Using Miller Pipe Worx 400 to practice for a weld test. This is the most expensive machine I have used. 3/8 inch plate with 37.5 angle bevel, 1/8 root opening, 1/16 landing. Mig root downhill. Dual shield flux core up hill. If click the trigger on any of the two guns the machine will automatically switch over with the saved settings. Crazy expensive
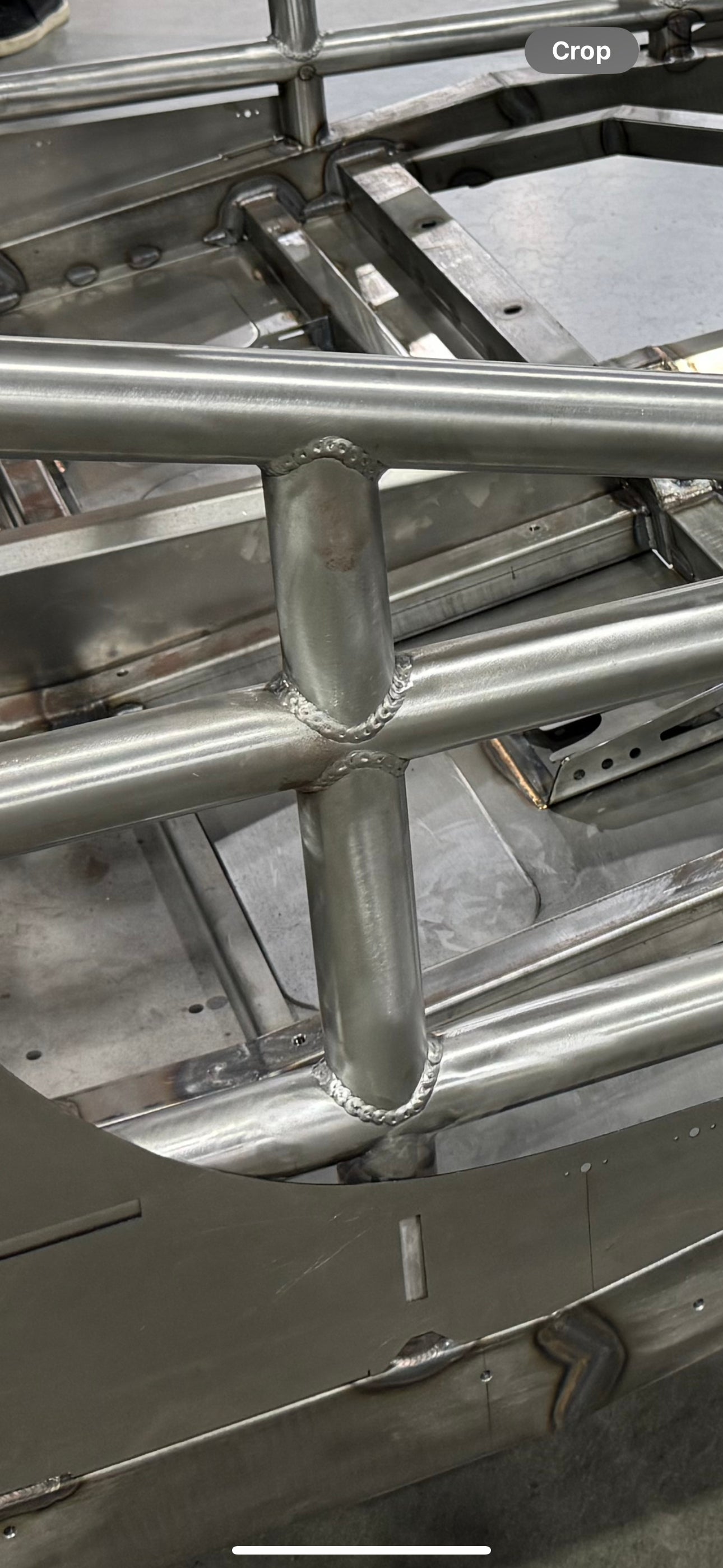
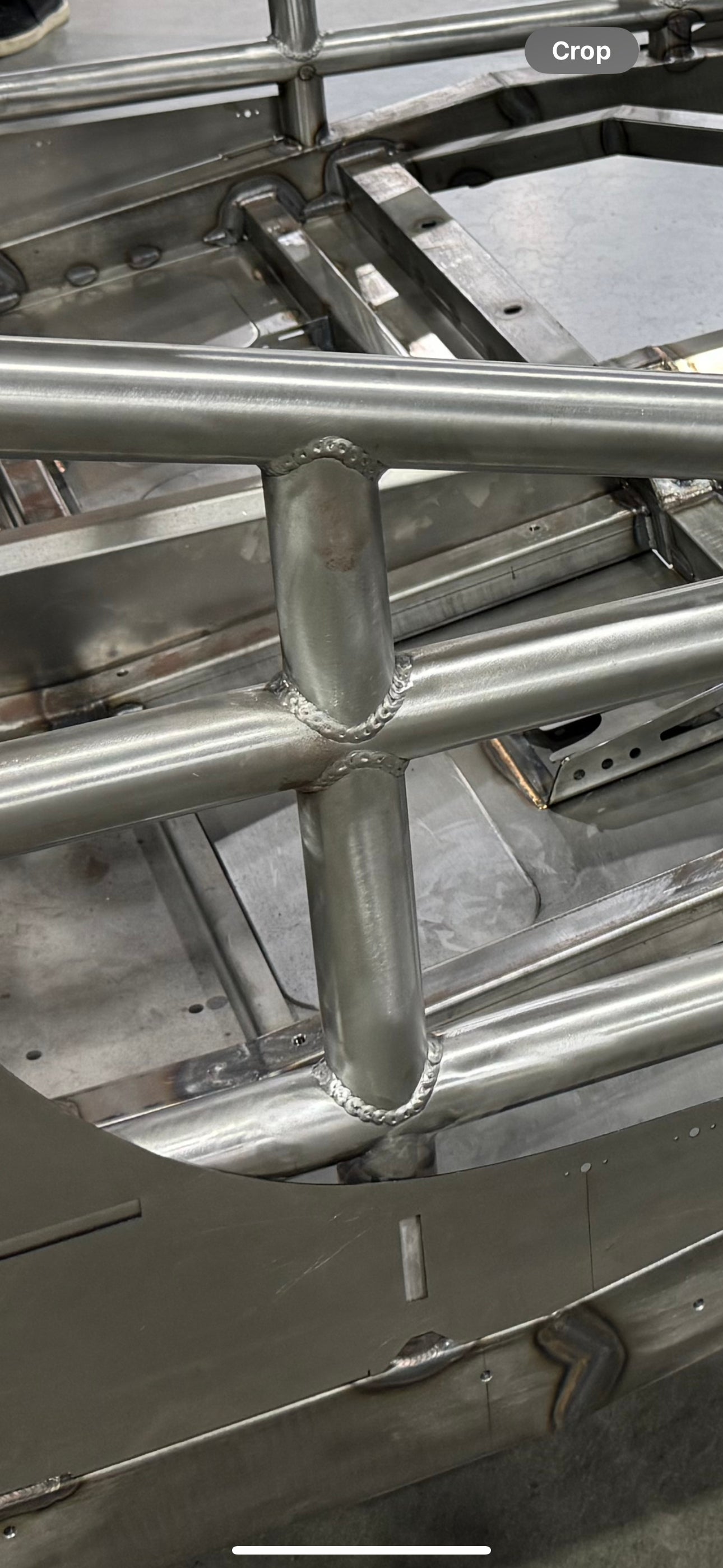
Hi all,
Tonight I was given the opportunity to have a tour of a race teams facility.
This is a photo of one of the chassis, they are a controlled component by the racing series and are made from chromoly
I have a question about the “tack” method of mig welding some of the tubes.
When I asked the guide, I was told that they would like to tig everything, but these certain joins are required to be migged, as per the design rules/specifications.
Just wondering if anyone could give any insight as to why these certain joins would need to be migged? As opposed to tig?
And also is the stack of tacks method used due to it being chromoly and needing to control the heat input? Is this a viable technique?
I thought the series of tacks would maybe cause potential failure points, especially with the craters on each?
I will add another zoomed out photo in the comments
Thank you 😁
Hey everyone!
I own a small shop in NE Indiana, and I specialize in tig/micro-tig work. I do a fair bit of production runs, and lately I've had a few requests for some brazing/ silver soldering.
Unfortunately, I haven't had the opportunity to practice either one. Does anyone know of any good classes around the country for this? I've had to turn down a few jobs, just because I'm not confident in my brazing skills. Thanks!
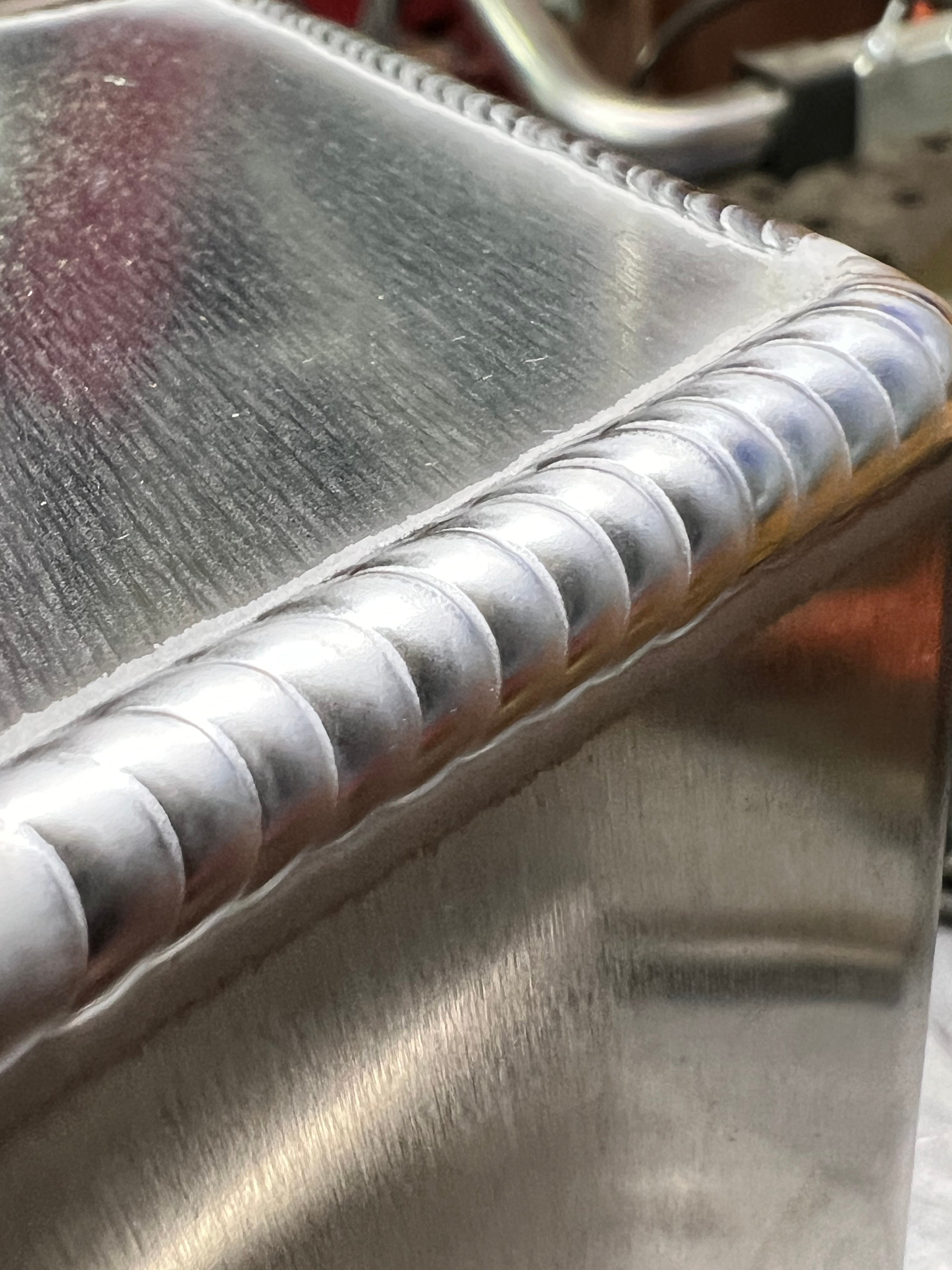
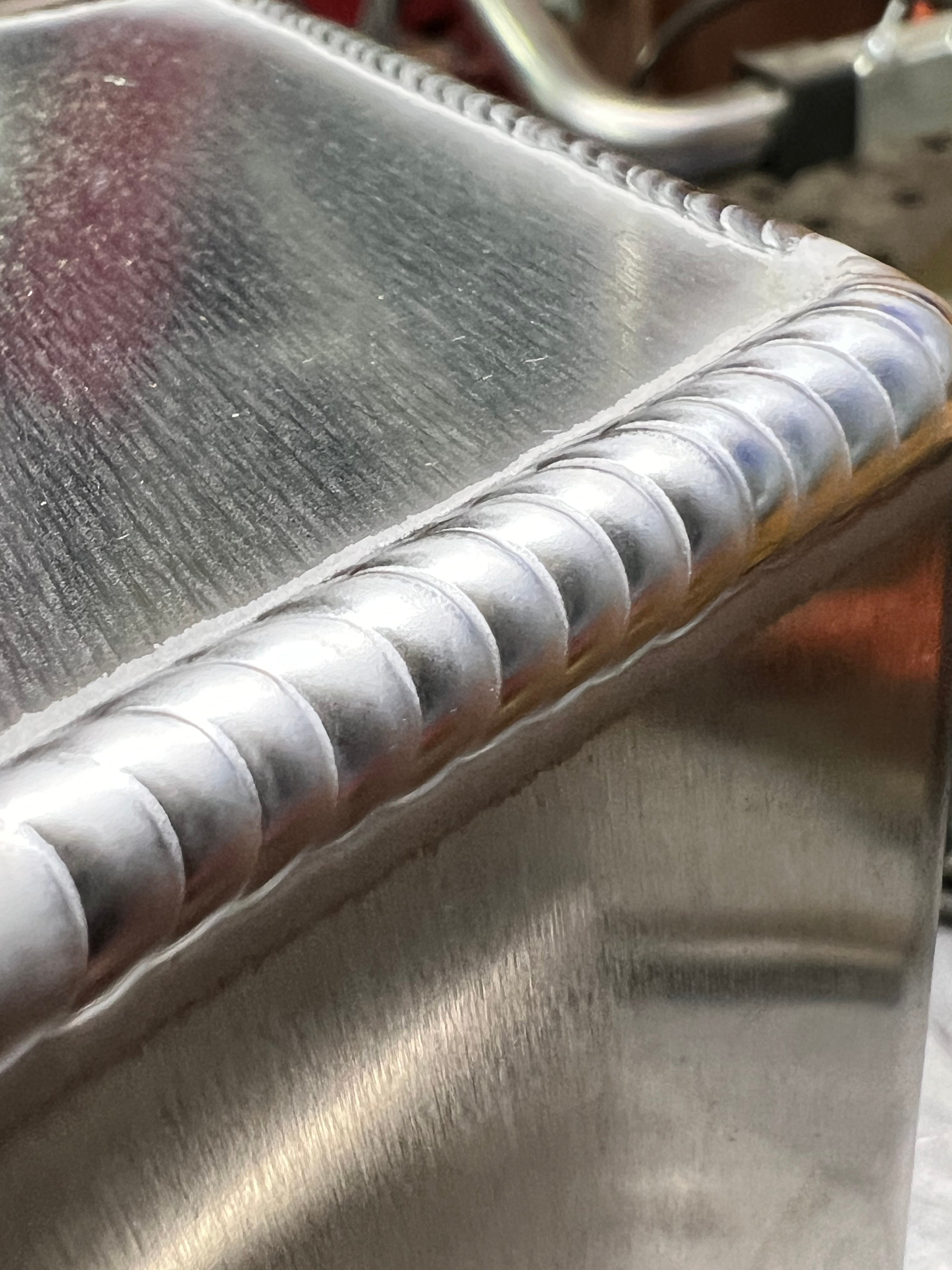
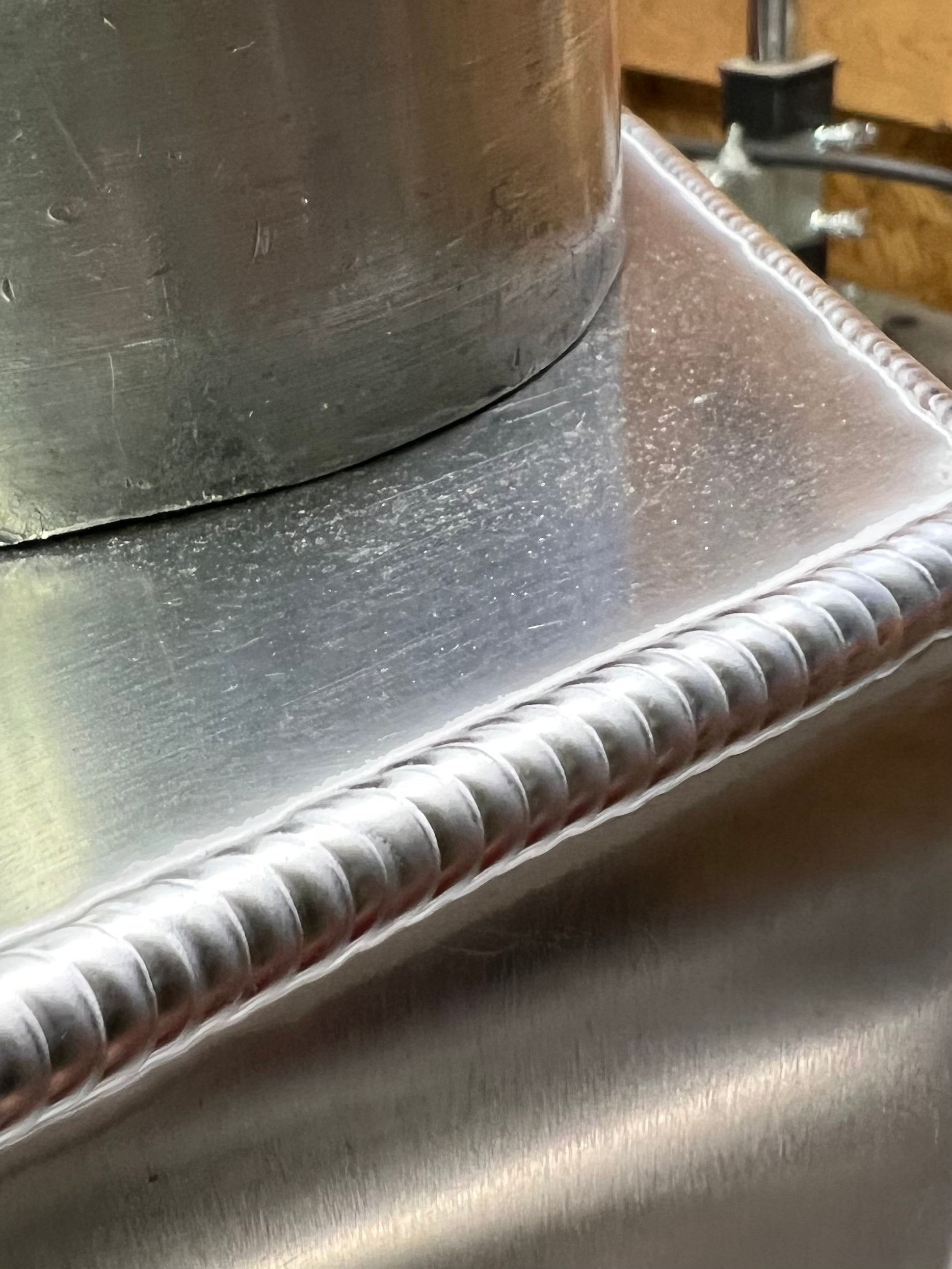
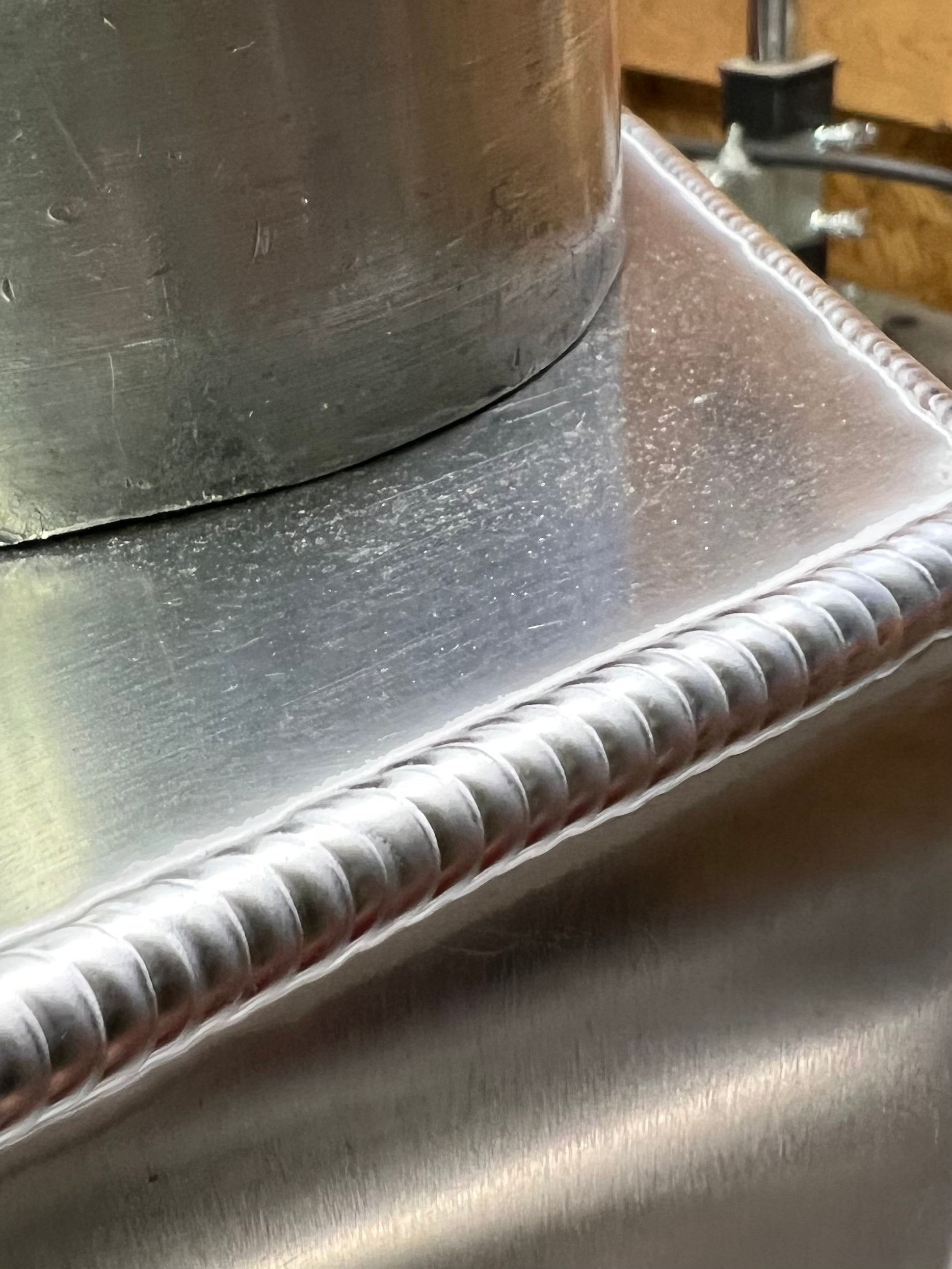
So here’s where we are Weld wise on Aluminum so far. Gonna be a cool video.
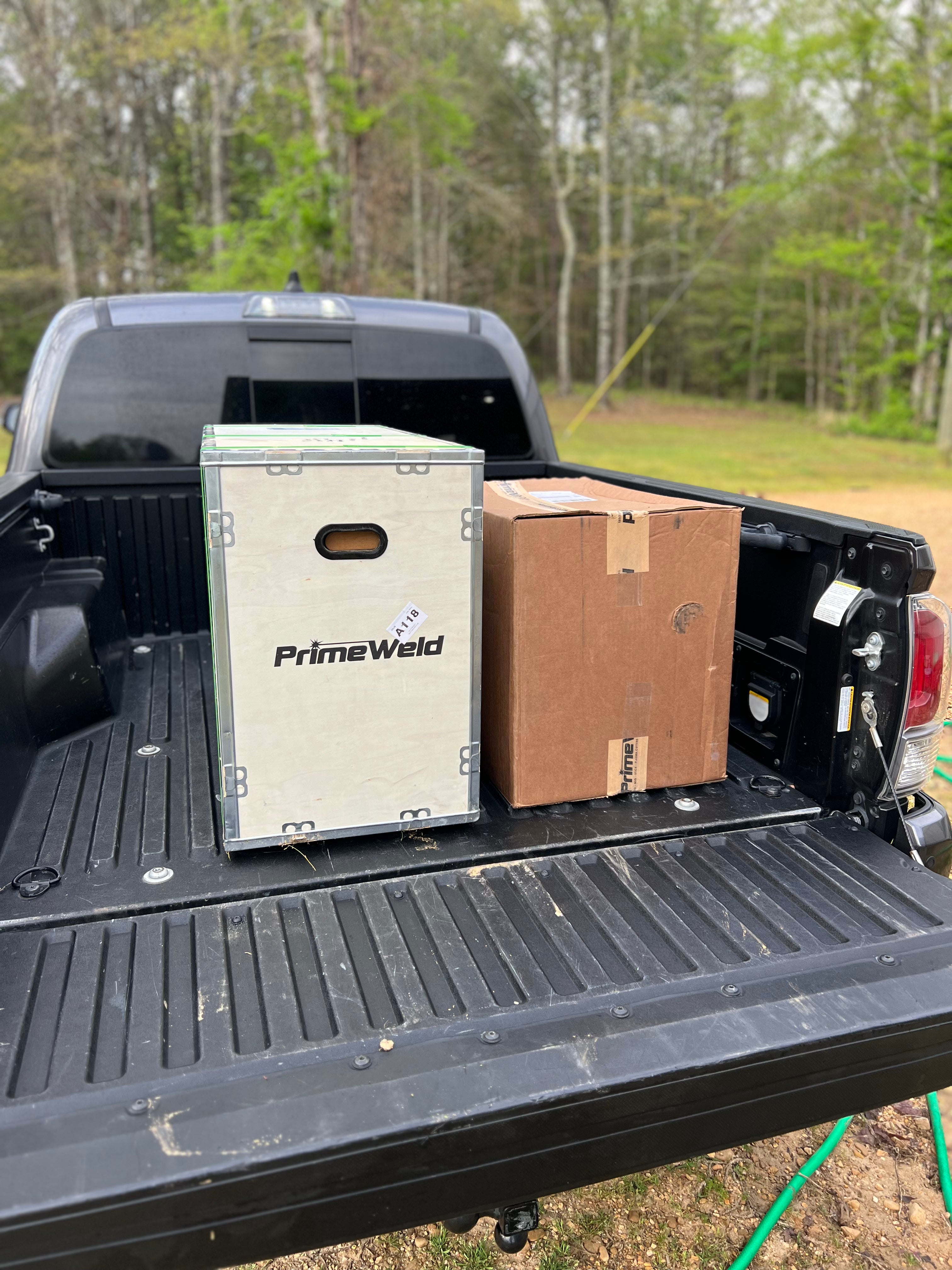
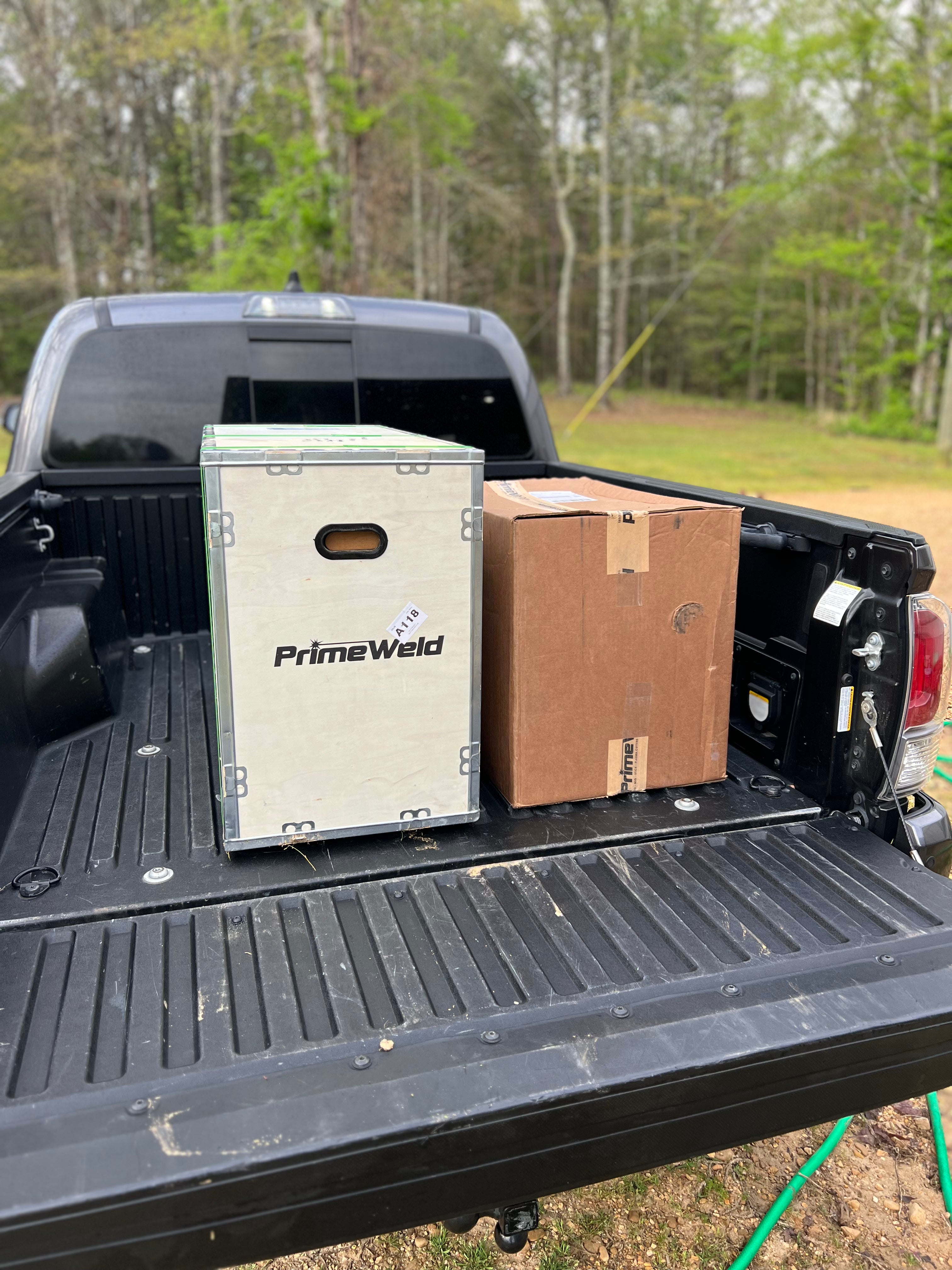
Unboxing the new Primeweld 325 this morning, about to see what this baby can do on Aluminum. Big Thanks to Primeweld for letting me test drive this machine for Welderskills.
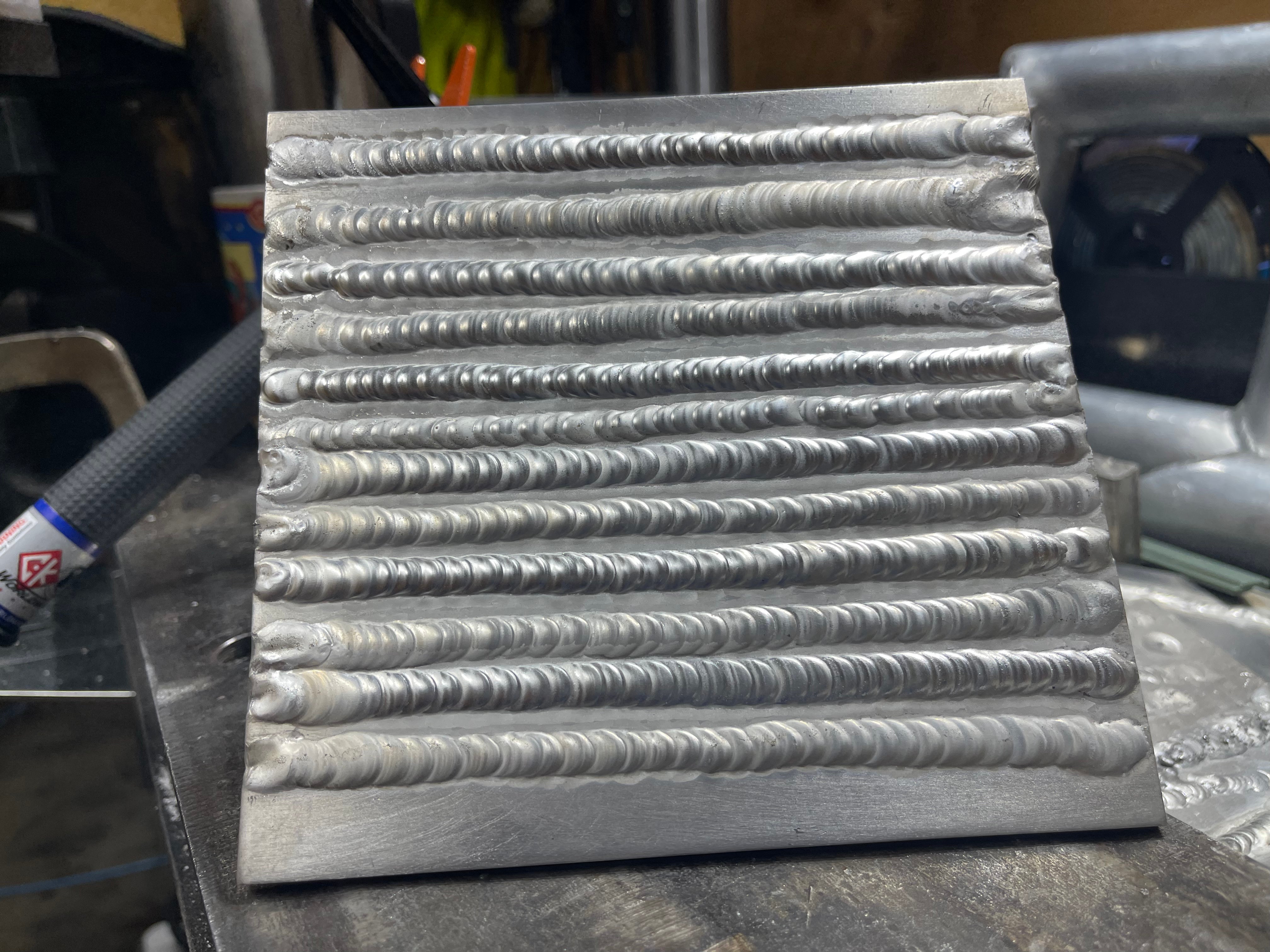
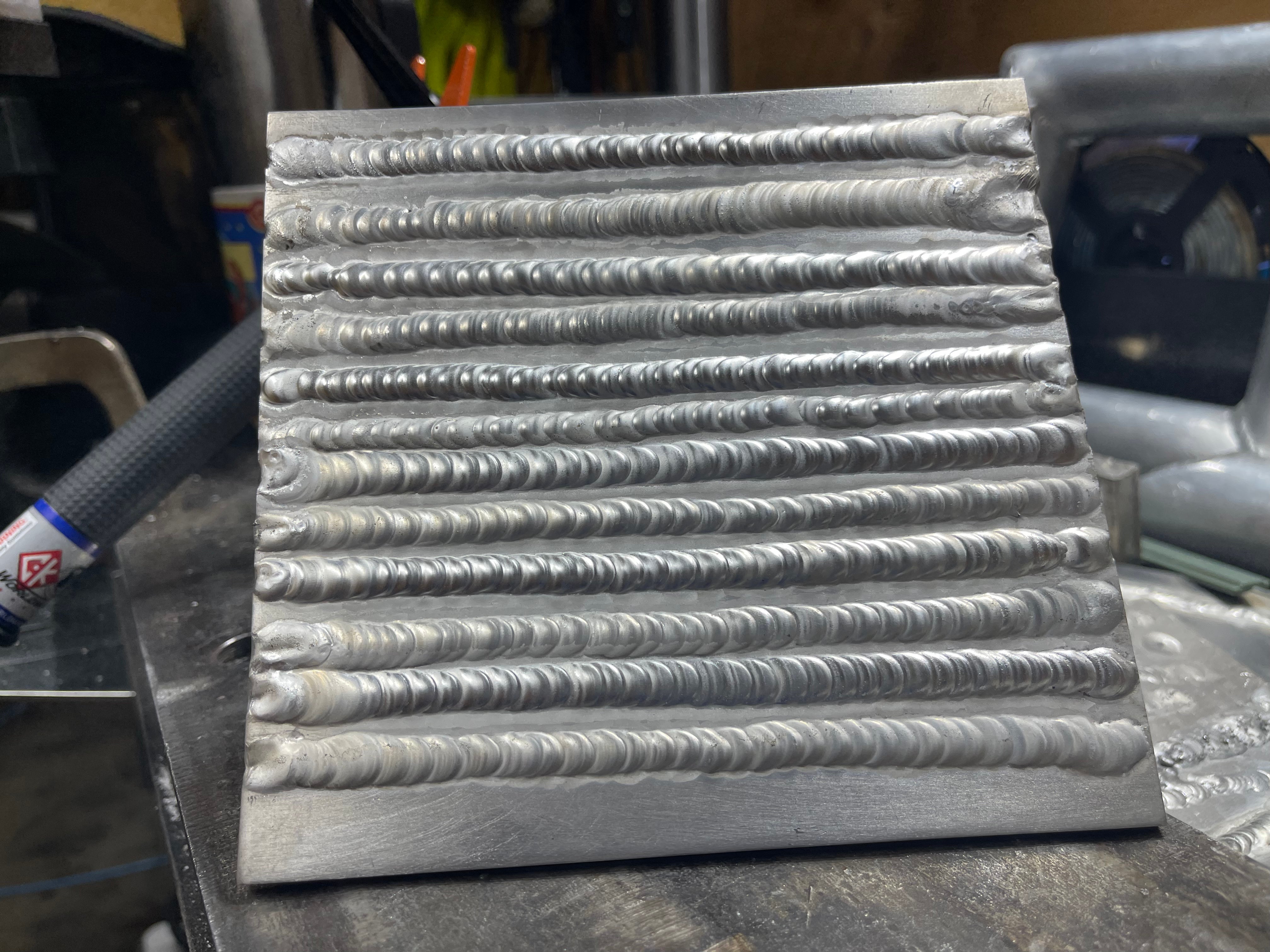
Any constructive criticism on these beads?
3/32 2% Lanthanated tungsten
3/32 5356 filler rod
17.5 SCFH pure argon
30/70 balance
120hz
1 sec preflow
10 sec post flow
CK #8 stubby clear cup
Thanks 🙏🏼
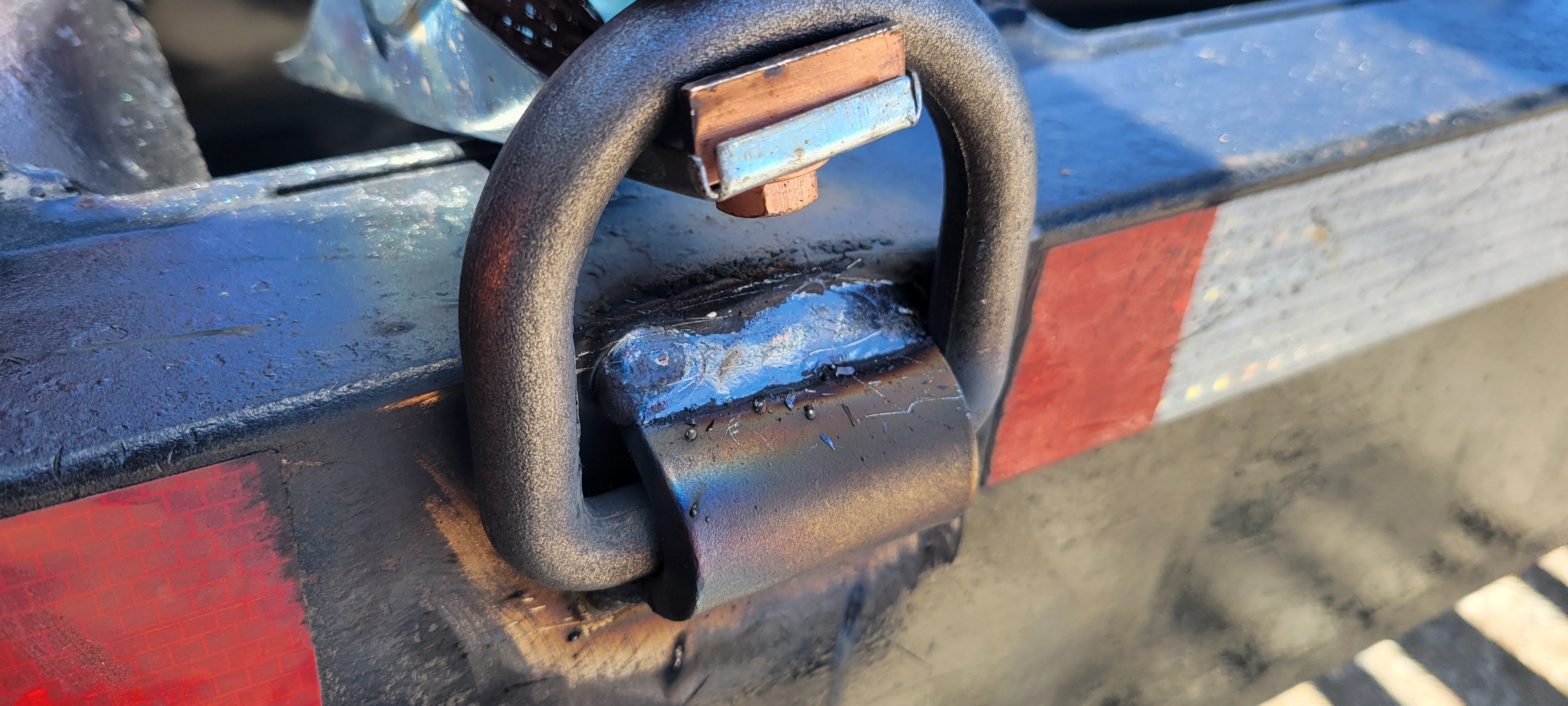
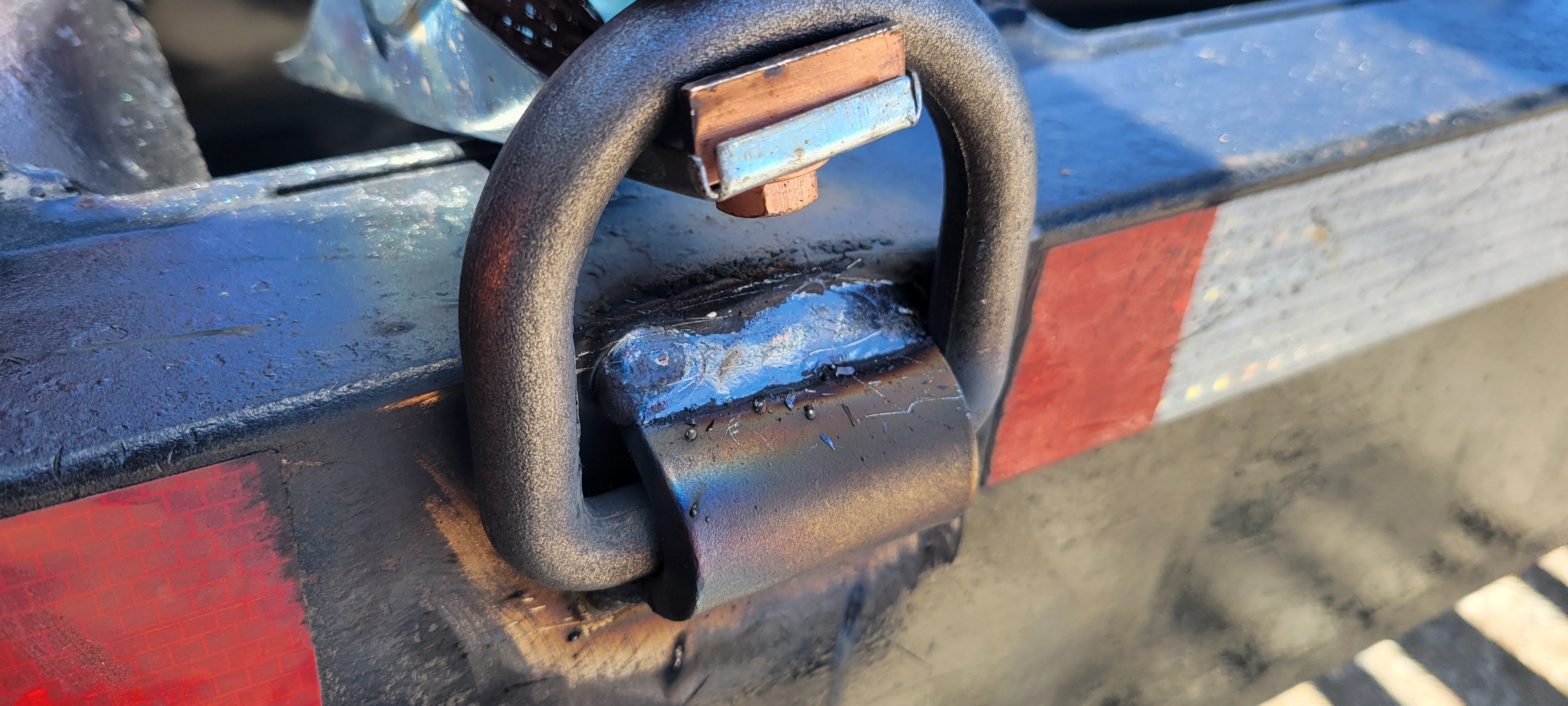
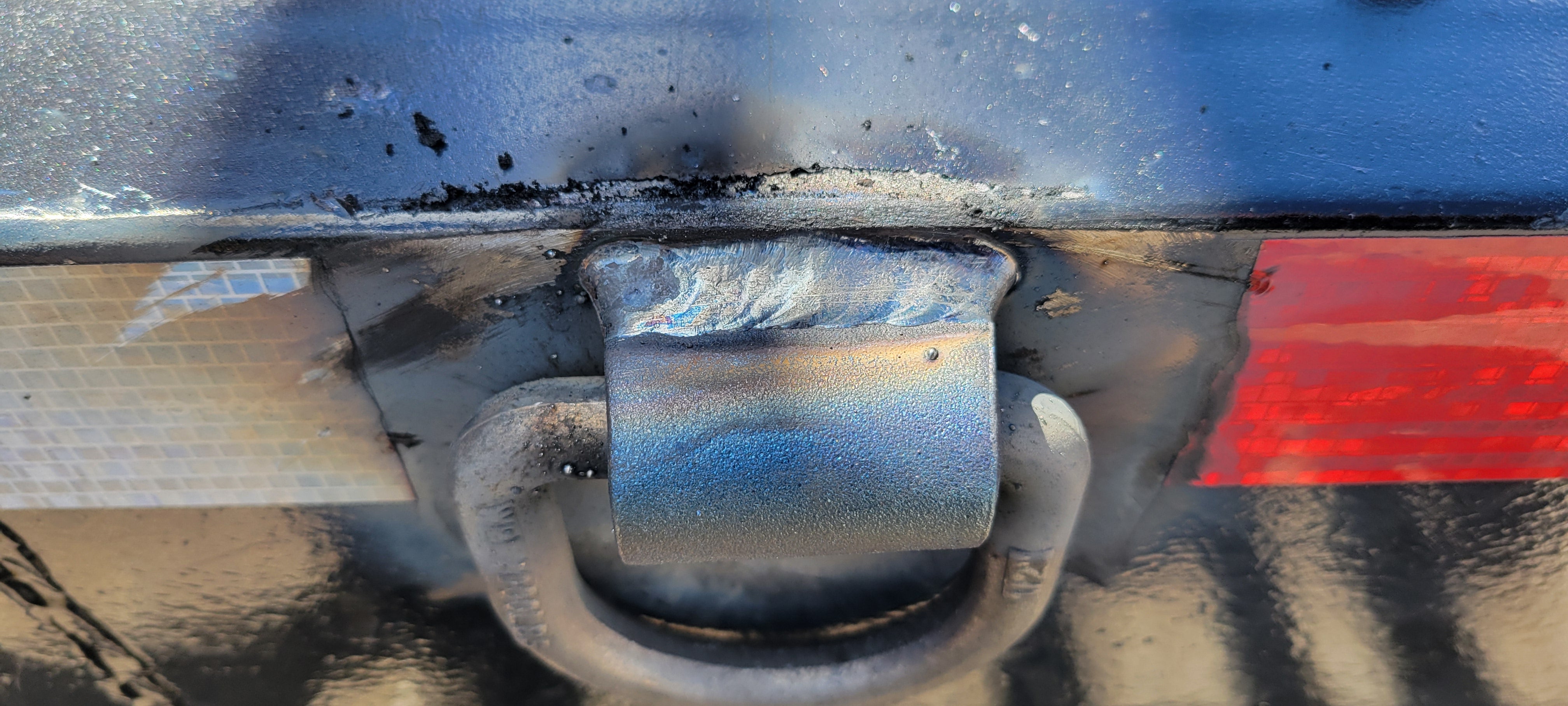
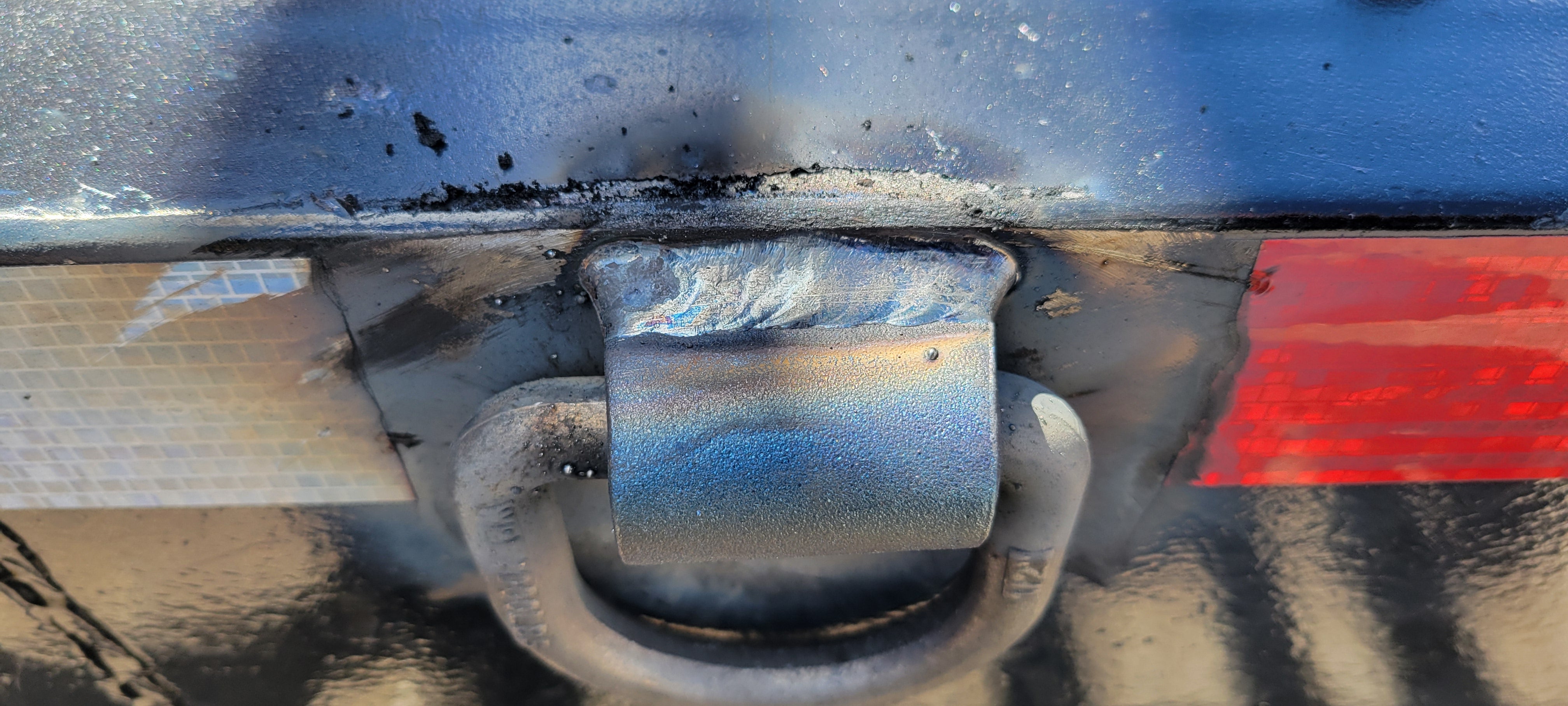
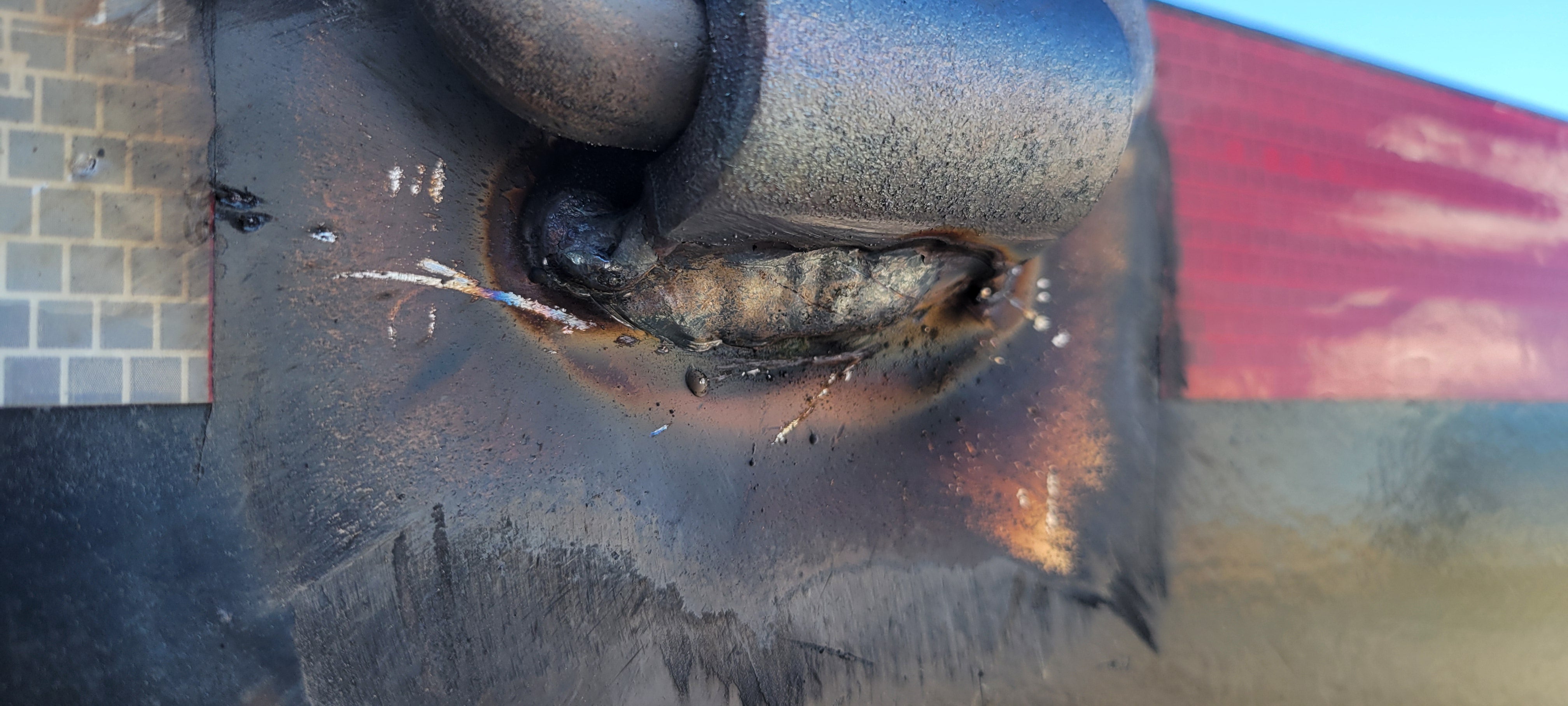
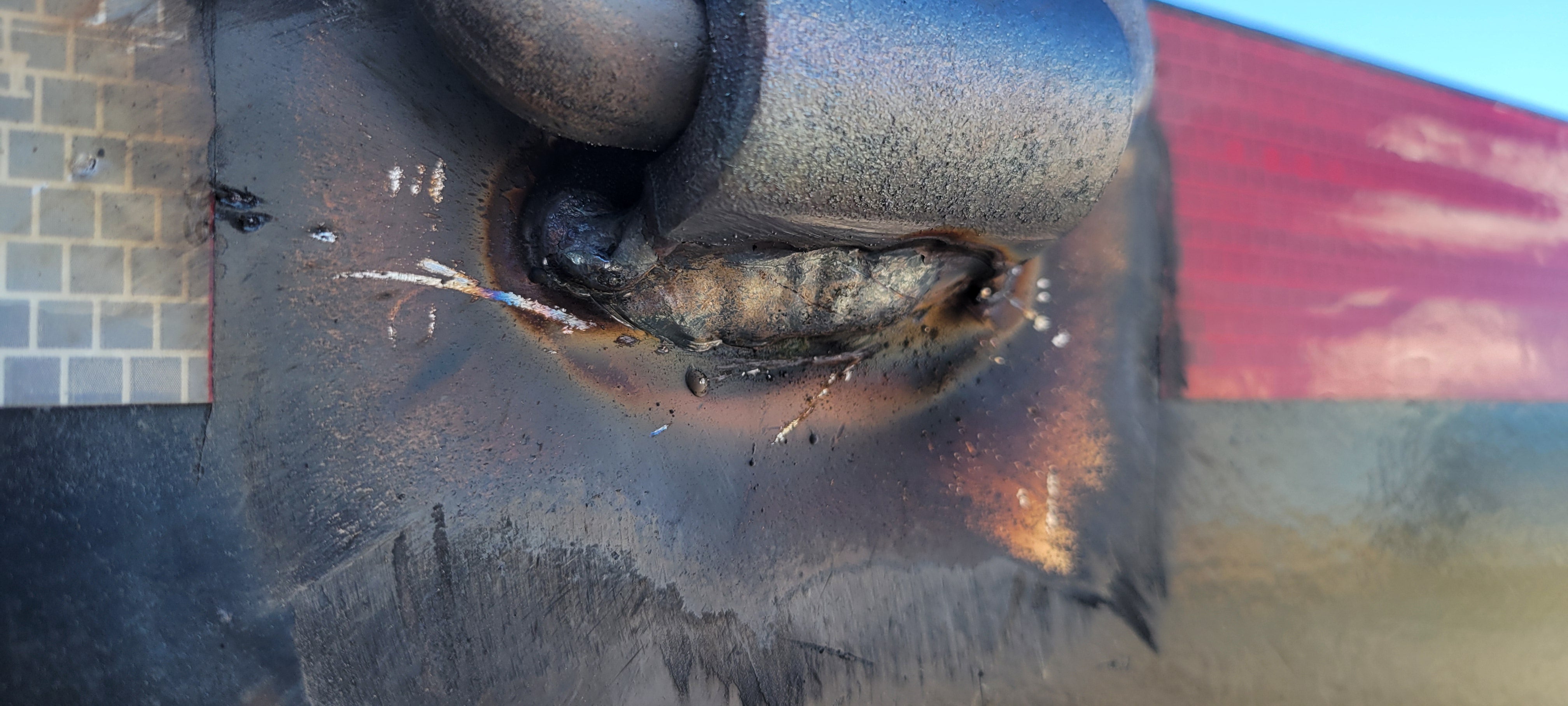
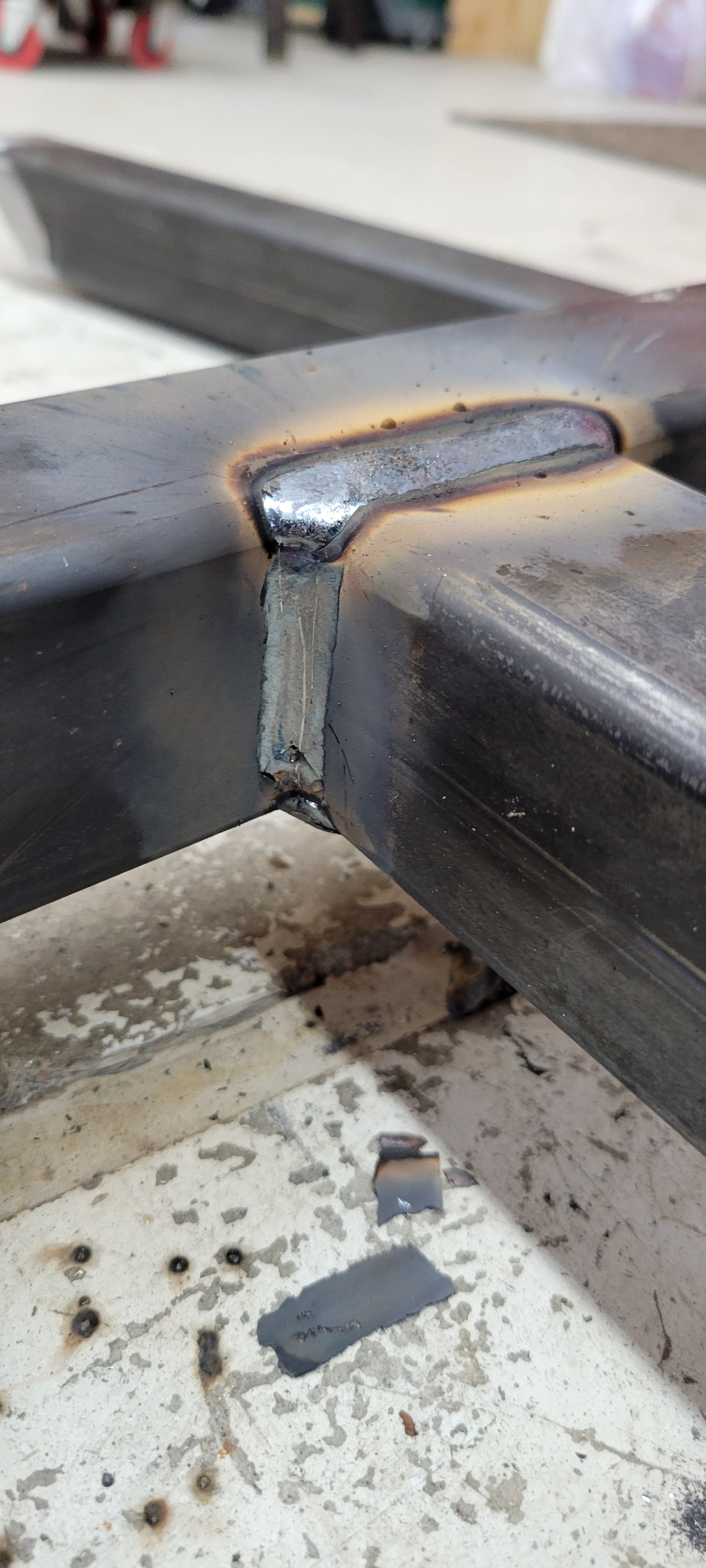
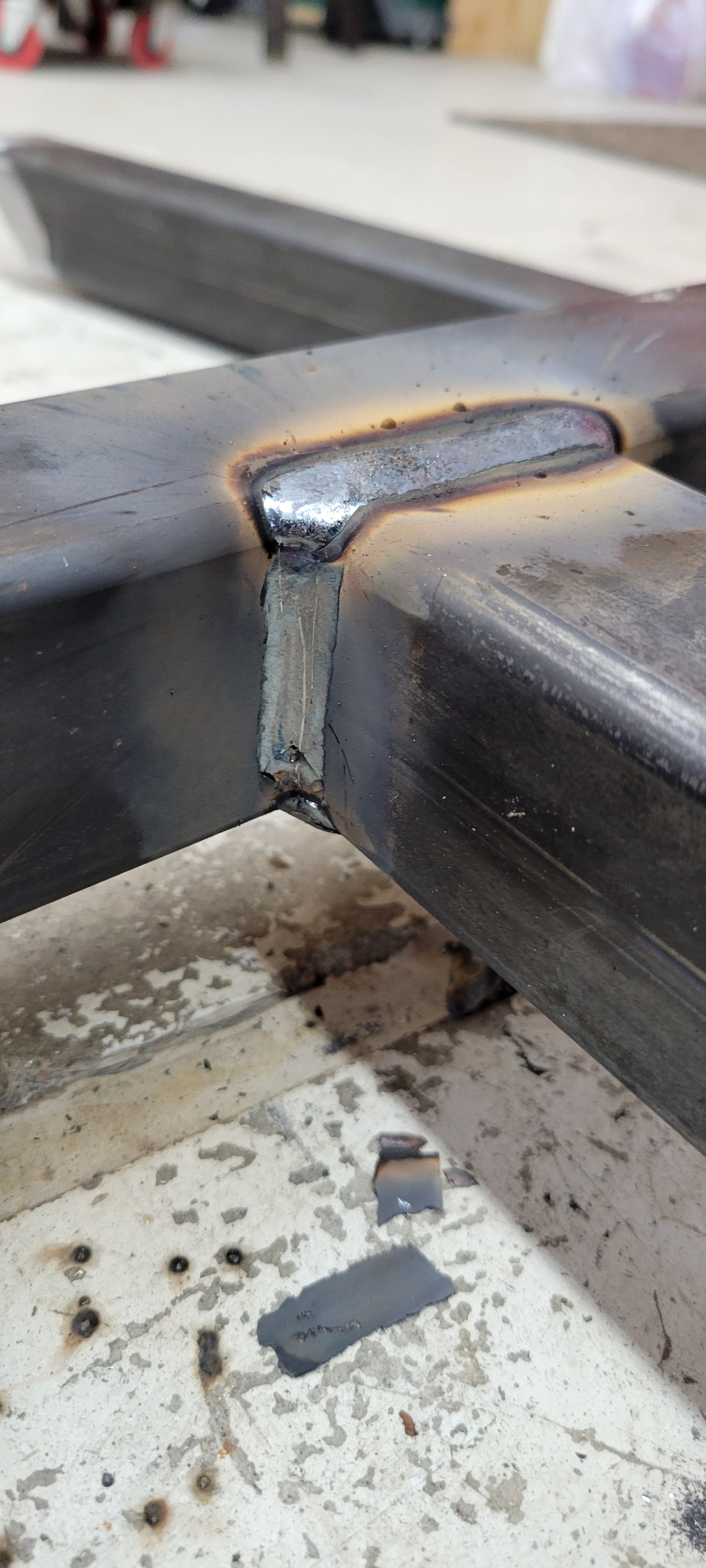
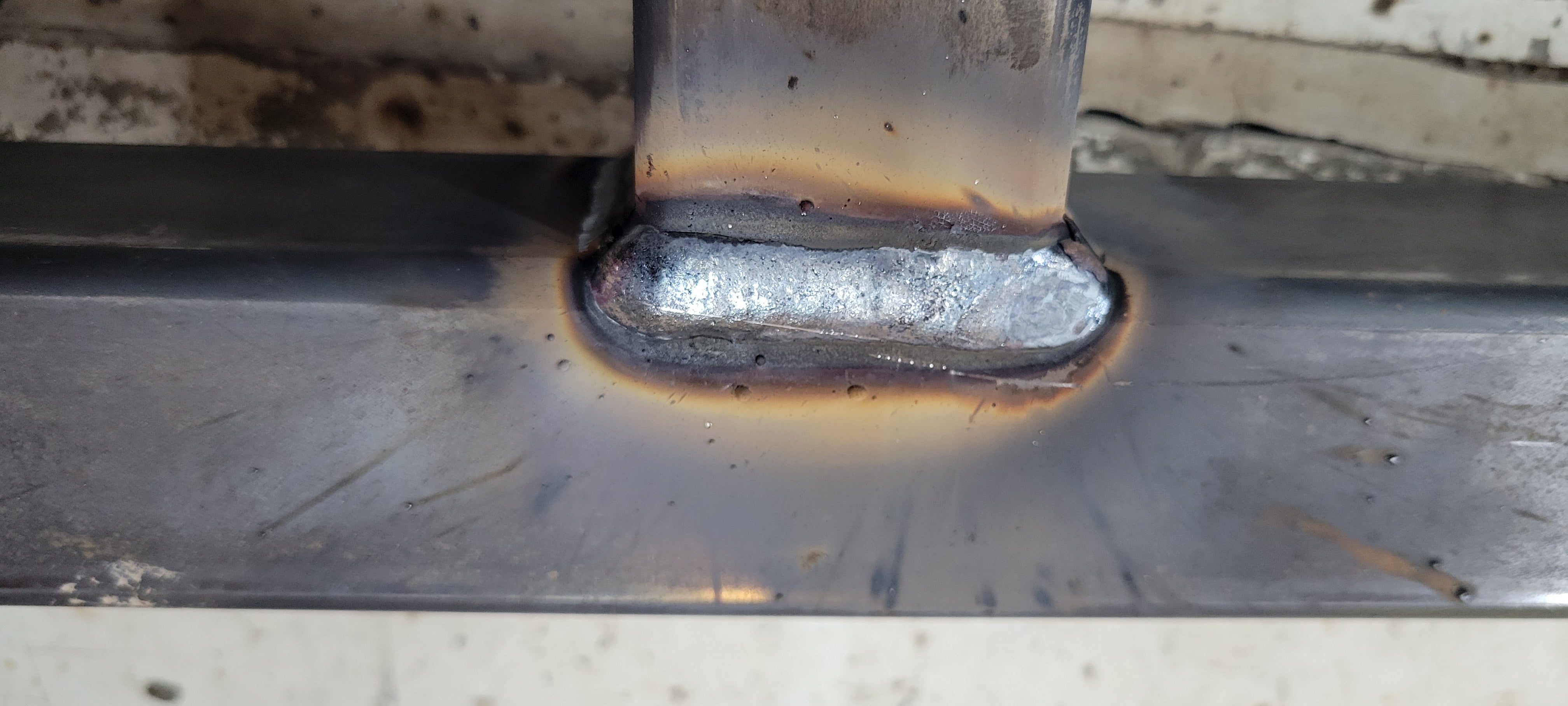
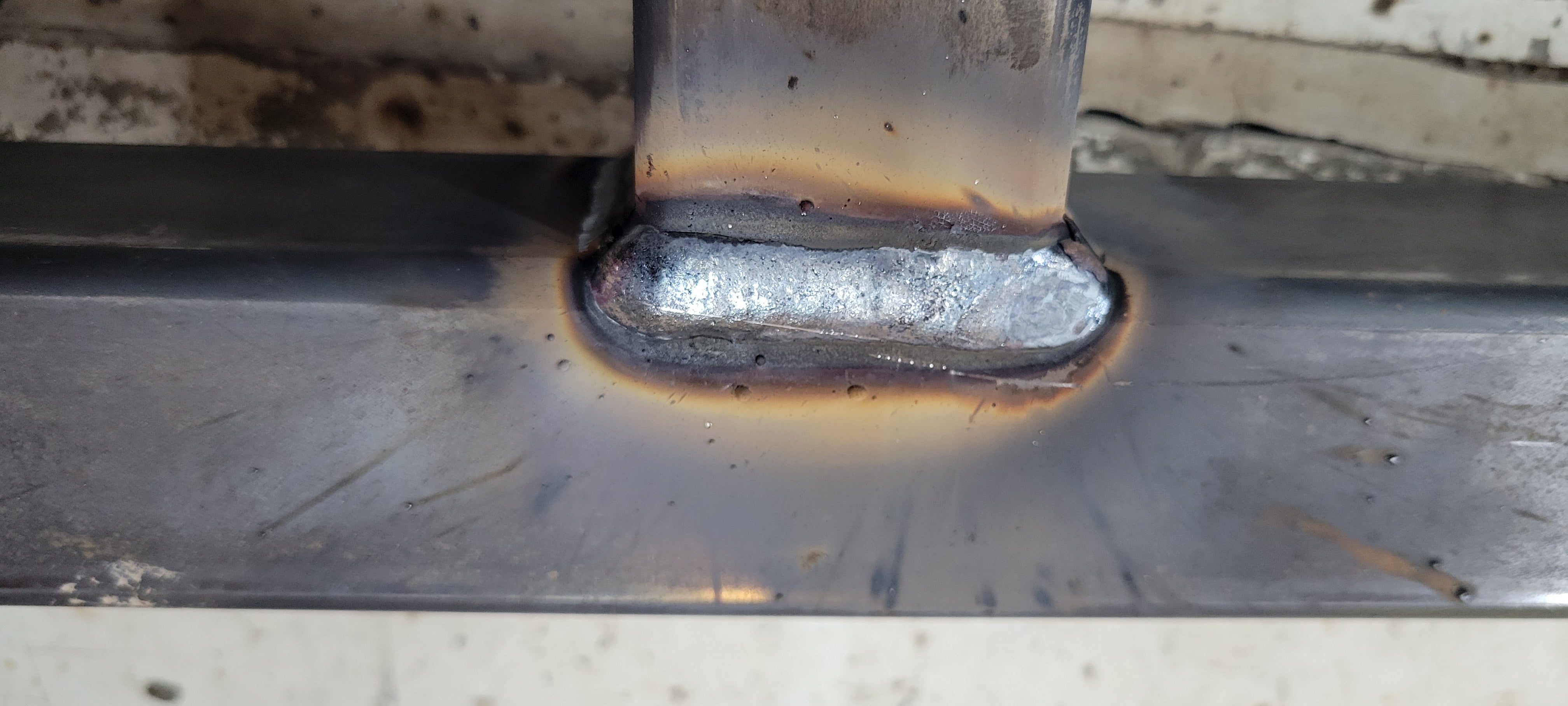
Matt Hayden
JD Brewer
Hey guys, I need some Dual Sheild help.
Dual Sheild Flux Core, Lincoln ultra core .045 71T
-22v @ 240in/min 75/25 @ 45cfh- 3/16 square tube
-25v @ 250 in/min 75/25 @ 45 cfh- 1/4- 5/16" D ring tabs
If I have a problem with the weld falling out, large balls of weld, would that generally indicate running too cold? Not enough arc force. I tend to weld alot of D Rings. The top weld goes in perfect, the bottom 4f t joint I always have problems.
I appreciate any advice
Has anyone used a brand of Dual Shield (FCAW) Electrode call "Diamond Spark" I heard a sales man came to the shop and had an employee test it. Salesman said that you did not have to chip off the slag because it would rise to the top after each pass over. No slag inclusion. It was cheaper than the Lincoln electrode and rated for structural AWS D 1.8 I did research and it is a German company.
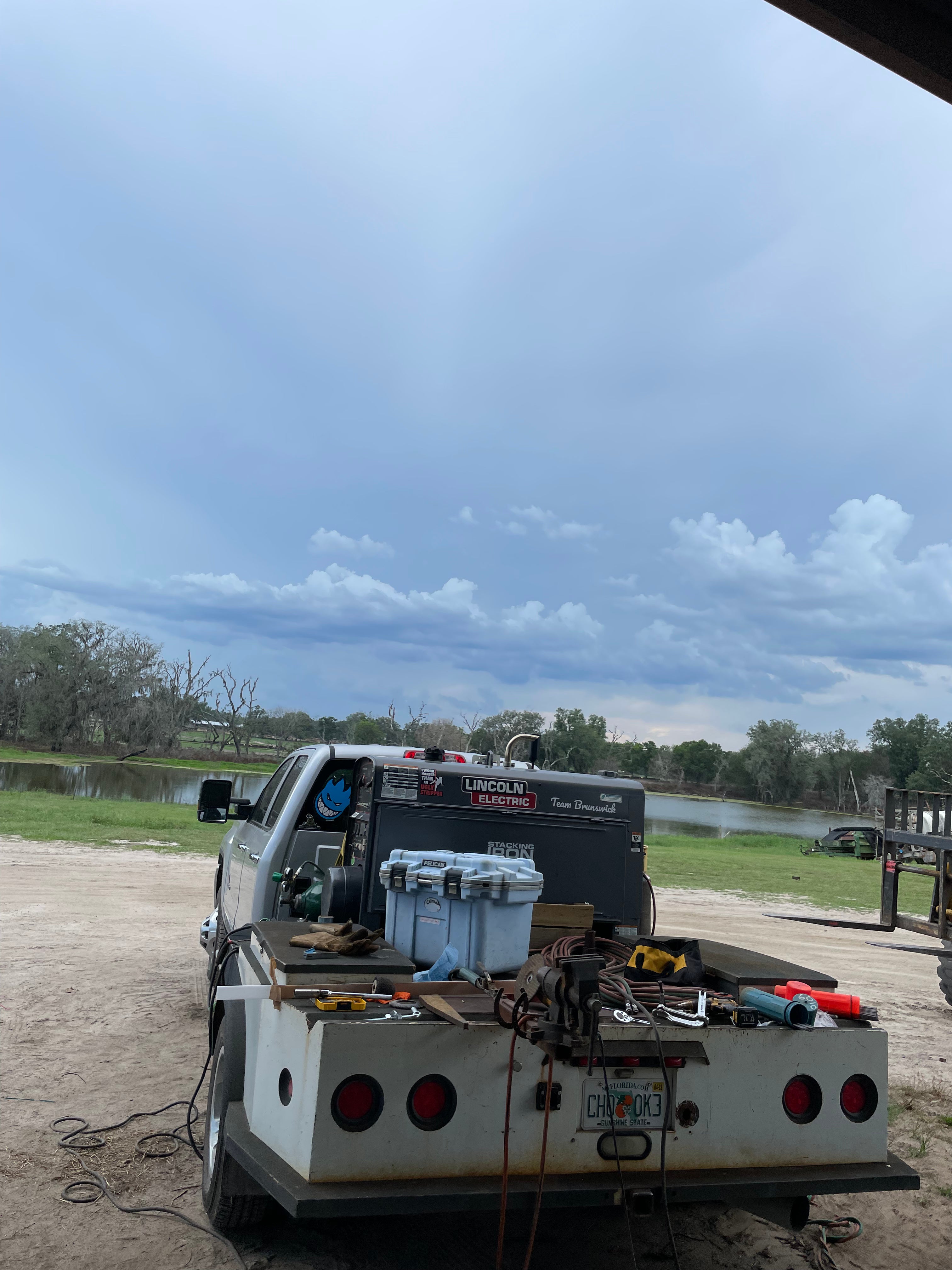
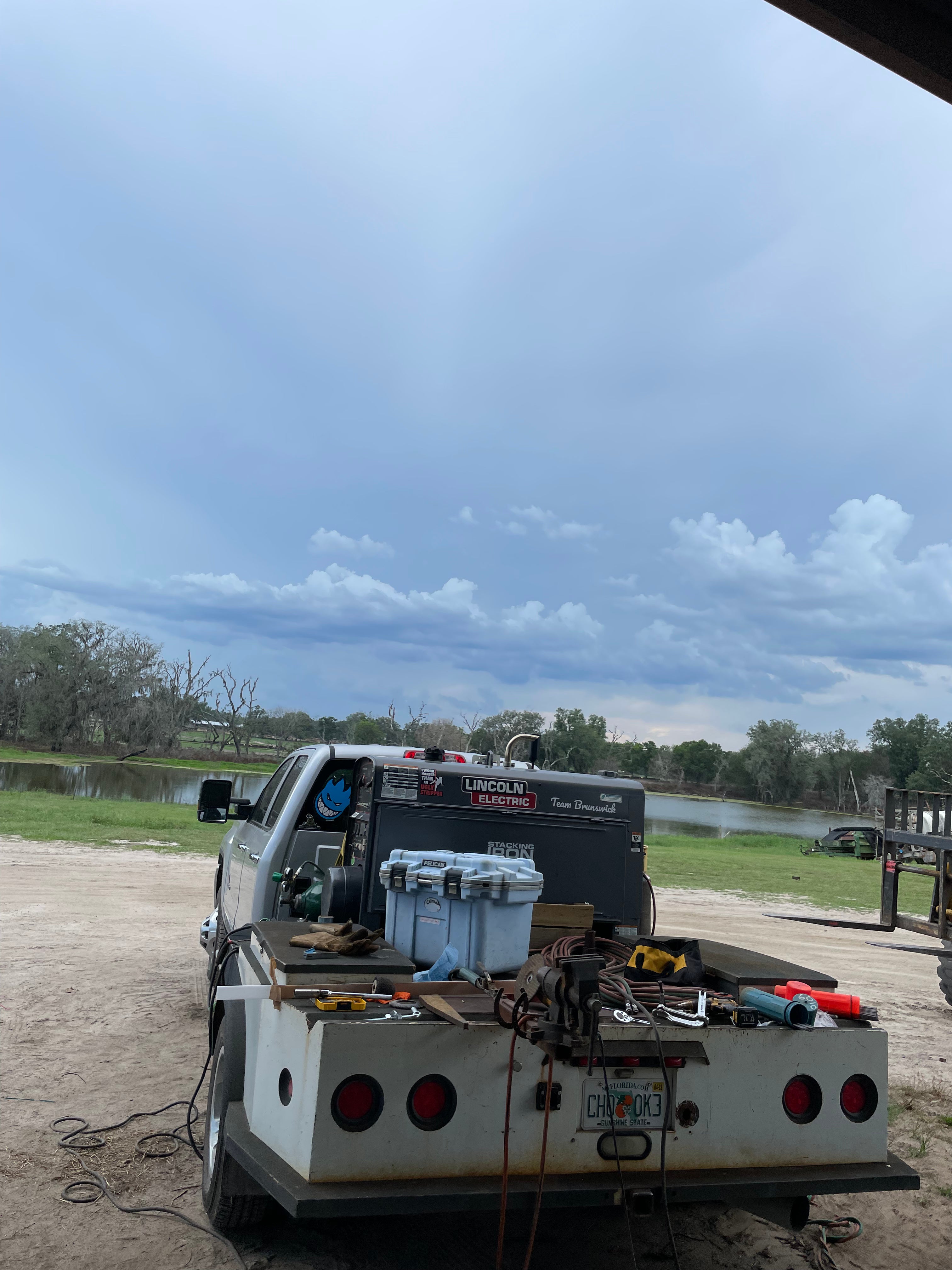
👋 Hello, I’ve been welding for about 11 years. From pipeline to shops I’ve bounced around a lot chasing that pot of gold. I want to start up with aluminum, and that’s the main reason why I’m here. Didn’t go to welding school, weldingtipsandtricks on YouTube years ago got me into my first spot.