Looking for some ideas on how best to store C clamps, particularly huge ones like these. What do you guys typically do? I've seen people use toolboxes, other chests, and some setups that are just a long horizontal bar to hang them on. Thanks.
Morning all
I am wondering how people that do alot of mobile work in rough weather conditions store all of your leads and torches, both welding and oxygen acetylene, so they remain in good condition and aren't getting damaged.
Cheers
Hate to ask a dumb question but how possible is it when welding edges together to laminate plates for trapped air to bubble up through the weld even though there’s some other gaps? When welding up this transom piece I noticed the puddle had little tiny bubbles coming up into it. Wasn’t like porosity bubbles cause eventually they’d seem to die down if I paused enough and never came through the weld.
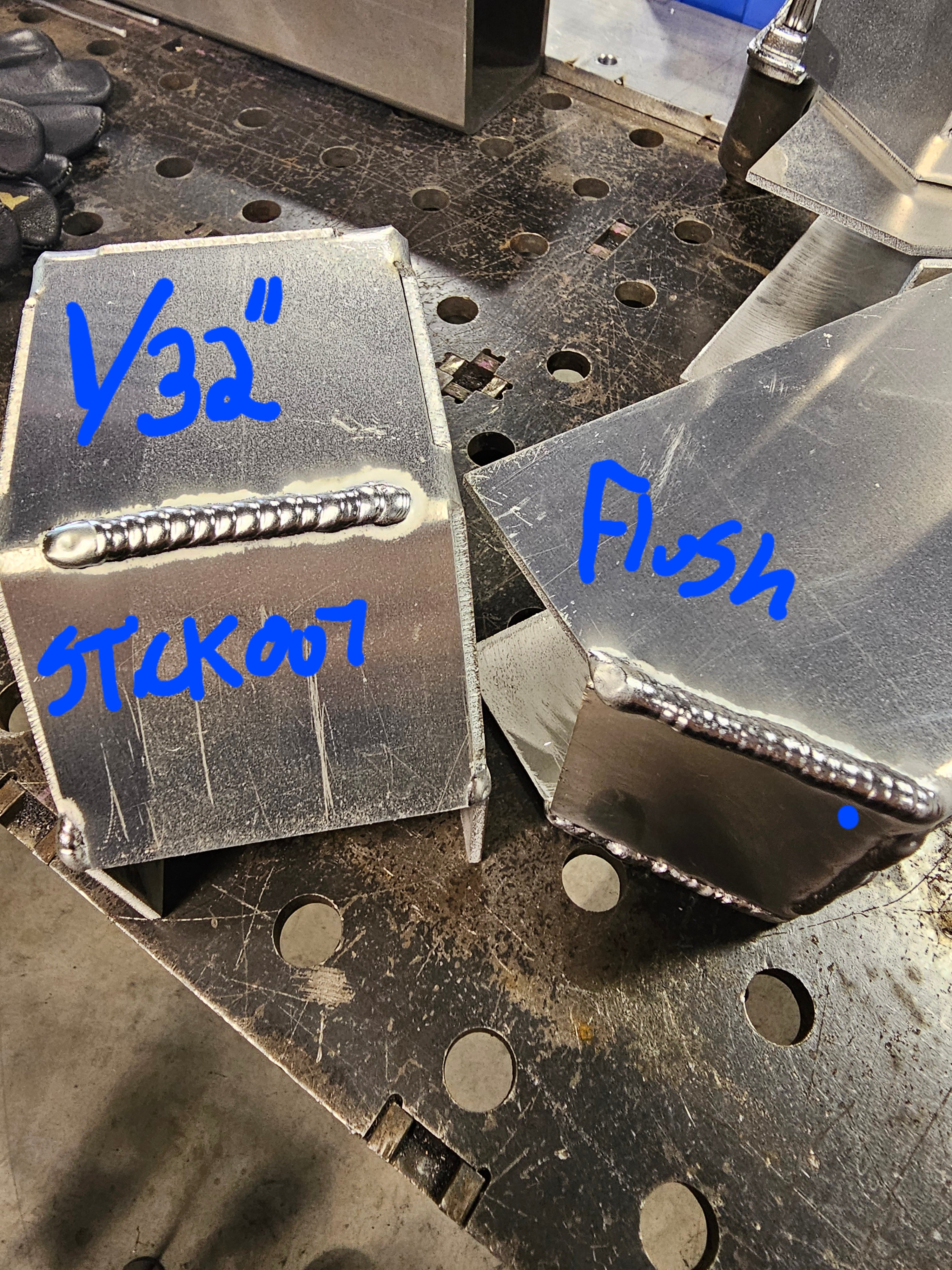
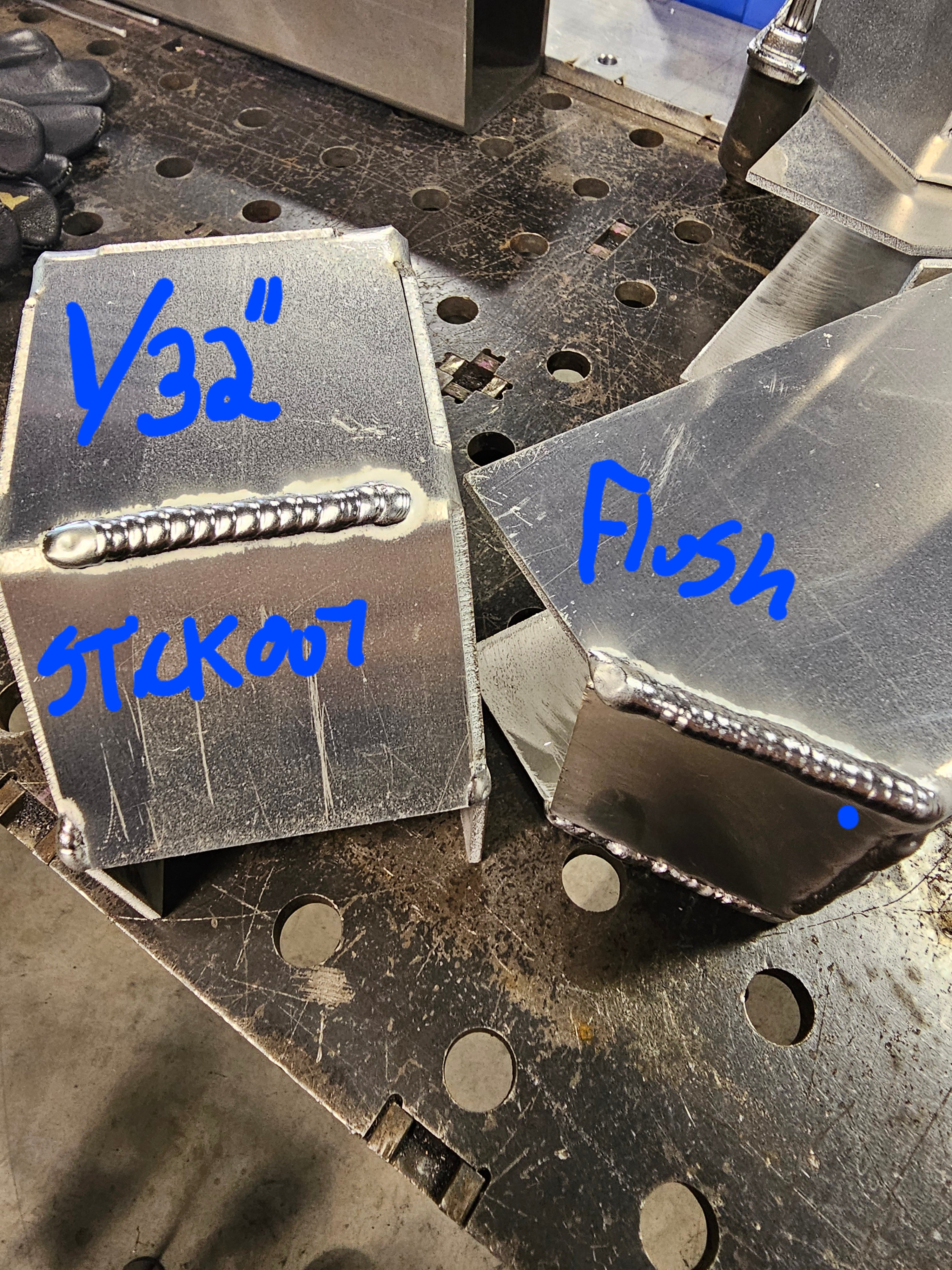
Welderskills!
I am welding tig aluminum and check out how much the stickout changes the bead appearance. The flush with the cup tungsten was more difficult to weld as well as a more erratic arc. What do you think is happening here?
Today is a first for me. I’ve welded 14 gauge lines up on an aluminum transmission cooler off a Toyota Camry before, and I welded a bunch of 1/8 plate but today is the thickest I’ve done before. I don’t have any pictures as of the moment but a client is having me build a transom riser that’s constructed out of 3/16” aluminum plate and 2”x1/4” aluminum square tube. No helium available and my machine is limited to 230 max AC. This is going to be fun!