Hi everyone,
My name is Kyle, I’m from Melbourne, Australia.
I’ve recently learning aluminium tig, I’m about a week in and I can’t get enough!
Loving all the content on this site!
I have a question on weld penetration for aluminium.
I’m just wondering if there is different “ideal” penetration welds for different applications?
-Such as something you want to be as strong as possible, obviously requires full penetration.
-where as something maybe not so structural, example: Brad’s dog feeder boxes maybe you would want less penetration to have a clean finish on the inside?
I’m not sure if I’m on the right track here, maybe once you are good enough, a full penetration weld is just the norm and second nature.
If this is the case, it would be cool to see different examples of levels of penetration and the best way to go about achieving that particular finish.
(On all of the main metals, not just aluminium)
I have an example of some of my practice - I’m still learning to feed rod, that’s definitely my limiting factor. Sometimes I can’t keep up with the weld and I panic then it doesn’t go so great.
I am padding beads to get it up to speed.
I’m just wondering also if this penetration is what you would expect on an outside corner weld?
2mm Aluminium sheet - outside corner
~120 amps (140 amps on machine, foot pedal)
120hz, 30% cleaning, 17 torch, gas lens + 6 cup, 15cfh, 2% lanth 2.4mm tungsten
1.6mm filler rod - I found that 2.4mm filler was making my bead too high and cold looking.
Again, loving all the content on here! And really appreciate all instructors taking the time to teach us their tricks!
Cheers
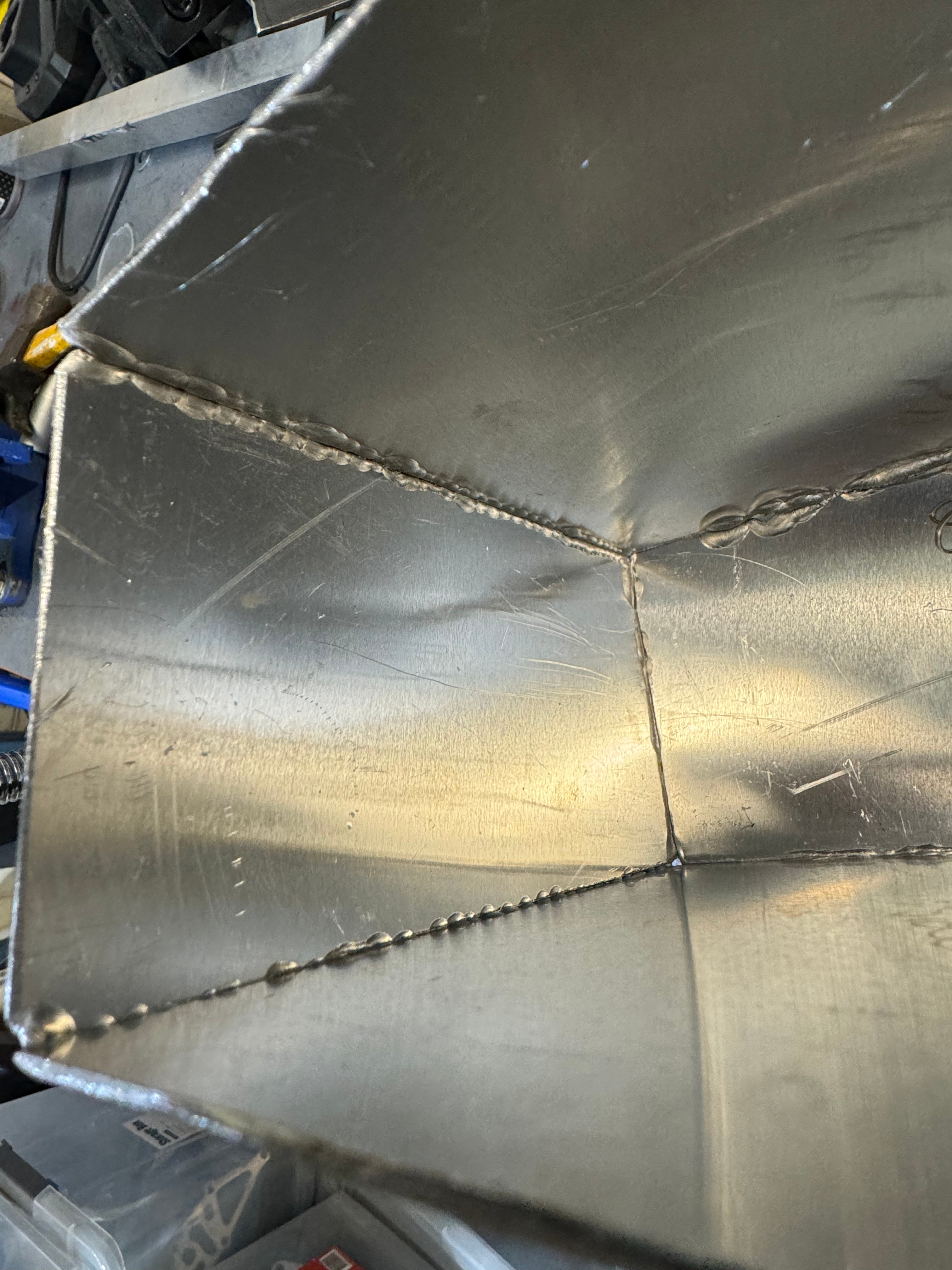
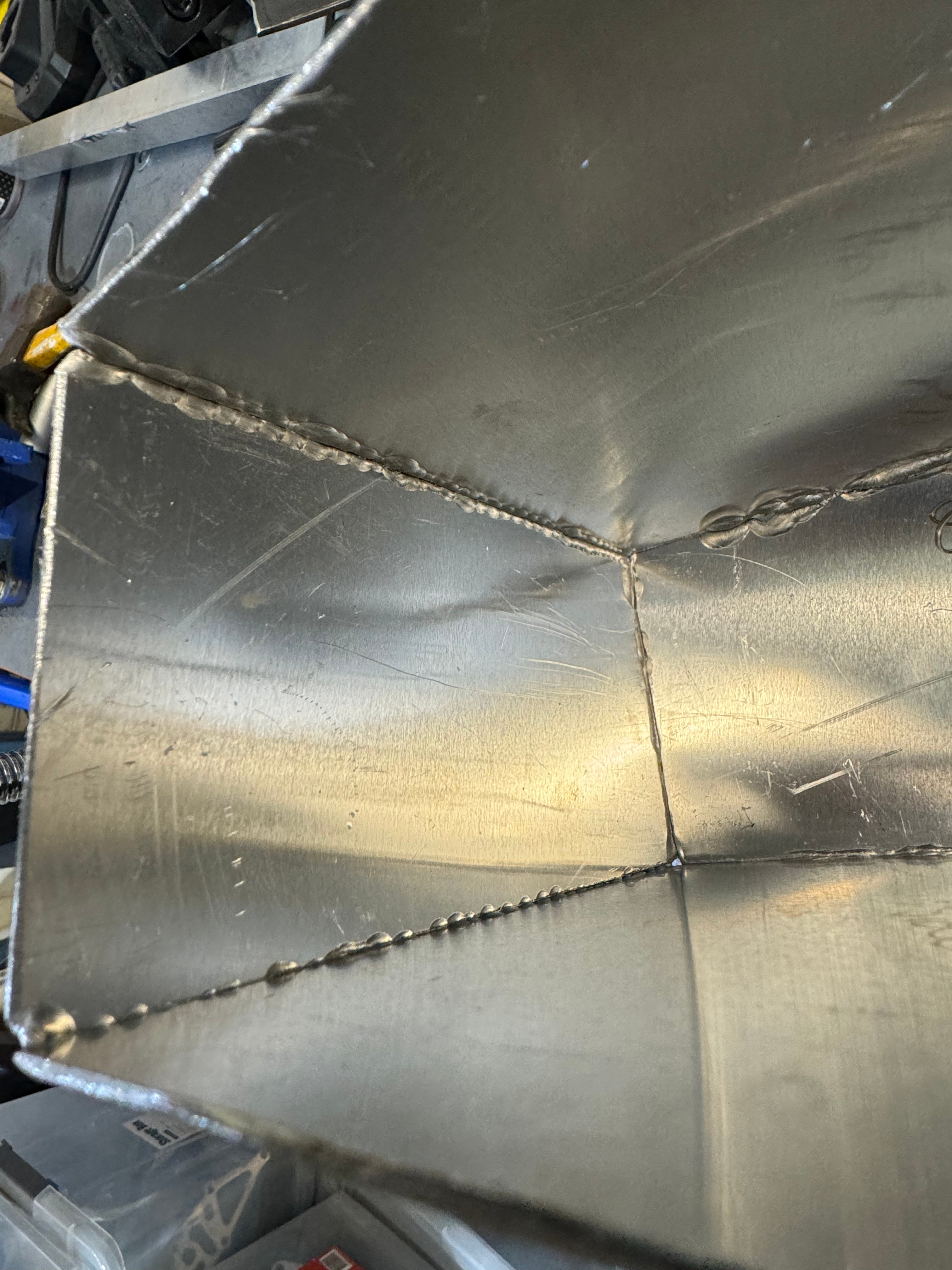
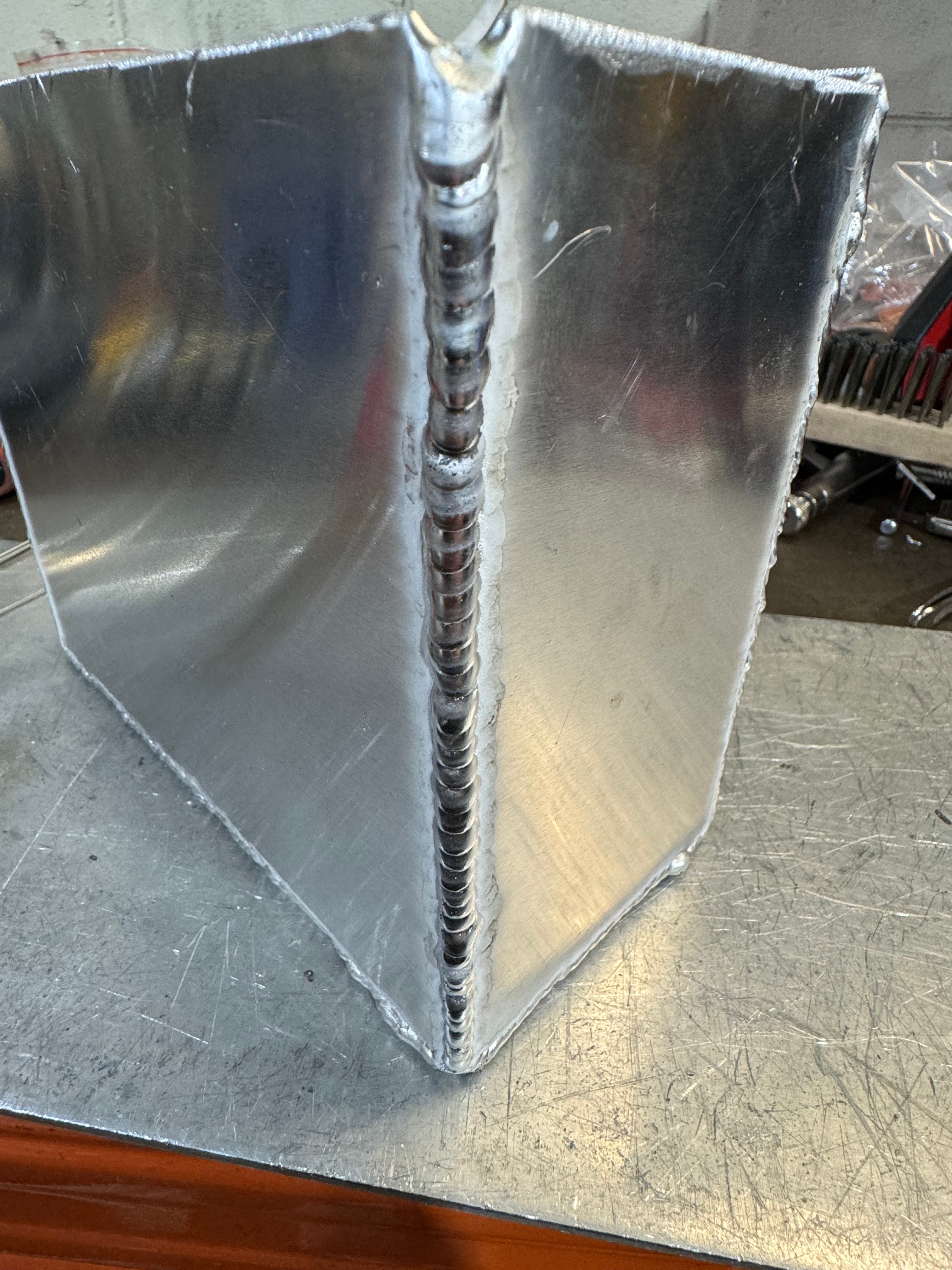
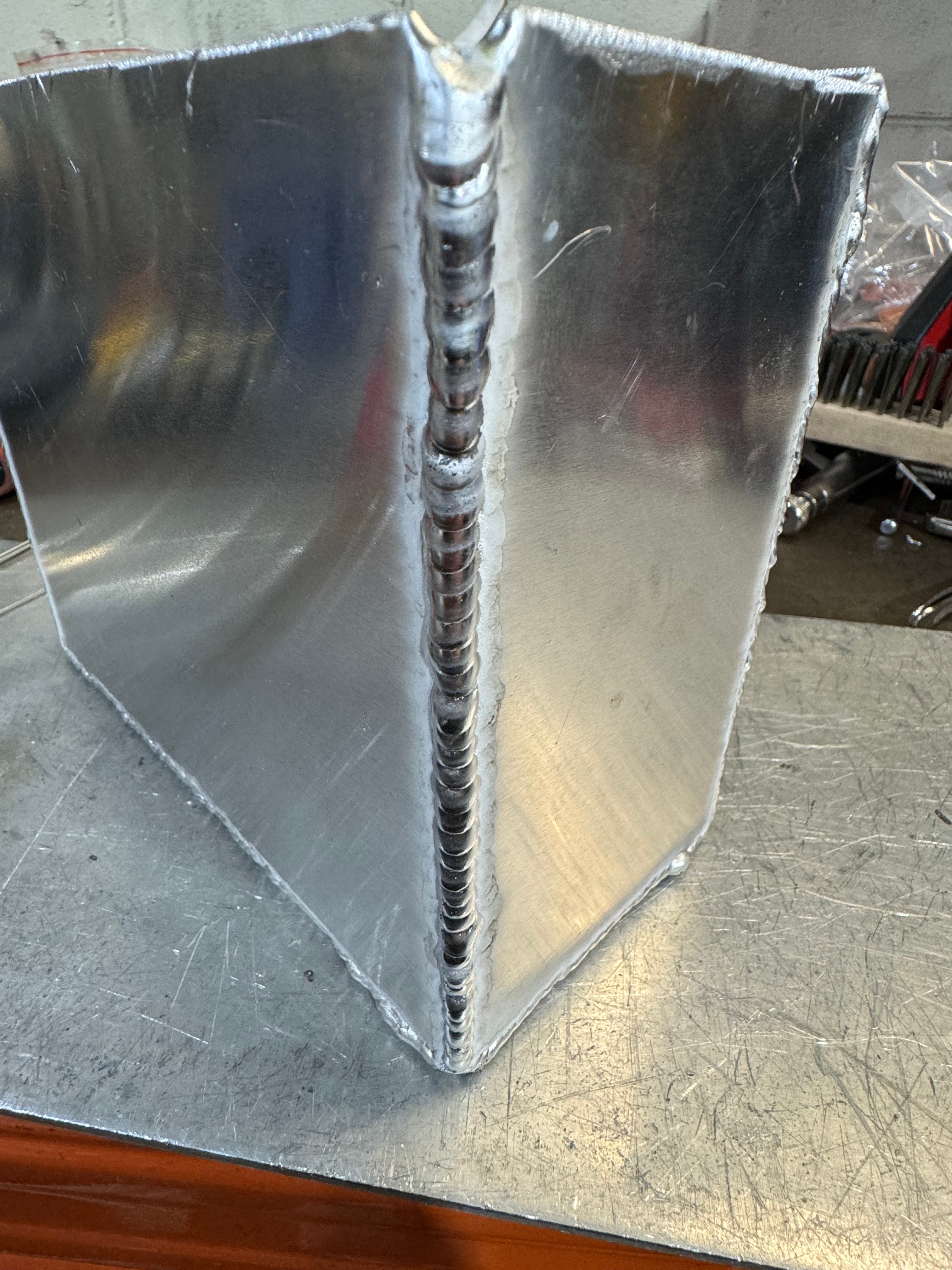
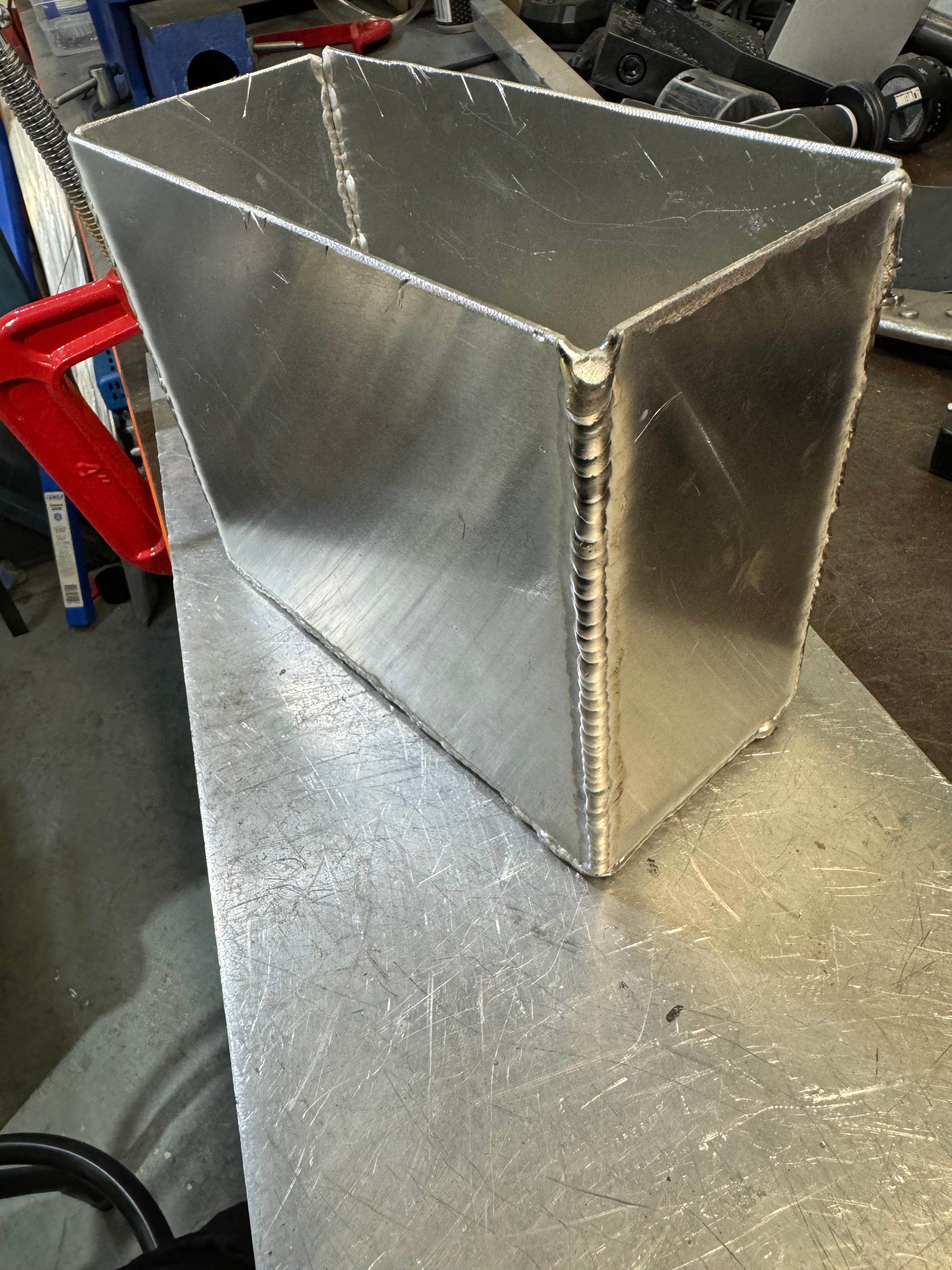
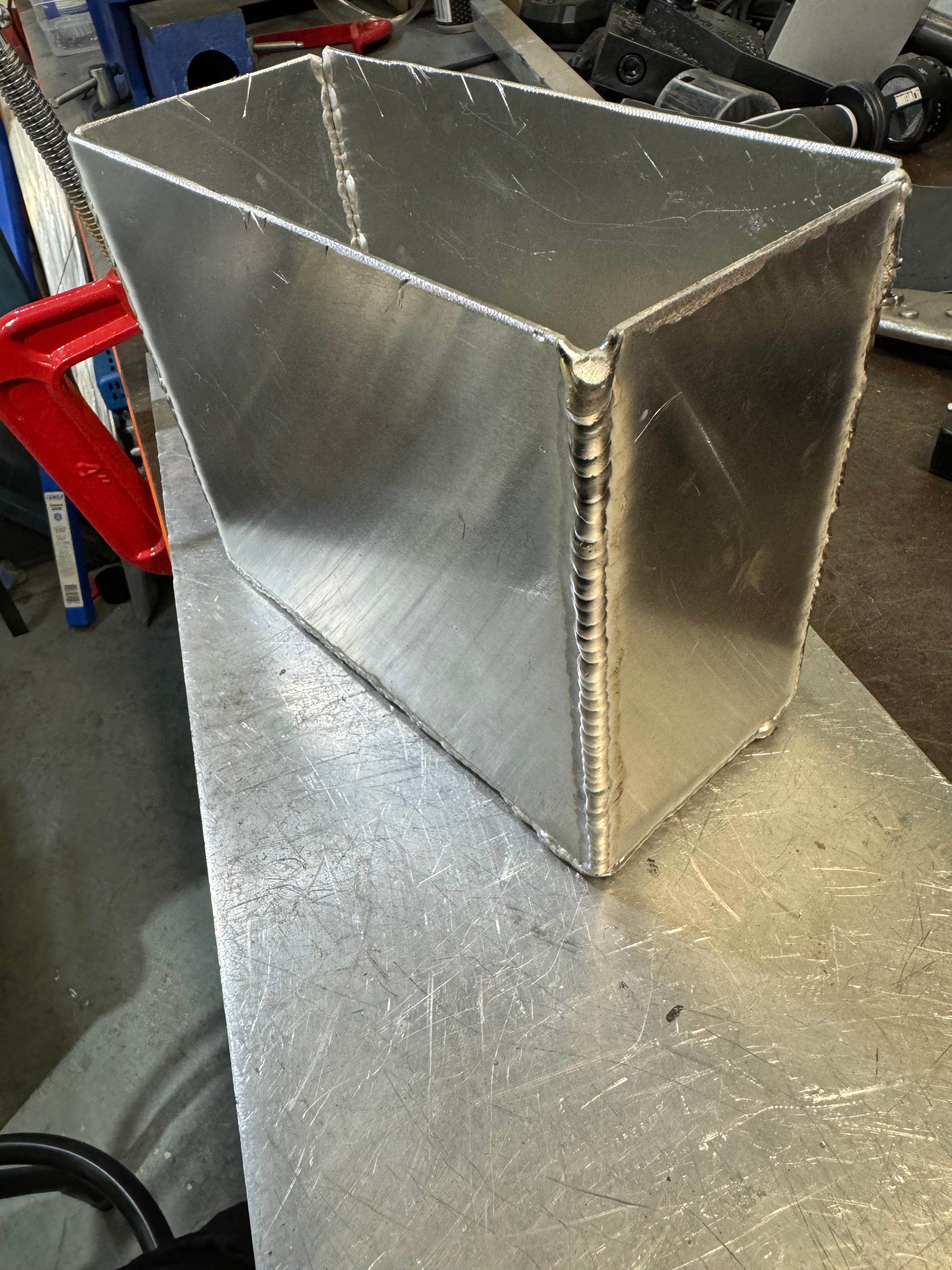
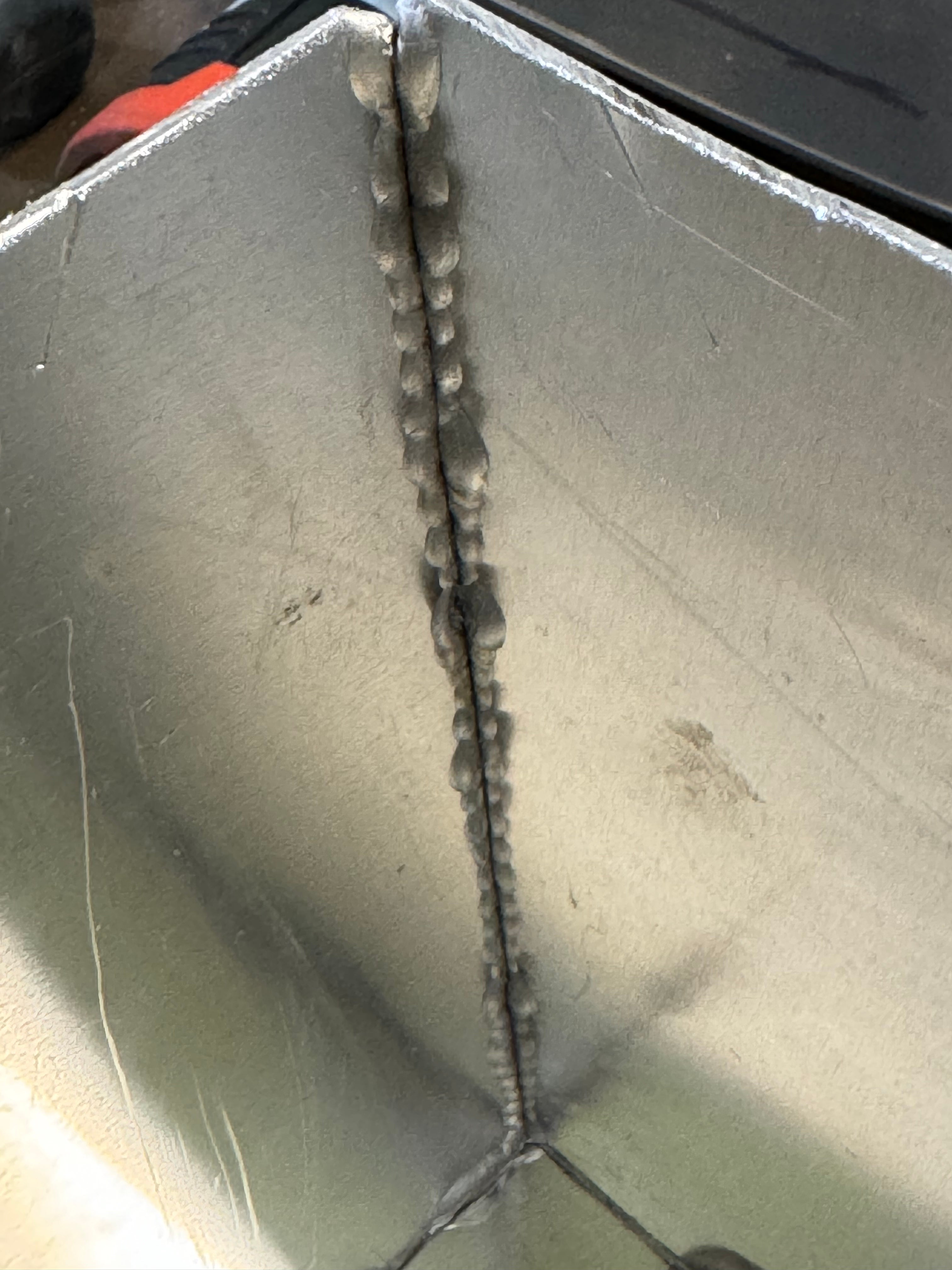
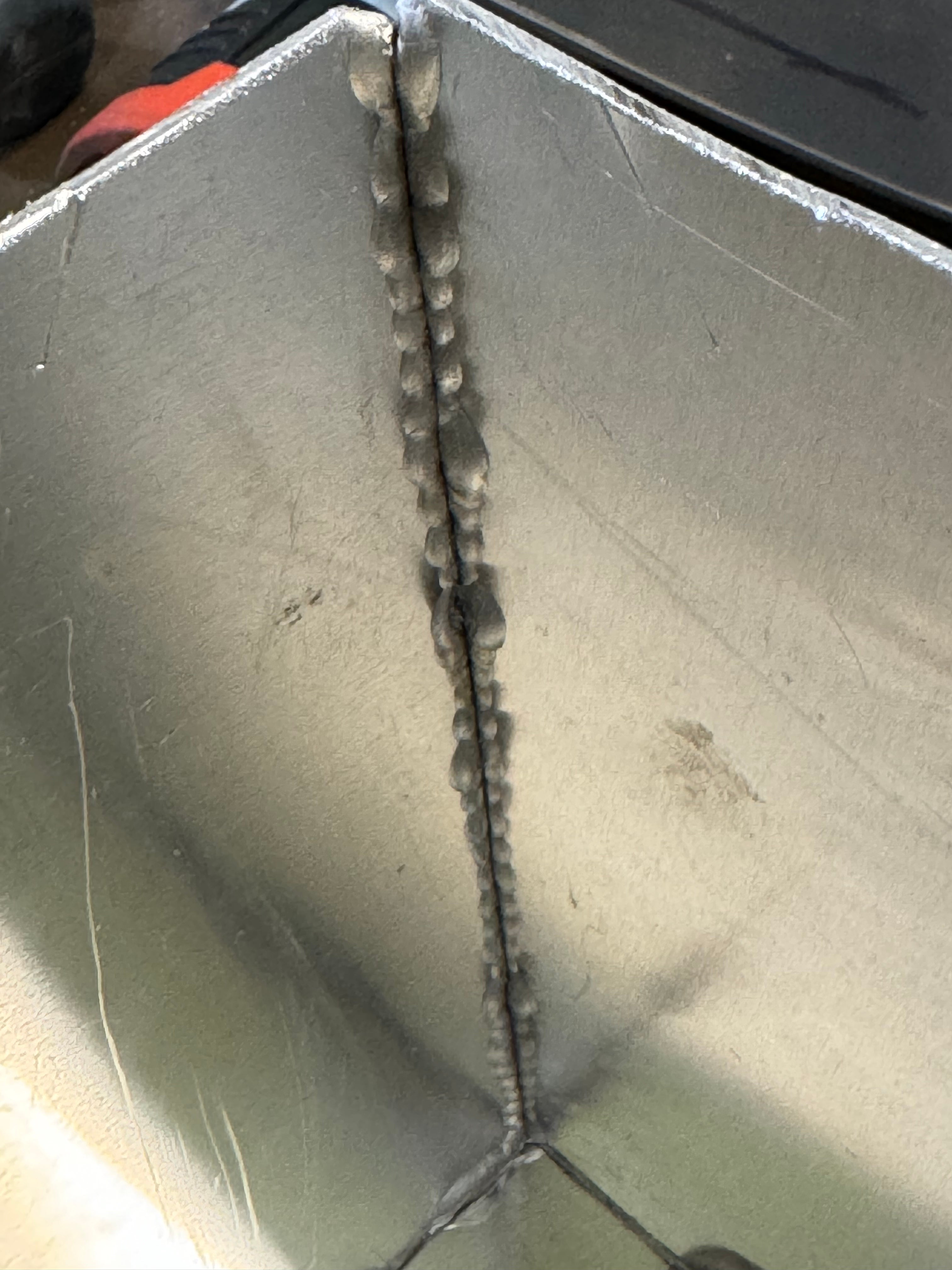
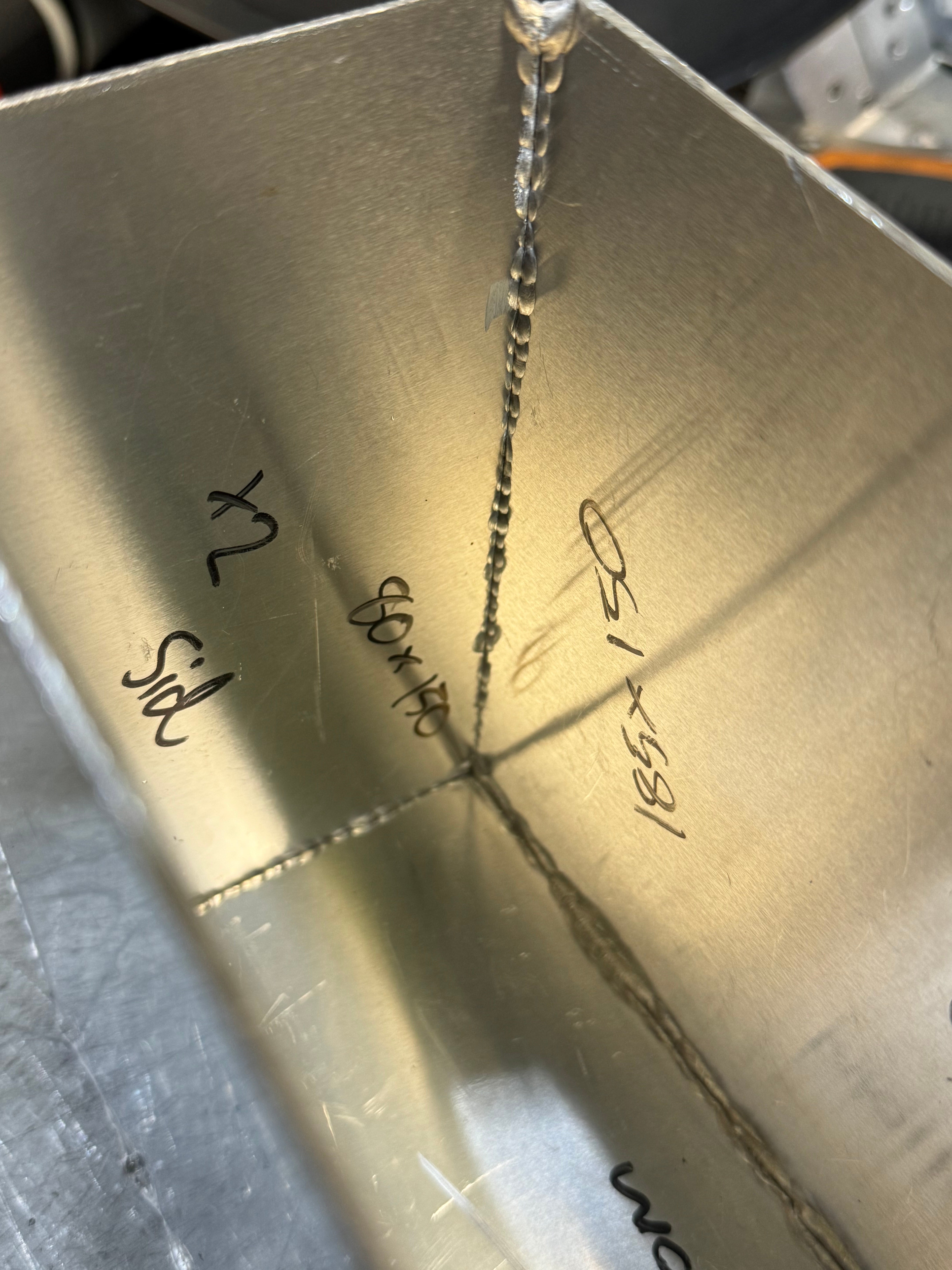
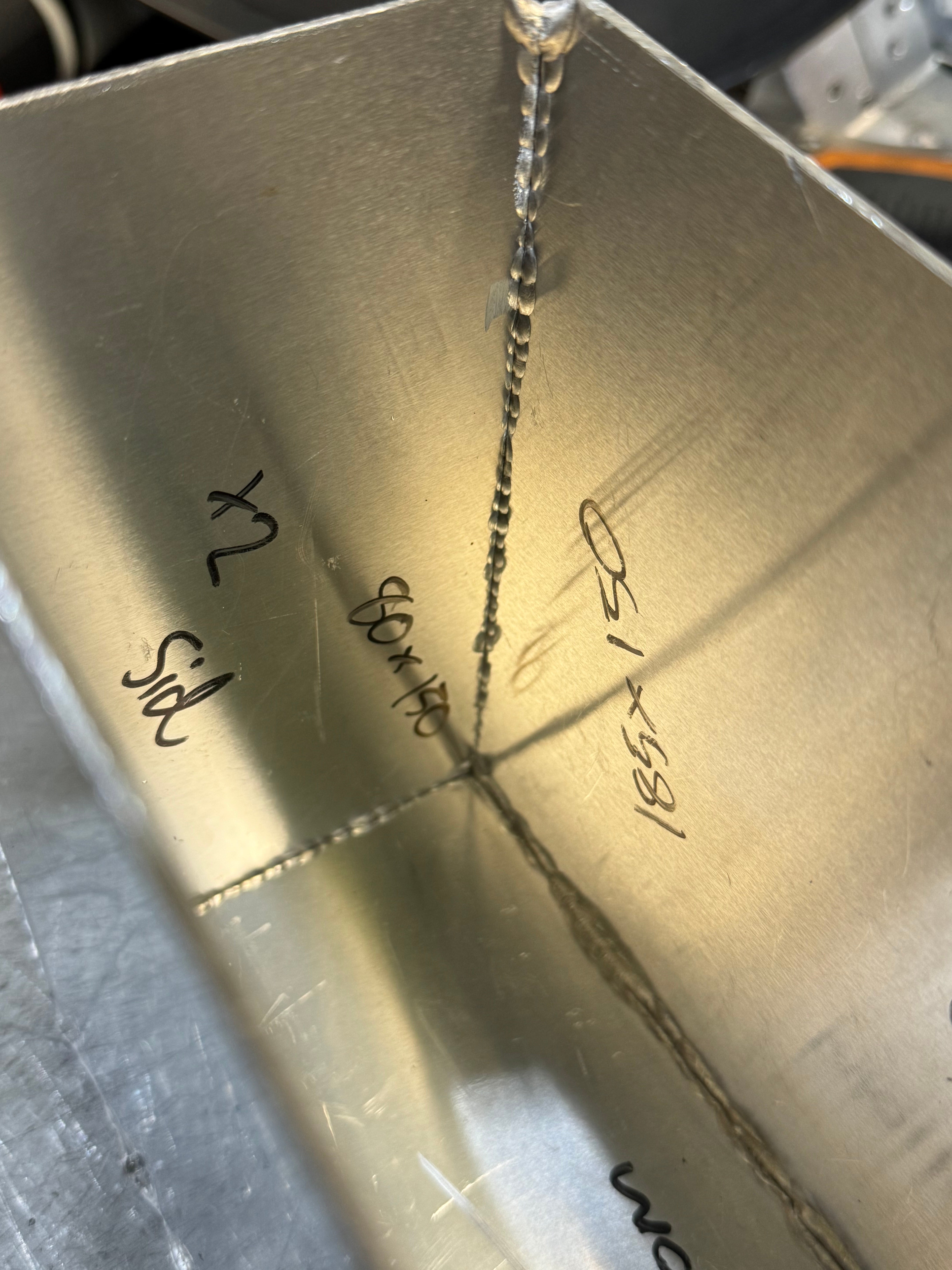
April 02, 2024