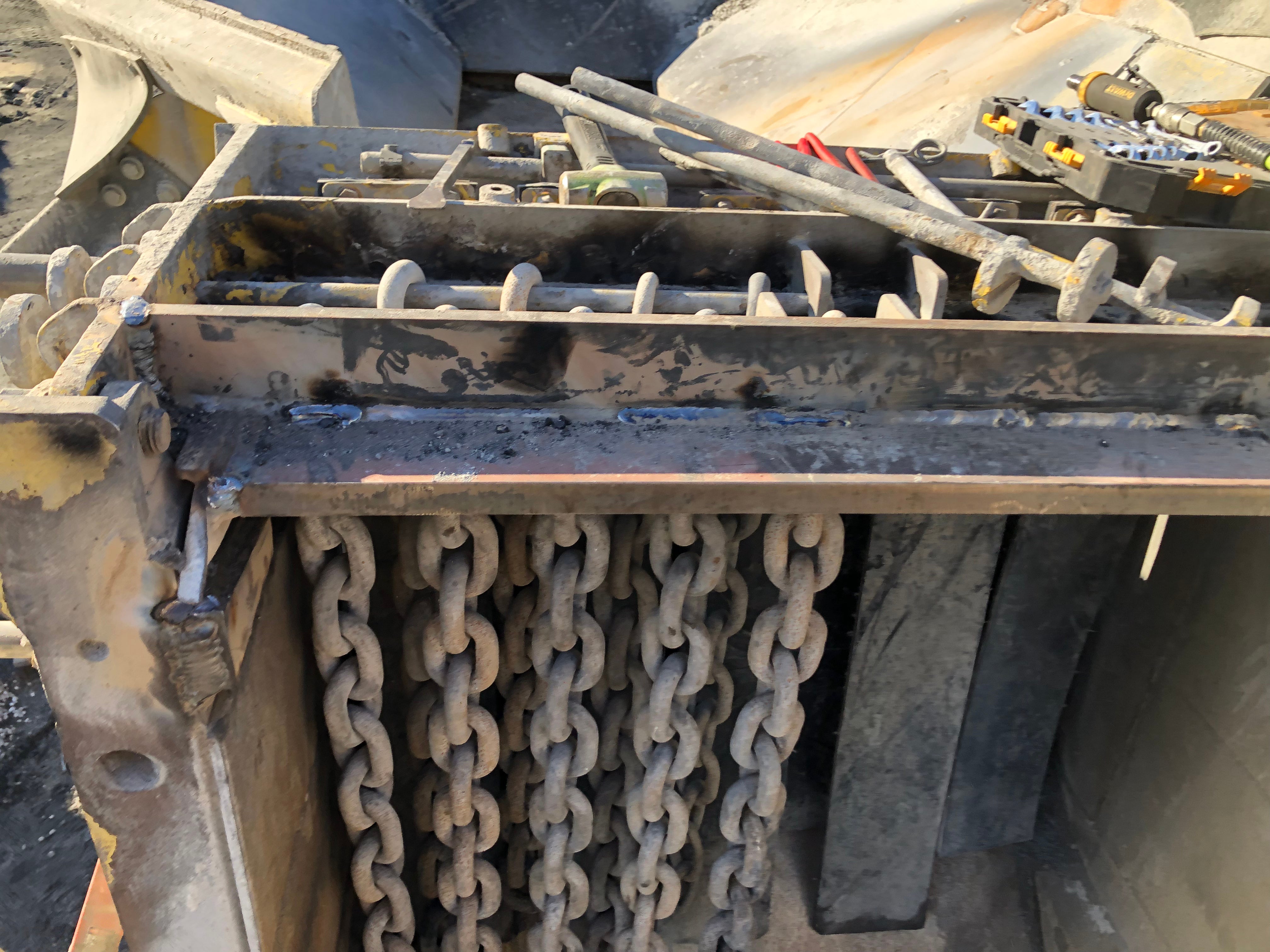
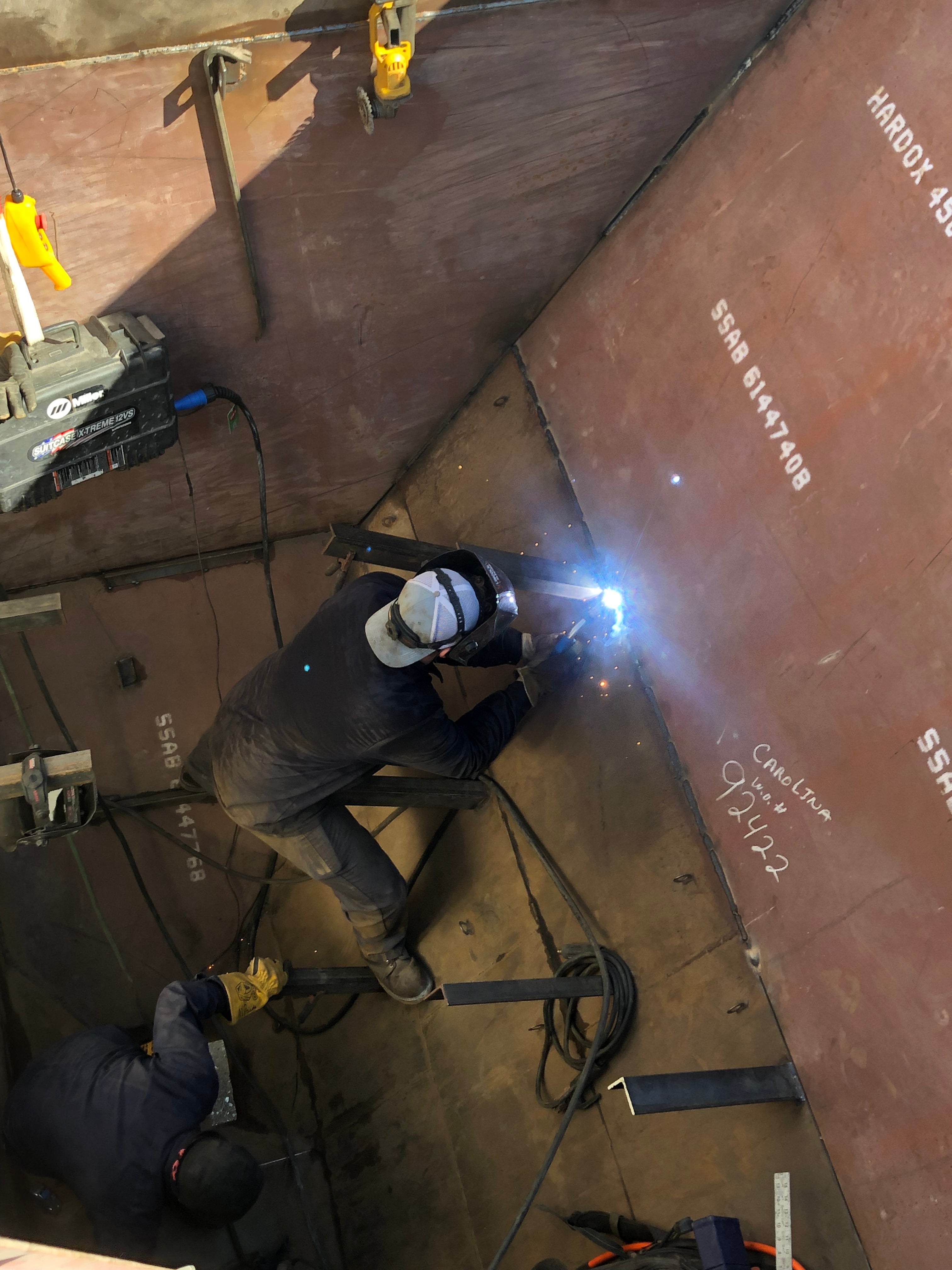
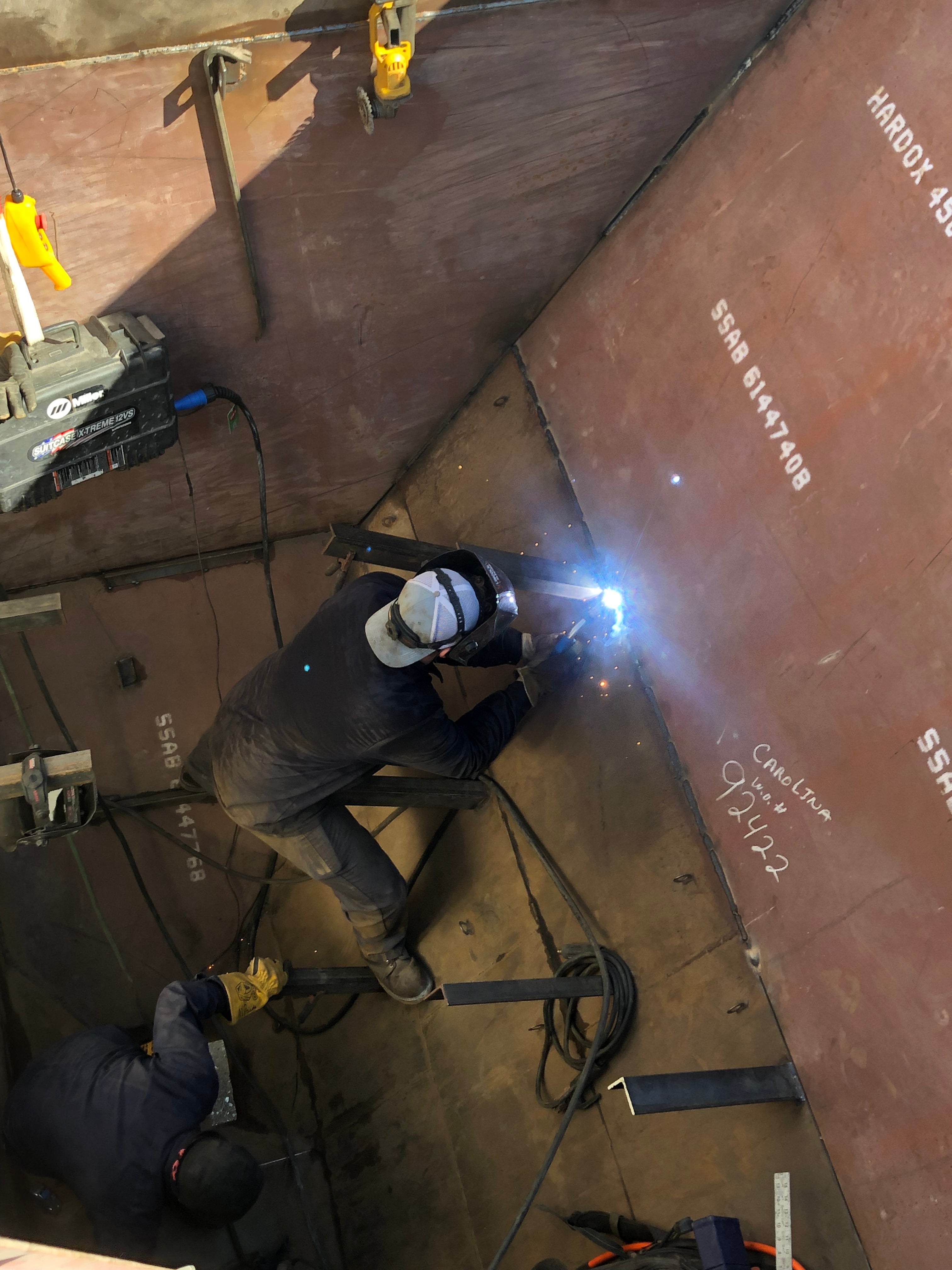
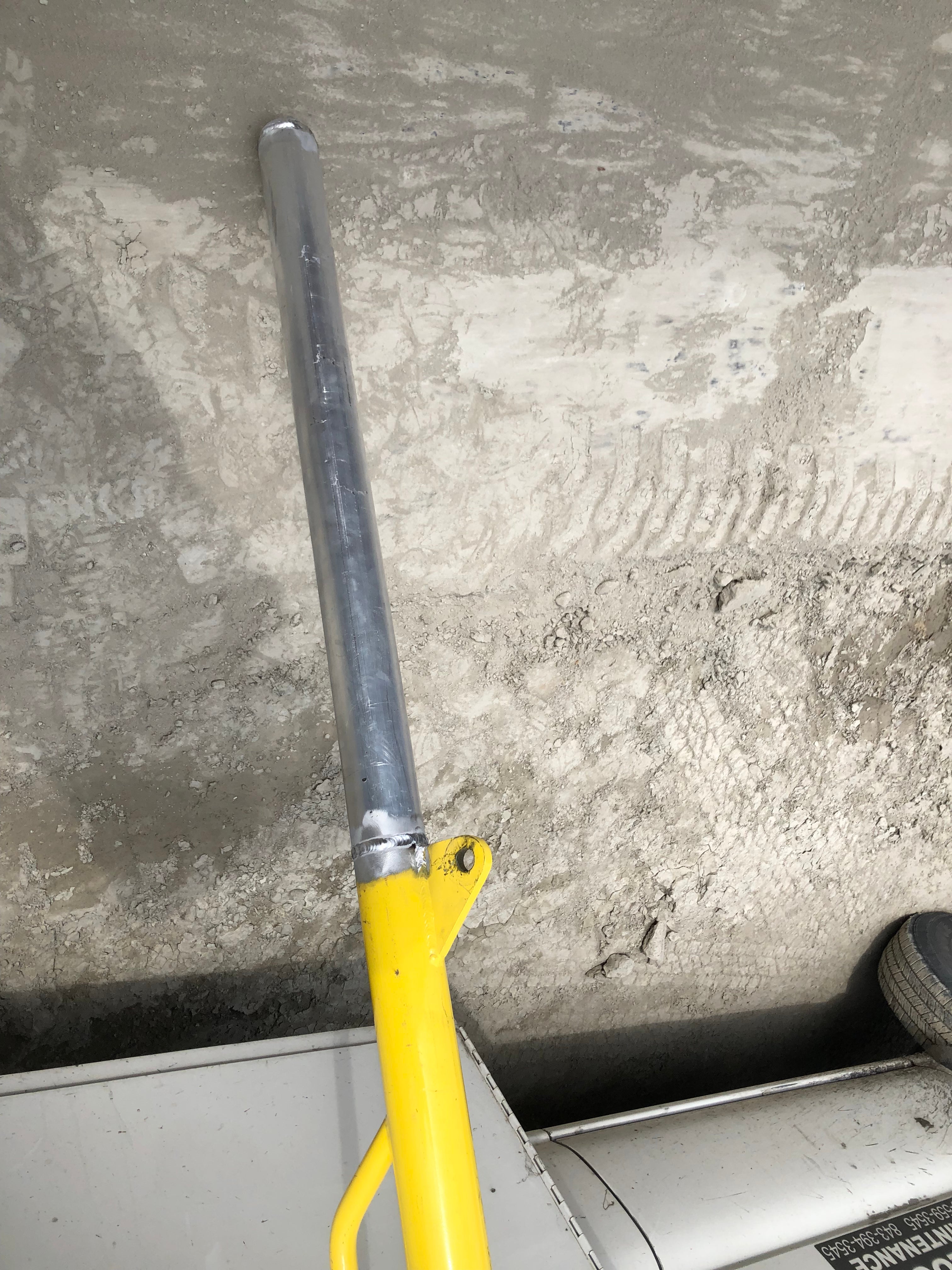
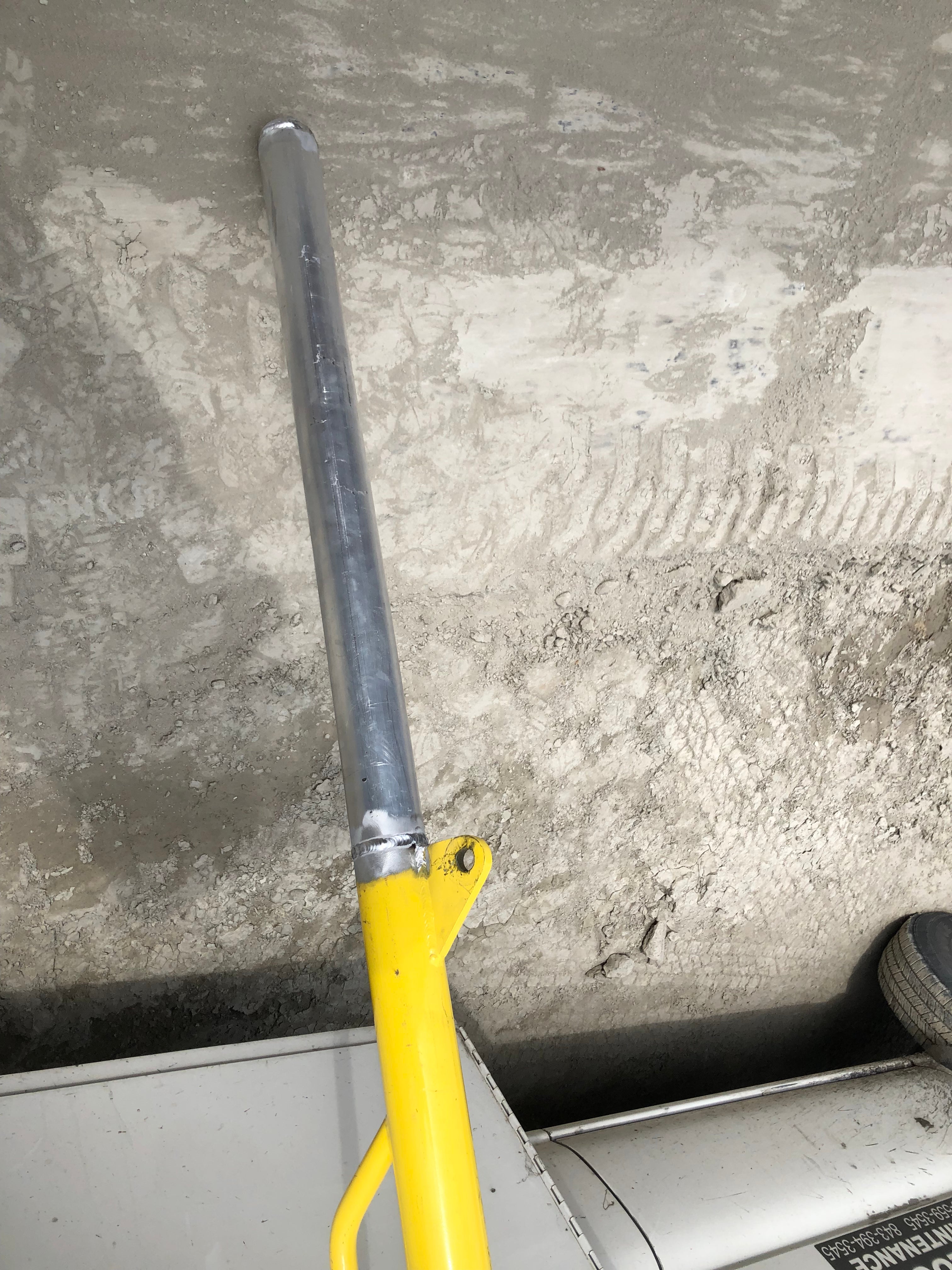
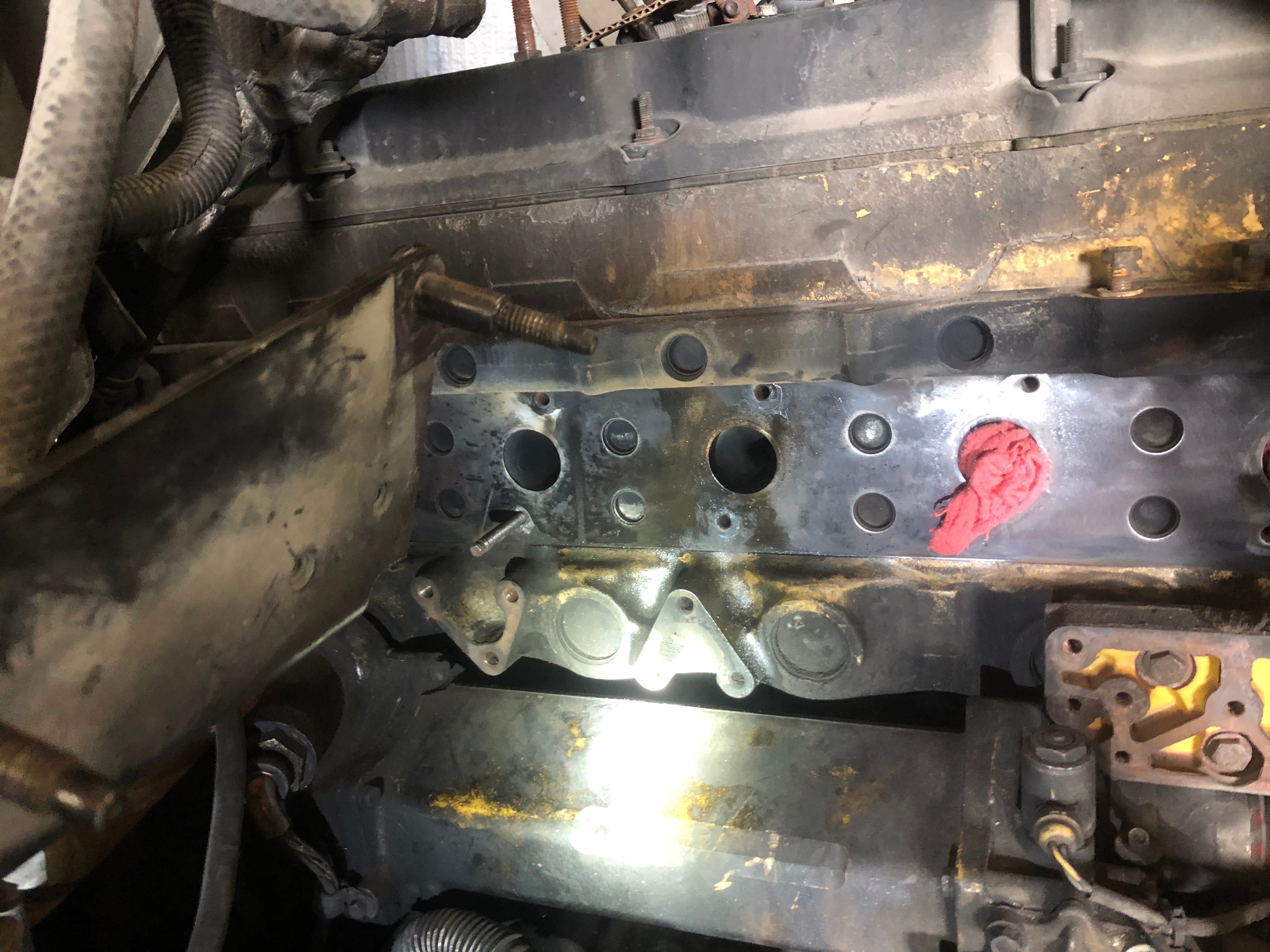
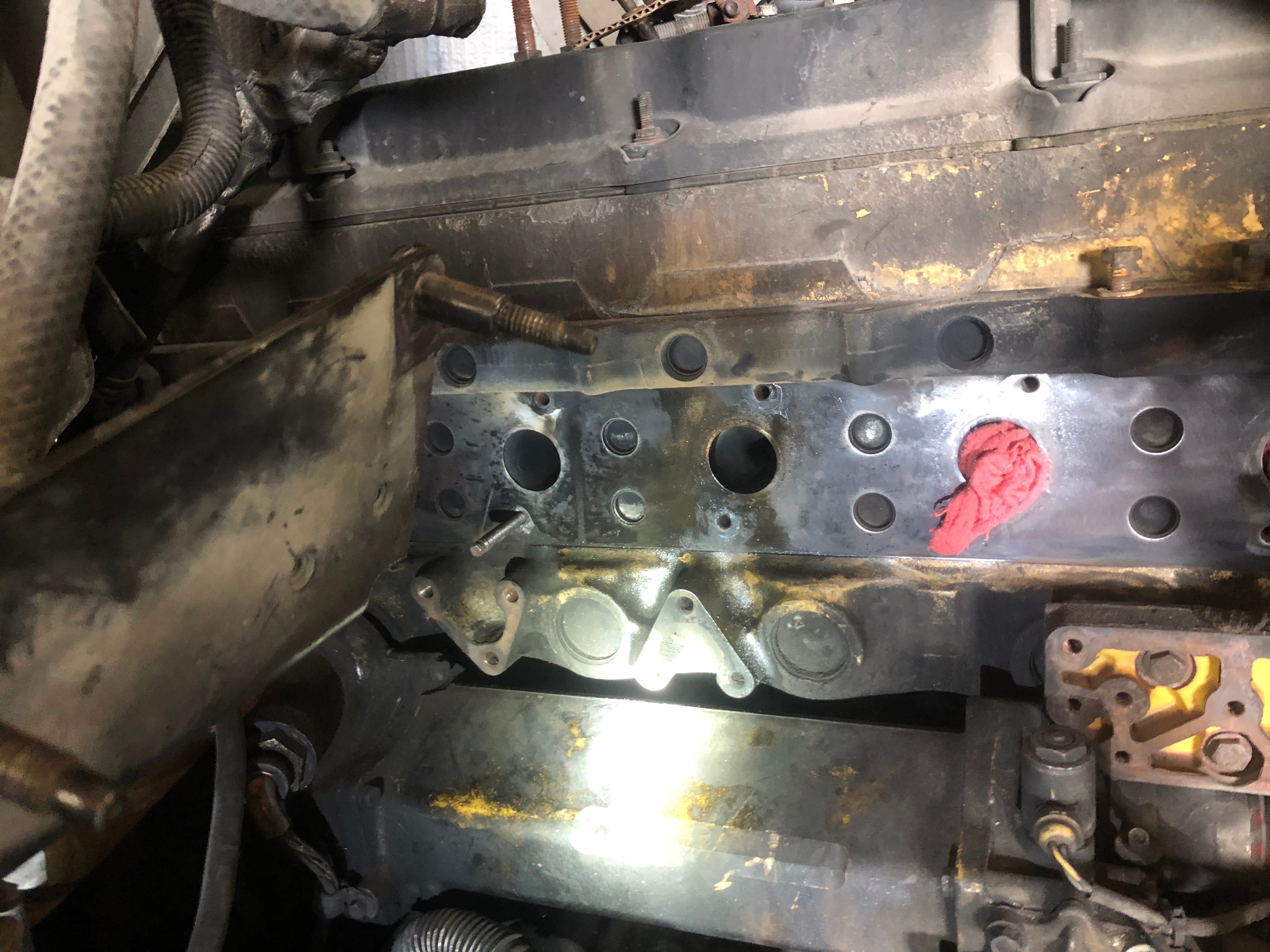
Hey just wanted to show some more of the interesting things I’ve got to work on.
1. Extending a trommel with customers old sheet metal
2. Repairing cracks and a hole were a stainless hopper had been punched through.
3. Super heavy duty split bushing hangers made to help with breakdowns on cement auger.
4. Emergency repair on a cement auger.
Tig alluminum on a hydraulic pump for a forklift supposed to be a bandaid till the new one came in but they are still running it lol.
6-7. Rebuild on the roof of a rotary impact crusher with hardox 500.
8. Lining aggregate hoppers with my brother.
9. Alluminum pivot handrail at cement processing facility.
10. Welding the broken studs out of the head of a international truck that snapped off.
I wish I could put more photos per post I have about a 1000 photos from my different jobs:)
Love the community on hear can’t wait to keep learning every day:)
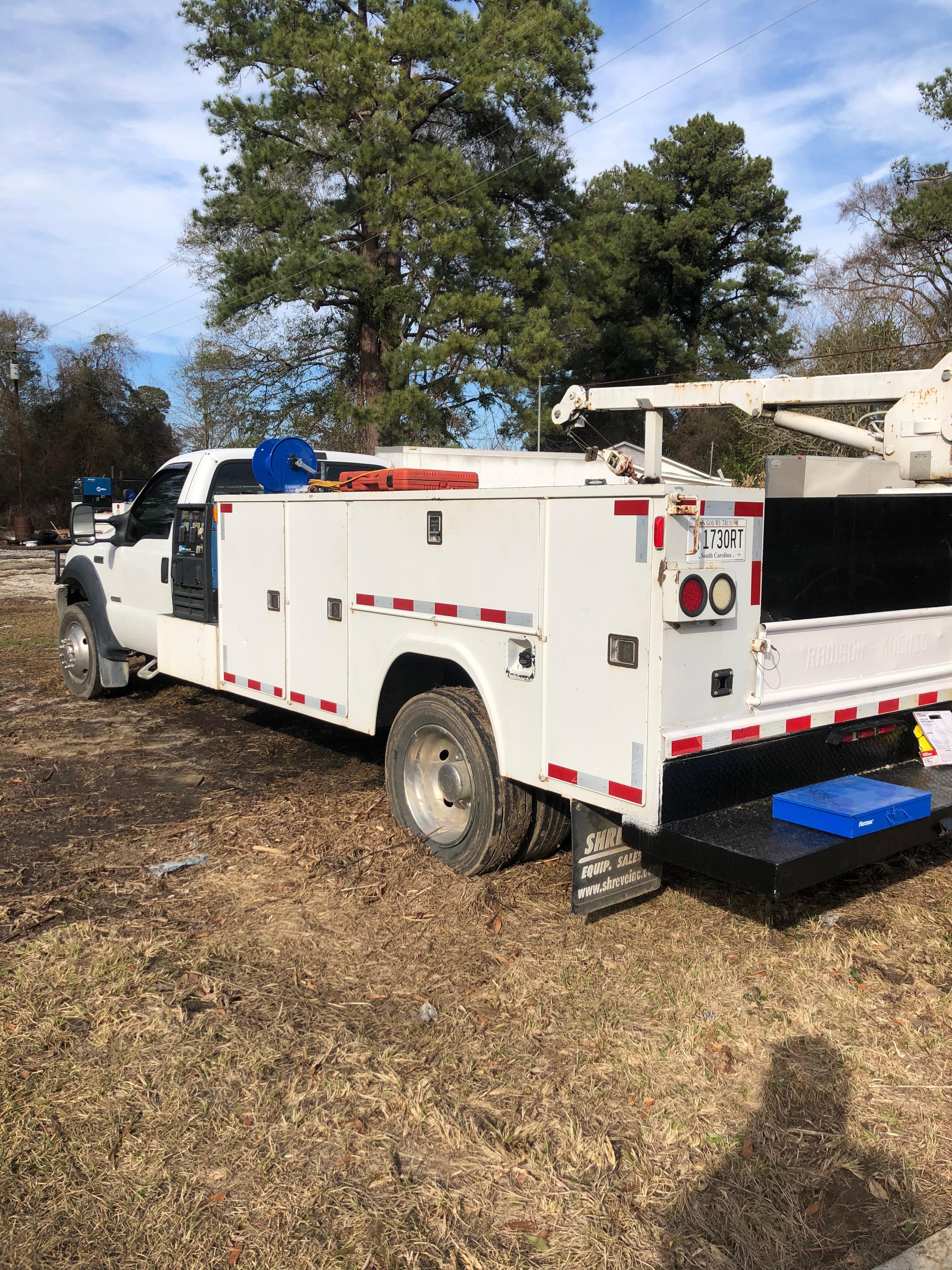
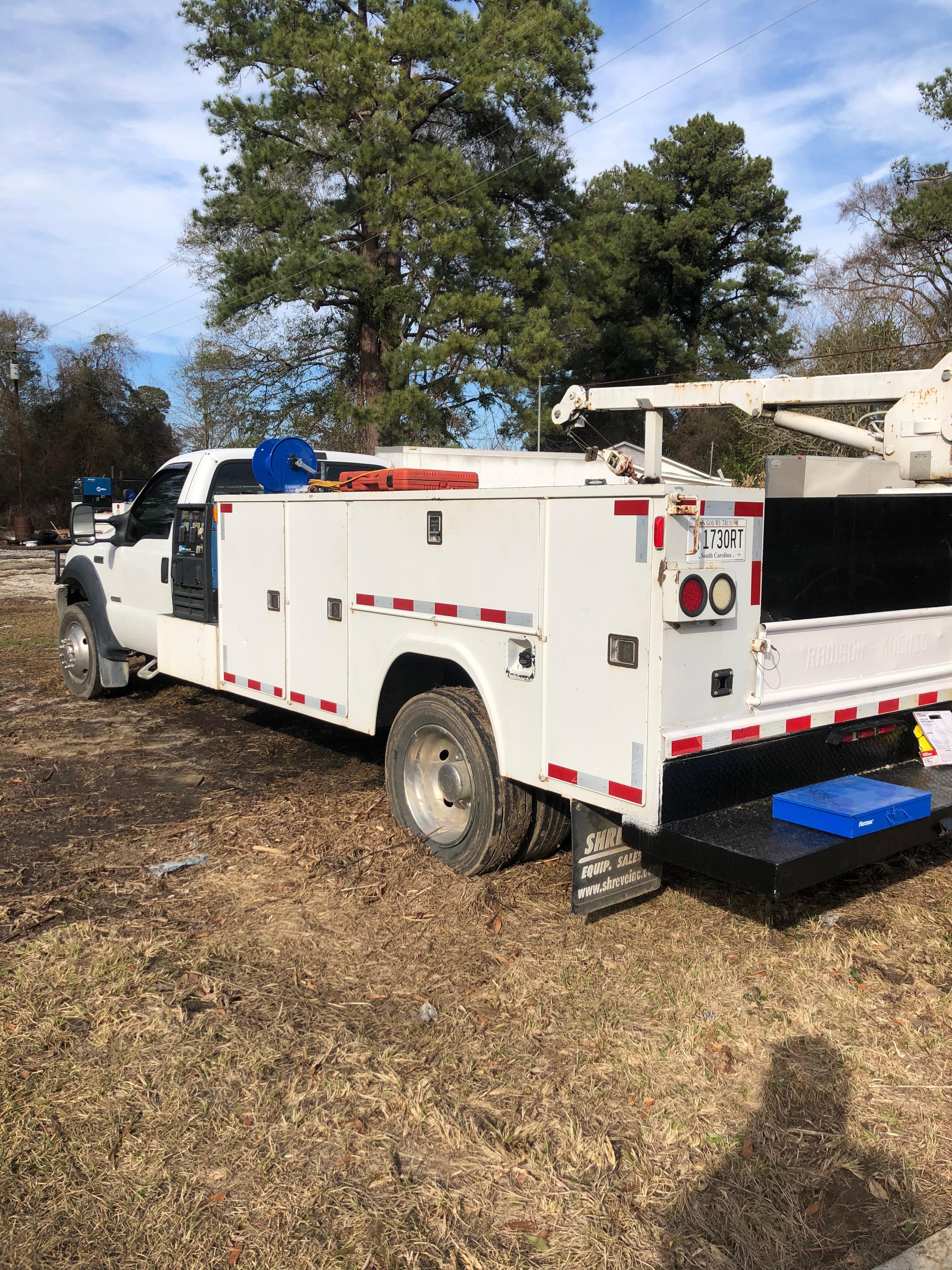
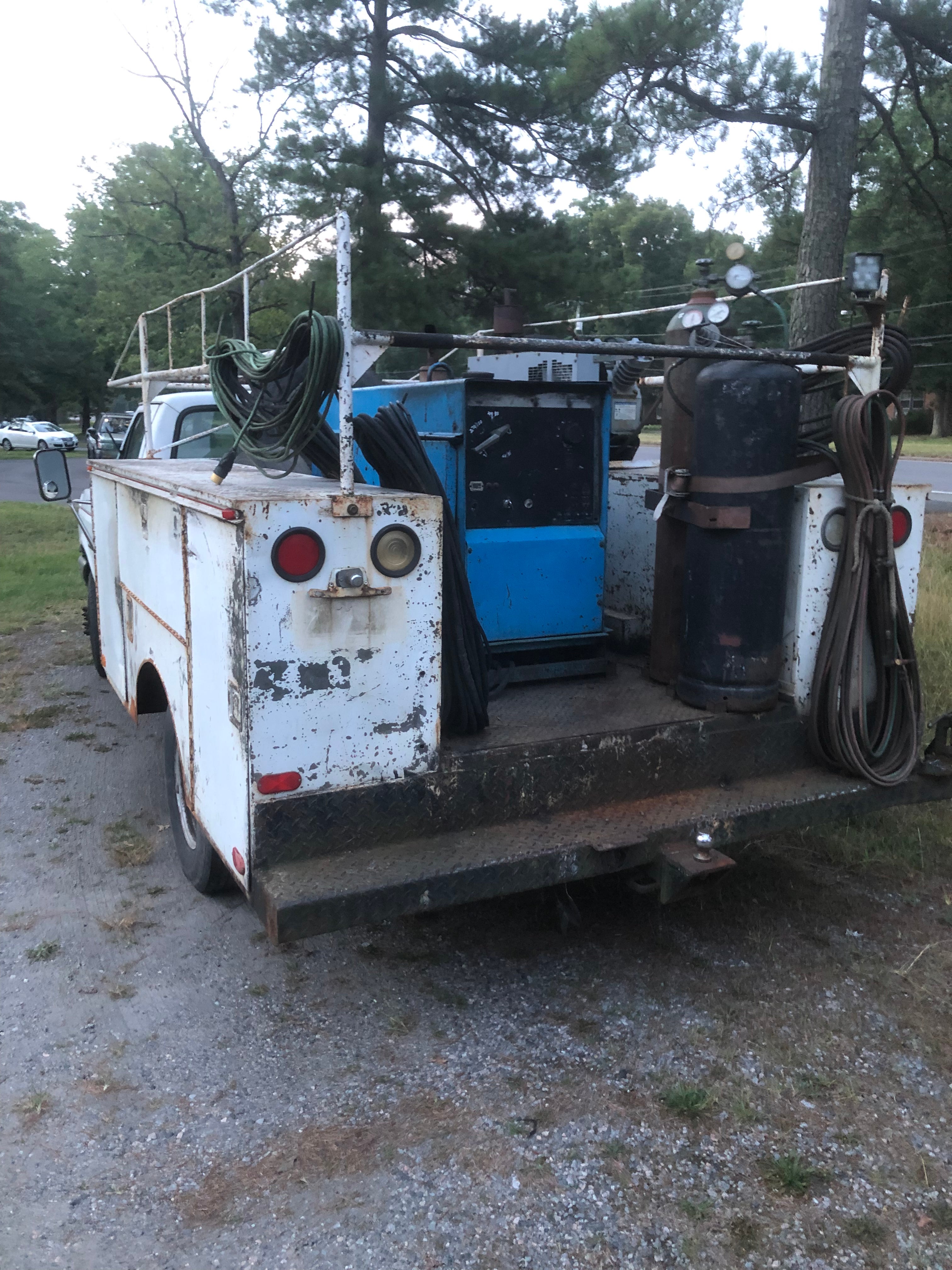
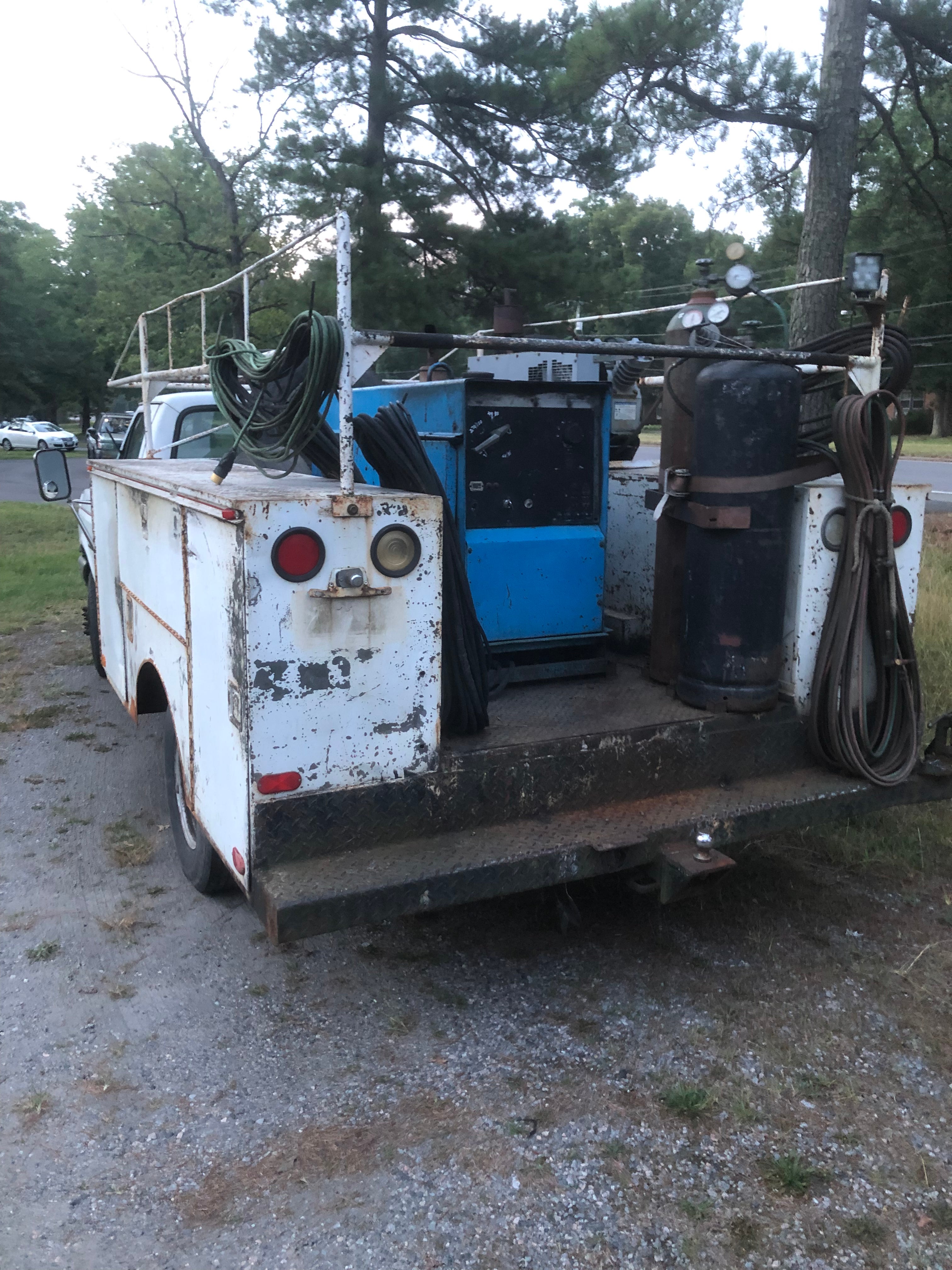
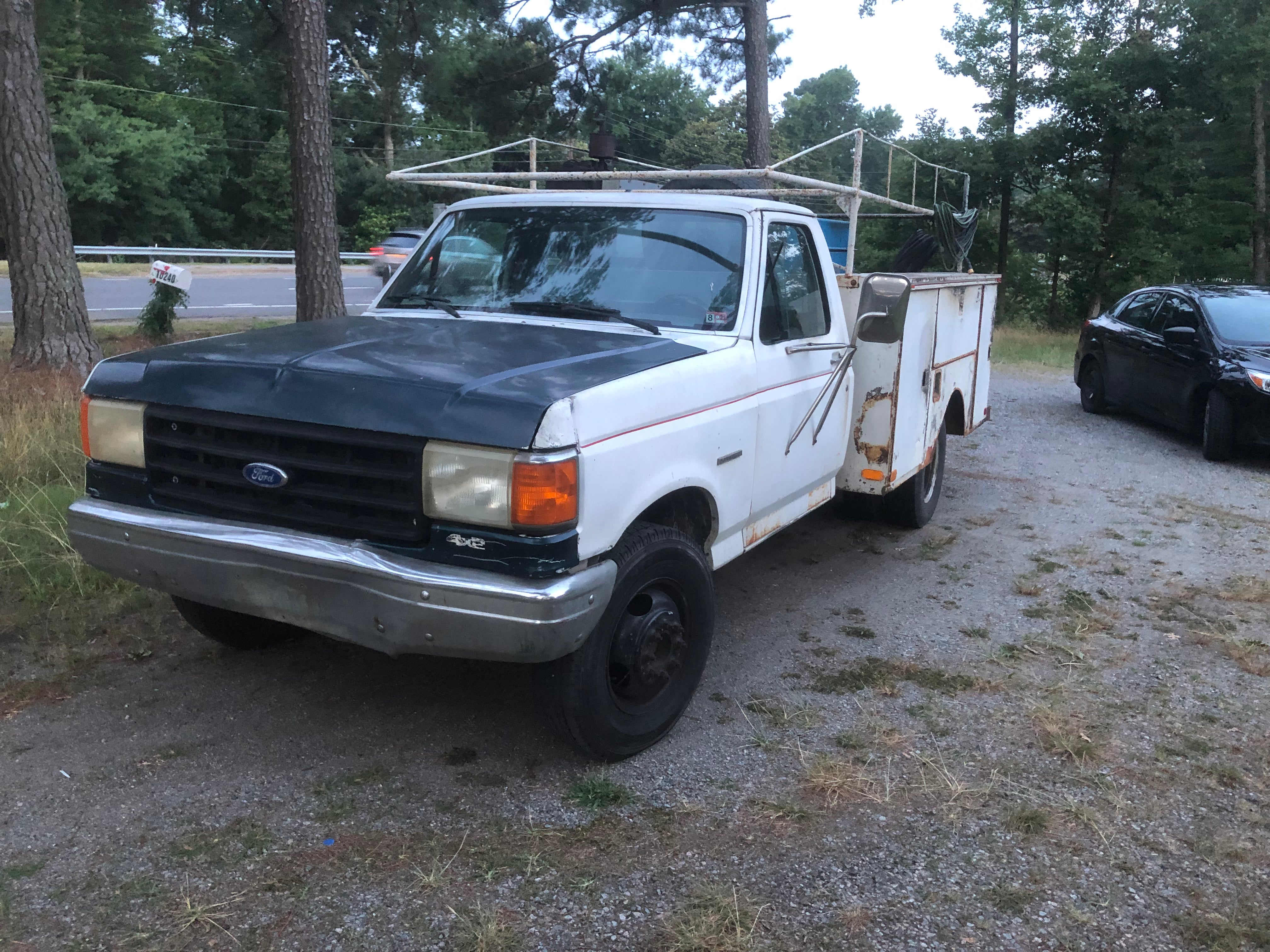
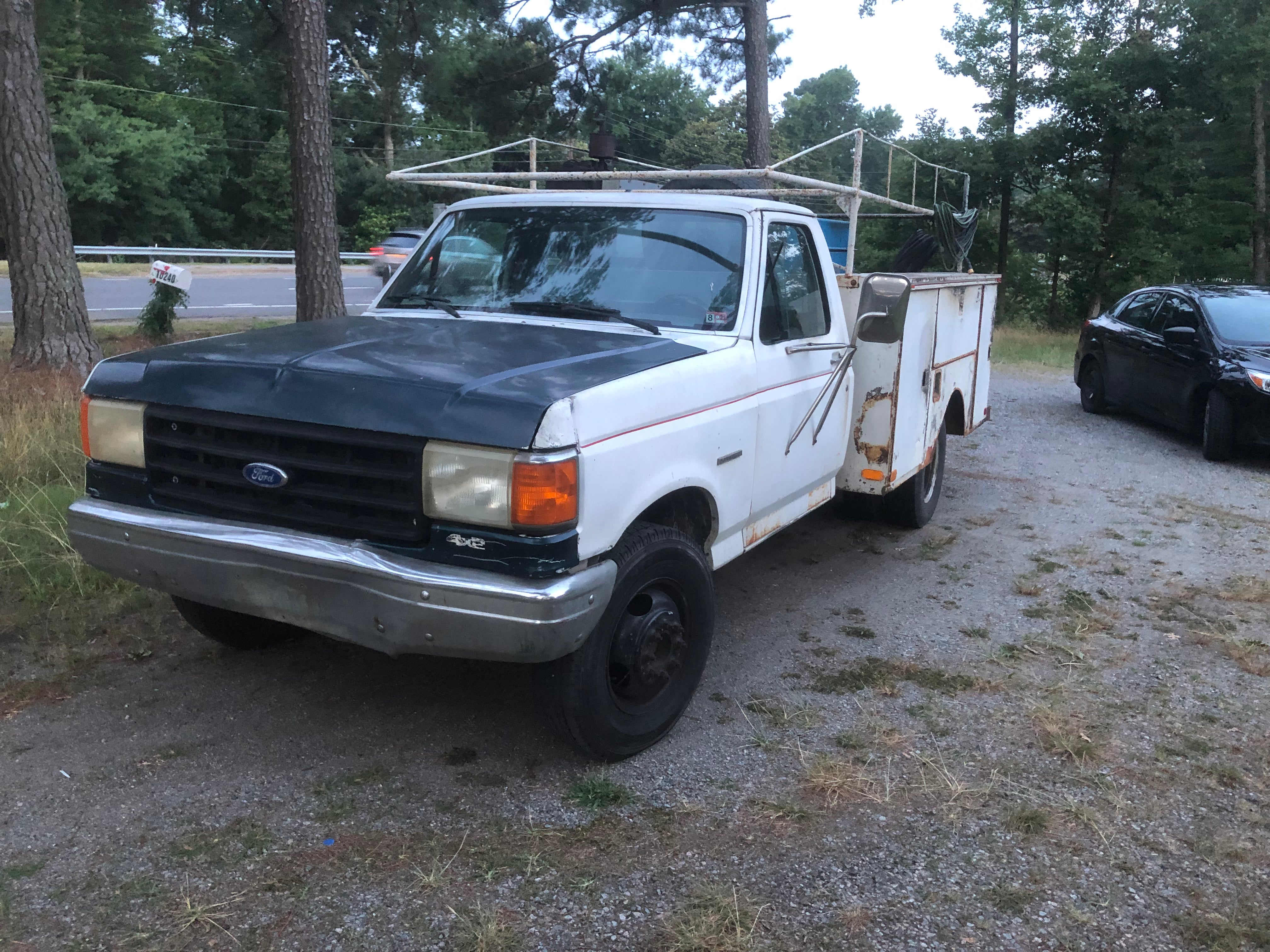
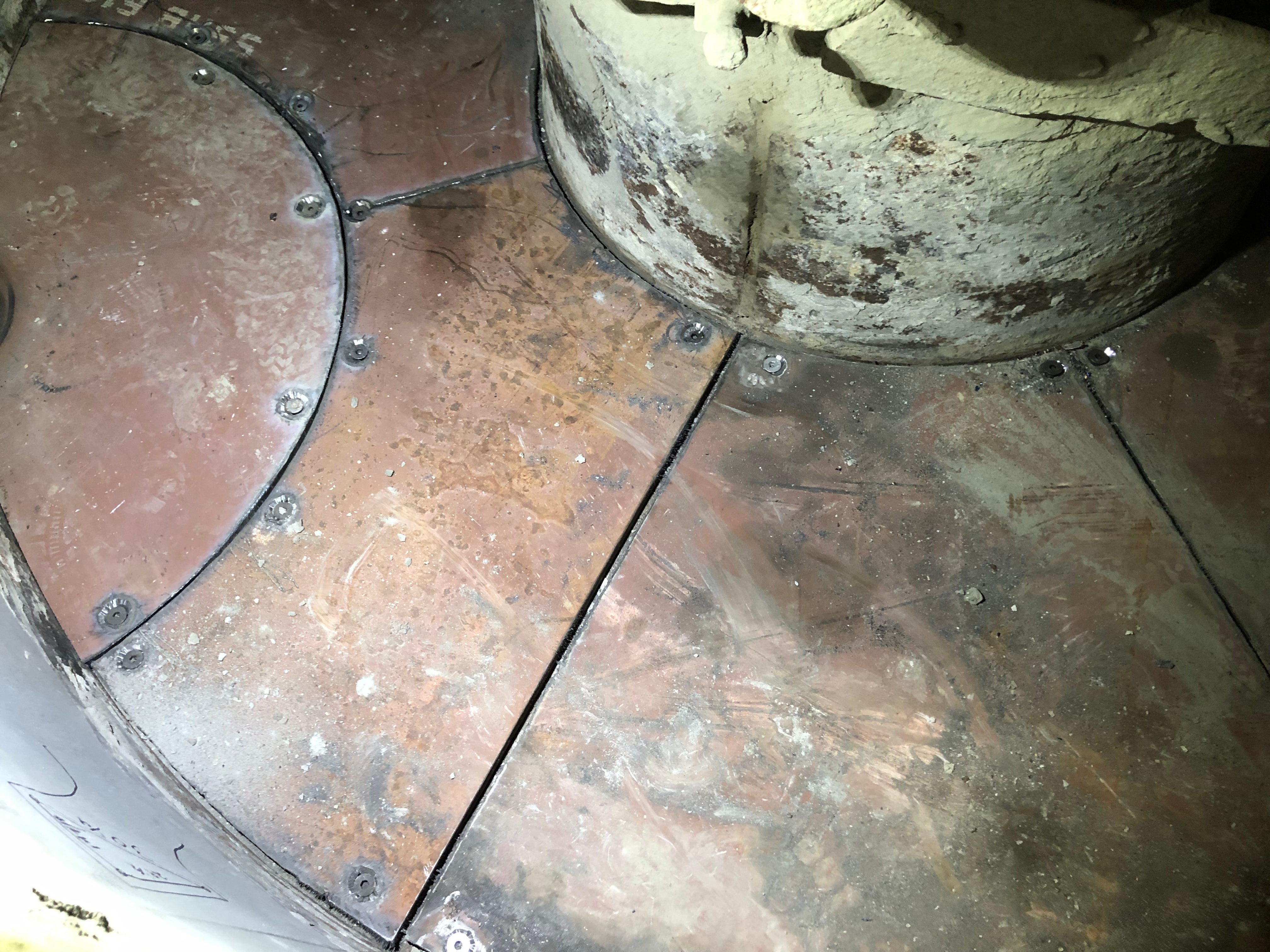
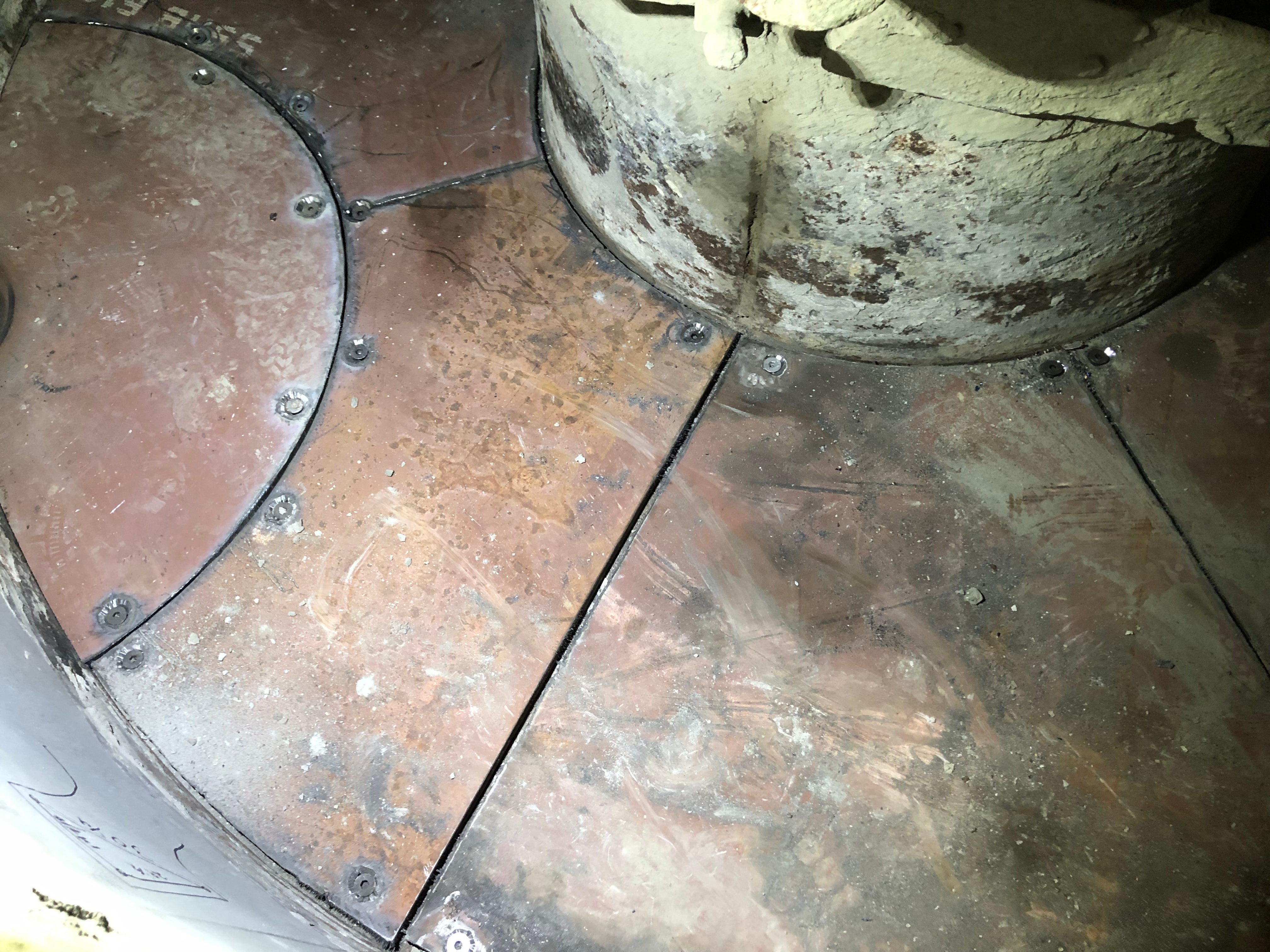
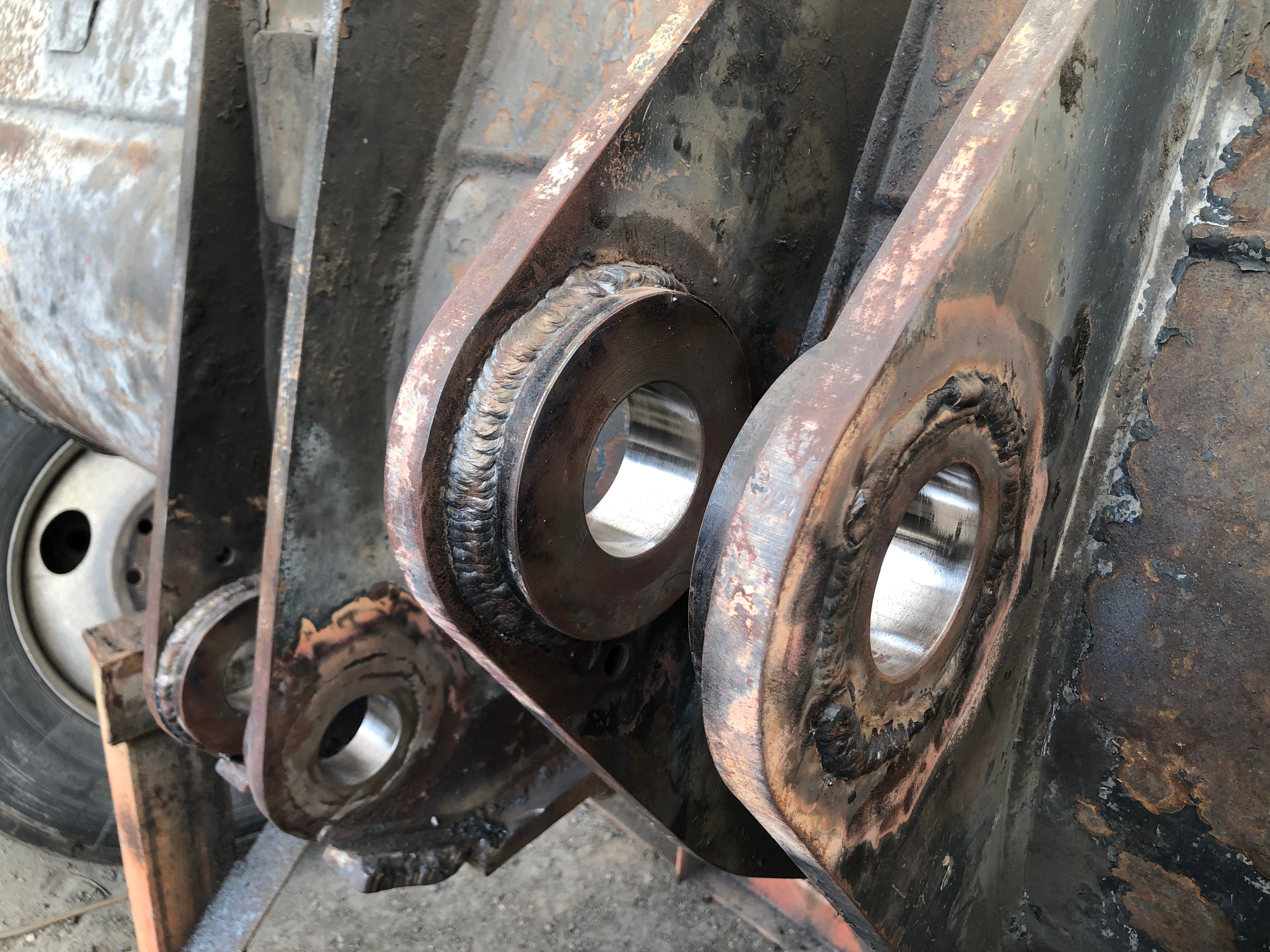
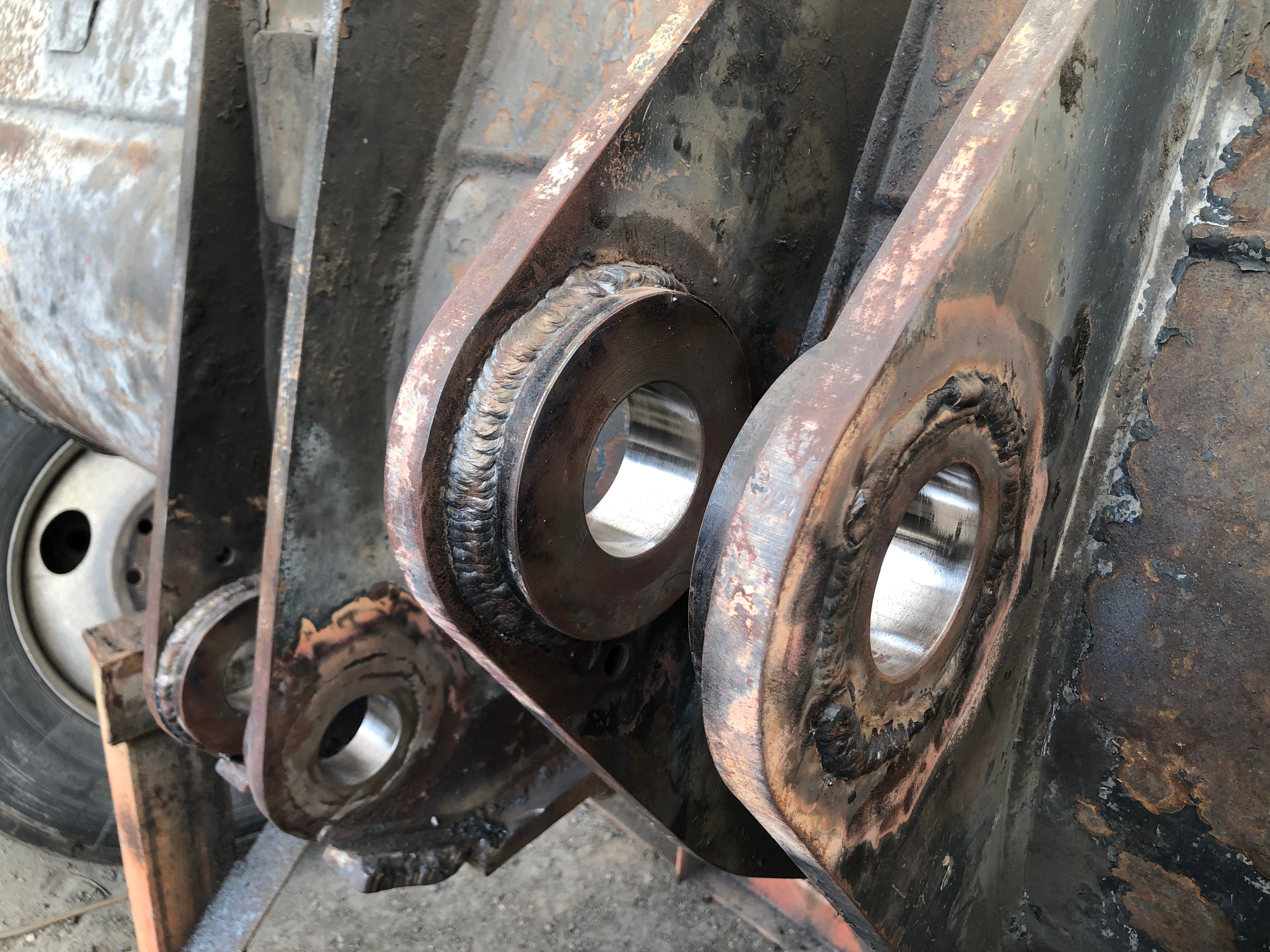
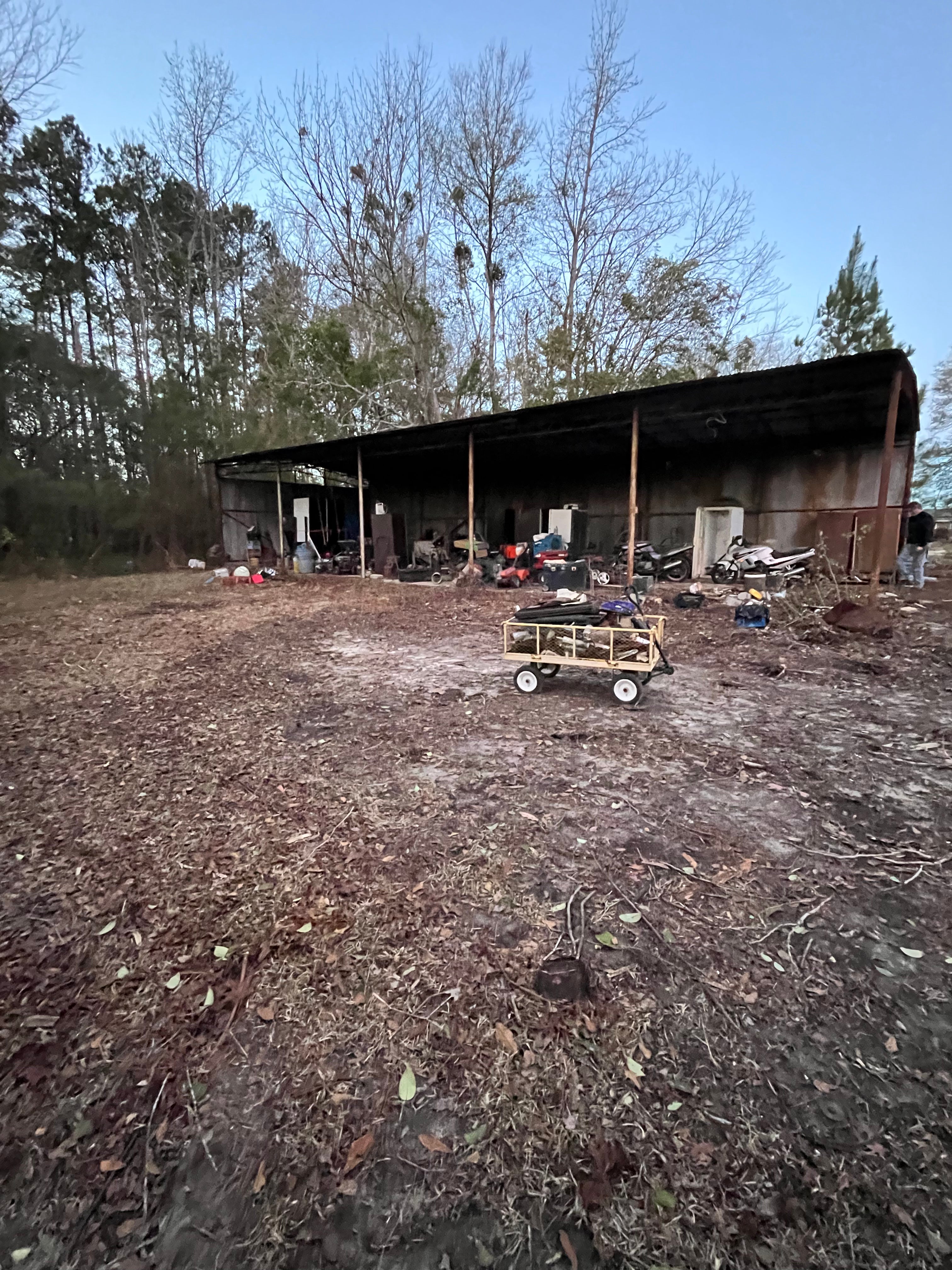
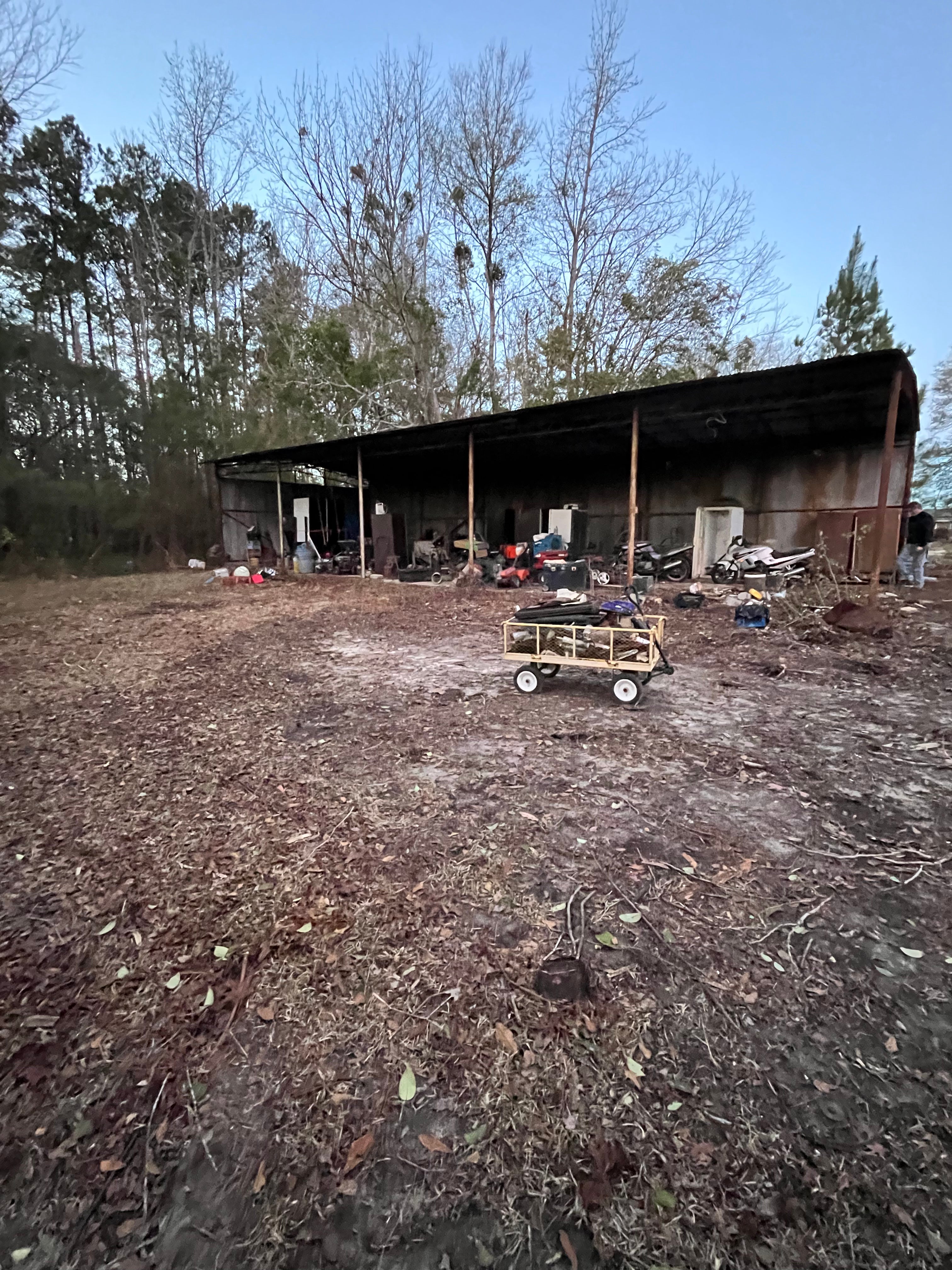
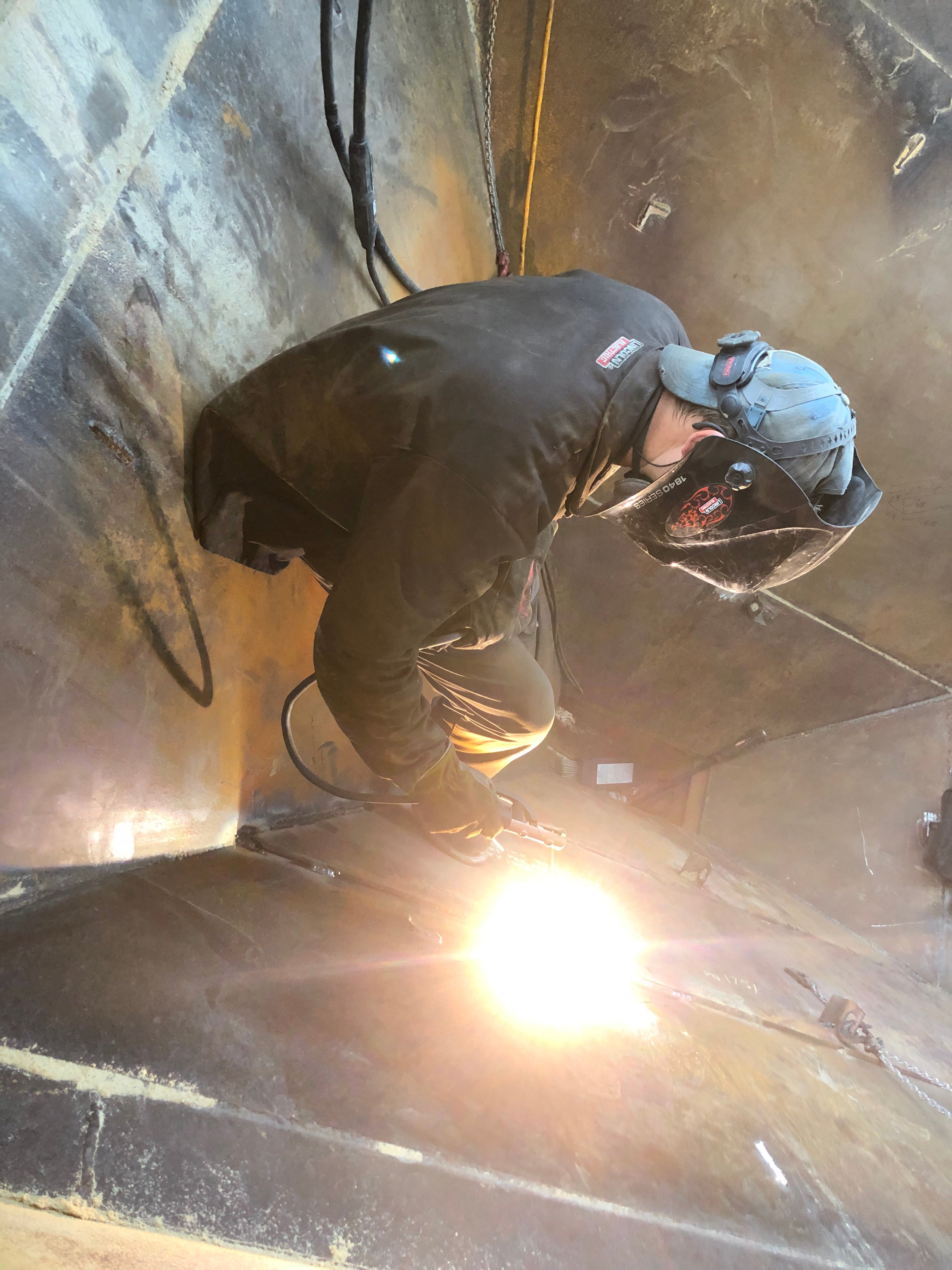
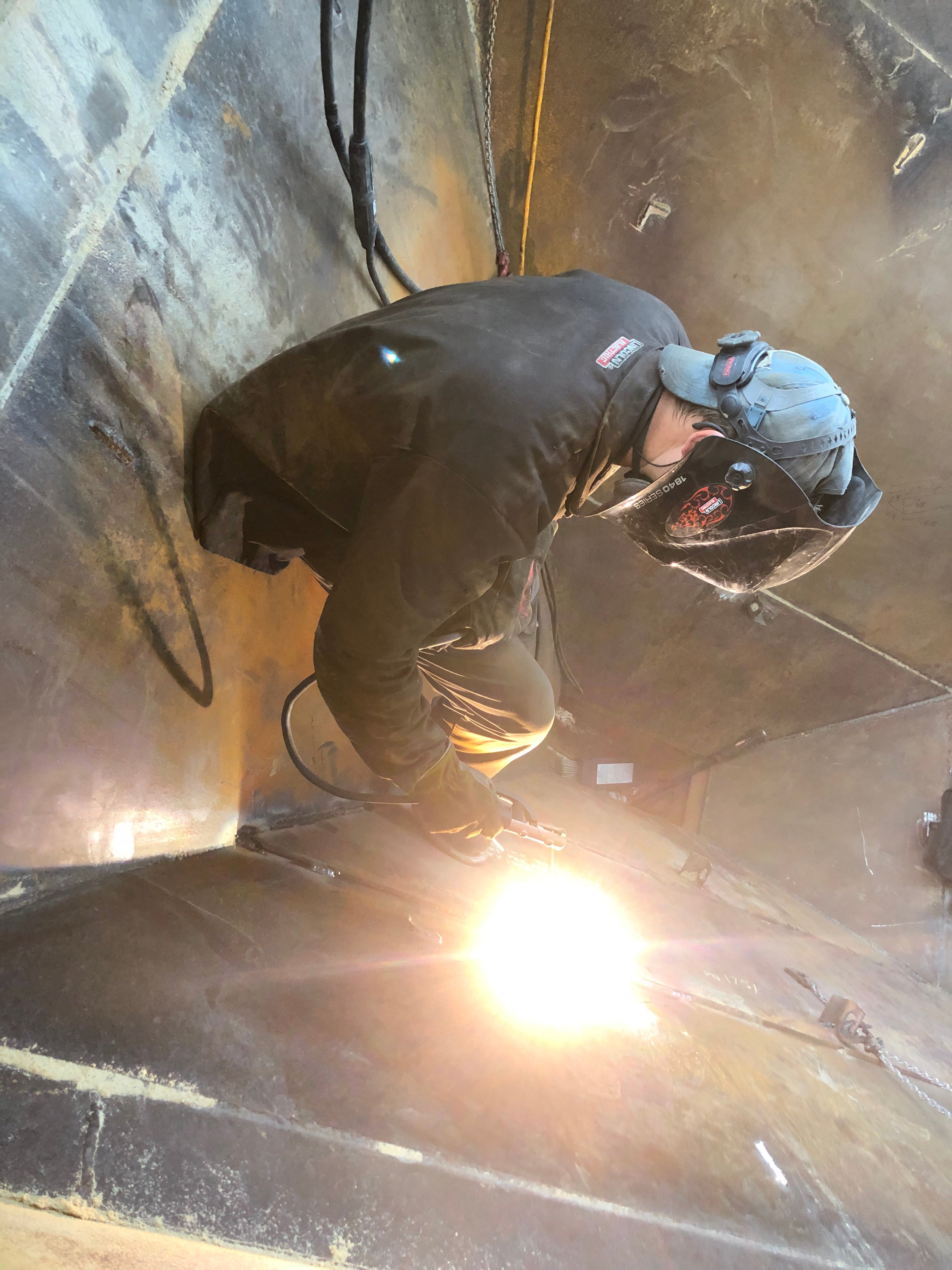
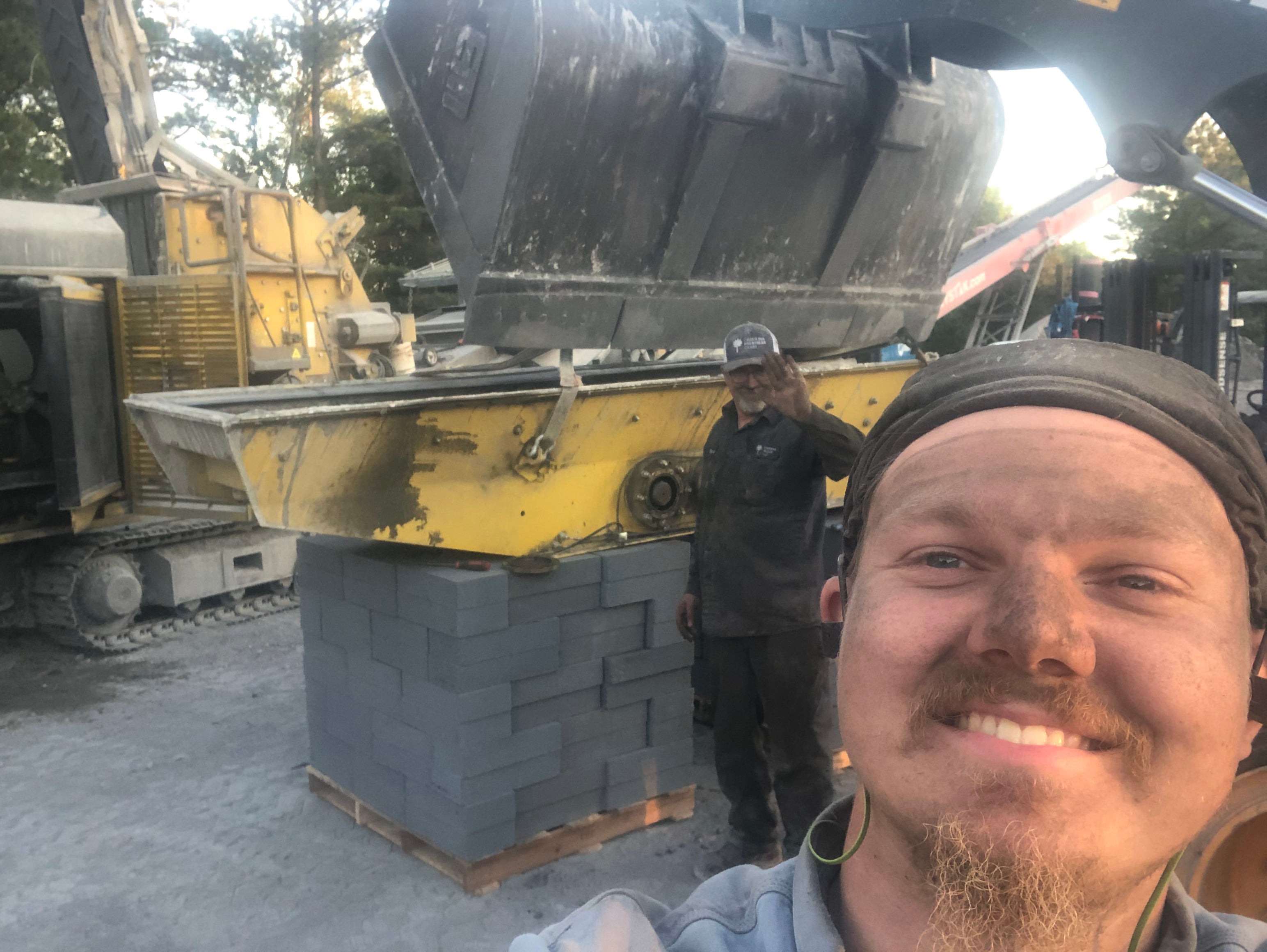
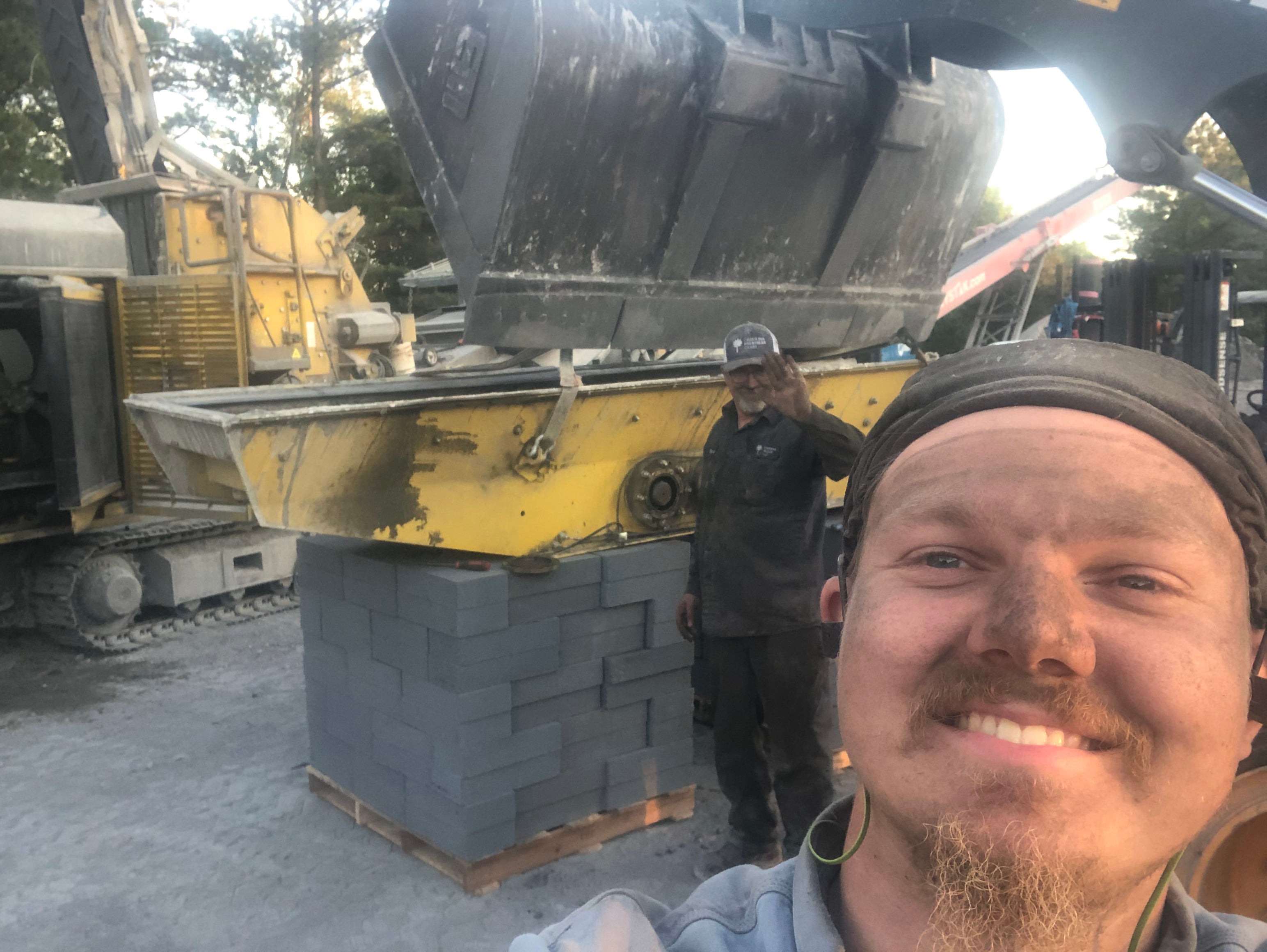
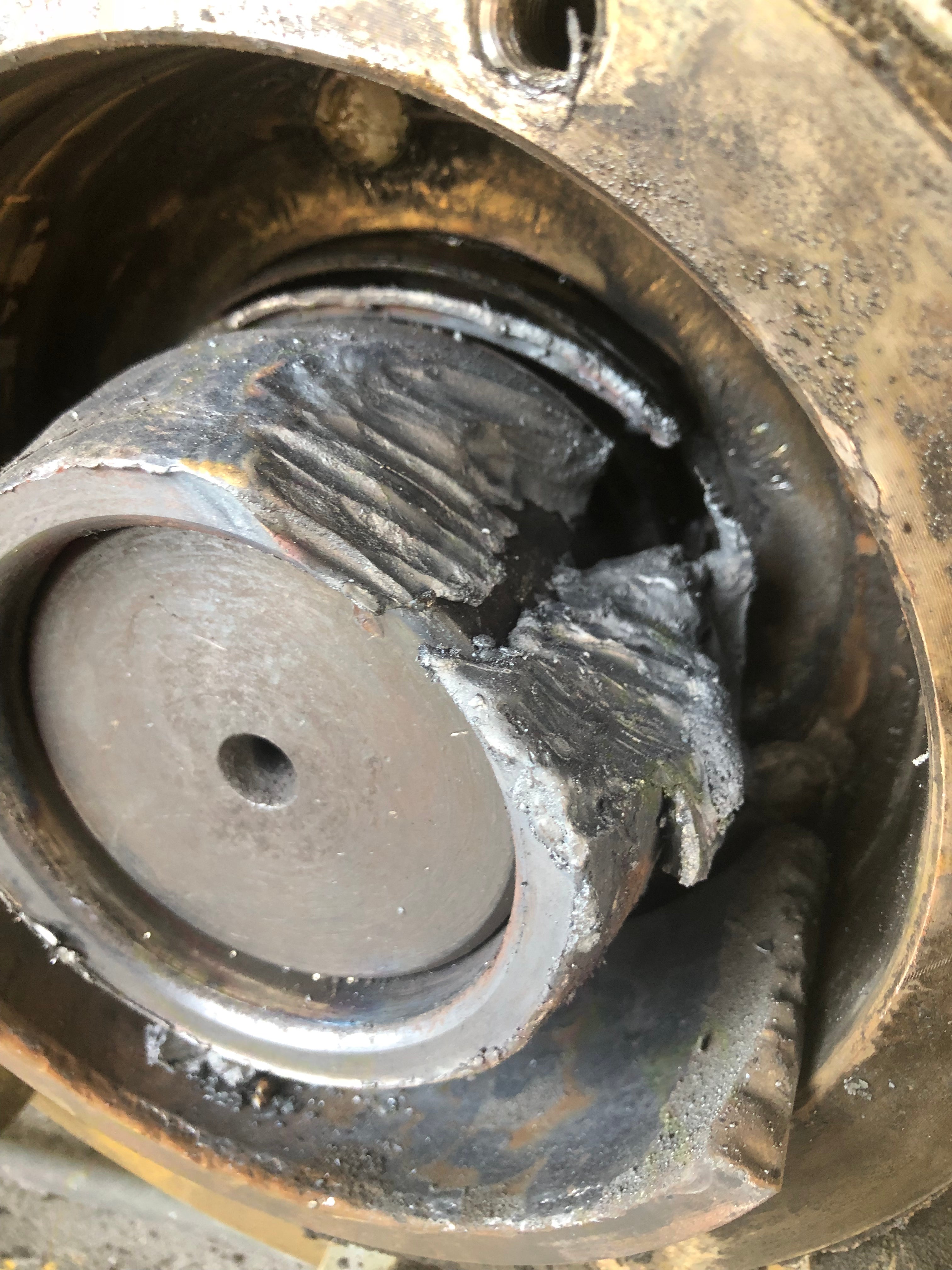
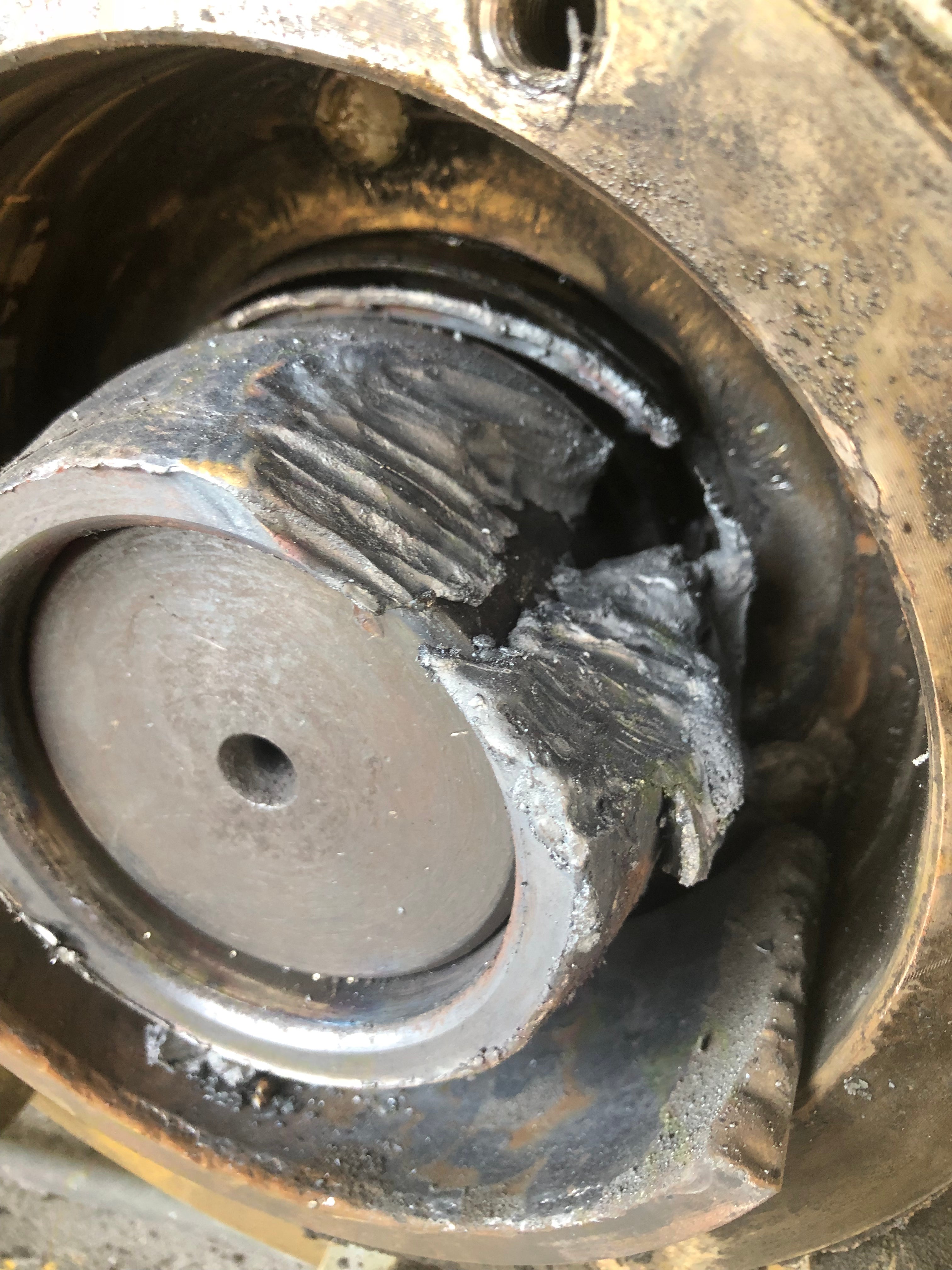
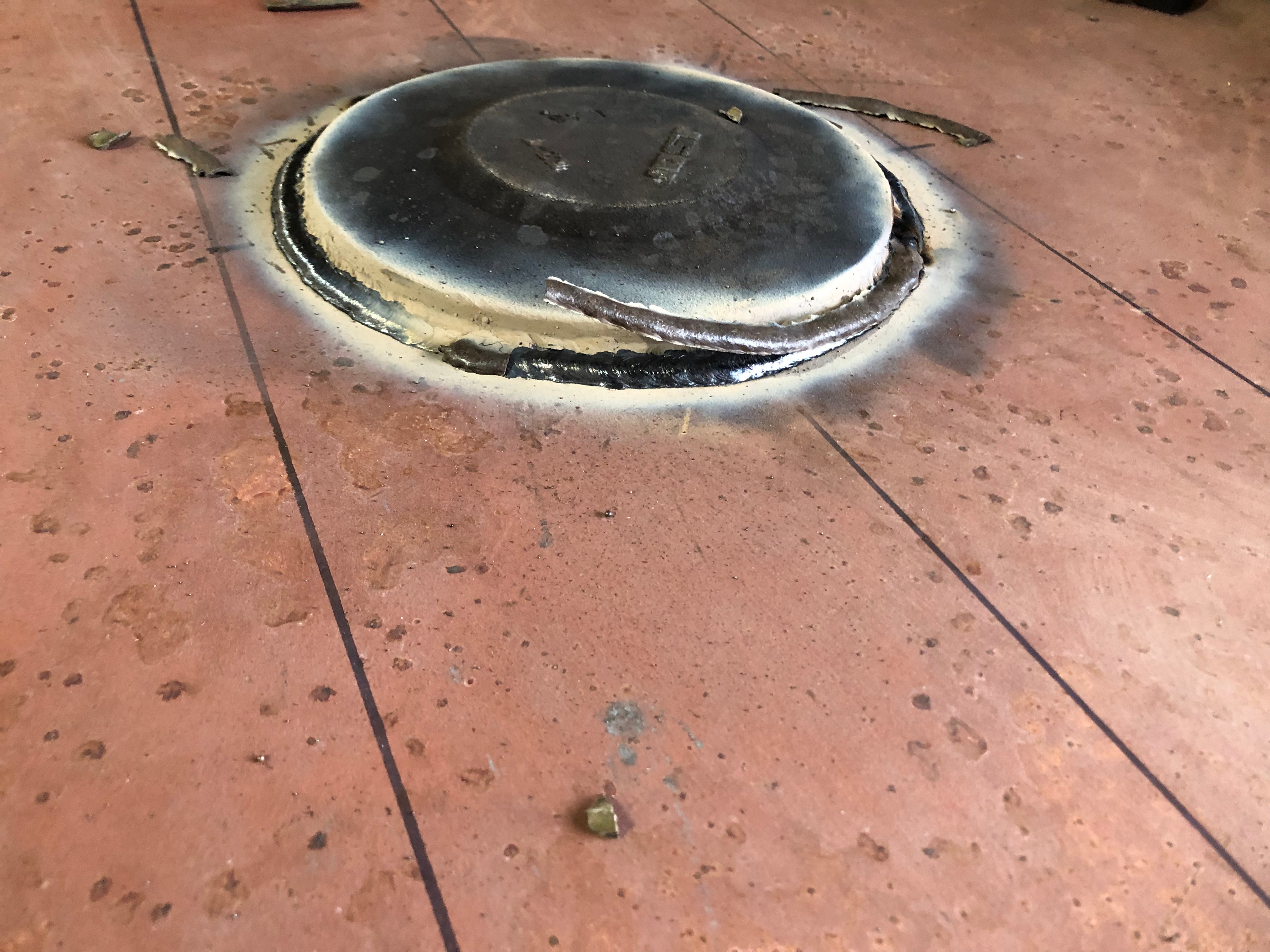
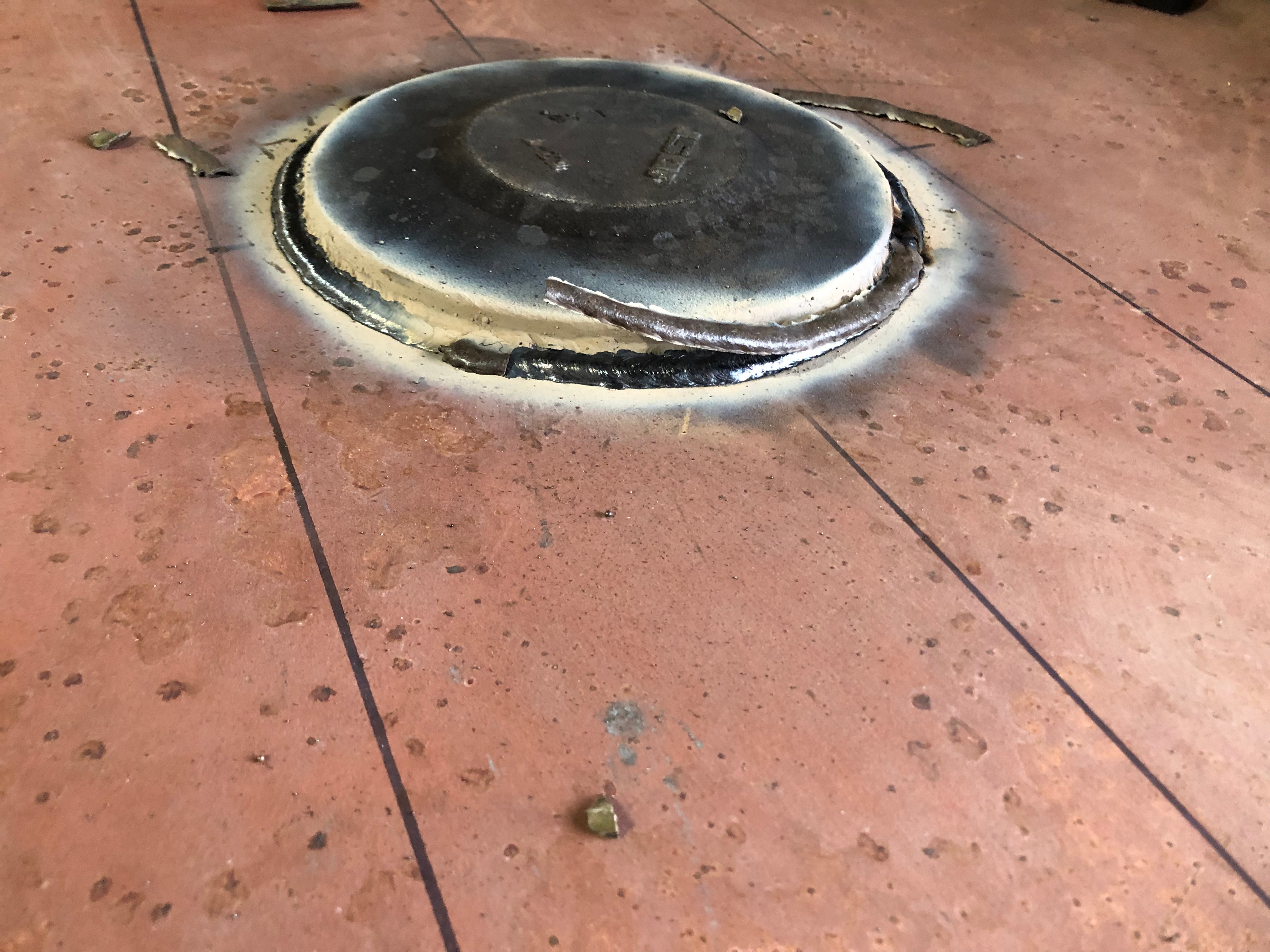
Hey everyone my name is Nathan Leiter. I’m 28 and own my own welding repair and industrial maintenance business. The first rig in the photos is the one I’m currently in and the old ford was my first rig. It had a Miller big 50.
I was working on industrial plants doing production and maintenance before college. I first started getting to weld right before I left for college. I studied business, then in college I worked in maintenance on appliance repair and then weld shop. Every summer I worked in the factories and welded.
I found welding tips and tricks podcast one year out of college. I had a passion for welding but was mostly self taught once I had the podcast I could listen to them while I worked. I’ve listened to every podcast and accelerated my learning.
I planned leaving my job 5 years ago and started to lay the ground work saving money and buying equipment. My wife and I kept our expenses low and we’re blessed to have somewhere to stay for very low rent. The last 2 years I worked for someone I made just over 100,000 and we lived on as little as possible. I was blessed with a boss who supported me as I grew. He gave me my truck for free it is a 2007 f550 with the long wheel base. It was cab and chassis with a blown head but it was free. I had it bullet proofed because it is a 6.0 I bought another truck with a blown head and used the telehandler that my boss sold me for a steal to mount the bed. I had to have front end work done.
It’s got a bulletproofed engine with 100,000 miles on it and almost 300,000 on the frame a Miller bobcat 250, a 4000 pound crane and 2 suitcase welders and a complete set of industrial tools. I had to fix everything myself or pay budies to help me. I’ve got about 20,000 in the set up and it has been going strong for me ever since I started. Like I said I was blessed and worked hard in the opportunities I was presented.
While I was working for my boss I convinced him to give me raises but I would use my own equipment. This allowed me to learn how to use suitcase welders build jigs and do production welding, weld repair on concrete crushers, screeners, scalpers, earth moving equipment, trucks, trailers, ready mix trucks, aluminum, stainless, steel, hardfacing bolt extraction, and all the repairs I could stand on the plant equipment. After leaving to be on my own my former boss is still my #1 customer and I give him priority. I’ve got a humble lean-too with really bad concrete but I had 3 phase power run to it. It’s a good start and I want to grow faster but I know that I should take it slow.
My father was a huge blessing helping me to do things right. He wouldn’t tell me I couldn’t do it but he would say if your serious then work harder and pay for everything up front. He kept me grounded. Here is some of the equipment I bought while I was working for my former boss.
I use a Miller bobcat 250
I have 2 8vs suitcases
One 12vs suitcase
A Miller 161 stl
a everlast 210 stl
A everlast 255 ext
A Lincoln 350mp with a push pull gun
A old Miller dial arc high freq ac unit
A old 400 amp Hobart for arc gouging
I have two Amazon cheap buzz boxes
A thermal dynamics plasma cutter
I have some shop equipment but most of it is in storage. Still saving to get new concrete and close in shop.
75 ton press with a swag finger brake for small stuff
40x10 Pearson milling machine
Langmuir fixture table
Small craftsman lathe
8k telehandler that runs rough but does everything I need it to do.
I just feel like I stumbled upon a great way to accelerate your journey to having your own business and did it slowly so that it was as safe as it could be. Definitely get a Cpa immediately though lol
I absolutely love the guys on welder skills and the blessing that wtat and welder skills have been are far beyond the cost of the platform. Would love to meet the guys one day:) I’m in sc but I travel a lot for work:) I really appreciate the help of all the instructors!
A month ago I took on this trailer , making some small odd repairs, including removing that battery, and relocate in side the newly mounted tool box. The real challenge was replacing the hydraulic pump , hose and fittings to match up with the original hydraulic ram. Then figuring out how to wire in the switch for a single action hydraulic line ( manufacturer had it set for dual action)
Finding the right fluid wasn’t to difficult, and with support of a local hydraulic parts supplier it only took a couple of trips. lol
Ill show the hydraulics in action on the next video.
This thing felt like I was working on a giant rat trap. Now that I’m done I want to see it dump a load. lol also make me wanna build a crane or something, imagine that.
Hi all. I'm Rick. I've been welding for about 20 years as an occasional part of my job. Mostly MIG aluminum & steel, and some stick. I've never had any formal training and I thought it was time to find out all the things I'm doing wrong and/or "the hard way". Also, I just bought a TIG welder for my home shop and it is WAAAY more involved than I had anticipated! 😄 I'm looking forward to learning those skills the right way right off the jump. I feel like I've found the right place to get it done!