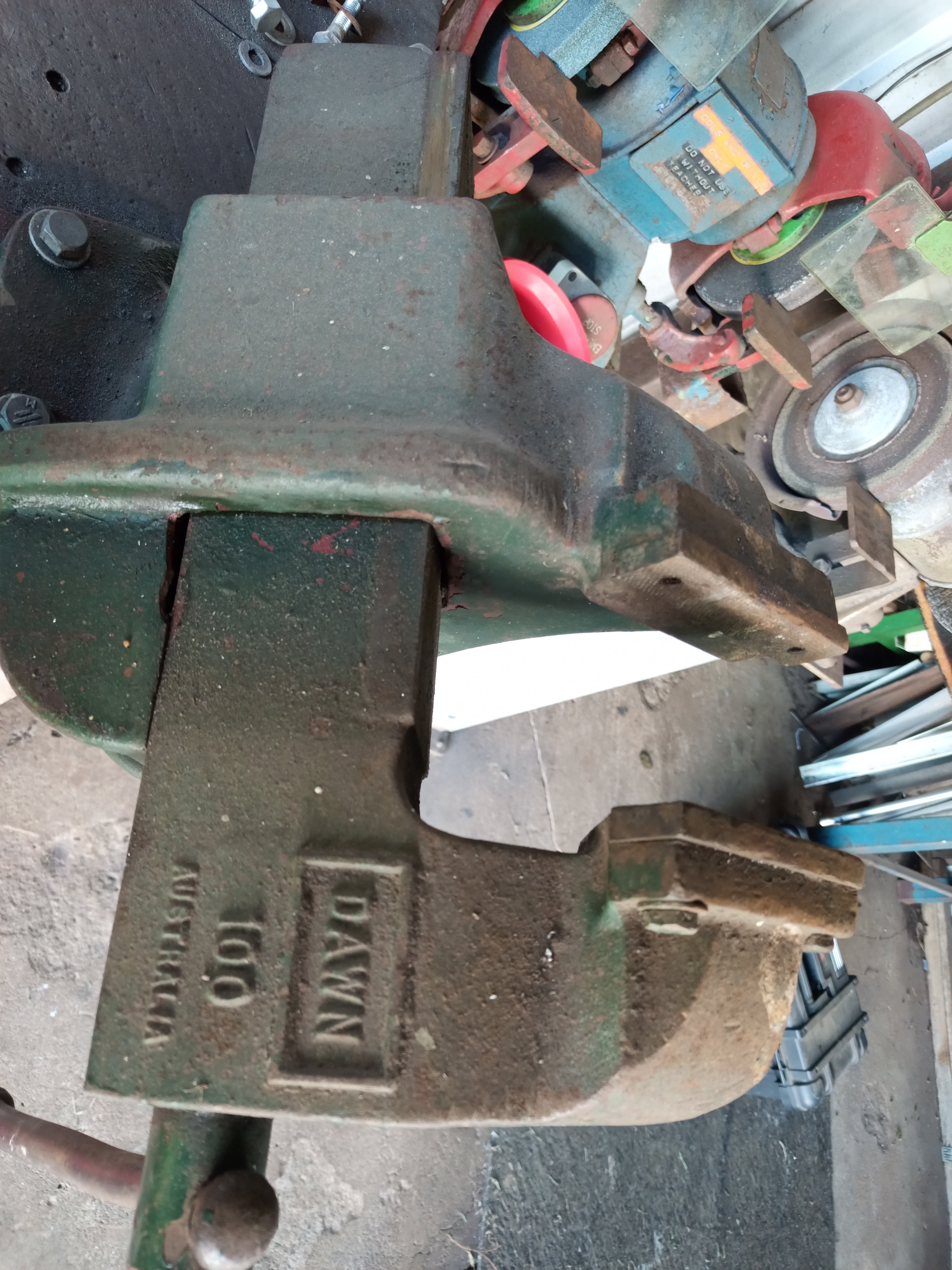
MICHAEL KEARSEY
Dorrigo, Australia
Commented on JD Brewer - Cast Iron Repair with Silicon Bronze
Commented on JD Brewer - Cast Iron Repair with Silicon Bronze
Commented on I fully restorated this 12 Year old F...
Dorrigo, Australia
Commented on JD Brewer - Cast Iron Repair with Silicon Bronze
Commented on JD Brewer - Cast Iron Repair with Silicon Bronze
Commented on I fully restorated this 12 Year old F...
Replied on JD Brewer - Cast Iron Repair with Silicon Bronze
15 Feb 00:51
Hi JD, I had this welding table laser cut. I TIG welded it mostly from the inside but wanted to fill the top tab cavities with something, so they didn't collect garbage.
Welding the cavities would no doubt have worked well. I didn't need that level of strength and didn't want' to introduce any more heat than necessary.
The answer was SilBro again, and it was easier to grind down with a flap disk.