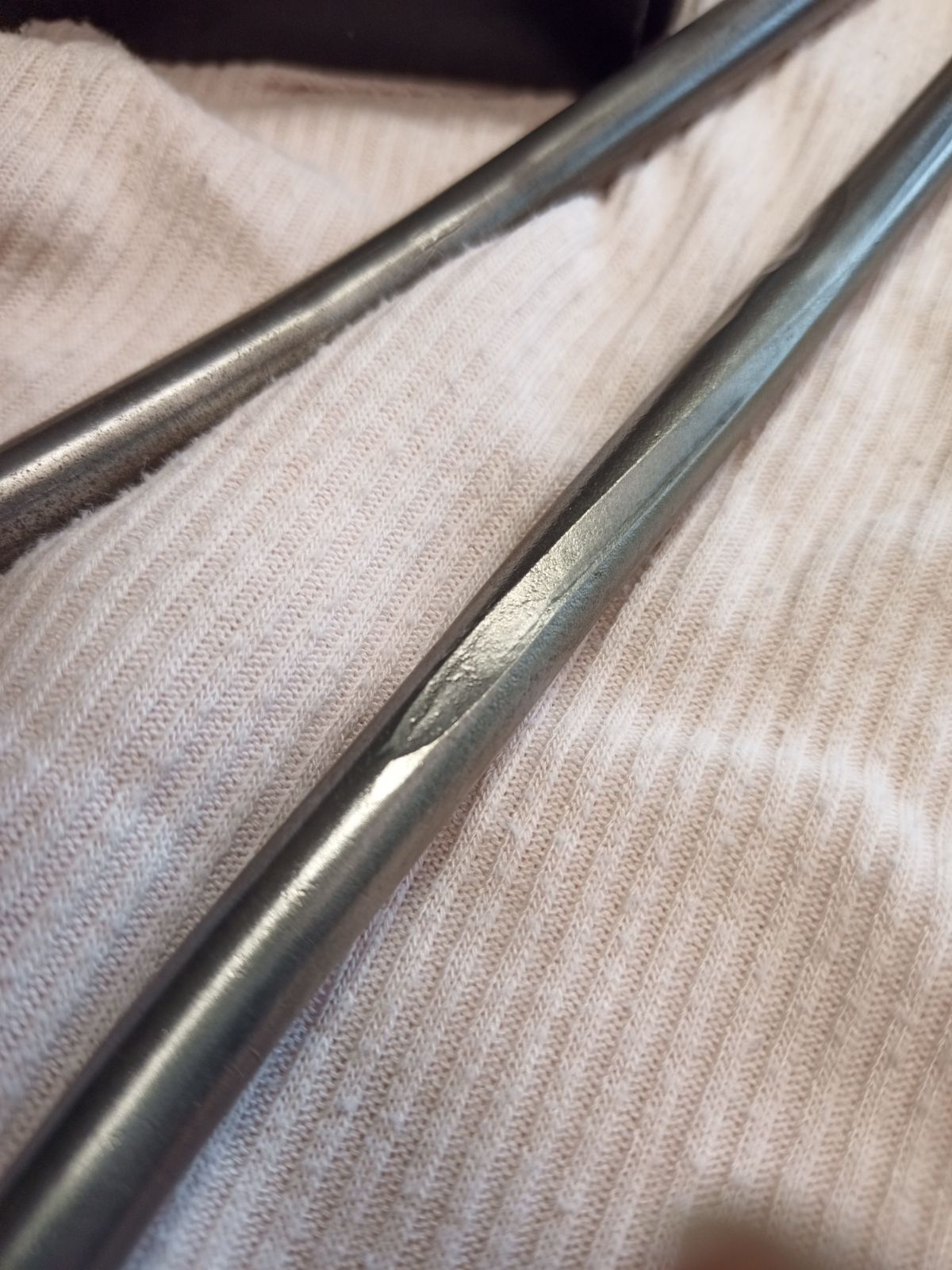
Part 2) I don't seem able to add more than one photograph.
Dorrigo, Australia
Commented on Restoration of hydraulic pipework
Commented on Restoration of hydraulic pipework
Posted
Commented on Tips for Feeding Tig Rod
Commented on Tips for Feeding Tig Rod
Commented on Restoration of hydraulic pipework
01 Jul 22:11
Part 3) I carefully formed the burst area back to it's original shape. Light tapping with a lightweight hammer.