More machining than welding, but got to at least weld a little today. Turned a slug, and milled a square hole in a round peg. then welded a piece of tubing that the end of a shaft will eventually fit inside and be welded. This will ultimately operate the oil valve that feeds the burner of a steam locomotive boiler. Got to try out the TIG function of the engine house's Miller Multimatic 220. It seemed to make a nice smooth DC TIG arc. I'd stick welded 7018 with it before, and it did that well(but I don't believe it will run 6010.) I was happy with it, considering it was the first TIG bead I'd ever ran with it.
!/8" wall tube to a square socket made of 1045. Pre-heated the 1045, and welded at 150A. ER70S-2. There's a 1/2" long stub that the tubing is pressed over to locate it, so it had a nice heat sink behind it.
Jeff Loffert
Posted
27 Apr 11:03
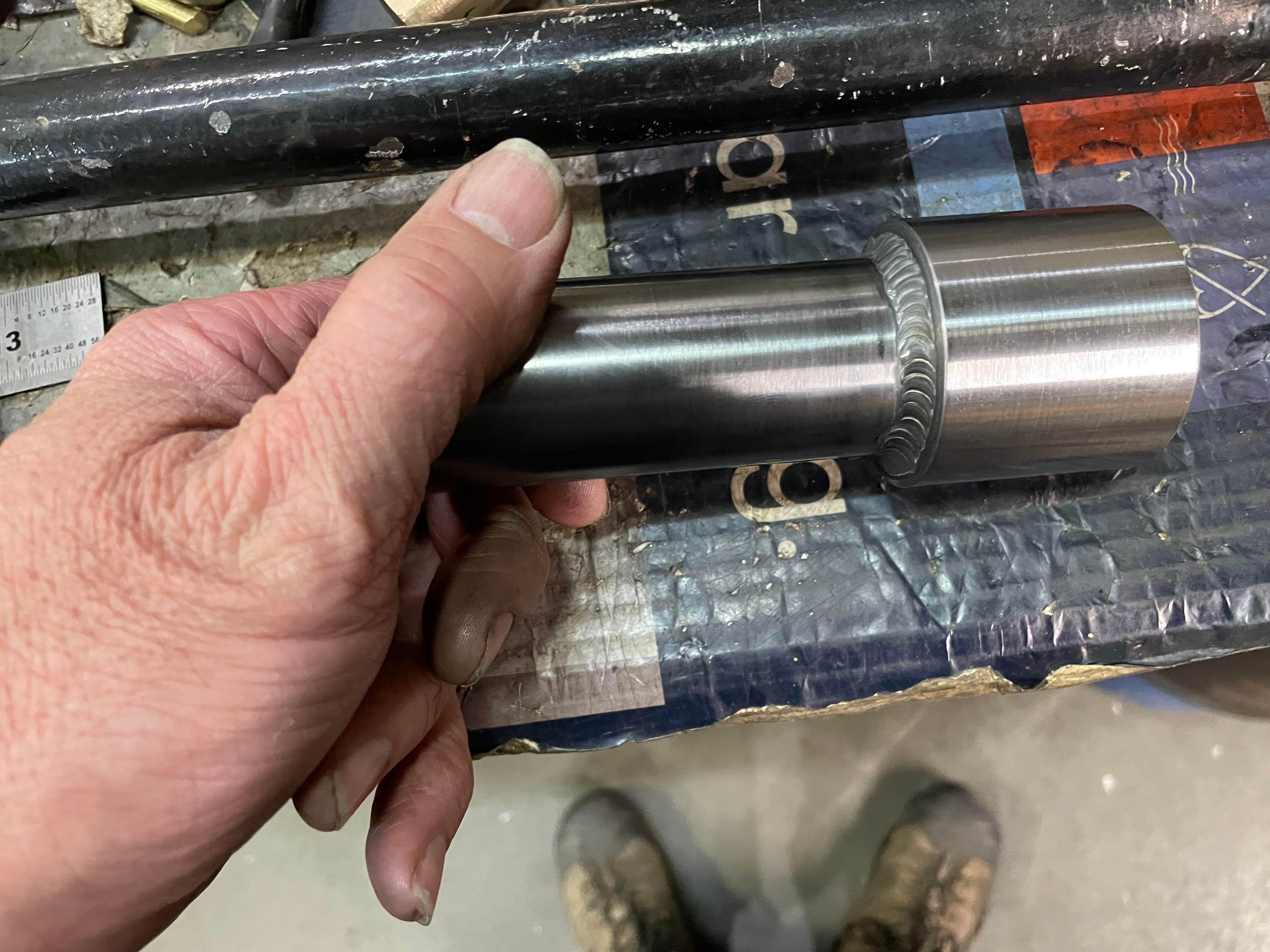
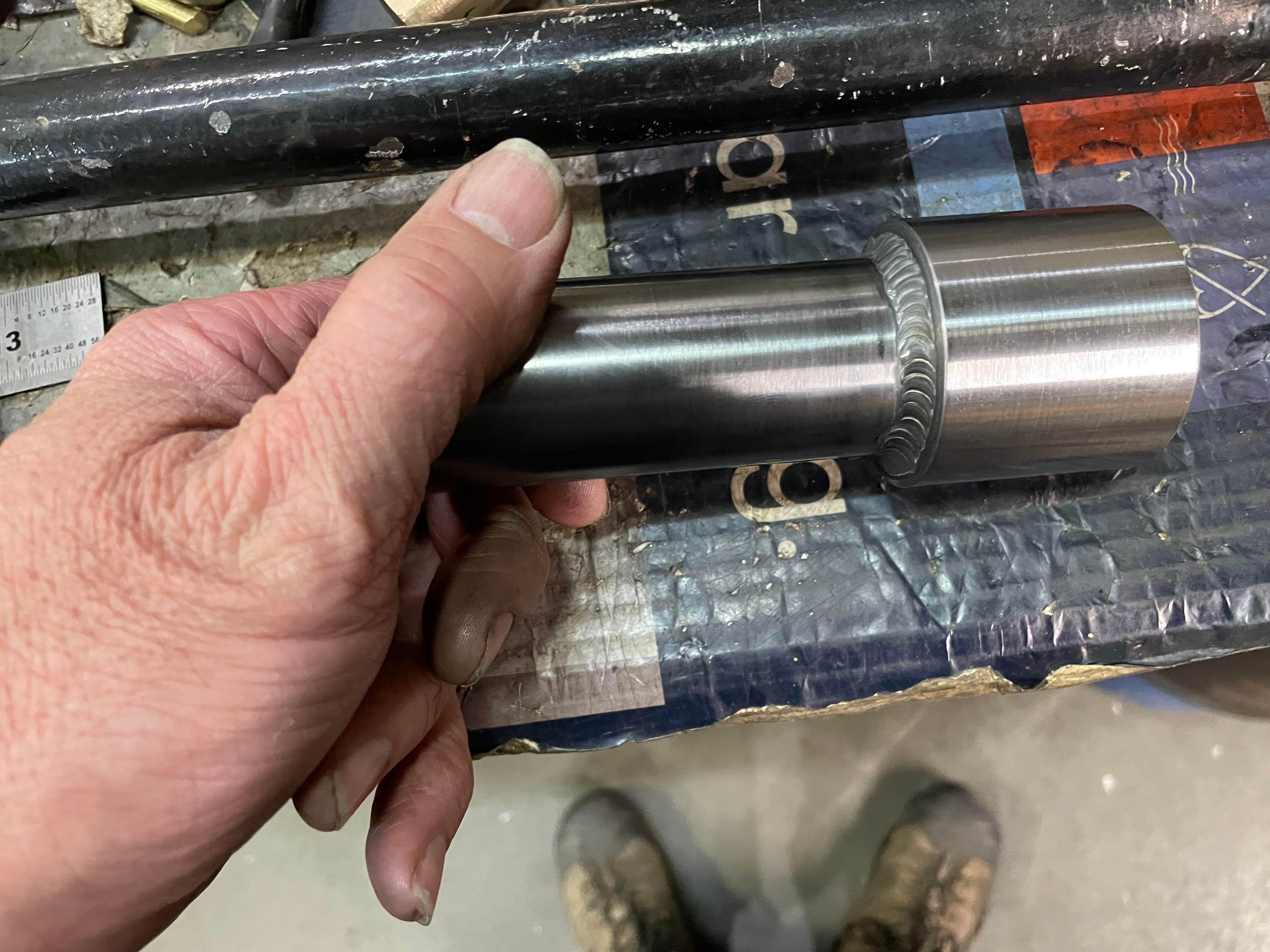
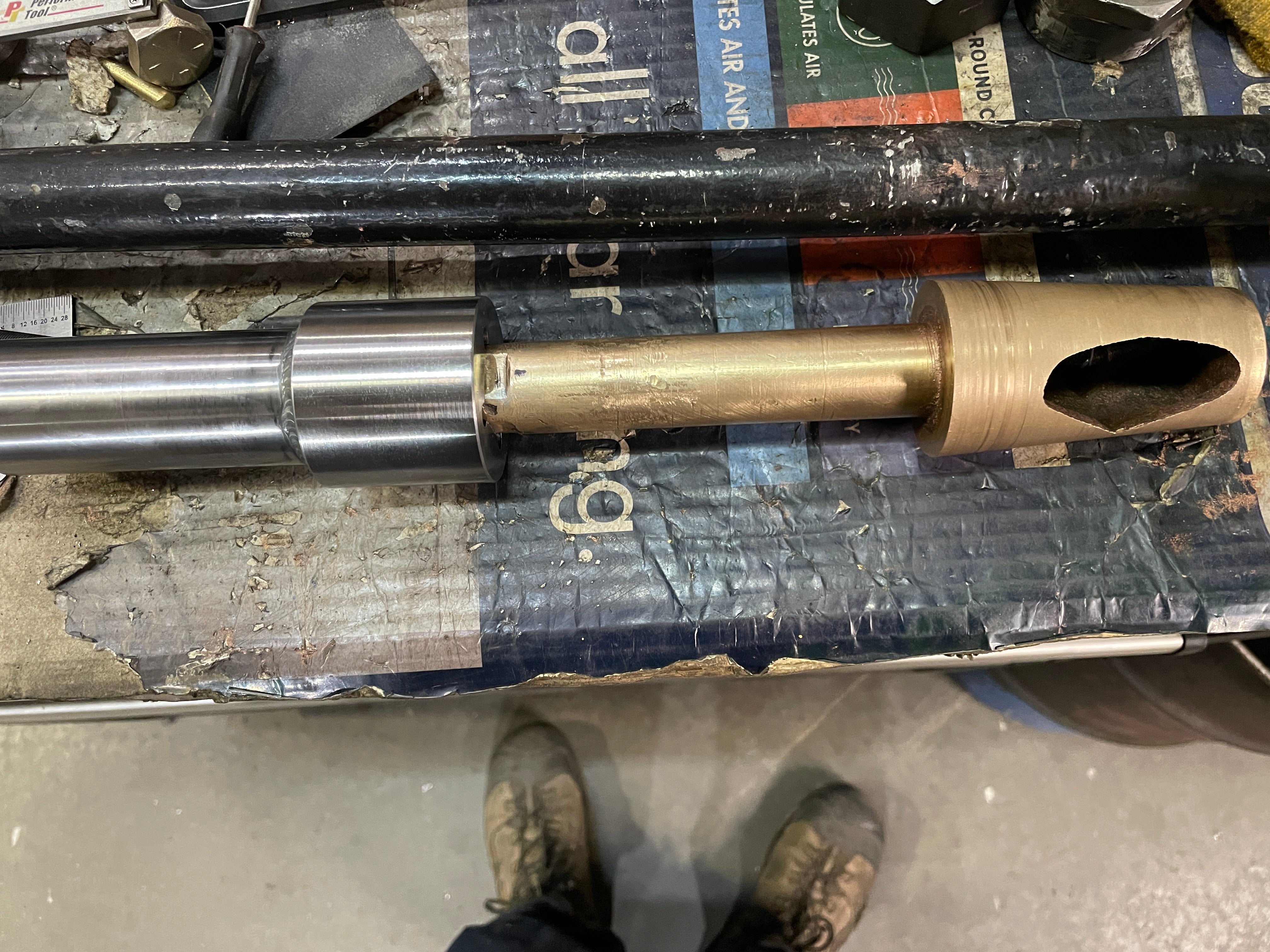
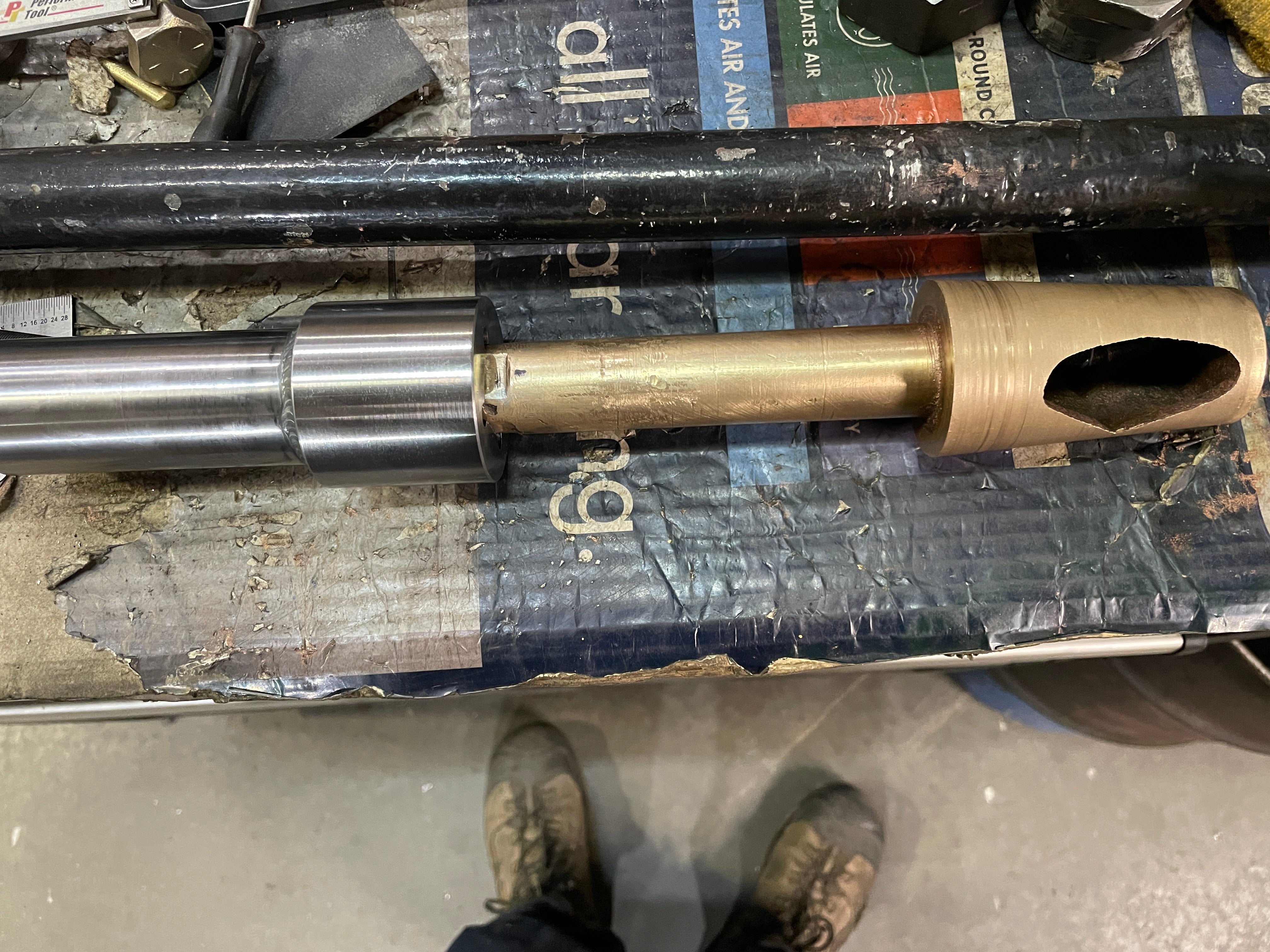
Posted
11 Apr 10:15
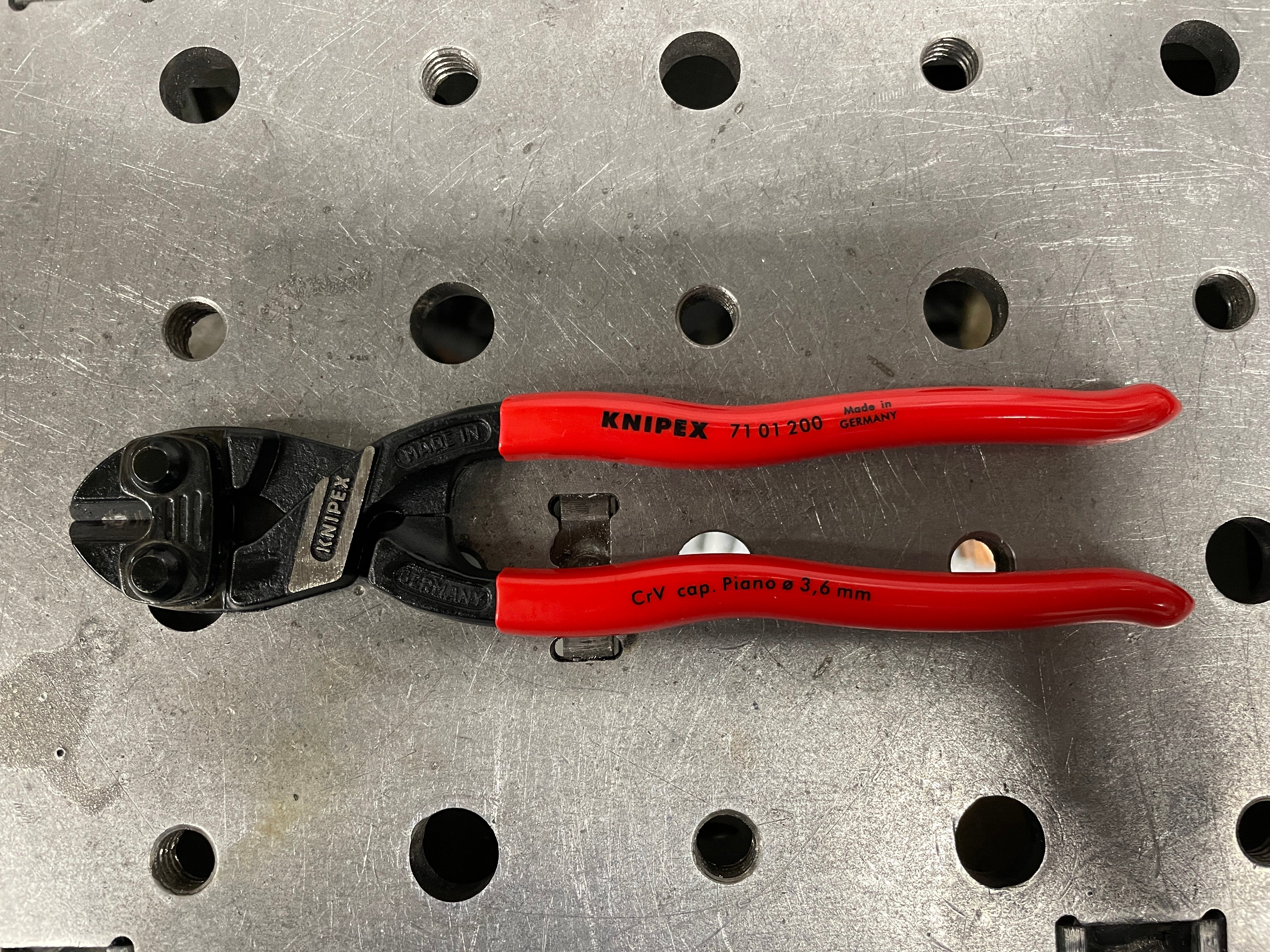
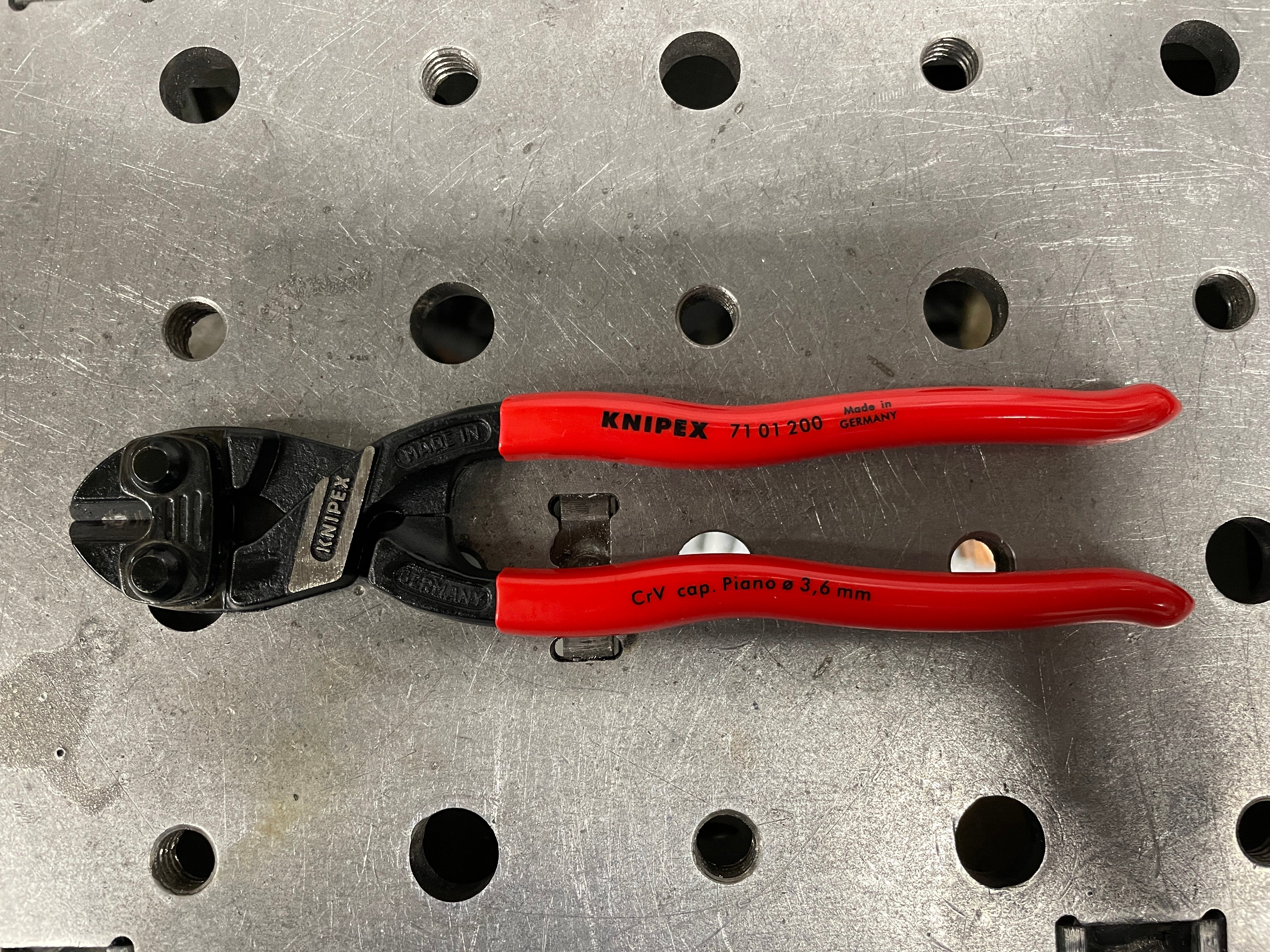
Recently became aware of these Knipex mini bolt cutters. Man, they make cutting 1/8" steel and stainless filler rod so much easier. No more Welpers for me. They'll be on the MIG cart where they are best suited. At fifty bucks, I think they're a bargain, considering they're a high quality German made tool, not some Chinesium POS.
Edited to correct the price. I paid around $50 not $30. They'll outlast me, so I think its still a good value.
Posted
30 Mar 13:49
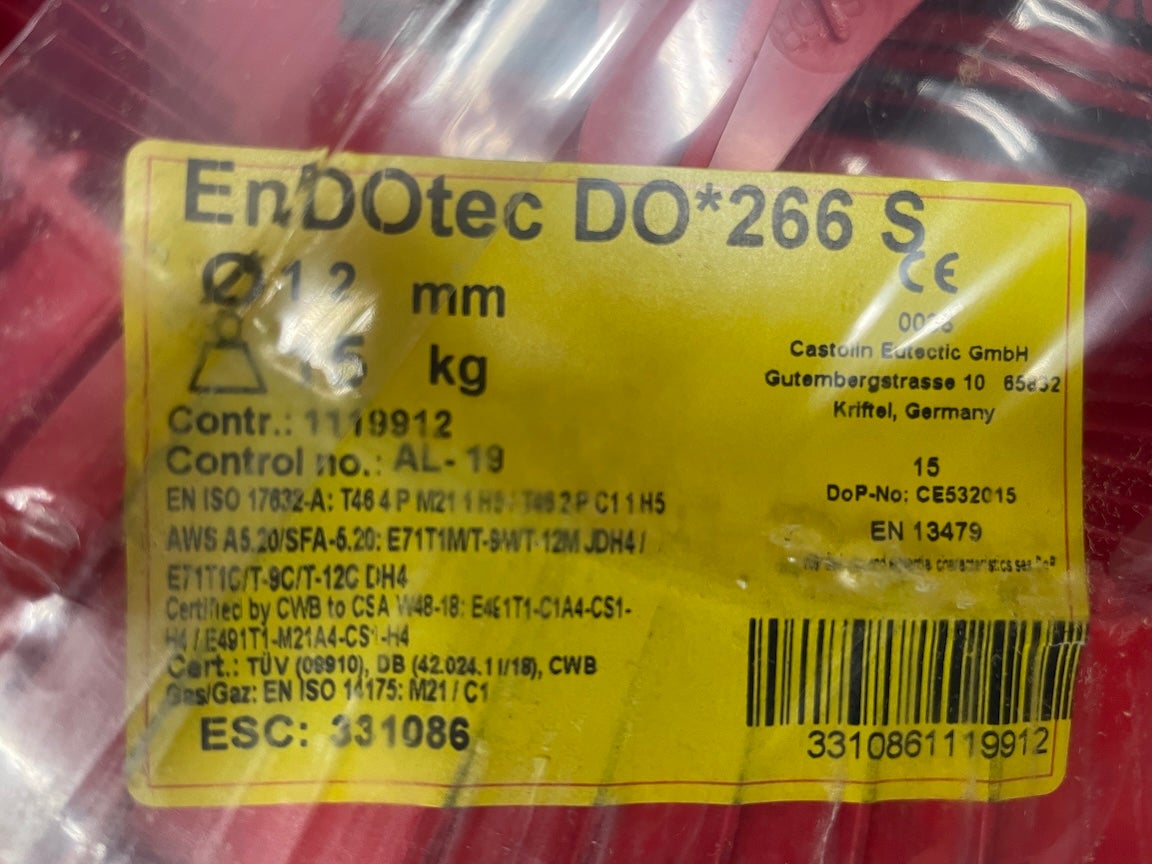
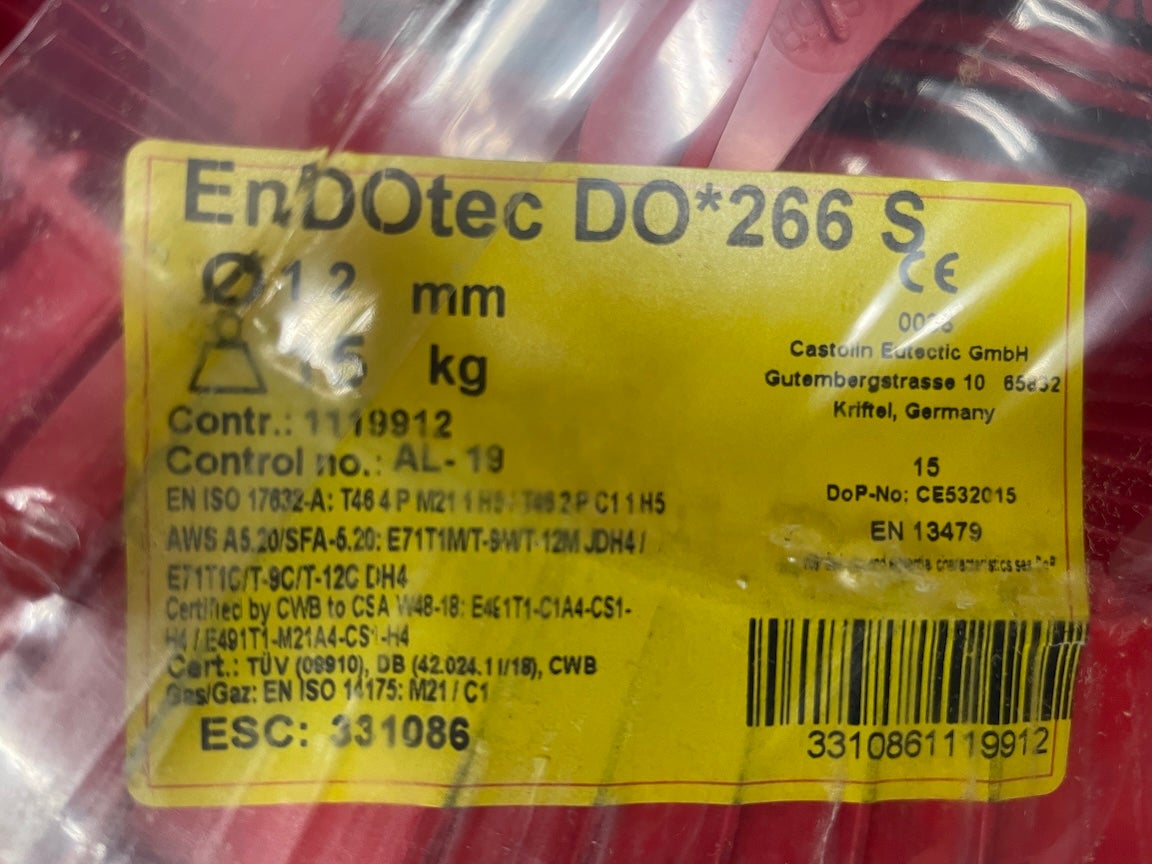
Tagging Matt Hayden as we'd communicated earlier on dual shield questions. Wasn't happy with the performance of the Lincoln 71M dual shield wire I tried. No matter what I did, there was random worm tracks, lousy root fusion in 1F, and man it was smoky. Decided to try another flavor and wow what a difference. This is Eutectic DO266S set at 25V/250 IPM 40 CFH 75/25 gas. The first thing I noticed was a fraction of the smoke, and no worm tracks. Wet in really nice. And even in 1F there's root fusion. Very promising. Still need to get used to it. Definitely need to slow down for more fill, and shift my aim up a little, as I'm favoring too low in the fillet. This may end up my go to dual shield. It's a little spendy at about $8.79/pound, but it works.
Posted
17 Feb 11:49
In the process of adding a motor drive to a rotary positioner kit, that was originally designed to be driven my a cordless drill motor. I bought the positioner kit knowing this, and never intended to use the drill motor, as that seemed pretty useless. Welded an adapter plate to one of the shoulder bolt axles, so it all moves as one unit, and happy with how it works. The combo of the 100 RPM 12VDC gearmotor, and the 40:1 gear reduction in the positioner, makes for a turntable that rotates at 0-2.5 RPM. Next is to make an enclosure for the motor, and a control box that will have the speed/direction control board and the battery( this will be powered with a Milwaukee M12 tool battery ). A foot switch will start/stop the table.
Before sinking too much effort, decided to run a test bead in DC and AC to make sure the HF start and/or AC freq didn't screw with the electronic speed control and motor. Didn't miss a beat, so will proceed with the remainder of the project. First beads ever using a positioner.
Edit. Thought I'd add a rundown of the major parts I used to motorize this Weltables rotary positioner. My subscription here expires in a few days, and not sure if I'll be renewing. Some work came in, so I won't have time to finish this project until next week.
PWM Speed Control-https://makermotor.com/pn00218-cyt13-25amp-7v-58v-high-voltage-dc-motor-driver-speed-controller-md25hv/
I got the flex coupler, 12V battery adapter, and foot pedal on Amazon, and should be simple enough to find in a search. I had to turn the hex end of the positioners shaft on a lathe. You could also simply adapt a socket to the motor shaft.
Edit to add: Another follow up, with a few photos of the final assembly of the motor housing and battery holder. Positioner works great and has plenty of torque. Set a 60 pound chunk of 1045 bar on the plate, and it rotates it smoothly at any speed. Very happy with it.
Posted
14 Feb 16:36
Posted
17 Jan 16:17
Edit. I thought that I'd posted this in the questions but ended up in General. So I thought I'd tag Matt Hayden in case he doesn't see it here.
Not real crazy about what I saw when cut and etched some sample 2F welds with the dual shield at 25V/250 IPM 35 CFH C25. They look OK on the surface, but about zero root fusion, and pretty shallow penetration. The etch wasn't great and didn't photo well. The 1/4" material was spotless clean and square; no rounded over sheared rolled edges. It was belt sanded square. Maybe I was traveling a little too fast? The throat is definitely under 1/4". Thoughts anyone?
Photo 1 cross section is pull beads top left/bottom right, and pull top right/bottom left. Photo 2 is pull, and Photo 3 is push.
Edit to add: Not sure what the hell is going on. Ran two more beads. Photo 4 is 25/250 and photo 5 is the Auto Set suggested 22.9/265. Slower travel speed to build up a bigger bead, which it did, but as you can see in the last photo, the root fusion in both is terrible. Squashed it in the 40T press and it held up OK, but I would hope so, welded on both sides.
Posted
15 Jan 22:21
Question for you guys that run a lot of dual shield. Do you think that "slag you drag" is a hard rule? I was padding beads of .045" Lincoln 71M Outershield( C25 gas ) at on plate today set to 25V/250 IPM. Dragged the beads left to right, and pushed the beads right to left. Darned if I could tell the difference. Just used a very slight ( 5-10 deg ) tilt either to or away from the direction of travel, with the gun pointed straight in. I haven't tried a cut & etch yet to see if there's any difference inside, but on the surface it runs great either way. Love the spatter free welds. I must admit I was wearing Crocs and never so much as felt a spark in an hours welding! I know, I know, it's not proper footwear. My shop, my feet, my rules! :)
Posted
06 Jan 19:15
My neighbor brought me a couple of receiver hitches that came off the fleet of snow machines that are used to groom the Iditarod trail before the sled dog race is run each spring. These machines take a pretty good beating, and the hitches have a couple of common failure points. He wanted me to see if I could add a few additional beads to beef them up. After burning off the powder coating and bead blasting, they were good and clean. Added a fillet around the three un-welded faces of the tubing, starting and ending on the ends of the lone factory weld. Then butt welded the inside end of the tube to the flange. He was very happy, and will be bringing in six brand new ones to receive the same mod, before they install them on the fleet. I chose ER312 filler, as I wasn't sure if it would be 100% clean, and it's supposed to leave a ductile, crack resistant weld. Plus, I just like the way it welds! Turns out the weed burner/bead blast got it plenty clean, so I'm sure plain old ER70S-2 or -6 should be fine for next ones.
Posted
01 Jan 20:33
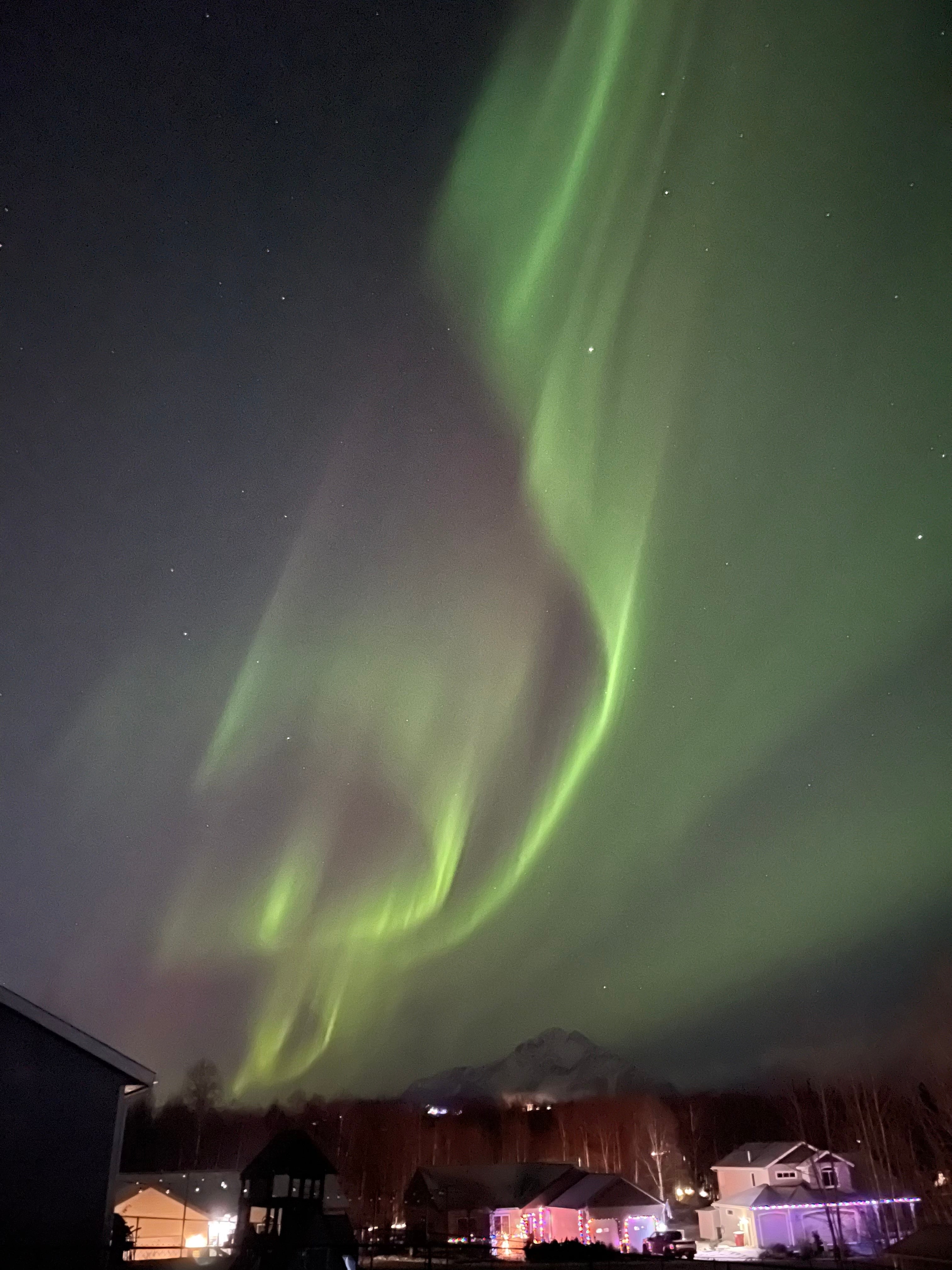
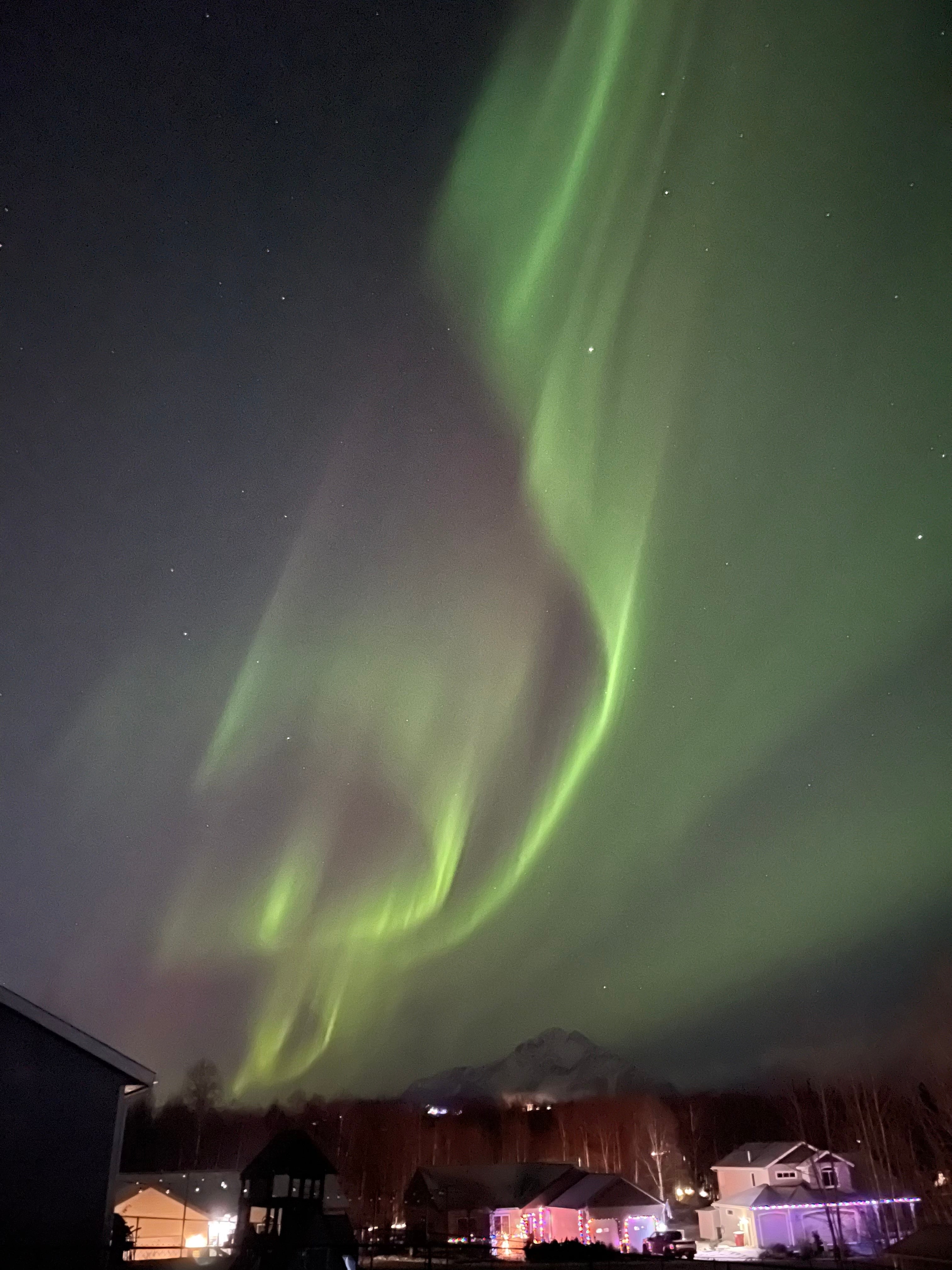
Happy New Year! Hope you all have a great 2025. Last night Mother Nature put on a great light show for us here in Alaska. Better than fireworks!
Posted
05 Dec 22:17
Edit, I guess it's not new, as I just saw a YouTube video about it from 15 years ago. Never heard of it, and got an email from Arc-Zone about it today, so I assumed it something new.
Have any of you guys tried the latest miracle tungsten from Arc-Zone? https://arc-zone.com/arctime-hybrid-tungsten-a-ewg-3?utm_source=Klaviyo&utm_medium=campaign&_kx=QWXqW_gFuz1wtJ2U8Snwf4q8I7UjWsXFTMFJNpul7SI.QZDYtd
At $75 for a 10-pack, it better be damn good!