Need some help here. I got a .45lb spool of Stoody 101HG and I’ve been having trouble with the welds being really rough and also just not setting out well. Now I will say I noticed that the paperwork calls for 98/2 and all I have is either 100% Argon or 75/25. Unfortunately i had someone pick this up for me so they didn’t know. With preheat I can make them okayish. Is the gas the main culprit or am I just bad at it?
Ben Coody
Posted
02 Sep 19:34
Posted
20 Jul 17:23
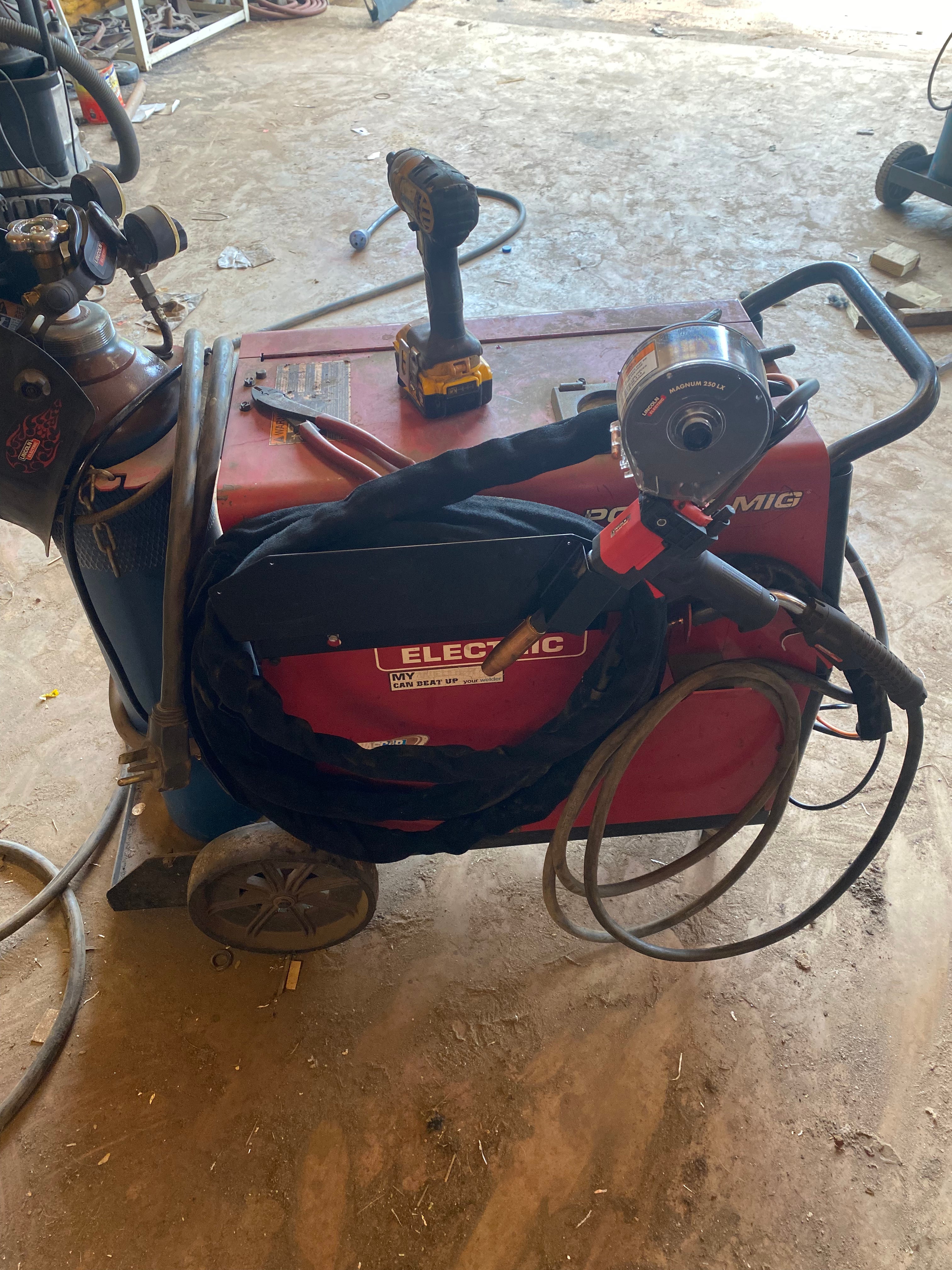
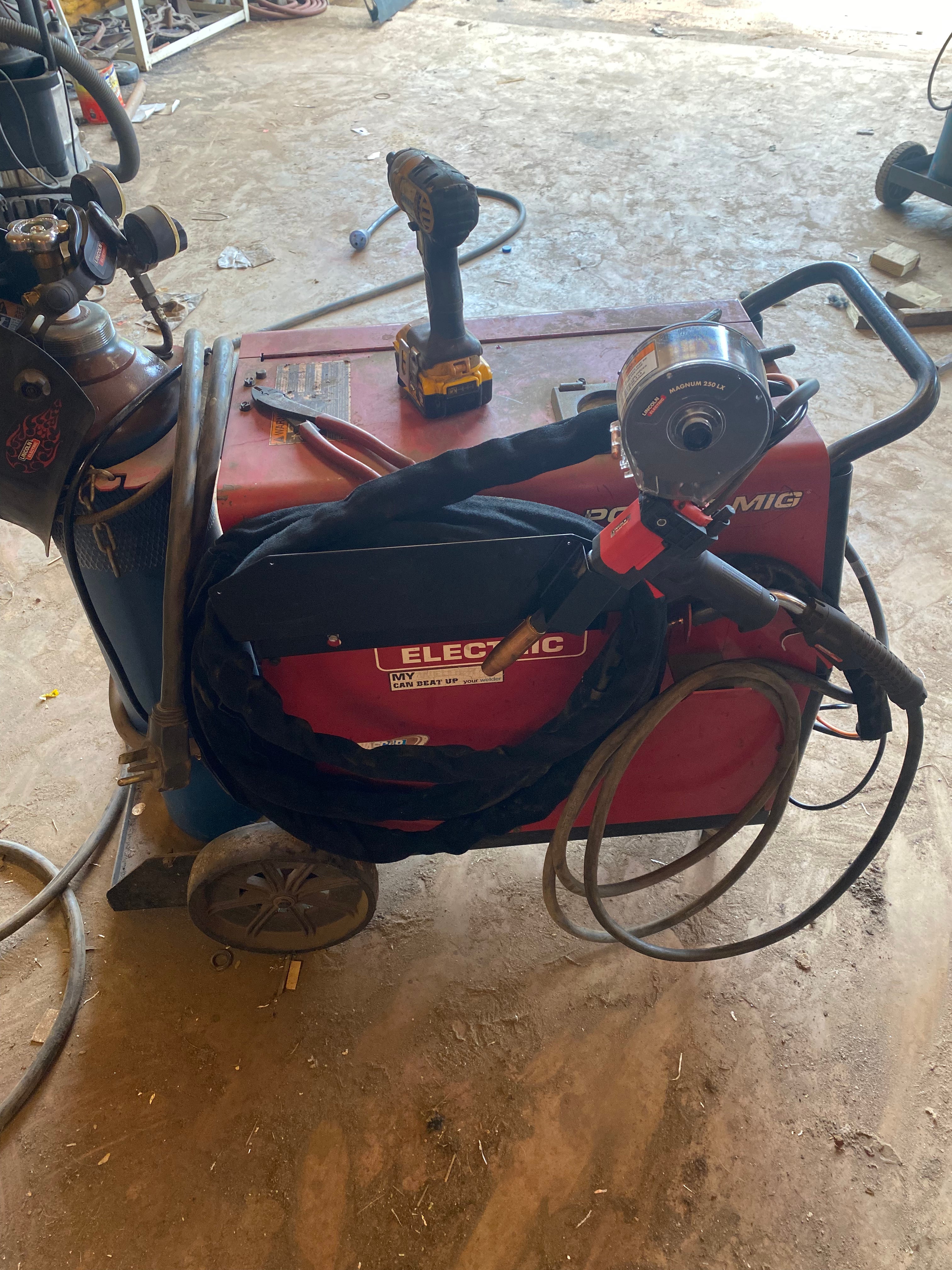
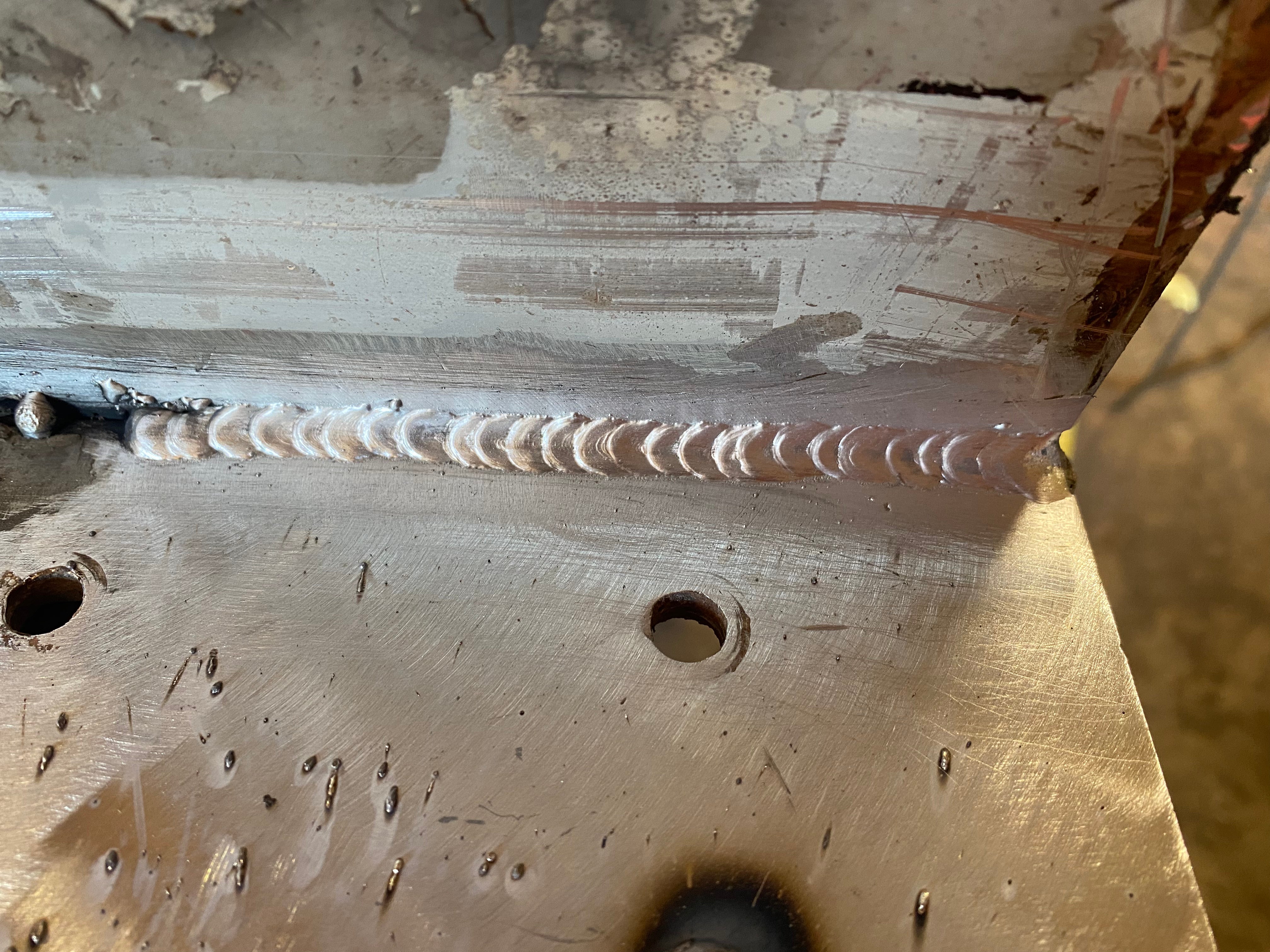
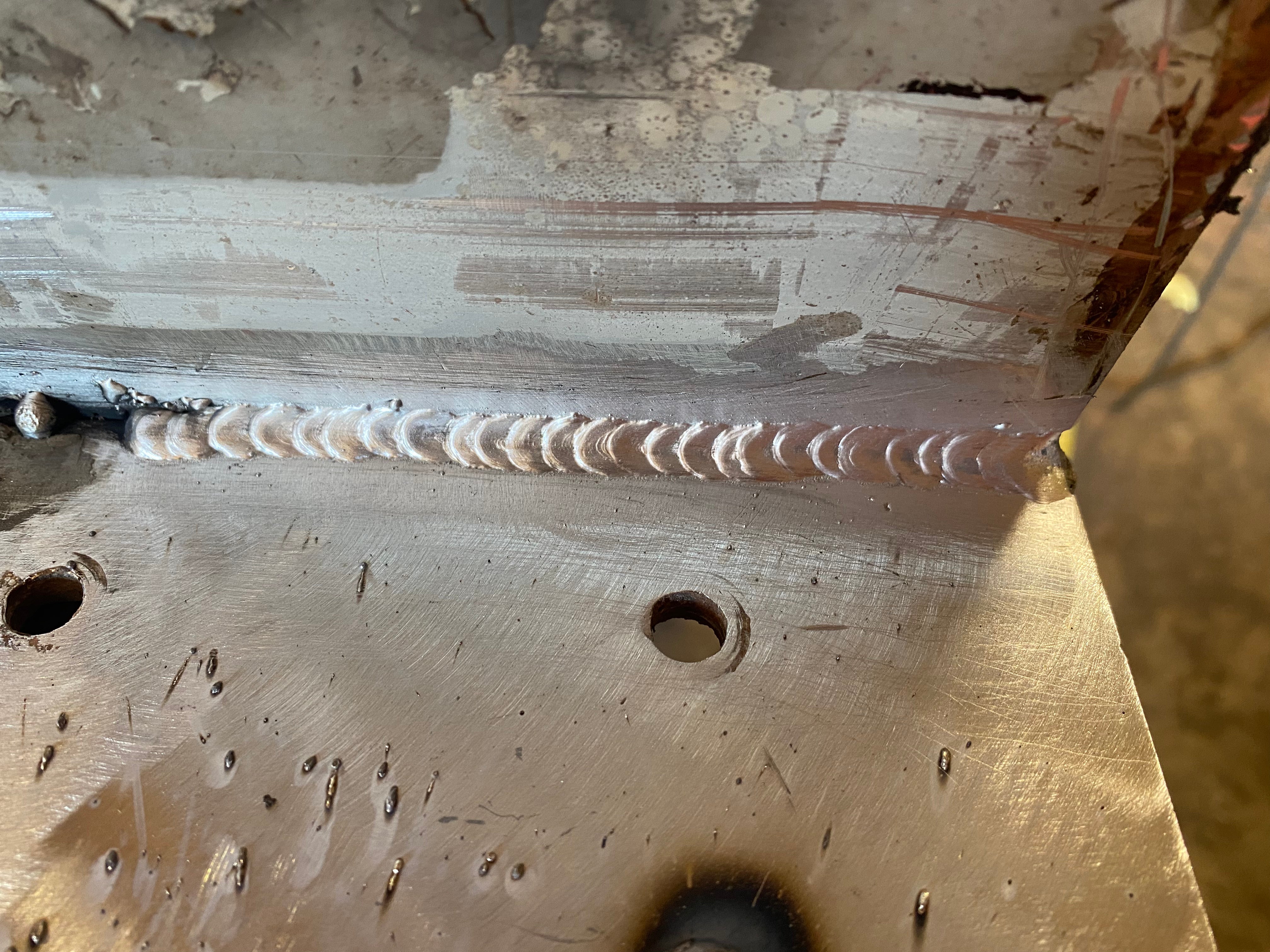
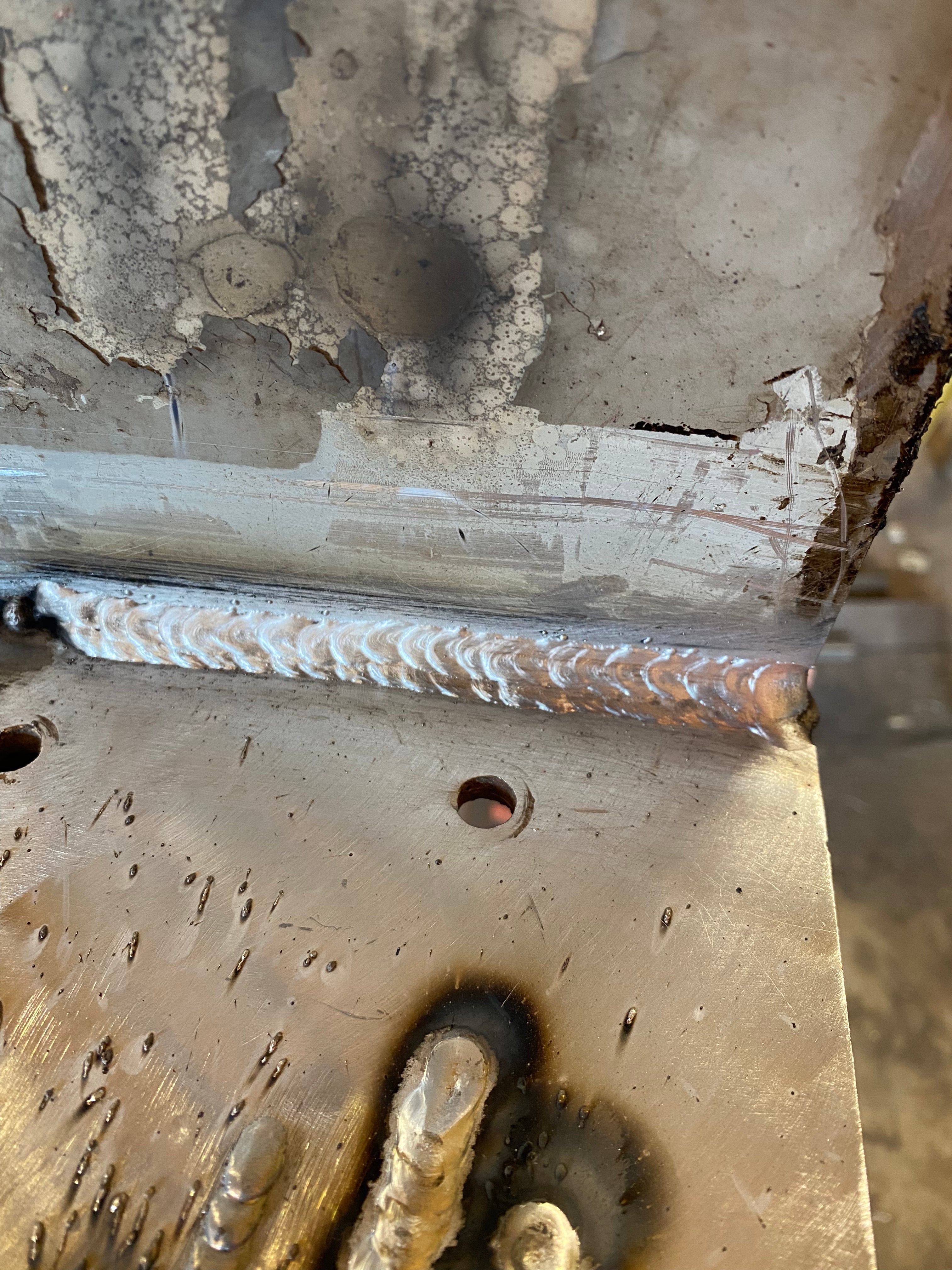
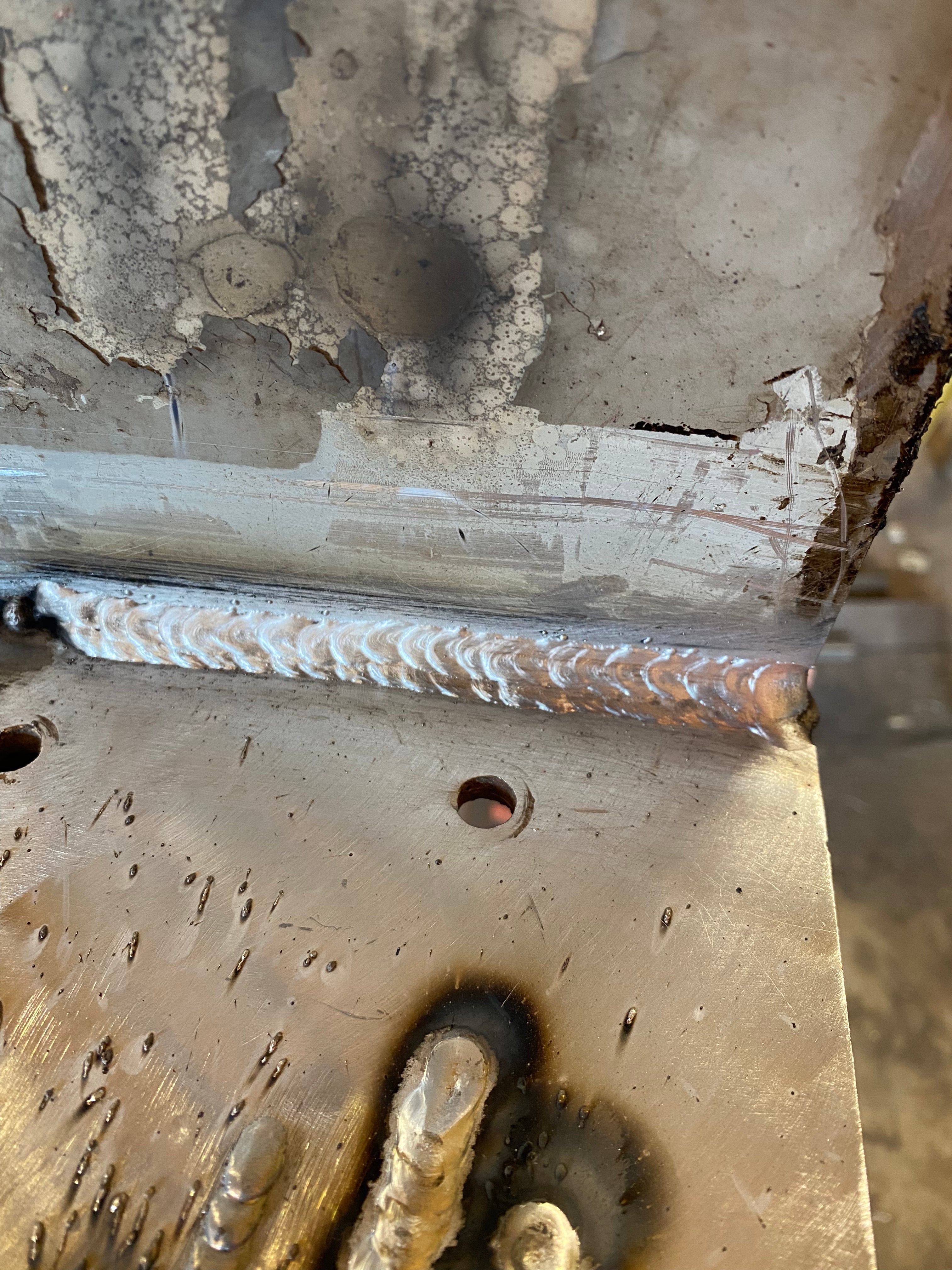
Finally took time to get my spool gun installed. Only downside is (provided I installed correctly, I went by Lincoln’s directions and even they stated this) it seems the wire feed on the front of the machine has no effect on the spool gun and the only WFS adjustment is a numberless dial on the back of the gun. But hoping to run some test beads in a couple of minutes!
Edit: attached are the first beads I’ve run with it. Never touched a spool gun before and this is on just some old scrap 1/4 aluminum plate a customer had me remove and I kept. Running about 10cfh on argon, E setting on my machine (A-G settings) and no clue on wire feed. Machine called for 400 for .035 4043 on 3/16 so I just guesstimated it and dialed it down a bit. Any advice?
Posted
13 Jul 11:58
Hate to ask a dumb question but how possible is it when welding edges together to laminate plates for trapped air to bubble up through the weld even though there’s some other gaps? When welding up this transom piece I noticed the puddle had little tiny bubbles coming up into it. Wasn’t like porosity bubbles cause eventually they’d seem to die down if I paused enough and never came through the weld.
Posted
10 Jul 18:51
Today is a first for me. I’ve welded 14 gauge lines up on an aluminum transmission cooler off a Toyota Camry before, and I welded a bunch of 1/8 plate but today is the thickest I’ve done before. I don’t have any pictures as of the moment but a client is having me build a transom riser that’s constructed out of 3/16” aluminum plate and 2”x1/4” aluminum square tube. No helium available and my machine is limited to 230 max AC. This is going to be fun!
Posted
09 Jul 16:25
Hello all. I just joined yesterday, I’m Ben and I run CWR (Coody Welding and Repair) in a small town in Midwest AL. After graduating from Tulsa Welding School in Jacksonville in 2019 I worked around for a while and as of last year I started my own welding business. I mainly do heavy equipment repair with here recently I’ve done a good bit of aluminum boat repair. I’m hoping to branch out more and get more work to hopefully become full time self employed now that I’m getting more attention and with my new plasma table. I came here to learn more and invest more skill into my business and since I’ve listened to the Welding Tips and Tricks Podcast since high school, watched ones like Jody, Roy, Jonathan and many others since then as well I know there’s going to be lots of stuff for me to pick up and learn from. Thanks!